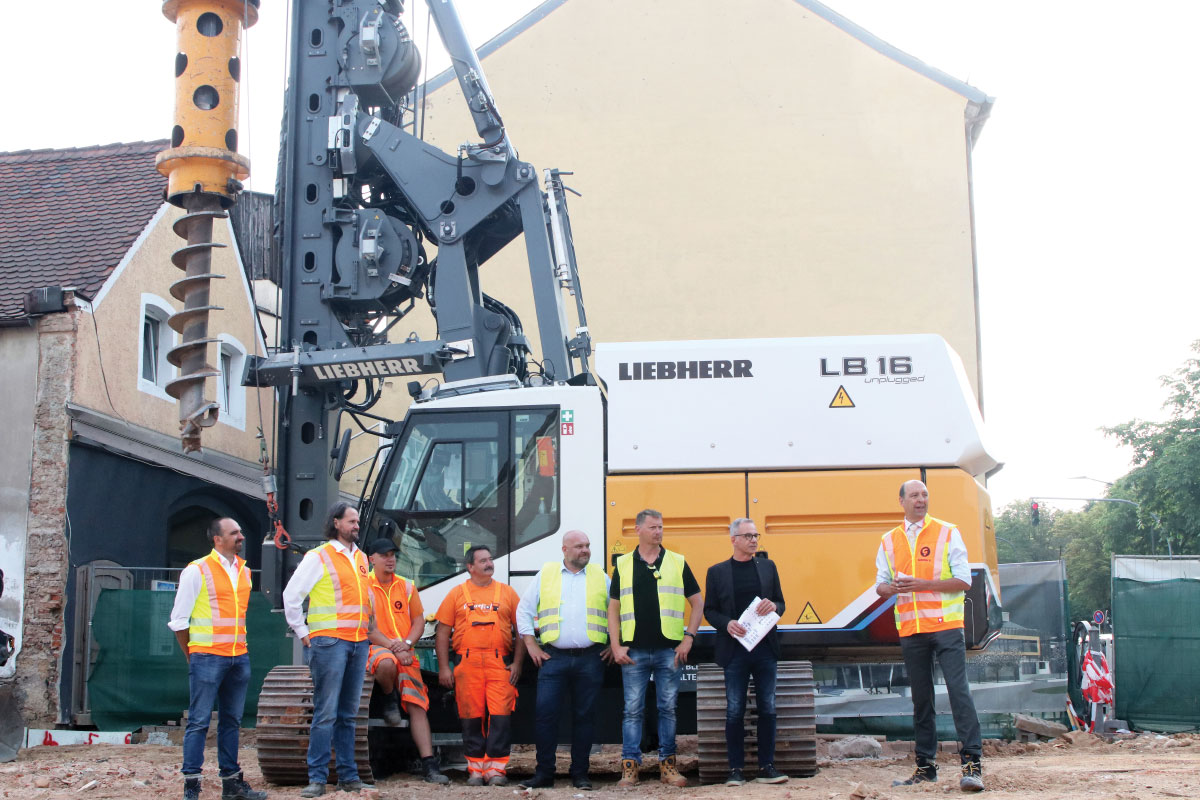
The progressive effects of climate change require a fundamental and urgent change. Politics and industry are expected to develop solutions that can contribute to significant reductions in CO2 emissions. Years ago, the automobile industry took a pioneering role and began to change their fleets to an increasing number of vehicles with alternative powertrains. Construction machine manufacturers shouldn’t miss out on taking part in this process. Recent research found out that a single 14-tonne diesel excavator emits 32 tonnes of CO2 per year – a passenger airplane has to travel the distance from Munich to Berlin 150 times to cause similar emissions (www.traktuell.at).
The deep foundation industry can contribute a lot to carbon emission reduction as it is mainly machinery-dependent work by its very nature. Manufacturers can play an important role in the development of battery-powered machinery and offer the market an additional option other than powertrain technologies.
Nature Drill hosted the world’s first comparison test between a battery-powered and a diesel-powered large rotary drilling rig to inform about the differences. The performance test on a deep foundation happened at a construction site in Weiden, Germany, and provided crucial information regarding the performance of an electric drilling rig compared to its conventional diesel-powered counterpart.
In August 2022, the battery-powered drilling rig Liebherr LB 16 Unplugged was sent to a competition with the diesel-powered Liebherr LB 16. Both rigs performed the same tasks under identical conditions, such as soil, drilling depth, drilling tools and equipment operator.
The test focused on identifying the performance and economic efficiency of both rigs under the conditions of a real-life construction site. The following aspects were taken into account for both machines:
- Battery management
- Drilling performance
- Economy
- Energy consumption
- CO2 balance
- Heat emission
- Noise pollution
Testing procedure
To ensure comparability, both devices drilled piles with the same depth using the Kelly drilling method. One single working cycle included:
- Drilling two pile holes of 6.8 metres (22.3 feet) each
- Pouring concrete up to ground level
- Dragging of casings
Since a power supply of 125 amperes (A)/400 volts (V) AC was not available on site, the Liebherr LB 16 Unplugged had to be charged with 63 A/400 V AC instead. The rig was connected every day after the end of the shift and charged until the shift’s start the next morning. This was to ensure that the Liebherr LB 16 Unplugged was ready to be used for a full workday without additional loading operations. Likewise, the Liebherr LB 16 diesel rig was re-fueled daily after the shift’s end, up to the maximum tank level.
The following data was recorded to allow conclusions about drilling performance, profitability, CO2 balance, battery management, heat emission and noise pollution:
- Date
- Temperature and weather
- Pile number
- Battery charge (at the start of drilling)
- Battery charge (at the end of drilling)
- Battery consumption in per cent and kilowatt hour
- Consumption per drilling metre
- Temperature of battery pack
- Air conditioning
- Start time of drilling
- End time of concreting
- Production time and total working time
Battery life for the Liebherr LB 16 Unplugged
According to the manufacturer’s specifications, the rig with a fully charged battery is supposed to provide an operating time of up to 10 hours. Unfortunately, that was not the case. Test operators determined an average battery duration of seven working hours per shift (see Table 1).
The average charging time for the Liebherr LB 16 Unplugged in this practical test was 14.5 hours. The reason for this non-specific long charging time was the insufficient power supply of 63 A/400 V AC, while a 125 A/400 V AC power supply is ideal. Even with longer charging times, some days weren’t sufficient to fill up the battery pack to a level of more than 95 per cent. Therefore, a charging time of 15.5 hours must be anticipated for a power supply of only 63 A/400 V AC (see Table 2).
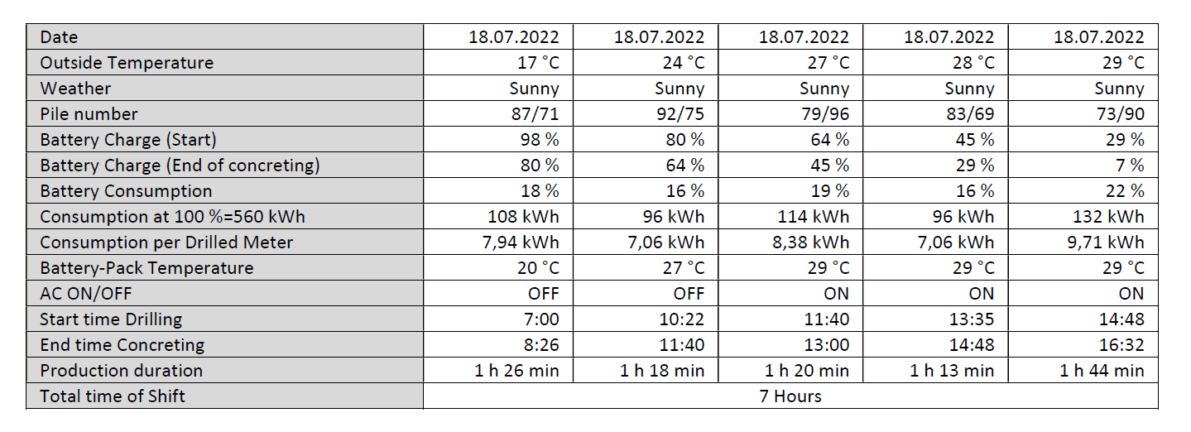
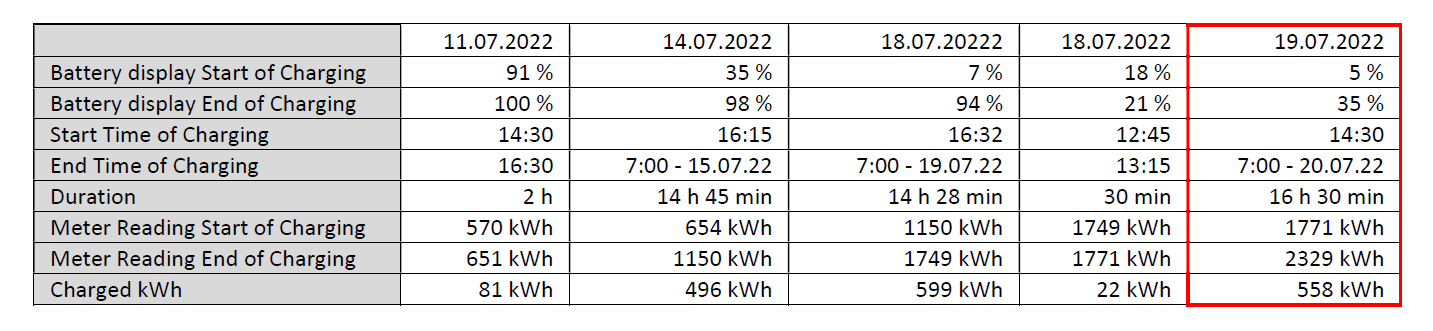
Drilling performance
Based on the reported data, an average output of 68 drilling metres (223 feet) per shift was recorded for the Liebherr LB 16 Unplugged – a worse performance compared to the diesel-powered LB 16. This is likely due to the limited capacity of the battery during the test period and a repair on the hydraulic quick-coupler.
On the other hand, the conventional Liebherr LB 16 performed 81.6 drilling metres (268 feet) on average. In comparison, the diesel device is ahead of its electrically powered competitor, the Liebherr LB 16 Unplugged, with a drilling capacity of about 17 per cent.
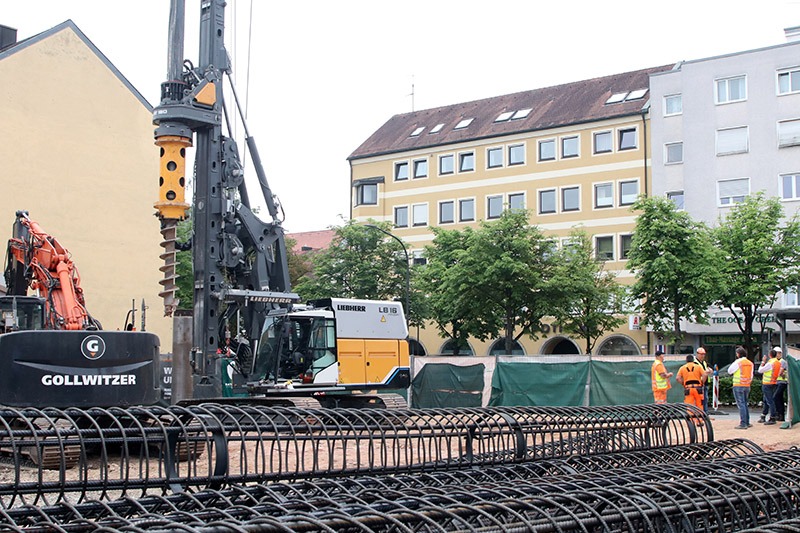
Profitability
One of the most important aspects for the decision between the emission-free machine and its conventional counterpart is cost-effectiveness. A first indication of this is provided by the operating costs based on the determined daily outputs (see Tables 3 and 4). Purchase and maintenance factors have not been considered.
The figures based on drilled metres indicate that the Liebherr LB 16 Unplugged is 27 per cent more economical than the diesel-powered drilling rig. Though the daily output is lower compared to its diesel counterpart, the electricity-diesel ratio relativizes this fact.
At this point, it should be noted that the basis of this comparative figure is solely the regional price for electricity and diesel at the time of testing. The purchase prices for diesel in Germany are subject to considerable fluctuations almost daily, which makes it difficult to determine this comparative value even in the medium-term. However, this comparison is sufficient as a tendentious proof of an economic advantage of the battery-powered Liebherr LB 16 Unplugged.
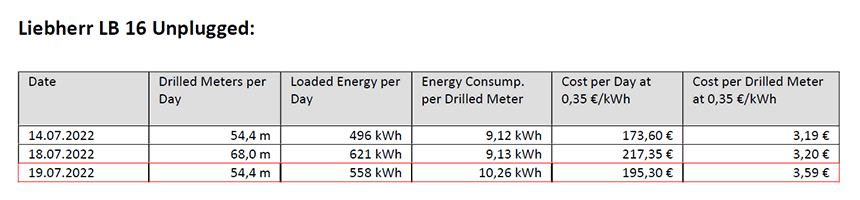
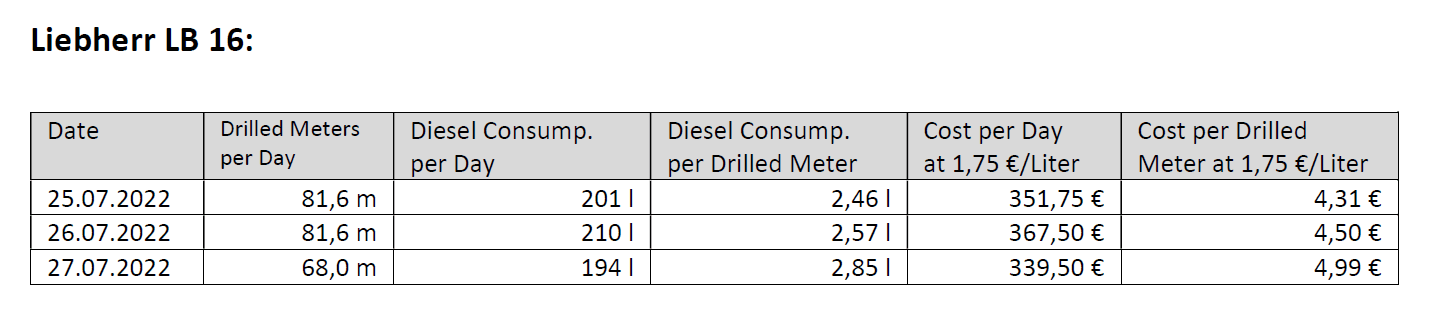
CO2 balance
The balance of CO2 emissions is evaluated according to Section 42 of the Energy Industry Act. Based on the standard electricity mix factor in Germany, the Liebherr LB 16 Unplugged emits approximately 4.61 kilograms of CO2 per drilling metre. The average CO2 emissions of the diesel-powered Liebherr LB 16 were approximately 8.27 kilograms per drilling metre, 44 per cent more than the battery-powered drilling rig.
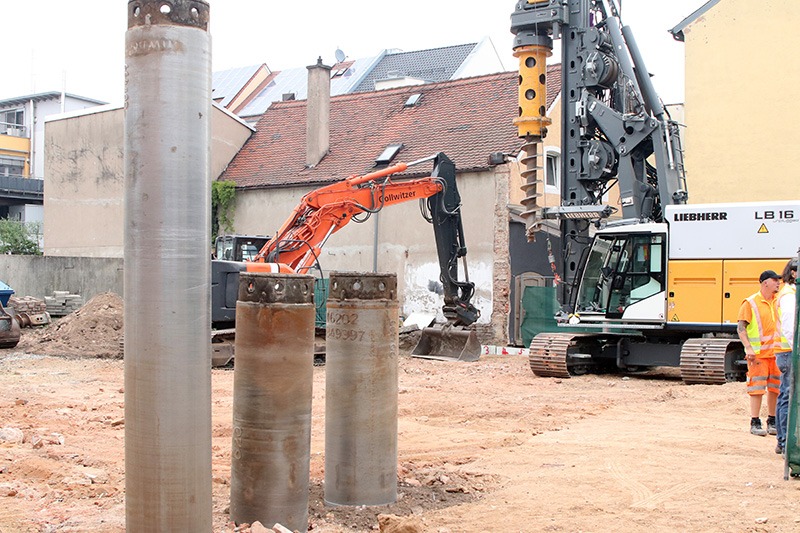
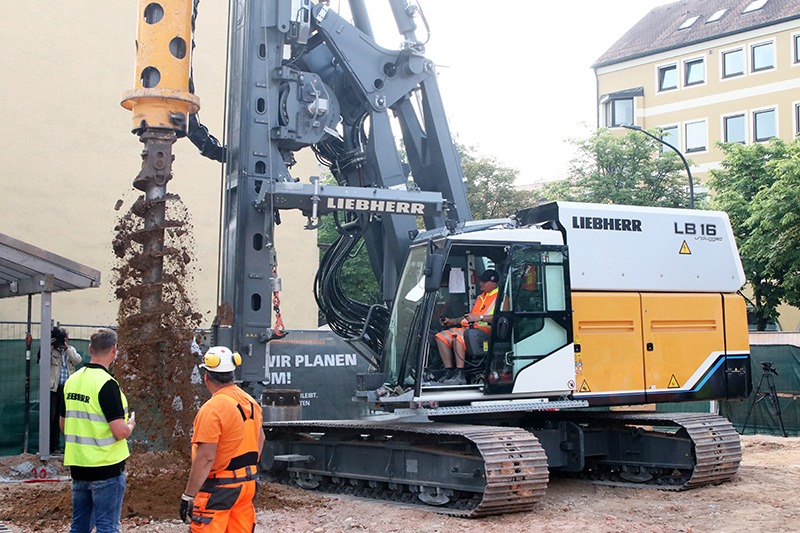
Heat emission
Both drilling rigs generate more or less thermal energy. To enable a correct determination of the differences, two independent measurements were conducted for each machine involving a handheld camera and a drone, both with thermal imaging.
As expected, measurements showed significant deviations between the two machines. As a result, it was determined that the Liebherr LB 16 emitted significantly more heat energy (see Table 6).
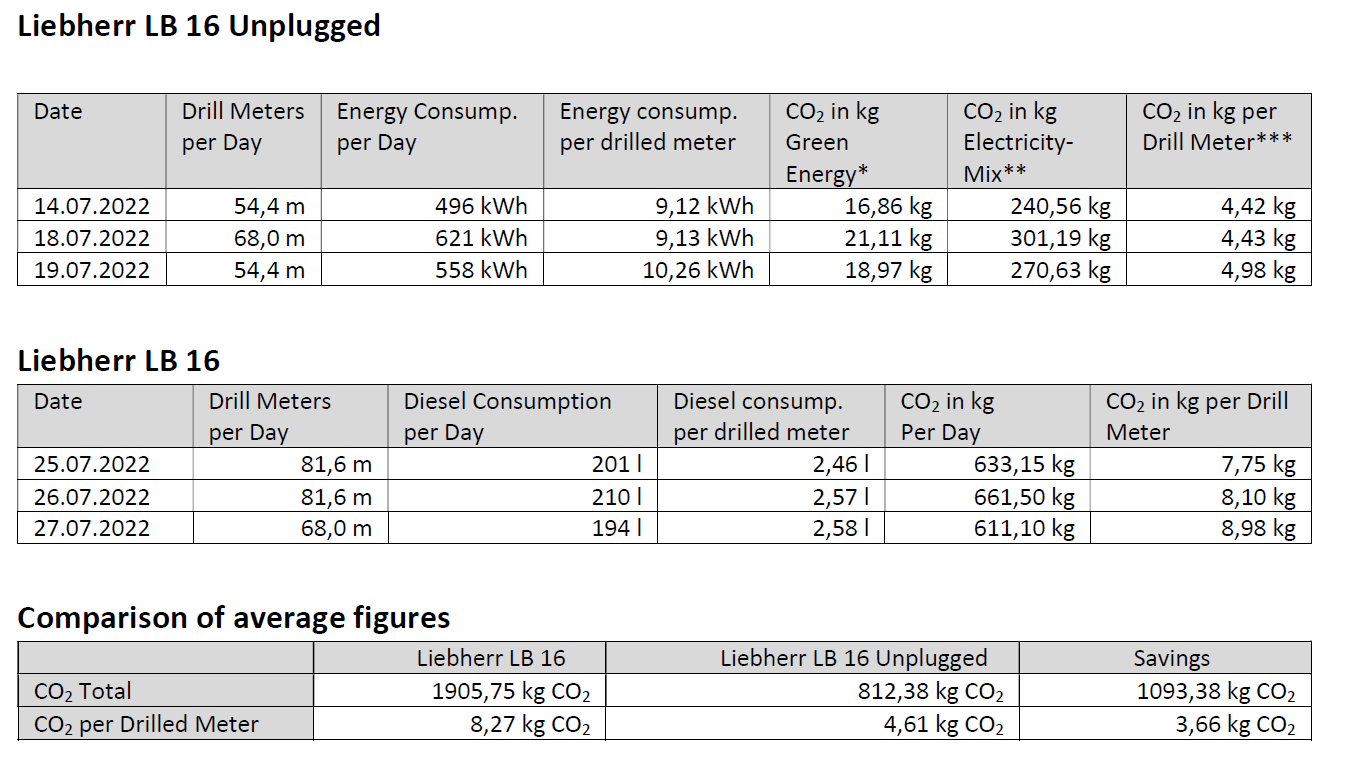

Noise pollution
Due to different drive trains, the Liebherr LB 16 Unplugged is less noisy than the diesel rig. It was found that the Liebherr LB 16 Unplugged works with an average of three decibels A lower than the Liebherr LB 16 while in operation. Operation noise such as cleaning the auger can be ignored, as these occur with both machines.
If official regulations for inner-city construction sites require adherence to certain noise levels, a battery-powered drilling rig is more adequate than its conventional counterpart. This is also true for restrictions on working times.
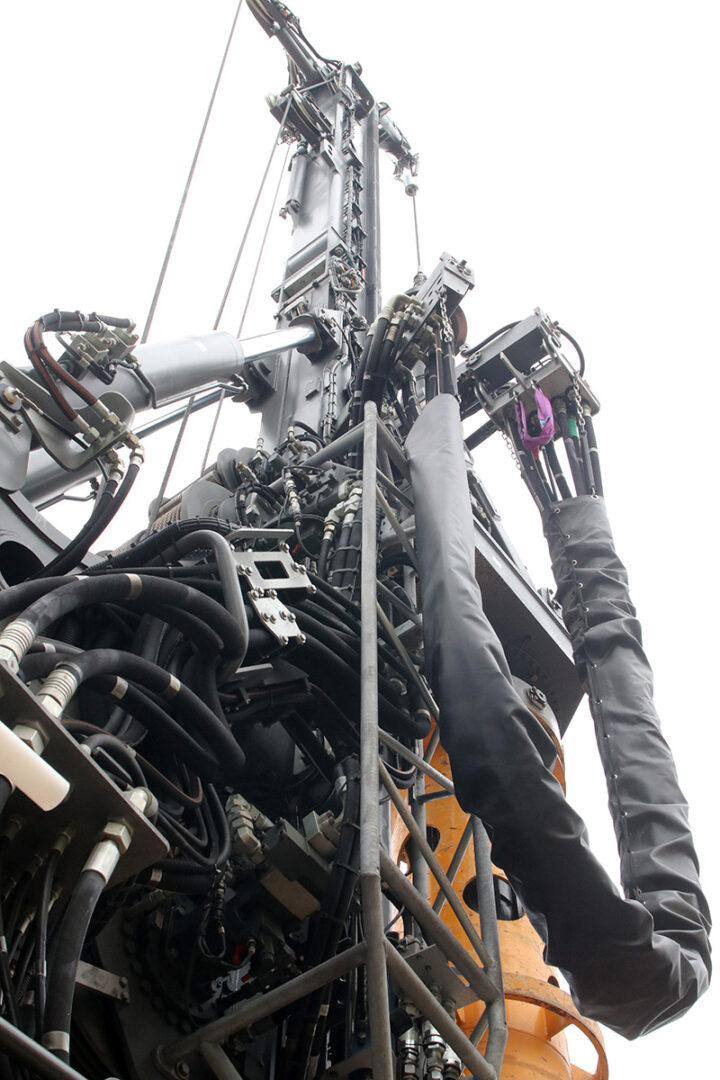
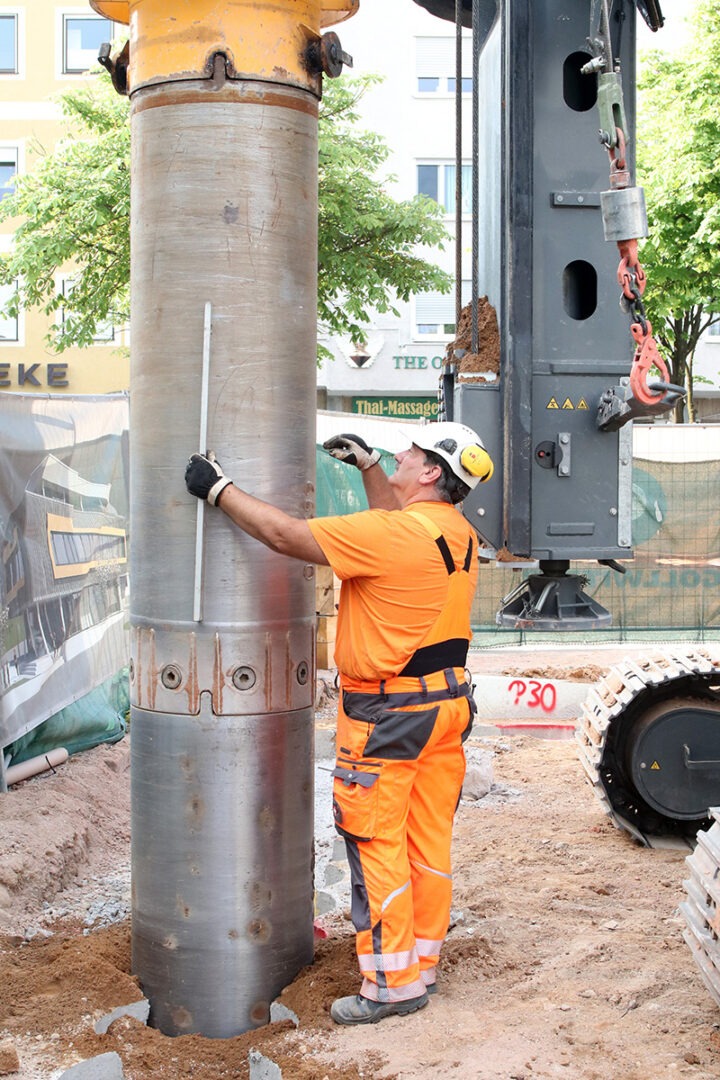
Conclusion
The Liebherr LB 16 Unplugged drilling rig is a very powerful machine for inner-city construction sites. Due to the low noise emission, it shows an advantage over a diesel-powered machine. The downside is its limited working time of about seven hours, if no intermediate charge is applied. However, it consumes at least 27 per cent less energy and emits about 25 per cent less heat than the diesel rig.
Further research needs to be done to determine additional factors such as the battery’s service life, since no data on long-term use is yet assessable.
Photos supplied by Borama Drilling Equipment