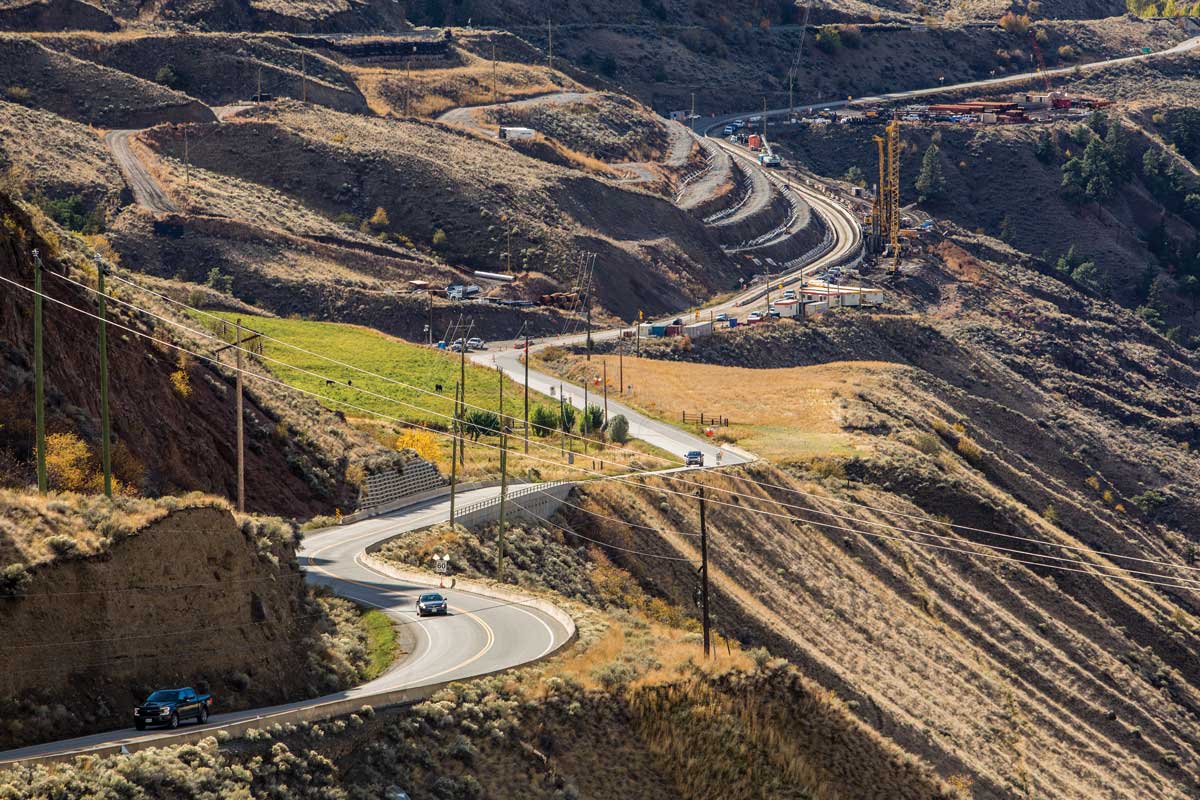
British Columbia’s Highway 99 is the most direct connection between Lillooet and Kamloops and plays a critical role in supporting the regional economy. Approximately 1,600 vehicles travel along this highway every day, of which nearly 20 per cent are heavy trucks delivering vital goods.
Highway 99 is also home to the Ten Mile Slide (TMS), an infamous 300 metre stretch of highway located within Xaxli’p First Nation (approximately 17 kilometres northeast of Lillooet) that has experienced ongoing slide activity for several decades. The movement of earth at TMS has been well-documented since 1988, with the slide crest retrogressing up the hill an average of seven metres per year, and six to seven millimetres of movement occurring every day at the highway itself.
“Ten Mile Slide is a very active landslide that moves slowly every day,” said De Wet Neethling, project coordinator at Henry Foundation Drilling Inc. “In addition, different zones within the slide had been identified that move at different rates. These zones are further affected by precipitation and the slide movement rate will typically increase during – or shortly following – rainfall or rapid snowfall events. We have drilled in some of the toughest conditions known to man, and this project was no exception.”
Over the last two decades, British Columbia’s Ministry of Transportation and Infrastructure (MoTI) has invested between $240,000 and $2.3 million annually to maintain the highway through this unstable area.
Recognizing that something needed to be done, MoTI kicked off Phase 1 of its TMS stabilization project in 2016, to improve the long-term safety and reliability of the highway, which included the installation of 44 soil anchors along the TMS. Phase 1 was completed in February 2019.
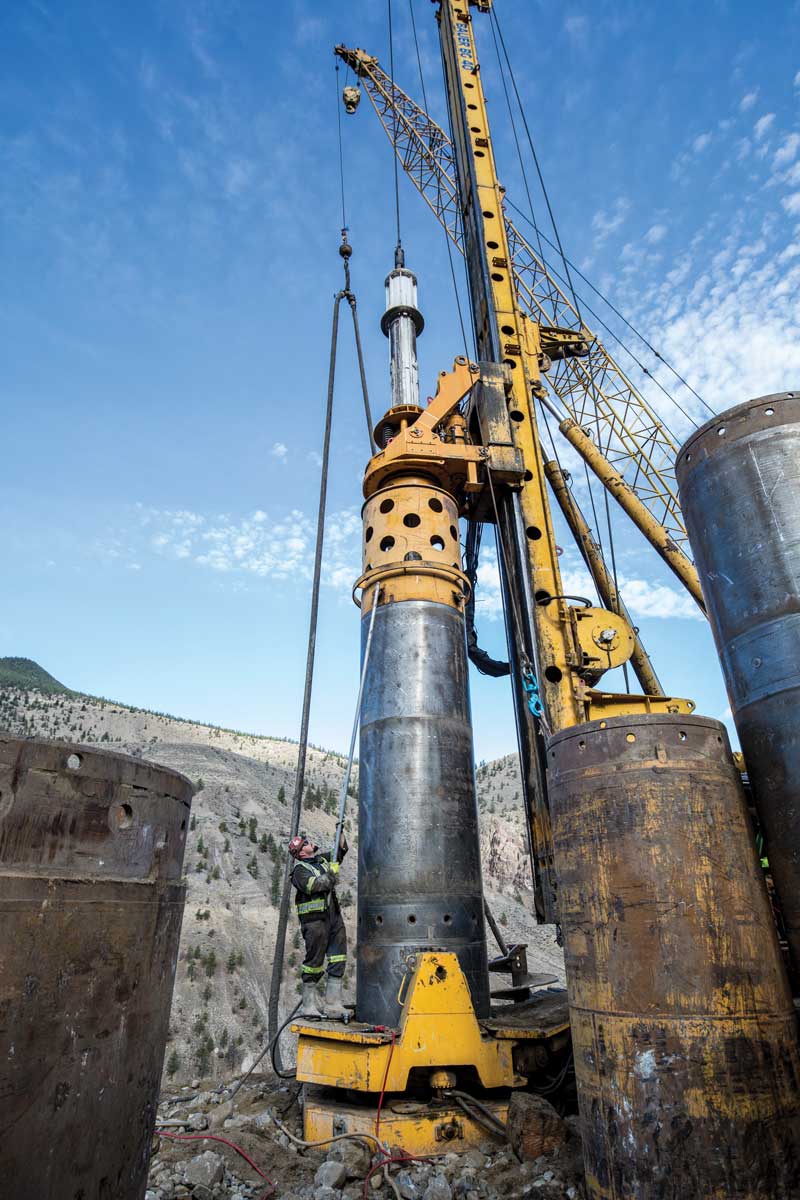
The $60-million Phase 2 portion of the main stabilization project was then awarded to general contractor, Flatiron Constructors Canada Limited, which seeks to permanently stabilize the highway through the installation of tied-back concrete and composite piles below the highway and 200 soil anchors above the highway. This work will lead to the eventual renewal and reconstruction of Highway 99 to two lanes with a guardrail.
In May 2020, Langley-based Henry Foundation Drilling Inc., was brought onto the project to install a slide wall that would slow the gradual movement of the slide. With more than 30 years experience in the drilling business, Henry Drilling has built a reputation for specializing in deep foundation services, including cast-in-place drilled piles, continuous flight auger piles, soldier piles and lagging, secant pile walls, tangent walls, rock drilling and gas extraction wells at landfills. At the TMS, Henry Drilling installed a total of 148 tangent piles – 49 composite piles (permanent steel-cased piles filled with rebar and concrete) and 99 concrete piles (temporarily-cased piles filled with rebar and concrete) – that were 1.5 metres in diameter and ran approximately 21 metres deep.
“We have a very knowledgeable and creative team of office and field staff that we can draw from to overcome any obstacles and challenges,” said Neethling. “We really enjoy getting stuck in and getting the tough jobs done – it’s a major source of pride for us.”
The pile wall installed by Henry Drilling included composite piles with a permanent pile shell of welded steel pipe and concrete piles with temporary steel casing that had to be removed as the concrete was placed. As the landslide was slowly – yet constantly – moving, the construction sequence required the composite piles to be constructed first, with the infilling concrete piles to follow. The pile shell protected the concrete within the composite pile from ground movement while it set.
“We have drilled in some of the toughest conditions known to man, and this project was no exception.”
De Wet Neethling, Henry Foundation Drilling, Inc.
“The composite piles are designed to provide enough resistance (without tie-backs) to stop slide movement. This allows for the installation of concrete piles into ground that is not significantly moving, and without the need for a protective steel shell,” said Neethling. “There were also restrictions on vibratory methods and impact driving for the installation of steel casings for piles in order to avoid damaging the piles while the concrete was setting.”
The landslide movement also caused deterioration, including downslope movement, crack formation and settlement of the highway and all access benches downslope from the completed stabilization measures within the slide limits. Significant deterioration of the highway, as well as the ground uphill of the pile wall continued to occur until the piles were constructed. Downhill of the pile wall, deterioration continued to occur throughout the duration of the project, including during tie-back anchor, waler and cap beam construction.
The TMS presented several challenging factors related to geology and site location that made this a unique project for Henry Drilling. The site featured a two-metre-thick shear zone at the base of the slide, across which all displacement occurred, and when the pile and tie back anchor drill hole penetrated the basal shear zone to enter the undifferentiated glacial sediment, the drill casing and other tools became vulnerable to a higher-than-normal risk of becoming stuck in the ground because of the differential displacement. In addition, the drilling was extremely difficult because of the significant presence of large boulders – some up to six metres in diameter.
In November 2019, there was a significant slide, prompting the project engineers to change the overall project design. Due to this, the drilling pad was cut down to approximately five metres below the existing highway, which effectively boxed Henry Drilling in; with the highway on one side (and above) and the canyon on the other. All of Henry Drilling’s equipment was then required to operate in tight quarters and, with so many machines and personnel working in a congested space, safety became a major component of the daily agenda.
“Conditions were unpredictable at the best of times, so we were constantly re-evaluating and adjusting to the changes,” said Neethling. “We had to work extra hard at keeping everybody safe and things happened a little slower than initially planned; but that is natural when you consider the extraordinarily tough drilling conditions. We worked closely with Flatiron and the MoTI to come up with viable solutions to the many challenges we faced.”
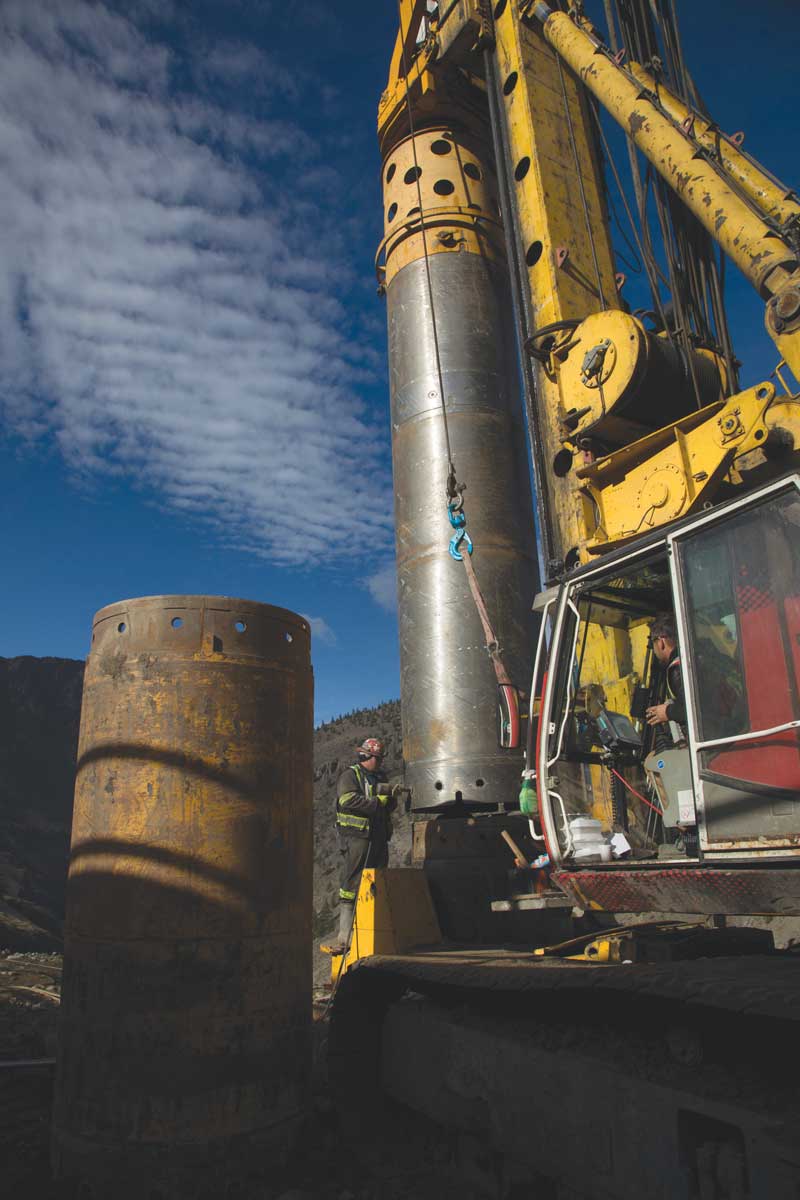
For this project, Henry Drilling made use of two Bauer BG 40 drill rigs, two 1.5 metre-diameter oscillators and three crawler cranes. In addition, the company had mechanic and welding bays where it could repair most tooling and equipment on the fly.
The project also required the use of Thermal Image Profiling (TIP) as part of quality assurance, which consisted of five equally spaced TIP wires installed inside the rebar cage, running the full length of the cage and then, after the concrete was placed, Henry Drilling would attach a data logger to each wire.
“As a by-product of hydration, the concrete emits heat and the TIP wires would send temperature readings to the loggers, which was then used to interpret what was going on inside the pile,” said Neethling. “It would tell us things such as if there was any sloughing that occurred, if we had enough concrete cover or if there was any segregation of concrete. From what we understand, this was the first time this technology was used here in British Columbia.”
Due to the sensitive nature of the area, there was a considerable amount of attention paid to the overall environmental impact of this project. There was a requirement for a bi-weekly environmental monitoring inspection, as well as the presence of an on-site environmental monitor who was provided by the Xaxli’p First Nation.
In addition, an environmental consultant was hired by the general contractor to draw up a Construction Environmental Management Plan, which included a wide variety of segmented mitigation plans, such as an Environmental Monitoring Plan, Clearing and Grubbing Plan, Noxious Weed Management Plan, Erosion and Sediment Control Plan, Storm Water Management Plan, Construction Waste Management Plan, Air Quality and Dust Control Plan and a Wildlife Management Plan.
“Eighteen wildlife species-at-risk were identified as potentially present in and around the project area, and we were given training on the wildlife in the area, as well as how to treat them,” said Neethling. “Our drill pads were also constructed from the native soils, using the spoils from the piles to build up any pads where required.”
While construction is expected to conclude later this spring, MoTI staff will continue to monitor the slide for approximately two years before paving the new section of two-lane highway.
Photos courtesy of Brad D Kasselman