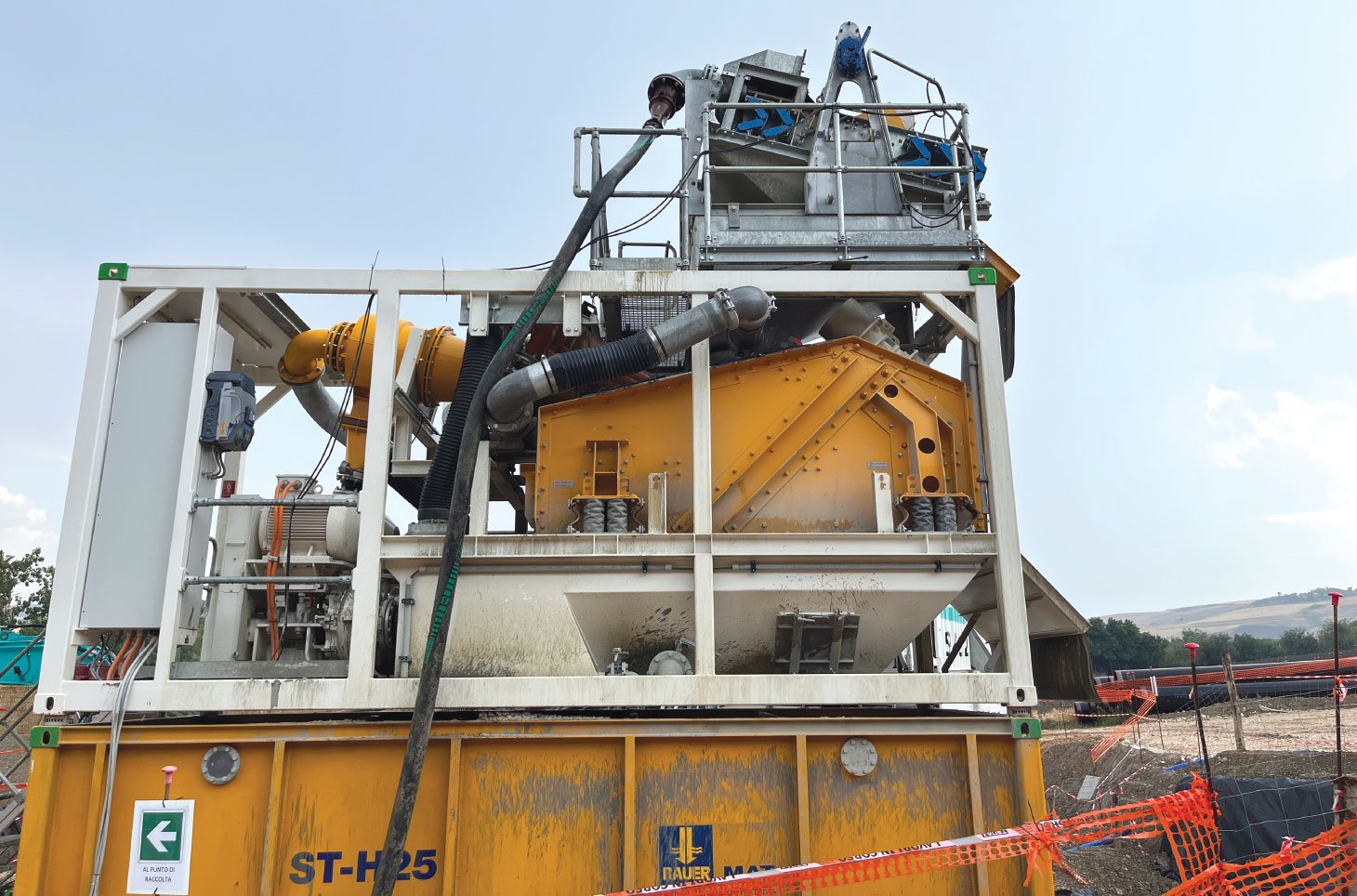
In the almost 60 years since BAUER Maschinen (Bauer) manufactured its first machine, the German brand has stood for excellence, performance, quality and – most of all – innovation. Bauer has added to this stellar reputation by introducing the next step in separation technology.
In June 2023, the Allgäu branch of Bauer launched the BE 600-C desanding system. The BE 600-C is the successor to the existing BE 550 model. It builds upon more than 30 years of delivering high-quality mixing and separation technology through BAUER MAT Slurry Handling Systems (a member of the Bauer Group).
The new BE 600-C is said by the company to “have it all.” The modular, two-stage system has a double cyclone for higher efficiency separation. It is completely contained (including the storage tanks and solids discharge, hose guide, all-round inspection and upstream coarse screen). For mobility, the BE 600-C can also be packaged within an optional CSC-certified container frame for easy delivery to the jobsite.
“Because all the components can be installed within the container frame, the transport, assembly and commissioning on site can be carried out quickly and easily,” said Kurt Ostermeier, head of product management for mixing and separation technology at Bauer. “We can install the complete desanding system and make it ready for running in under 12 hours, so one day is more than enough to get your system in place and put it to work.”
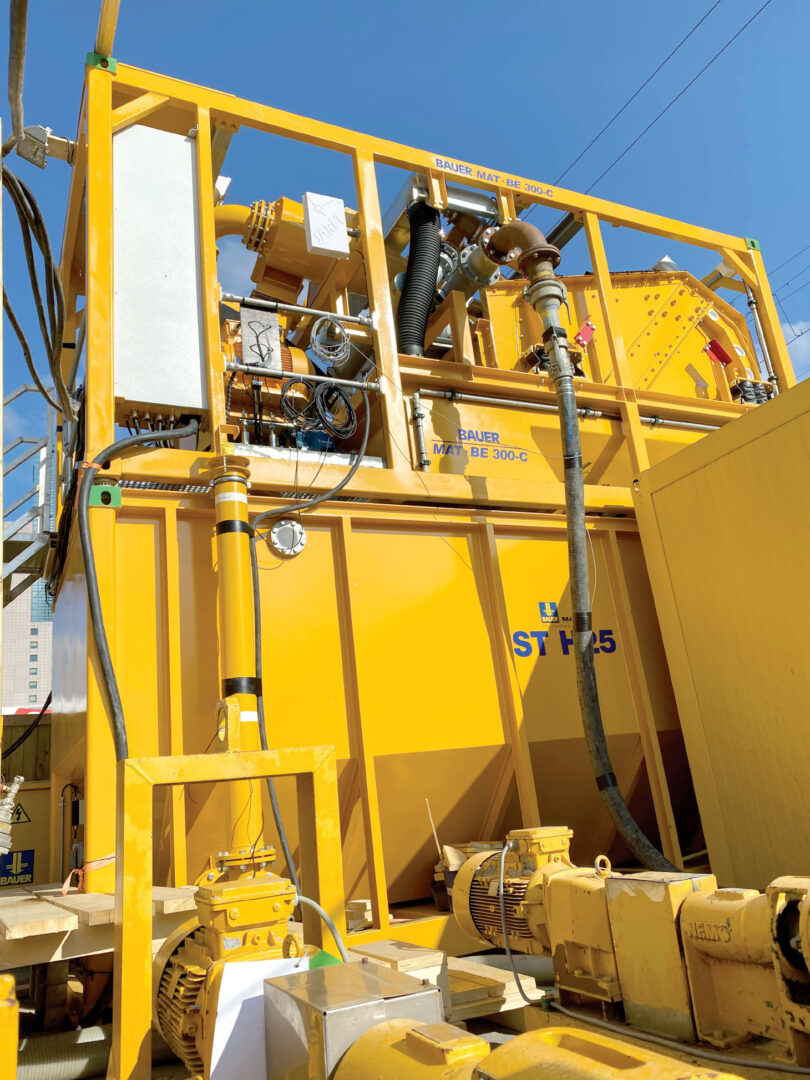
The BE 600-C features an impressive slurry throughput capacity of 600 cubic metres per hour and can process up to 120 tonnes of solids per hour, setting a new benchmark for desanding. The double cyclone also provides better cleaning of the slurry, resulting in less sand content in the cleaned slurry and fewer settlements in the storage tank underneath the desander.
The BE 600-C advantage
From large-scale cutting systems and tunnelling operations to smaller piling projects, the new BE 600-C is as flexible as its customers. Although the BE 600-C desanding system is relatively new to the marketplace, the technologies that underpin the new system are time-tested. The new unit comprises two reliable, standard BE 300-C desanding systems with optimized separation.
When called for, the BE 600-C can be easily split into two individual BE 300-C systems, with the upstream coarse screen being used to feed a single system. The modular advantage of the BE 600-C means that for smaller operations like piling – where a comparatively smaller slurry capacity is required – users can separate the system into two separate BE 300-C units and still desand up to approximately 1,200 gallons per minute.
“If you have a submersible pump with a capacity of about 2,000 gallons per minute, then you can use the BE 600-C as is,” said Ostermeier. “But if you need less capacity – say a piling project using 1,000 gallons per minute – then you can rely on a single BE 300-C rather than use the two together. It just depends on the capacity of what you want to feed into the desanding system.”
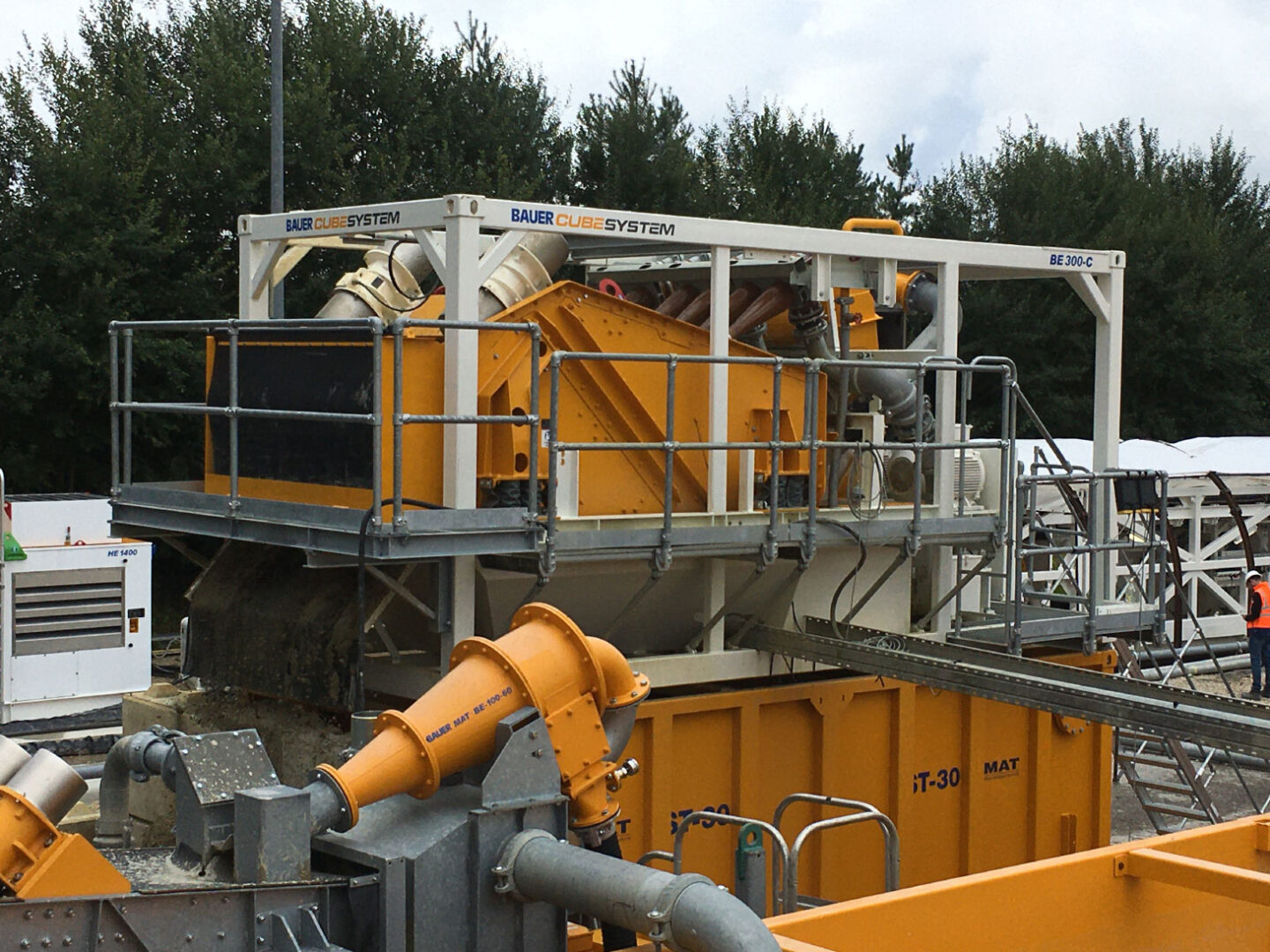
When the BE 600-C is split into two separate BE 300-C units, rather than run in tandem, it can also be used with or without the coarse screen in front for various applications. However, using the coarse screen can benefit projects encountering cohesive solids like clay. “Clay presents a problem in that, if it gets too dry, it can get stuck on the screen,” said Ostermeier. “But the coarse screen is slanted downwards with an adjustable angle. This means if we have a lot of clay, we can put the coarse screen on top to mitigate it by not allowing the clay to sit, dry out and become stuck. This is definitely a huge advantage of the BE 600-C.”
Another advantage to the new BE 600-C system is its relatively small physical space on the jobsite. As the pumps and desilters are self-contained and not outside as with standard double cyclone systems, the BE 600-C has a footprint of roughly 36 square metres and is a good fit for any project. “The size of the unit is a big advantage, and the BE 600-C is very compact, especially when compared to other desanders on the market,” said Ostermeier. “In addition, most of our competitors’ machines run at more than 200 kilowatts (kW) and as high as 250 kW. Our system, however, uses high-efficiency pumps that have a very low energy consumption when installed at 174 kW, which is becoming very important to society right now.”
The BE 600-C also has an optional tarp housing for noise protection, significantly reducing the sound power level from 95 to 93 decibels. The housing also serves as weather protection and heat insulation for regions dealing with freezing temperatures.
Digitalization and automation in focus
The BE 600-C also stands out in digitalization and brings users several new features. Each of the two BE 300-C systems has a 12-inch touchscreen display, and the entire system can be easily operated in ‘master-slave’ mode from just one screen. This allows the user to control either one or both BE 300-Cs from a single interface. The display also lets the operator see which parts of the system (conveyor belt, flow meter, accessories, etc.) are running and which are not.
An EWON router establishes a connection to the internet, meaning that all data – such as pressures, operating hours, power consumption and error messages – can be retrieved remotely. This enables Bauer service specialists to connect to the device quickly and easily – from anywhere in the world – and carry out a remote diagnosis if necessary.
“If you’re in America and are having a problem with your machine and need some troubleshooting from the BAUER MAT service department, we can plug into your machine and see what its message history is and then diagnose the issue from across the ocean,” said Ostermeier. “It also means that if we want to take control of the complete plant remotely, it should be possible.”
Digitalization and automation are ongoing processes that will continue to play a major role in the future. Bauer’s goal is to one day fully and permanently integrate its equipment into the cycle of a digital site. Going forward, the company wants to retrieve even more data on its machines’ wear and tear, and look into providing additional preventative maintenance – fixing a problem before it becomes a problem.
For more information about Bauer and the BE 600-C desanding system, contact the company at
bauer.de/bma.
Photos: courtesy of BAUER Maschinen