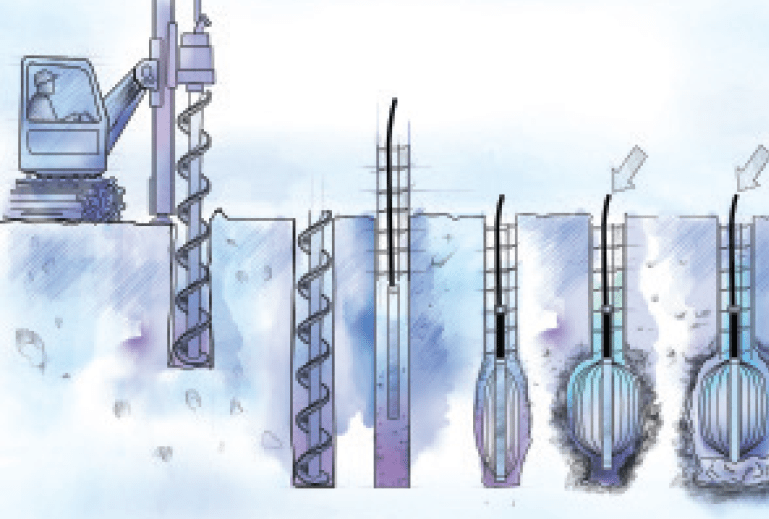
Expander Body International is setting out to fundamentally change the way we think about foundations
The installation of deep foundations has not changed much over the last half century. While there have been tweaks and adjustments to the technology, generally speaking, there are only two different types of piles primarily used today to hold up buildings: end-bearing piles, in which the pile is driven into the ground until it hits bedrock or other bearing materials, and shaft-bearing friction piles, in which the pile generally mobilizes more resistance the deeper it is installed. Ottawa-based Expander Body International (EBI) is setting out to provide a third option and fundamentally change the way industry thinks about foundations.
Now in Canada, EBI has worked on more than 200 successful projects around the globe and has more than 25,000 Expander Body (EB) units in the ground to date. The product is patented or trademarked in 188 countries and has conservatively saved organizations in excess of 30 per cent in costs and more than 40 per cent of labour when compared to traditional methods.
The EB pile technology was first developed by Swedish engineer Bo Skogberg in the 1980s before it was purchased a decade later by Prof. Mario Terceros, who saw the potential of the product to increase the capacity of bored piles in loose to dense soils. Over the next decade, the EB technology was advanced in Bolivia, making it more adaptable to different pile installation processes and soil densities, and providing broader savings for deep foundation projects internationally.
“We have surveyed hundreds of engineering companies, project development companies and design/build companies to ask them what challenges they routinely face when it comes to foundations,” said Richard “Biff” Heringer, general manager/VP sales at EBI. “The responses always come back to the same three things: cost, time and capacity. The EB significantly saves in regard to cost and time, and for capacity, it typically improves bearing loads for piles by as much as three times. For tie backs and anchors, the increase can be more than seven times.”
Before expansion, the EB looks like a long tube of folded sheet metal attached to a steel pipe. The EB-equipped pile (typically placed at the pile toe) is inserted into the soil to the required depth (either through a pre-drilled hole by self-drilling or driving) and a grout pump inflates the EB through a high-pressure grouting conduit. After expansion, the EB appears similar to a large, water-tight metal balloon filled with grout.
“You use the EB product itself to gain the capacity you need,” said Heringer. “When you expand the EB, the soil around it becomes much denser and this densification, as well as the enlarged toe area, considerably increases the pile bearing or tieback tension resistance.”
The EB is so versatile that it can be installed vertically, horizontally or inclined, and is completely reliable as a rock-solid anchor. In addition to improving the bearing of piles, the remarkable adaptability of the EB also allows the product to be used for a variety of other applications, such as, but not limited to: anchoring/ground stabilization, tunnelling and buoyancy control.
EBI recently visited a project in Victoria, B.C., where engineers were struggling with tieback issues concerning extremely soft blue marine clay. Multiple conventional solutions failed, reaching tension resistances of no more than 50 kilonewtons (kN), forcing them to look at traditional 120-foot-deep rock socket installation, with major drilling and skipping issues, and a significant cost to achieve the required capacities.
Following initial discussions – and with serious scepticism from the client – EBI flew to B.C., to test the EBs on site.
“We installed three EBs to a depth of 30 feet and at a 25-degree inclination,” said Heringer. “In our first test, we achieved a tension resistance of 240 kN of load prior to the client’s reaction base failing. The decision was made to build a second base out of reinforced shotcrete. A week later we returned for the second test, where again the reaction base failed, but this time achieving a 380 kN tension load. Needless to say, they saw the potential of the EB and were thrilled about how it fully exceeded their expectations.”
Unlike traditional piling and boring that rely on trial and error, the EB allows for reliable quality control and verification of performance during installation by relaying information on soil strength and stiffness. By recording the grouting pressure versus the volume increase, information about bearing capacity and soil condition can be transmitted electronically.
Also unlike conventional piling and anchor systems, the EB allows for reliable quality control and quality assurance for each unit installed. By continuously recording the grouting pressure and volume during the expansion of the EB, it is possible to flag and correct any eventual anomaly and deviation from the expected soil behaviour at an early stage, reduce uncertainty and comply with foundation requirements.
“We know the precise volume and pressure of the grouting process,” said Heringer. “Because of this, each EB unit inherently acts as a pressure meter test that provides instant actionable feedback on a specific project’s soil conditions and, if you encounter any issues or problems, you will know about it in real-time. Nothing else out there can provide this kind of response.”
In spite of the EB’s positive qualities, it is not for every job. Should a project have underlying rock that is quite shallow and the contractor is not required to drill deeply, the EB may not be needed. However, if a project is experiencing undesirable soil conditions such as sand, silt or soft clays, or looking for the opportunity to shorten pile or tieback depth, this is where the EB can excel. The EB allows projects to continue on soil conditions that would be prohibitive for conventional piles, while increasing accountability and generating considerable savings for project owners and developers.
“Anyone who has used the EB has been amazed at how quickly the savings add up,” said Heringer. “The EB can save you much in terms of money, labour, time and equipment. You are also receiving a superior foundation since the EB is pre-loading the soil. It’s a win-win for your project.”
Moving forward, EBI is seeking to build greater product awareness throughout Canada’s construction industry and the company is happy to provide on-site tests for those wanting to see what the EB can accomplish. EBI will supply samples of the product, engineering guidance and on-site installation support (all at a subsidized or deferred cost) to demonstrate what it says is the future of deep foundation engineering.
“We are educating the industry here in Canada about the EB because we truly believe that this product will contribute to better Canadian foundation practice,” said Heringer.
Find out more information about the Expander Body by reaching out to Expander Body International through its website, www.expanderbodyinternational.com.