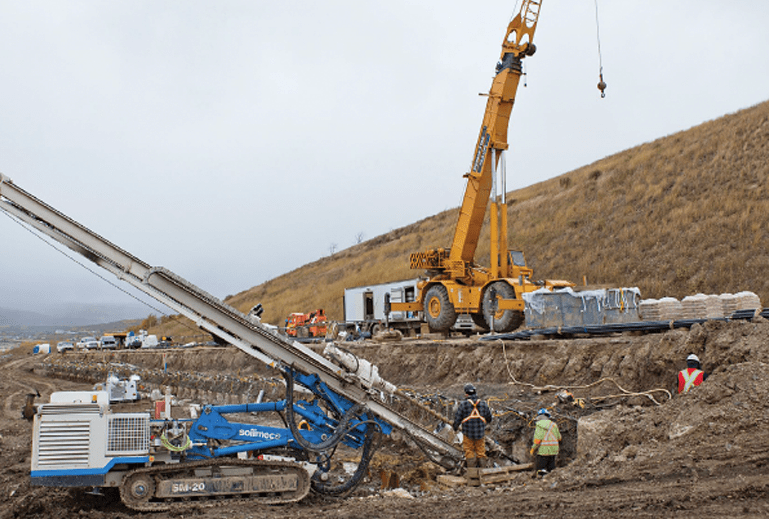
When Ian Hunt, president of Doublestar Drilling, purchased the company eight years ago, he believed there was a solid opportunity to grow the business. His vision was bang on.
Since that time, Hunt has tripled revenues, gone from four drill rigs to more than 20 drill rigs, and in October 2014, expanded the Edmonton headquarters to a 16,000-square foot stat-of-the-art facility. But the growth doesn’t stop there.
In 2011, Doublestar Drilling established a location in Regina to cover the Saskatchewan market, in a move Hunt calls, “very success-ful.” On May 1, 2015, they opened a third location in Calgary, complete with ten acres of property, after “aggressively pur-suing the Calgary market.”
That sort of growth isn’t fostered by being satisfied with the status quo. To Hunt, this translated to significantly adding to the company’s scope of services, which now include large diameter bored piles, every type of shoring, secant and tangent piling, in-house engineering, static load testing, segmental casing, mini-piling to get into tight spaces, vibra-tory hammer work, crane work and CFA drilling. In 2012, Doublestar expended its fleet into micropiling and anchor installation. The company currently has a fleet of nine micro-piling machines and a fleet of 10 mobile grouting operations.
Doublestar is also the largest belled pile contractor in Western Canada. “It’s a lost art, and not many do it,” said Hunt, “but this area of Western Canada is suitable for belled piles, which are dependent on soil conditions. We have the capability to install belled piles up to six metres in diameter.”
Putting employees first
Hunt is quick to credit much of the company’s success and growth to his employees. “What separates Doublestar Drilling is that we are non-union and most of our employees have 15-plus years with the company. Some have 25. I’m cognizant of the fact that these people want to be home in their own beds at night, and so we concentrate our work in cities. This philosophy has kept our labour force strong and loyal, and allowed us to grow the business in a market that’s sustainable.”
With a full-time safety department led by Willis Larose, the company’s health, safety and environmental director, Doublestar Drilling also boasts the lowest number of safety incidents in the industry, with a WCB assessment rate cur-rently 31 per cent below industry average.
“We have a very strict safety protocol,” said Larose. “We’ve created our own in-house safety program, and in conjunction, a state-of-the-art fleet maintenance schedule that operates off GPS. This allows us, from our head office in Edmonton, to know the hours on a machine, as well as when it was moving and when it stopped. Basically, it tracks everything an opera-tor is doing, and provides accurate data for preventative maintenance.”
“I’m cognizant of the fact that these people want to be home in their own beds at night, and so we concentrate our work in cities.”
Ian Hunt, President, Doublestar Drilling
The company also places a very high value on education. Extensive operator training includes both in-house equip-ment operator trainers, and employment of outside agencies. Additionally, senior crewmembers are paired with junior crewmembers.
“Statistically, and this is across Canada, workers are most prone to getting injured on the job between the ages of 18 to 25,” said Larose. “Our motto is ‘Worker taking care of worker,’ and we all take that responsibility very seriously. There are also weekly safety meetings, daily tailgate meetings and daily onsite risk assessment meetings to identify and control haz-ards. Attendance is mandatory.”
Notable projects
Doublestar Drilling is rapidly becoming the go-to company in Western Canada when it comes to undertaking challenging projects. One such case was the Calgary International Airport overpass expansion, which involved completing a critical slope of standard piling and shoring work, while solving the problem of completing two- to four-metre rock sockets in only 14 feet of headroom.
“Doublestar was an invaluable team member as they brought skills and expertise to the project that enabled us to complete the work in a timely fashion.” said Derek Lippai, Inc., International Facilities Project, Calgary International Airport. “There were areas of the project that required very unique equipment due to low overhead clearances. Doublestar took on the challenge and sourced out specialized equipment to meet the design and construction limitations to complete the work.”
The specialized equipment, designed for this type of work, is only made in Italy.
“Our motto is ‘Worker taking care of worker,’ and we all take that responsibility very seriously.”
Willis Larose, Health, Safety and Environmental Director, Doublestar Drilling
“Low headroom is not uncommon, however when you add the necessity of hard drilling, such as rock sockets, then it quickly narrows the equipment [options] down to only a few,” said Hunt. “We worked with our equipment supplier to modify the equipment to suit the specific requirements of this project. We also engineered a custom cage holder to place the rebar cage, as we needed to install 40-foot deep piles in only 14 feet of headroom.”
The Peace River Retaining Wall was another project that resulted in being awarded an additional contract.
“When Judah Hill on Highway 744 began to erode and slip into the Peace River Valley, Alberta Transportation enlisted us to complete all the drilled piles and anchor work,” said Hunt. “With tight timelines and strict budget guidelines, we began construction of the tie-back wall. Using specialized equip-ment, we successfully installed 260 double corrosion protection anchors on the hillside, ranging from 100 to 230 feet deep.”
The overwhelming success of the Peace River Retaining Wall’s Phase 1 resulted in Doublestar being awarded the contract for a larger, second piece of work, which included a technical assessment of the soil to determine equipment selection.
“As a result of the tests, we sourced and purchased a micro-pile drill to install over 280 anchors,” said Hunt. “At the end of the Peace River project, we had engineered and installed more than 43,000 linear feet of anchor systems, totalling 498 anchors, pressure grouted for over 600,000 kilograms of high strength concrete.”
Pile load tests are also an integral part of Doublestar’s rep-ertoire, and they are one of the few Canadian companies with this expertise to perform load tests above 20,000kn. Before construction began on Edmonton’s Roger’s Place, the com-pany was contracted to execute a pile load test. “The magnitude of the job resulted in a strategic partner-ship with Enerpac,” said Hunt.
The new system required the design and creation of six interwoven beams, each measuring six feet by 50 feet and weighing 35,000 pounds each, to control the four 500-ton jacks. “Together we designed and created a fully automated system capable of completing Canada’s largest load test to date – 14,000 kilonewtons,” said Hunt. “This new technology has increased our capacity, allowing us to take on Western Canada’s largest load test requirements.”
Hunt’s passion for piling continues to fuel the company’s quest for challenging projects.
“We believe in continuing education and being on the forefront of the latest technologies and equipment. In this vein, we sent project managers and field personnel to the International Foundations Congress & Equipment Expo (IFCEE) 2015 in Texas to see the latest developments. We also employ some of the best workers in the business, and are confident in our abilities to tackle any problem with an innovative solution.”