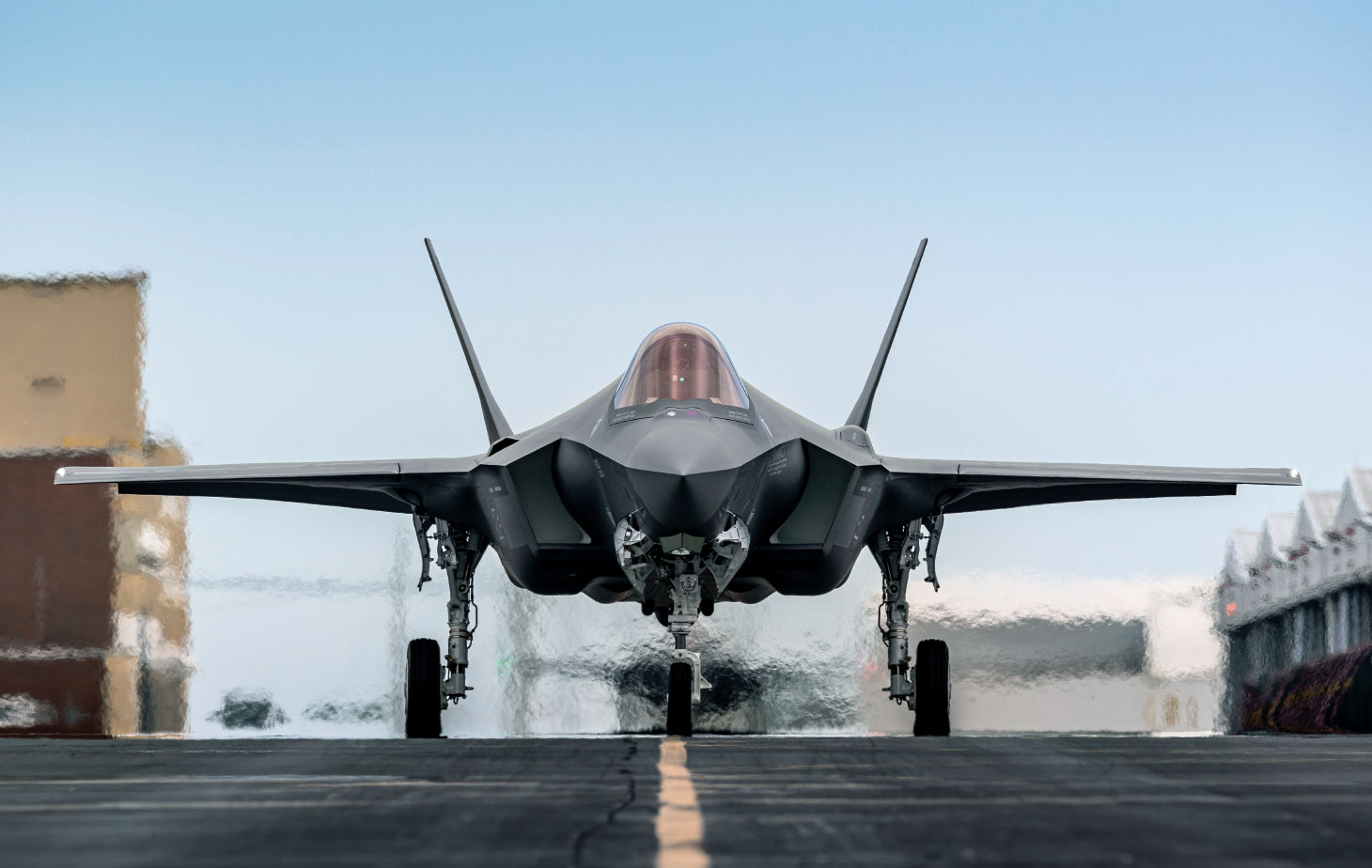
The 4 Wing Cold Lake Air Force base in Cold Lake, Alta., is the busiest fighter jet wing of the Royal Canadian Air Force (RCAF), providing mission-ready aircraft, personnel and equipment to promote Canada’s interests at home and abroad. It is about to get even busier, thanks to the Future Fighter Capability Project (FFCP).
The largest investment in the RCAF in more than 30 years, the FFCP is a large multi-billion-dollar initiative from the federal government to strengthen the Canadian Armed Forces by acquiring dozens of new CF-35A stealth fighter jets.
The new fleet, comprised of 88 Lockheed Martin-built F-35As, will replace Canada’s aging fleet of CF-18 jets and is expected to last more than 30 years. The first CF-35A fighters are expected to be delivered to Canada starting in 2026 for aircrew training in the U.S. Deliveries in Canada are expected later in 2028.
The FFCP also includes a commitment to build new facilities to support the new aircraft, at 4 Wing Cold Lake and Canada’s 3 Wing Bagotville air force base located in Bagotville, Que.
A key new facility under construction at 4 Wing Cold Lake, located about 300 kilometres northeast of Edmonton, is known as the Fighter Squadron Facility (FSF). The FSF will host two tactical fighter squadrons, an aircrew Operational Training Unit, an Operational Support Squadron, elements of an Air Maintenance Squadron, and other operational, maintenance and support elements.
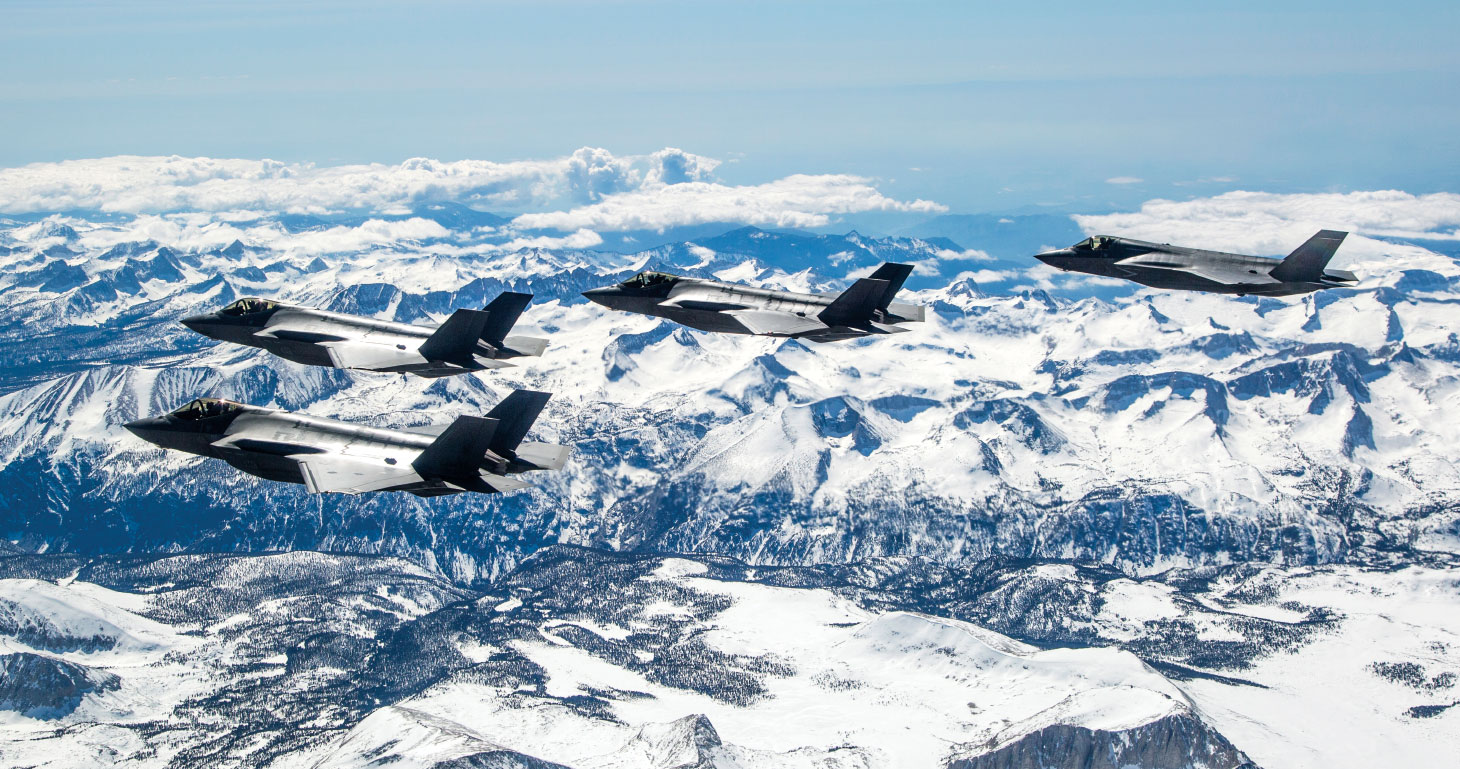
The FSF will house operational and training facilities for the new fighter jet fleet and be used for daily operations, maintenance, administration, mission planning and simulator training. The Government of Canada selected EllisDon Construction Services to design and build the FSF and associated complex in Alberta.
In January, EllisDon hired Marathon Underground Constructors to build the foundation for a parkade, one of the first FFCP structures going up at 4 Wing Cold Lake. Marathon’s piling subcontract was completed in July. In an interview with Piling Canada, Marathon project manager Corey Willard says his company installed 126 concrete cast-in-place belled piles needed to support the four-level parkade.
The piles were about 15 metres long, with shaft diameters ranging from about 0.9 to 1.4 metres and belled diameters of approximately 2.3 to 3.8 metres.
According to Willard, Marathon became involved with the parkade project early on, assisting with front-end design and value engineering work, including pre-installation static pile load tests.
Willard says his company recommended static pile load tests to save time and money as load tests provide project planners with accurate assessments of soil strength, which factor into decisions regarding the quantity and type of piles used.
“There’s nothing worse than rolling into a piling project that’s very difficult to construct. We want to help guide them, get their sizes and costs down, and make a good executable project for us.”
Corey Willard, Marathon Underground Constructors
Marathon’s load testing at the parkade site revealed soil strengths were much higher than initially thought, meaning fewer piles were needed to support the structure. Willard says piling plans were adjusted, which led to substantial savings for EllisDon and its client, Canada’s Department of National Defence (DND).
“The biggest component of a piling price is concrete. It’s normally about 40 to 50 per cent of your price, so the name of the game with value engineering in piling is reduce your piling quantity. It’s going to save you money almost all the time,” Willard said.
He says Marathon also provided some insight and recommendations on reducing risks and boosting efficiencies on the project.
“There’s nothing worse than rolling into a piling project that’s very difficult to construct. We want to help guide them, get their sizes and costs down, and make a good executable project for us,” he said. “When you can do that, the client sees the benefits, and you’re able to build trust.”
More piling work
Willard says his company’s work on the parkade is just one of many projects at 4 Wing Cold Lake that Marathon hopes to work on over the next four or five years. Marathon has already embarked on its second FFCP project for EllisDon, performing static pile load testing at the site of a soon-to-be constructed operations centre for the new FSF.
Willard says the testing will result in more cost savings for clients, like it did on the parkade project. Following the load tests, Marathon will bid on the piling subcontract for the operations centre, which has a footprint of approximately 200 metres by 150 metres.
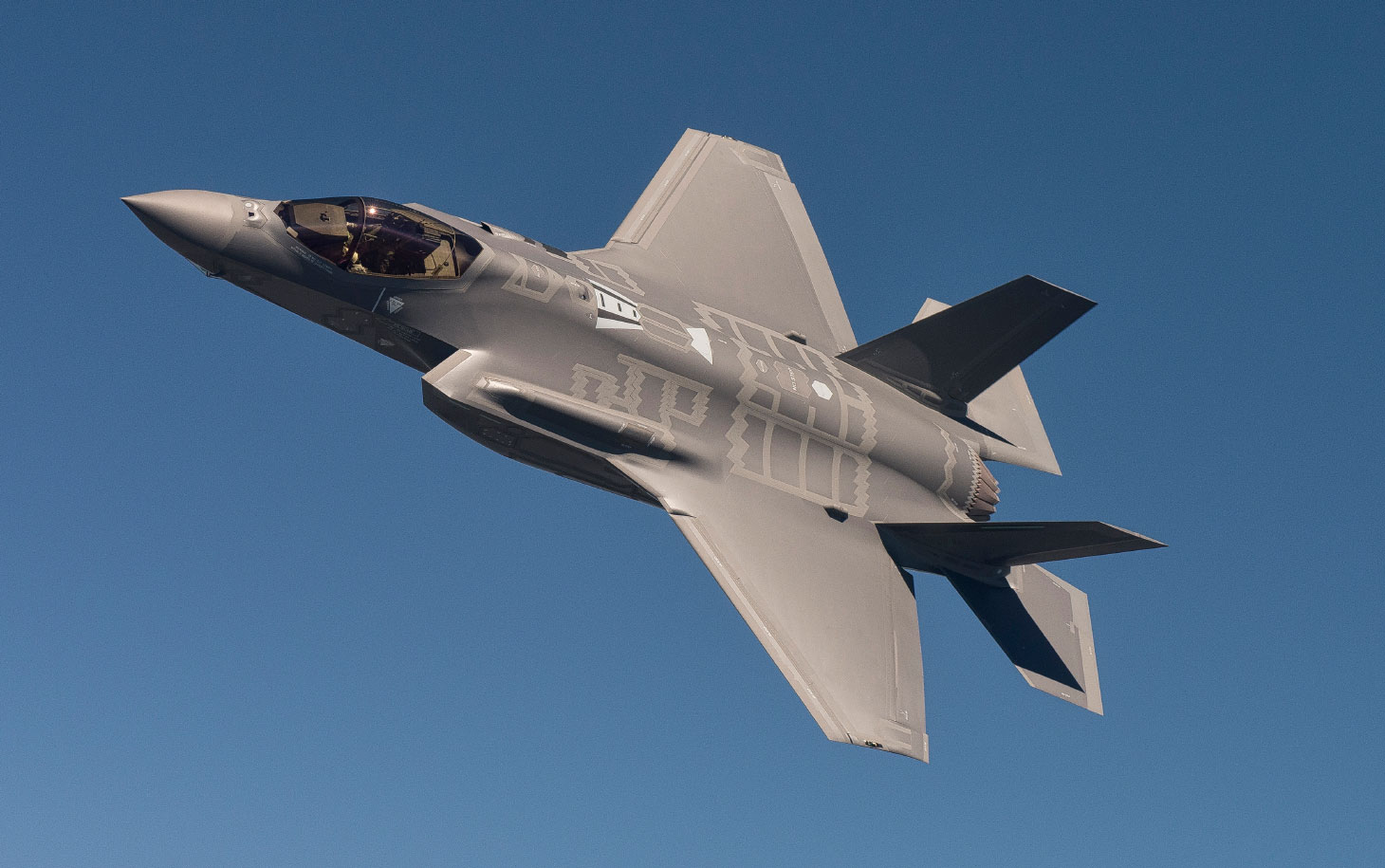
Willard says this work would involve installing approximately 450 cast-in-place concrete belled piles. Construction on that project is scheduled to start in early 2025.
Marathon also hopes to acquire the subcontract for foundation work required to build 50 hangerettes (small hangers, each housing a single CF-35A jet) located along an airfield ramp adjacent to the new operations centre.
For Marathon, one unusual aspect of the FFCP work is the need for enhanced security. Willard says his company was vetted by the DND and its piling team must observe tight security measures required for construction workers at military installations such as 4 Wing Cold Lake.
“It’s an active base with some very sensitive information, so security is top priority on a jobsite like this,”
Willard said, adding people need to be very cognizant of that while they’re working and doing things like taking pictures, which is not permitted unless approved by military authorities.
Jobsite challenges
According to Willard, the parkade piling project at 4 Wing Cold Lake presented numerous challenges. One was an environmental issue: groundwater contamination caused by a previous dry-cleaning establishment at the site.
Willard says the piling crews had to be very careful and take special measures whenever they encountered water during drilling. Contaminated groundwater had to be contained with one of two methods: either leaving it where it was and sealing up shafts with casings, or by removing the water and transporting it to a water treatment plant located at the air base.
Willard says soils were sometimes very soft and wet, creating liquid mud during drilling that had to be scooped up and carted away to a spoil disposal location at 4 Wing Cold Lake.
Another, even bigger obstacle for the Marathon piling team was the size of the belled piles and the very challenging ground conditions that made drilling difficult and sometimes hazardous. Willard says the static pile load tests revealed that bigger belled piles were required for the job to support lateral loads up to 625 kilonewtons.
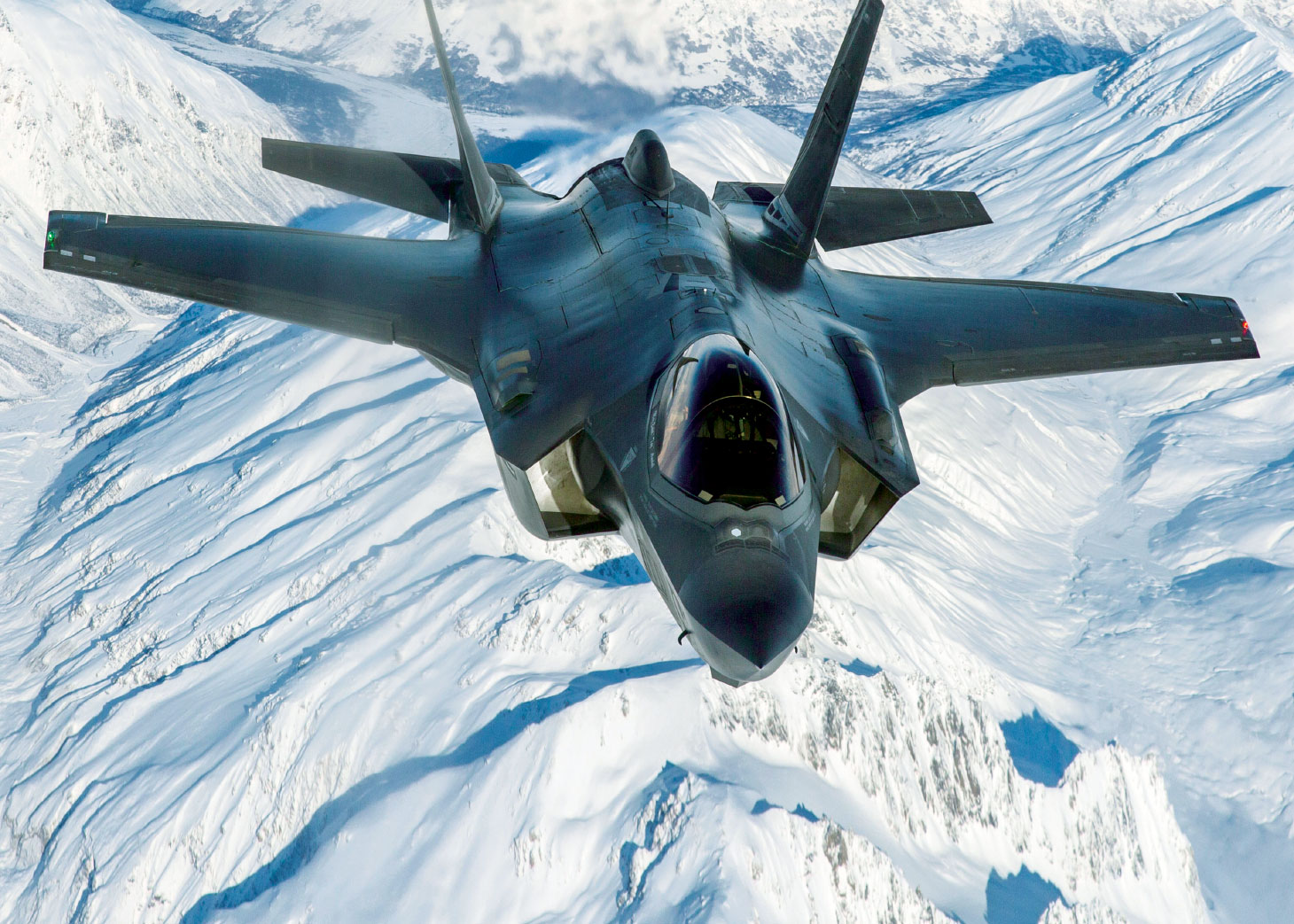
“This was a little more unique than a standard belled pile job,” he said. “What made this job challenging was the size of the piles and very large lateral load, the sideways load on the pile. When you have piles this size, you need big equipment, you need big rebar and you’re pouring large volumes of concrete.”
The big machines Marathon used to build the parkade foundation included three different drill rigs: a Liebherr LB 35, a Liebherr LB 30 and a Soilmec SR-65. Support equipment such as loaders, skid steers and a zoom boom were also used.
Marathon’s 14 team members on site required heavy equipment not only for installing the massive piles, but to deal with the tricky ground conditions. As an example, Willard says Marathon’s Liebherr LB 35 rig sometimes took up to six hours to cut through boulders while drilling piling shafts.
“Day to day, you just don’t know how many obstructions you’re going to encounter. That was the biggest challenge, trying to plan for the unplannable,” he said.
Rick Maidment, western regional manager for Marathon Underground Constructors, says he’s looking forward to more FFCP projects in the years ahead and is proud of his company’s accomplishments so far.
Maidment says that given the difficult ground conditions and other challenges at the parkade site, the project really illustrated the value of having the right equipment, the right people and the right leadership team for the job. The result, he says, was high-quality work that was also performed safely.
“Everyone was outstanding on this project,” Maidment said. “Our guys did an excellent job dealing with all the unknowns and most importantly, they did it safely and we did not have any major safety incidents.”