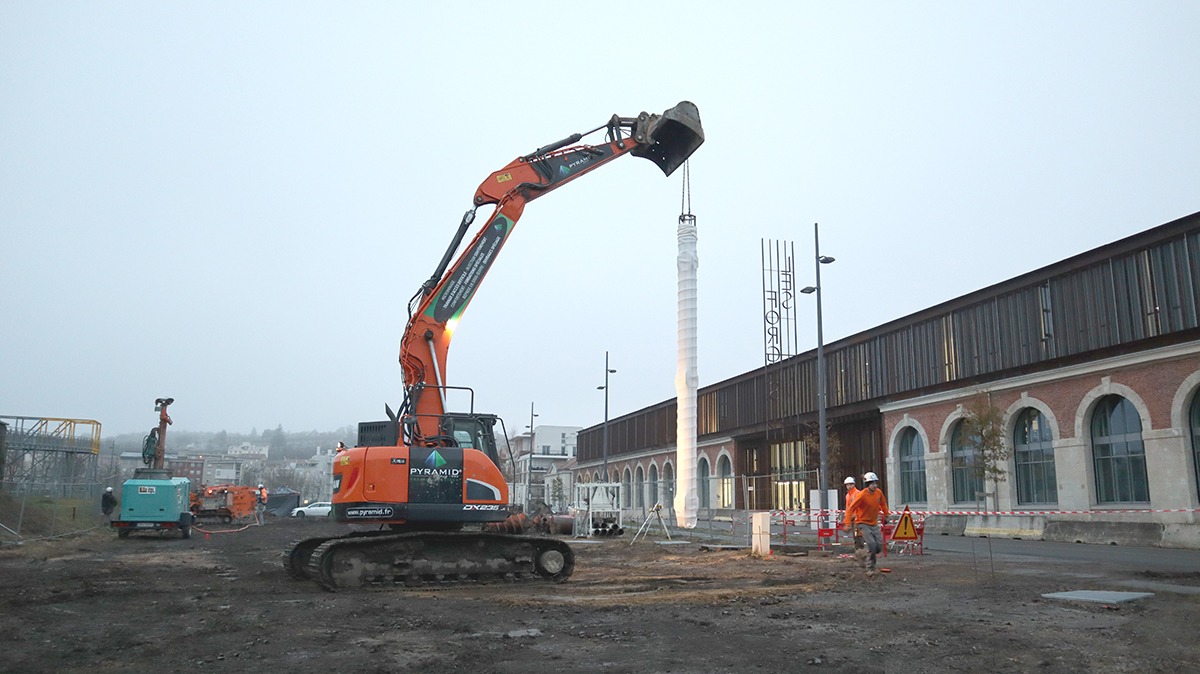
In 2019, three French companies specializing in textiles and composite materials joined forces to create an innovative new textile sleeve that replaces traditional steel casing in specific geotechnical applications.
CHAB Solutions – founded by Balas Textile, Composite Textile Materials Innovation (CTMI) and SMB Bord Cote, in conjunction with associated civil engineering experts – has roots going back 20 years. The company was formed to develop and launch a lighter, more compact and greener alternative to traditional steel casing. Its name comes from the French term “chausette à béton,” or concrete sock.
CHAB’s textile sleeve is billed as a “disruptive solution to the foundation market.” Currently undergoing field testing in France, the new product delivers the same functionality for deep foundation projects as steel casing, but more quickly and at a significantly lower cost.
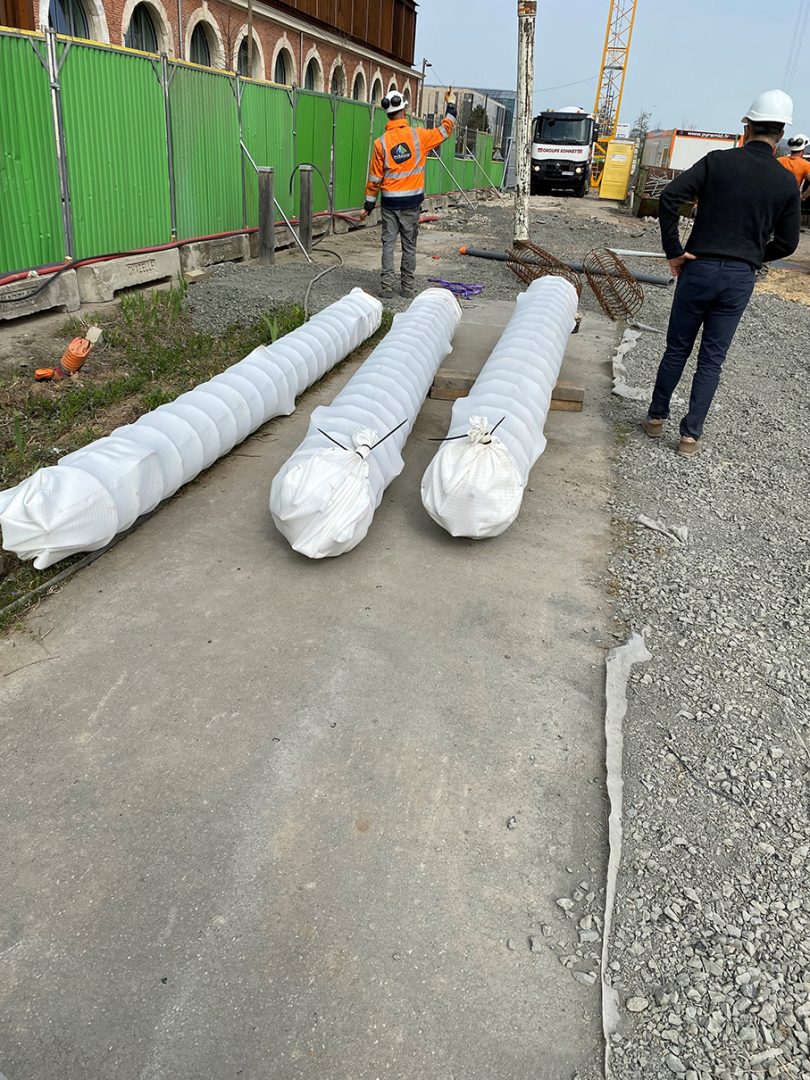
When drilling into unstable soils, steel casings have traditionally been used to assist builders with pouring and setting reinforced concrete pilings. Encased in the steel, concrete is prevented from leaching into gaps or crevices in loose soil, which would pollute the ground. However, the installation of steel casings is complicated, from the logistics of delivery to the use of specialized machinery for insertion. In addition, manipulating heavy steel casing poses a possible safety hazard for workers.
Aside from the logistics involved in getting steel casing to the building site and its cumbersome installation, there is also the environmental cost of carbon-intensive steel manufacturing and the high fees associated with purchasing the product.
Now, CHAB Solutions is offering the piling industry a way to avoid the cost and complications that come with steel casing. Essentially, the company knits a circular sock that is applied over a standard rebar cage and then lowered into a drilled shaft, similar to caseless operations.
“The benefits are reduced cost, reduced carbon footprint by 98 per cent compared to steel casing, improved safety and security on the site, and an easier and quicker process.”
Oliver balas, chab solutions
After eight years of R&D and numerous demonstrations and tests in partnership with Institut National des Sciences Appliquées (INSA Lyon) during the last four years, CHAB Solutions has developed a light, eco-friendly textile casing with just the right amount of elasticity and resistance for deep foundation applications. Strong yet flexible, the textile sleeve expands slightly when concrete is poured, filling the complete diameter of the shaft. However, the highly resistant material stays intact, even when adjacent to underground cavities or voids. By keeping the integrity of the poured concrete piling, CHAB’s textile sleeve prevents pollution and helps to set the pile properly.
“The technology is circular, with no point of weakness or resistance on the fabric,” said Olivier Balas, CEO of CHAB. “A combination of the yarn and the knitting technology is what makes it so strong.”
CHAB’s textile sleeve is best used any time concrete can be lost in the cavities of loose or karstic ground, as well as for micropile and geothermal applications.
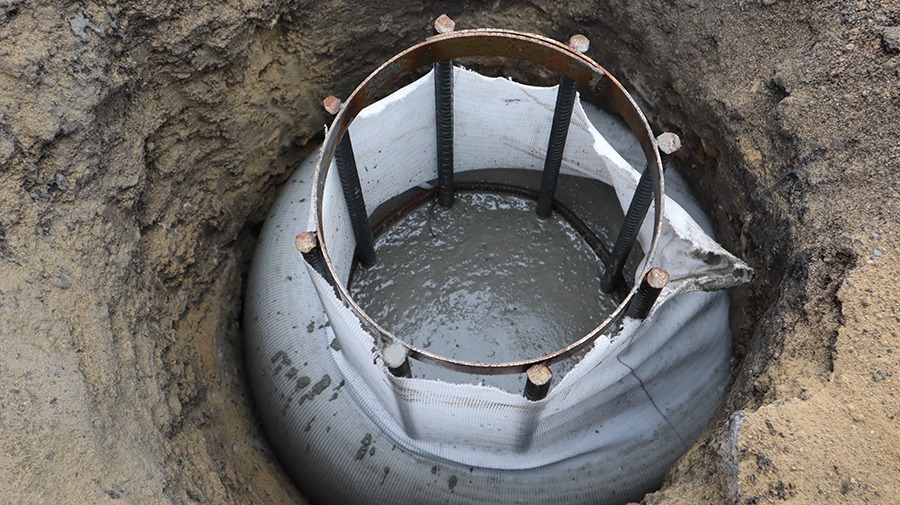
“When we go deep, instead of using steel casing, we are using 100 per cent polyester compositions, with a neutral pH,” said Balas. “This is best for the future. The benefits are reduced cost, reduced carbon footprint by 98 per cent compared to steel casing, improved safety and security on the site, and an easier and quicker process. As well, when you have steel and water together, you have corrosion entering the water. That doesn’t happen with this fabric.”
Ali Daouadji, a geomechanics professor at France’s INSA Lyon and a consultant working with the CHAB Solutions team, says a single worker can carry a 25-metre (82-foot) roll of textile sleeve. A commercial vehicle can carry the equivalent of 50 steel casings.
“It is an easy and simple process to deploy the sleeve around the enforcement cage,” he told Piling Canada. “Because of the elasticity, we can fit this textile tube around the steel cage. It is quite an easy process. It takes five to ten minutes.”
Daouadji says the testing for the textile sleeve has progressed from small-scale evaluations with a shaft two metres (6.5 feet) deep with a 0.6-metre (two foot) diameter, to larger-scale testing on a real jobsite.
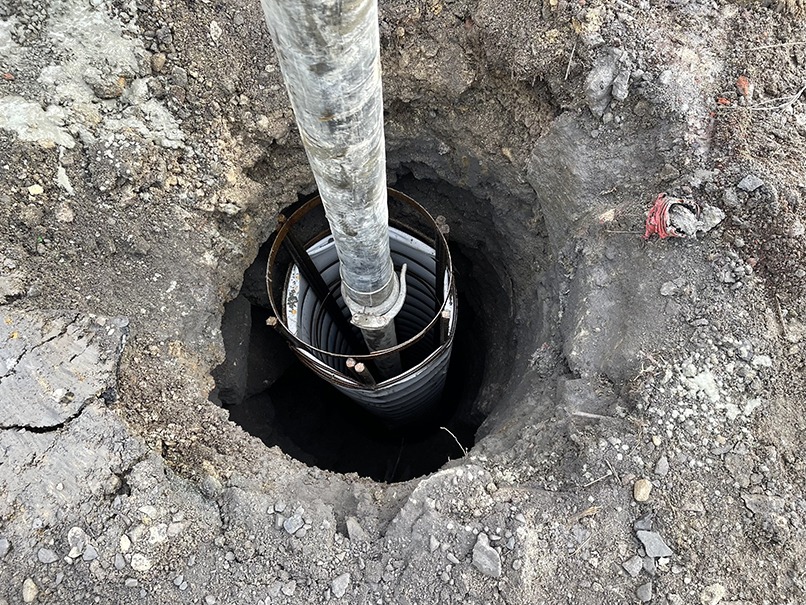
“We used the CHAB sleeve on the reinforcement cage and put that in the borehole. We poured fresh concrete and checked the integrity and did in situ testing to check,” he said. “There are different sizes of sleeves, ranging from 40 centimetres (15 inches) to one metre 20 centimetres (3.9 feet) in diameter, and they are different, the way the knitting is done. Depending on the application, you want to keep the textile as small as possible.”
The next step for CHAB Solutions is to build a facility to produce the fabric, says Balas. “For the moment, we are launching an industrial process. We are not just selling a fabric; we are selling a process. We are now working in different areas to see how we can improve the fabric and the process.
“The next step is also to build the machines for the different size of the fabric. We are working to be more efficient.”
Balas said that “tens of millions” will eventually be invested in CHAB’s textile sleeve, with about 50 people working on its development. “In two years, the concept should be widely used; and in three to four years, we should be growing in production.” Meanwhile, he is hoping to partner with a construction company for product testing and evaluation.
“We all want to have a positive impact on the environment. The textile sleeve will reduce the carbon footprint by 90 per cent – even more if you include the reduction of loss concrete. There is a huge benefit for a lower price.”
Ali Daouadji, Institut National des Sciences Appliquées de Lyon
“Innovation (for the piling industry) is good when it’s done by a building company. It’s not so easy when it’s coming from a textile company,” he said. “We need a partnership arrangement, and we are close. The big groups in France are very interested in our solution and we will work with them over the next year to identify the best process.”
Test it, use it
While CHAB’s textile sleeve is currently manufactured in France, Balas says the eventual goal is to produce it on different continents. In addition to France, the company has patents throughout Europe, North America, Japan, and China.
“For us, it’s very important to go everywhere,” he said. “The environment is very important globally, which helps us to develop quicker today than we would have five years ago. In France, we have a goal to reduce our carbon output by 30 per cent. This solution can be a big step for France and for other countries and their green story.”
CHAB’s strength lies in providing textile-based solutions for technical applications. The company is eager to refine its textile sleeve and says it can deliver quickly.
“It’s not simply a product; it’s a solution that will help customers. We strongly believe that if they test it, they will use it. It’s so easy to use and costs less,” said Daouadji. “We all want to have a positive impact on the environment. The textile sleeve will reduce the carbon footprint by 90 per cent – even more if you include the reduction of loss of concrete. There is a huge benefit for a lower price.”