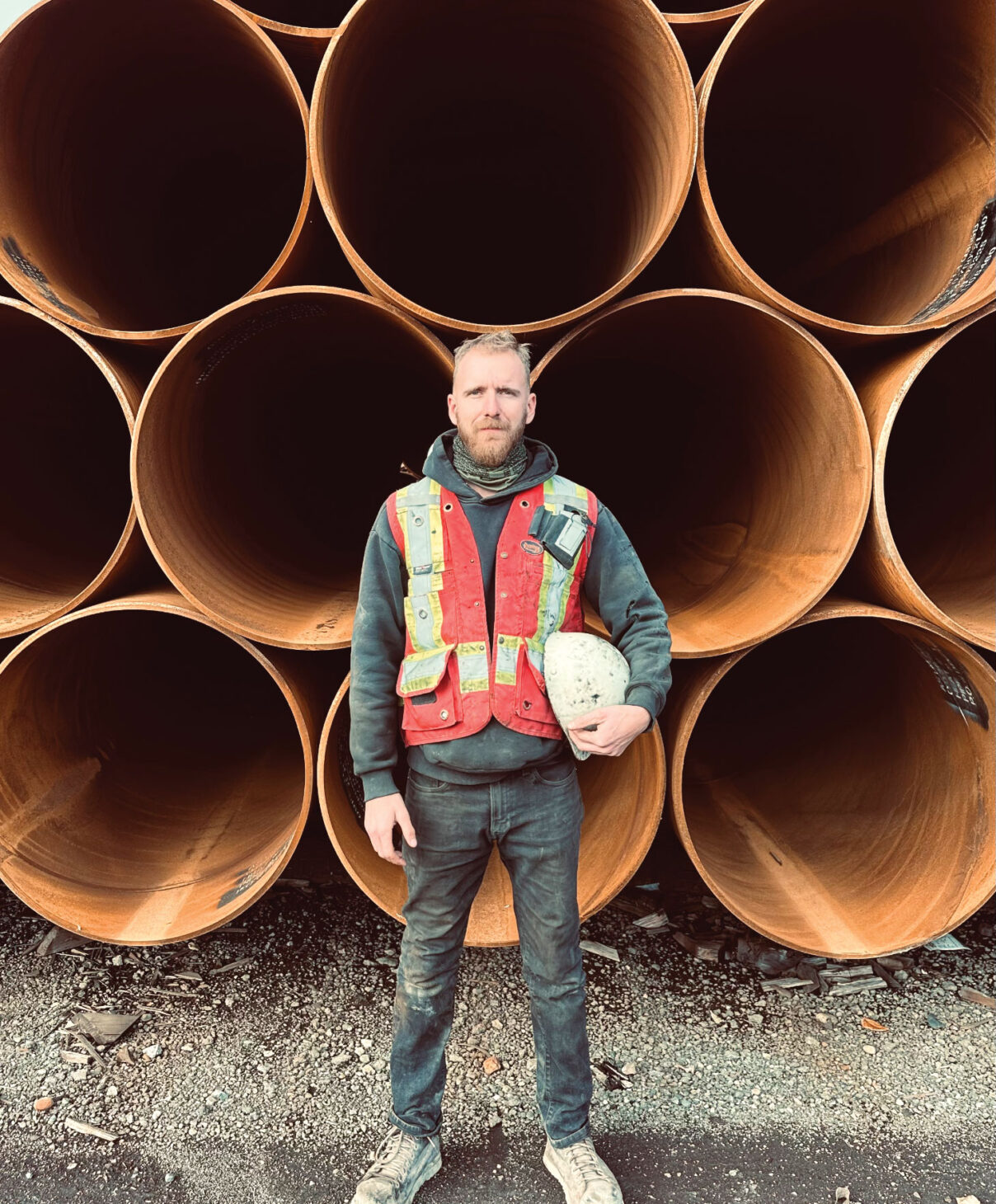
An industry specialist with 11 years of deep foundation construction experience, it’s no surprise that Anthony Calnan has in-depth knowledge of secant pile installation and best practices – in addition to site layout and initial planning, guide-wall design and installation, project planning and critical path evaluation, co-ordination of drilling rigs and pile placement sequencing.
If this isn’t enough, Calnan – a project foreman at Henry Foundation Drilling Inc. in Langley, B.C. – is also experienced with sheet pile walls, cells and cofferdams, and the installation of driven piles with hydraulic impact, diesel-driven and conventional installation methods.
Calnan opens up about his extensive career, the challenges that keep him motivated and what he thinks it takes to succeed in deep foundations.
Where are you from, and how did you begin your career in the deep foundation industry?
Anthony Calnan (AC): I’m from the small hamlet of Vernonville, Ont., a great rural community with an ever-growing population of around 50 residents. It sits atop the oak ridges with a distant view of Lake Ontario.
Growing up, summers consisted of stacking what seemed like endless square bales on the local farm. I branched off from that into a local residential construction company, building houses, operating equipment and pouring concrete. This led to my interest in Fleming College’s Resources Drilling and Blasting program and, ultimately, opened the door to the [deep foundations] industry.
You’ve gained extensive experience in secant pile installation, guide-wall design and more. What excites you most about working with deep foundations?
AC: It’s a constant challenge. Almost every time you’re ahead, you’ll be presented with another challenging obstacle. The industry is [always] evolving, so you need to stay focused and stay sharp. Remember what worked well in the past – but more importantly, don’t forget what didn’t produce positive results in the past.
What do you like most about being a project foreman?
AC: My favourite part of working [at Henry Foundation Drilling Inc.] is the abundance of challenging projects and having a solid crew of teammates to complete them with. In the last two years, I’ve had more exposure to the driven pile world and walked into an opportunity to develop and work with one of best crews in the industry.
I want to give a big shout-out to my main site crew for our last few projects. A big thank you to Scott Roberts, Daniel Arguedas and John MacArthur! And let’s not forget the best welding crew out there – Andrew Bartfai, Dane Szakacs and Brandon Purcha.
I’ve also always been fortunate to have excellent project managers. Jared Poirier and Cesar Sheen are just a couple names that come to mind when I think of people who have excelled in this area.
How do you approach the initial planning and layout for a site to ensure the project’s success?
AC: It’s important to approach this phase with major emphasis on just how critical this step is. A well-thought-out, organized jobsite with a logically sequenced scope of work is probably the main determining factor of a successful project. Even more importantly, this ultimately contributes to a much safer jobsite, as well.
Lately, we’ve been using retail drones for initial layout phases. A bird’s eye view of the jobsite is a great tool for planning a site layout. You can optimize the placement of materials that way. The drones are helpful for creative marketing and flashy social media posts, but they also play an important role in our overall site layout.
What’s the biggest challenge you’ve faced in co-ordinating a deep foundations project and how did you overcome it?
AC: The biggest challenge to date – by a large margin – was managing the concrete order and placement at the new St. Paul’s Hospital in Vancouver, B.C. [We installed] almost 900 one-metre-diameter secant piles with an average depth of 20 metres. At times, five drill crews were working simultaneously.
At first, we tried to divide up orders and placement between multiple people to break it down and simplify. However, this had almost the opposite effect, causing more confusion. Placement is the driving factor to high productivity on a production secant pile job. You need concrete delivered on time, within spec, and a concrete truck backed up in view of the drill rig operator. The concrete shoot has to line up with the centre of the piles, just swung off to the side. The second the operator swings the auger clear of the sectional casing on the last pass, you should be pouring concrete. That’s the level of efficiency you need to create.
We learned that a single point of contact was best for managing the logistics of concrete for the project. Stumbling into this position myself, I was at the front of a major learning curve. Five drill crews were working – all with varying pile completion times – spread across a massive jobsite. And on top of that, there were varying depths and concrete volumes from one pile to the next.
We managed to maximize delivery with every single truck. The real challenge was providing the drilling sequence to multiple crews, adjusting and dividing the concrete between crews and piles accurately. We also had to ensure concrete was discharged within the allotted timeframe, and the trucks were on and offsite as quickly as possible in a safe manner.
How do you handle unexpected site conditions, such as poor soil quality or water infiltration, when planning and executing a foundation project?
AC: At the start of every project, there is going to be a quick learning curve. You notice trends so you can almost predict what is coming. You become familiar with certain soil conditions. Plan for the worst. Hope for the best.
You also have experience installing driven piles with hydraulic and diesel impact hammers. What factors go into choosing one method over another?
AC: Essentially, equipment needs to work. Generally speaking, our crew is outside a practical range for mechanical support from the main office or yard. The simplest and most reliable system will have clear advantages.
We’re playing with a serious amount of energy transfer here. Safety and reliability are often the deciding factors in one system over the next. Drop hammer and diesel impact hammer are often chosen for their reliability and proven performance. However, with advancements in hydraulic impact technology, it will likely become the frontrunner.
What do you find most rewarding about your role?
AC: Watching people grow and your crew advance. We’re constantly striving to be better, safer, and to minimize downtime, improve systems and improve methodologies.
It’s also very rewarding to start a project and, as you close in on the finish line, you are two to three times more efficient. Even a reduction in the amount of energy to complete a task is a big win.
What qualities do you think are essential for someone working in deep foundations?
AC: It takes grit at the entry-level, so you need to be tough, have a thick skin and adapt to working outside year-round. You need situational awareness and not be afraid to get dirty.
At the operator level, you need to direct your crew on the task at hand. You need to be patient and level-headed. It’s your responsibility to train and keep the people working around the equipment safe. At the supervisor level, you need to lead by example. Lead your crew and create the best working conditions possible for your team. Look out for them and they will look out for you.
In your opinion, what’s the biggest misconception people have about working in the deep foundations industry?
AC: The entire industry is still largely unknown and there isn’t really a specific pathway into it. For the most part, there seems to be an assumption that deep foundation construction is a branch of oil and gas drilling. Our work is always buried and there is a general lack of understanding when it comes to ground improvement, deep foundation drilling, shotcrete/shoring and pile driving. It’s not something you’re looking at every day.
What advice would you give to someone just starting out in the deep foundations field?
AC: Learn as much as you can. The sky is the limit. You will get as much out as you put in. Each new skill means consistent, meaningful employment, with a steady growth path.
The most valuable people have a multifaceted skillset. For example, a drilling rig apprentice that can front end well, but also operate support equipment, complete basic weld repairs and help a mechanic with set-up will be the first person getting seat time.
Employment in the industry can be volatile. Don’t get discouraged if you are laid off or cut back between projects. It’s not always a reflection of your skill or work ethic. Sometimes it’s just a financial calculation. Stick with it.