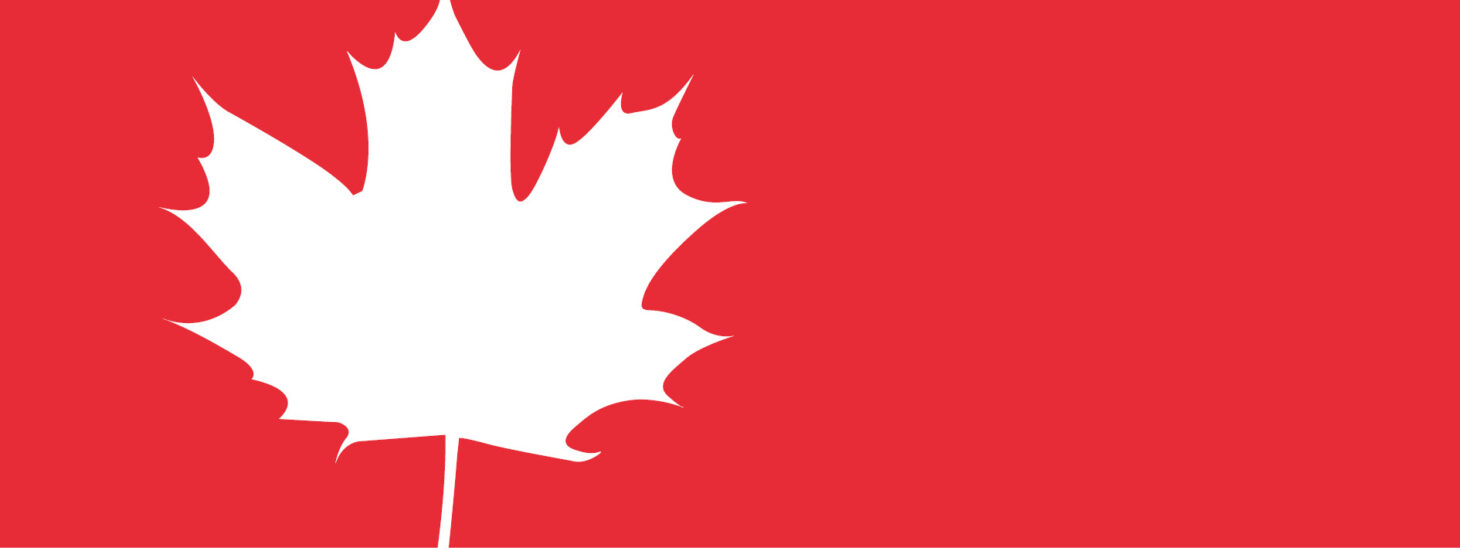
On Judah Hill Road, tied-back tangent pile walls stabilized the landslide mass and anchored the remaining strata
Two-lane Highway 744, known locally as Judah Hill Road, traverses along the southwest face of a hogback ridge separating the Peace River and Heart River valleys. Since it was built in 1984, active landslides have plagued this ill-fated, 2.5-km stretch of highway that rests above the town of Peace River, about 500 km northwest of Edmonton.
Keeping this road open is a serious challenge. Government of Alberta Ministry of Transportation (Alberta Transportation) managed and remediated 15 landslides grouped into eight areas along the ridge. These stabilization efforts included the use of realignments, timber pile retaining walls, mixed lime and gravel columns, anchored cast-in-place concrete retaining walls, geotextiles, surface drainage diversions, pumping drains, earthworks, lightweight fill and temporary portable bridges to span failed areas.
The most recent landslide, Sunshine Slide, first visibly impacted a 120-metre section of Judah Hill Road on May 3, 2013, when highway maintenance workers noticed transverse diagonal cracks in the asphalt. Both lanes of the highway continued to rapidly deteriorate, developing open horizontal gaps up to 250 mm (9.8 inches) wide, vertical drops up to 300 mm (11.8 inches) deep and the protrusion of previously installed large stone columns upwards through the existing pavement structure. Alberta Transportation closed the road due to safety concerns on May 17. By May 21, large sections of the highway had completely collapsed due to the shifting earth underneath the roadbed.
Even though it’s in a relatively remote area, Judah Hill Road acts as a vital lifeline to the town of Peace River for the thousand cars that pass along it per day. Therefore, Alberta Transportation decided that permanently closing the highway or building an alternate highway outside the landslide area weren’t viable options.
Instead, Alberta Transportation moved quickly to provide a temporary fix so at least one lane could be reopened to traffic. Geotechnical engineers determined the landslide failure plane and remediation plan. Within two weeks, emergency grading work was performed and a steel pipe was installed to divert highway surface water runoff past the landslide area.
As a long-term solution, tied-back tangent pile walls were selected as the best remediation method to stabilize the landslide mass and anchor the remaining strata. Two tied-back walls were constructed about 300 metres apart from each other just below the damaged sections of highway. Both walls were installed by Doublestar Drilling using Soilmec SM-14, SM-20 and SR-30 rigs. Once the walls were complete, three layers of expanded polystyrene geofoam blocks were used as backfill to reconstruct the highway embankment and reduce the soil pressure on the walls.
Challenges and solutions
Performing stabilization work on a sloping hillside within an active slide area and with limited access was extremely challenging. The landslide had the potential to continue to move downslope. Furthermore, this demanding work occurred during an abnormally cold Alberta winter at temperatures as low as -30 degrees Celsius (-22 degrees Fahrenheit). Safety was a great concern for the people and equipment.
Subsurface conditions at the site consisted of up to four metres of firm clay fill underlain by a hard, high-plasticity clay interbedded with silt and sand layers to depths of about 20 metres, which was underlain by very hard clay till. The landslide failure plane was primarily located in the upper high-plasticity clay layer about 12 metres below the ground surface where the highway traverses the hill. The groundwater table was about nine to 10 metres below ground surface, and above the failure plane. These soil conditions, typical of slide areas, resulted in challenging drilling conditions.
The proper selection of equipment and methods was important to the success of the project. A Soilmec SR-30 drilling rig was used to install both tangent pile walls, and Soilmec SM-14 and SM-20 drilling rigs were used to install all tiebacks. These rigs were selected to overcome the working space restrictions due to the sloping hillside and active landslide area.
Cranes were also deployed to help lift and move the tieback anchor bars. And temperature-controlled, enclosed grout units were crucial for ensuring continuous operations throughout the frigid winter.
Tangent pile walls
Doublestar Drilling constructed two continuous tangent walls, with piles penetrating into the hard clay till, in order to guard against the possibility of a deeper slip surface developing at some time in the future. Both walls were installed parallel to the curving highway on the downhill side.
Continuous tangent pile walls were comprised of a series of reinforced concrete piles in which adjacent piles touched without a gap or overlap. These cast-in-place, reinforced, straight-shaft concrete piles were constructed, and then secondary piles were constructed in between once the primary piles reached sufficient strength.
The first continuous tangent pile wall was constructed using 108 reinforced concrete piles with a diameter of 1.1 metres and depth of 18.3 metres each. In the original geotechnical design report, this was the only tangent pile wall proposed.
However, there was subsequent concern about the groundwater displaced by the first tangent pile wall, so it was decided that additional support from a second tangent pile wall was necessary. The second continuous tangent wall was constructed 300 metres south of the first wall. It consisted of 72 reinforced concrete piles with a pile diameter of 1.2 metres and depth of 18.3 metres.
Tieback anchors
Ground anchors were also required to supplement the shear resistance provided by the piles. The anchors were bonded deep into the ground behind the failure plane, beyond where any future landslide activity was expected to originate. Doublestar Drilling used two Soilmec SM-14 microdrilling rigs and one Soilmec SM-20 anchoring rig to meet the geotechnical design requirements.
For each tangent pile wall, two or three rows of tieback anchors were installed. Using a special coring bit to drill through the reinforcing cages, full-length holes were drilled through the soil and into the bond zone. A combination of augured, cased and hollow-stem drilling methods were required to deal with the sloughing conditions. For instance, casings were required for some holes due to groundwater seepage and sand pockets. The bond zone was limited to 12 metres in length and 0.2 metres in diameter.
Double-corrosion protected, 32-mm threaded bars were inserted into the holes above and through the tangent walls, and then the holes were filled with high-strength grout. Multiple stages of post grouting were required for this anchor installation to eliminate voids. The lengths of threaded bar above the bond zone were also covered by bond breakers to eliminate load transfer above the board zone.
After installation, the anchors were stressed to prove capacity. Enerpac 60-ton jacks were attached to the threaded bars with a bracket, set to a predetermined tension and the tension load was held for a set amount of time while anchor displacements were measured.
A continuous, reinforced concrete waler or pile cap was then installed along the top of each continuous tangent pile wall. These 2.2-metre-thick concrete walers were used to secure all tieback anchors and transfer loads evenly.
For the first tangent pile wall, a total of 216 tieback anchors were installed in two rows. The upper row of anchors were tensioned and locked off 0.35 metres below the top of the waler and inclined at 25 degrees to horizontal. The lower row of anchors were tensioned and locked off 1.05 metres below the top of the waler and inclined at 30 degrees to horizontal. The upper row of anchors extended 40 metres and the lower row of anchors extended 35 metres from the centerline of the piles.
Similarly, three rows of tiebacks were installed in the second tangent pile wall: the upper row at 23 degrees, middle row at 28 degrees and lower row at 32 degrees to horizontal. A total of 322 anchors were installed in this second tangent wall. These anchors were spaced 0.5 metres apart, each providing a design load of 192 kN (43 kip) that supplemented the design load of about 250 kN (56 kip) provided by the pile wall.
Tying up the job
Doublestar Drilling installed the first tied-back pile wall at Sunshine Slide between December 2013 and June 2014. The second tangent wall began in April 2014 and was completed in April 2015.
During the entire Peace River project, Doublestar drilled more than 25 linear kilometres to install all piles and anchors. The installation of the 538 tieback anchors required 21 trucks with a total of 357 pallets of grout.
Despite the challenging subsurface, access and weather conditions, both tangent pile walls were constructed without any safety incidents. All anchors passed the acceptance tests and post-tensioning criteria. Both lanes of Judah Hill Road are now open and busy.
{gallery}peaceriver{/gallery}
Photos courtesy of Doublestar Drilling, Queen’s University and Alberta Transportation
This article originally appeared in the July/August 2015 issue of Deep Foundations magazine, the flagship publication of the Deep Foundations Institute (www.dfi.org). It is reprinted with permission.
{fastsocialshare}