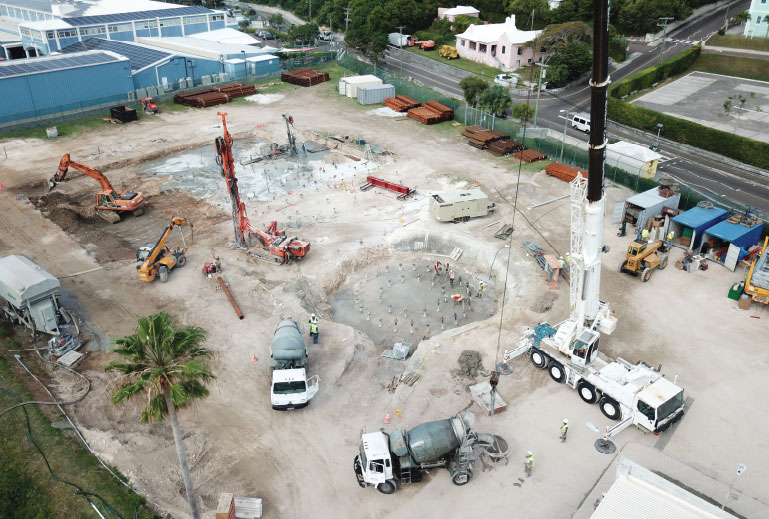
Brewster Drilling and Piling and Burmeister Wains Scandinavian Contractors overcame logistical challenges brought on by a remote island location in the Atlantic Ocean
It was back in December 2017 that Brewster Drilling and Piling – a division of FTE Drilling, with locations in Nova Scotia, Newfoundland, Quebec, and Ontario – was contacted by Burmeister Wains Scandinavian Contractors (BWSC). The Danish global turnkey developer, contractor and operator of tailored engine-based and boiler-based power plants tapped the Canadian company to assist with a piling solution for the BELCO North Power Station in Bermuda.
BWSC had built the previous power station on the island in 2009, but had experienced difficulties with the driven piles achieving refusal in the carbonate rock. In the end, BWSC needed to drive piles to refusal on the basalt rock approximately 49 metres below grade. This potential impact to the schedule was something that BWSC was determined to avoid this time around.
Brewster Drilling and Piling worked together with BWSC to develop a hollow bar micropile system consisting of 640 piles to support the required infrastructure for the BELCO North Power Station project. This solution would enable piles to be terminated in the carbonate formation above the basalt and substantially reduce the project’s cost and schedule.
Due to the tight schedule of this project, material orders had to be placed immediately after the financial close and project award.
“Brewster Drilling and Piling arrived onsite in late September 2018 and began installing test piles on Oct. 5, 2018,” said Kyle Fetterly, Brewster Drilling and Piling’s Eastern Canada manager.
“We installed 14 test piles at varying depths and carried out pre-production testing in order to confirm the design assumptions before commencing work on production piling.”
Materials and equipment used
“Steel casing was installed through fill/peat material from surface to a depth of six metres,” said Fetterly.
“Titan hollow bar T103/T52 bars were used to complete the installation to depths of 21.5 metres. A total of 3.5 million pounds of cement was sourced locally and used to complete the installation.”
A MDT 230B dual rotary drill rig was used to install 300 millimetre and 200 millimetre casing to six metre depths.
A Commachio MC8D was used with a TEI 1000 drifter to install the hollow bars.
“An Obermann VS109 grout plant coupled with a DMI 60,000-pound cement silo was used to mix and deliver grout to the drill rig as required,” said Fetterly. “A 300-tonne hollow core jack and reaction beams were used to proof test the piles.”
Due to the nature of the local carbonate geology, it was determined to be the best option to reduce vibration and project costs.
“Previous installations were plagued with refusal criteria issues. When conducting re-taps, piles which had previously achieved refusal criteria would mobilize and continue to move until they reached the basalt 150 feet to 160 feet below grade. The size of the site, the local geology and the proximity to residential properties made it a perfect candidate for hollow bar technology.”
While a near surface void was encountered onsite early in the construction process, it was determined to be an old septic pit, which was not documented. Activities were suspended until the site could be scanned for additional voids using a ground penetrating radar.
The completed structures consist of a 67.4-metre tall concrete chimney, the powerhouse which houses the four main engines, the electrical annex, a tank farm, a water treatment plant and four transformer pads.
Unique challenges
The biggest challenge of this project was its location on a remote island in the Atlantic Ocean, which proved difficult from a logistics perspective.
“Getting materials or parts to the island could only be achieved by air or ship,” said Fetterly. “Co-ordinating shipment with numerous suppliers from Bermuda, the U.S., Canada, and Europe, was critical to the project schedule. The crew was also required to travel to and from site by moped as non-residents are not permitted to drive vehicles with an engine exceeding 50 cc.”
Sand-filled voids and cavernous conditions existed onsite which meant special care had to be taken to ensure the quality of the installations.
Logistics for the project were also challenging due to the aggressive project schedule. Two drill rigs, a silo and grout plant, three 20-foot sea cans of equipment, 11 48-foot trailers of casing and 30 20-foot sea cans of hollow bar material had to be shipped from various locations in Europe and North America by sea and arrive in time to avoid delays throughout the duration of the project. Space on the site was also limited so the timing of these deliveries was critical.
A rigorous testing and quality control program was also developed to ensure the success of the project. Due to the size and capacity of piles required, a testing program was established to test the grout to soil bond in four- to six-metre horizons to reduce test loads. A composite grout to soil bond was calculated to determine the required pile length.
Fourteen verification tests were completed at 250 per cent design load to validate the design assumptions. Sixteen additional piles were proof tested throughout the duration of the project.
Brewster Drilling and Piling employed the use of an automated cement batching system with a 60,000-pound silo to ensure grout quality and also to allow for quick water cement ratio changes during drilling and completion.
“We completed piling installation in early March 2019,” said Fetterly. “The project was completed in phases as portions of the site were made available. A total of 90 working days to complete the piling, including pre-production testing.”
As a result of the efforts of Brewster Drilling and Piling, and the equipment and skilled workers deployed on the project, the job was completed two weeks ahead of schedule with no downtime on critical path equipment.
The entire BELCO North Power Station project is scheduled for completion in early 2020.
Photos courtesy of Brewster Drilling & Piling.