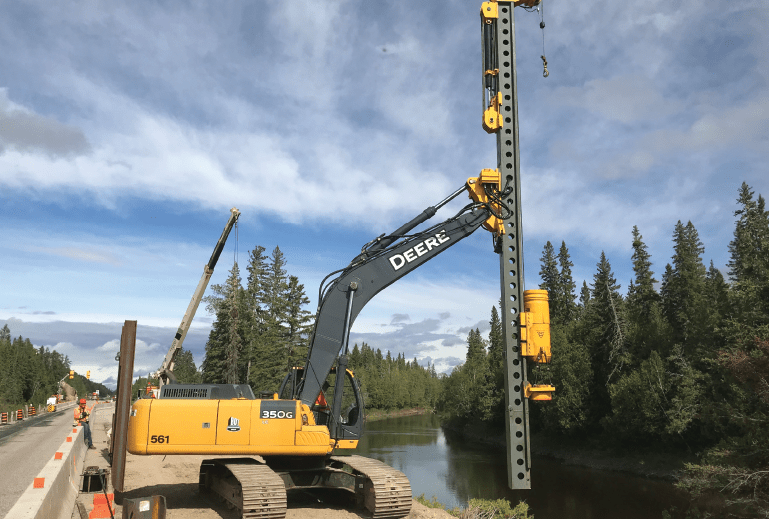
Berminghammer’s new EML30 excavator-mounted pile driving unit offers portability, costs savings and could change the way some foundations are built
The equipment manufacturing division of one of the country’s oldest foundation contractors recently introduced a new pile driving system that could revolutionize the way some foundations are built.
Hamilton, Ont.-based Berminghammer Foundation Equipment introduced its Excavator Mounted Lead system for 30-ton excavators, or EML30, earlier this year. The system features a lead and hydraulically actuated drop hammer that attaches to the boom of an excavator to drive piles, including both H and sheet piles, into the ground.
The company has offered crane-mounted VTL lead systems and diesel hammers for many years, but the EML30 is its first full production model of an excavator-mounted piling system.
David Zanchetta, Berminghammer’s sales and service representative for Ontario, says the inspiration for the new system was customer demand. A number of contractors doing work in Northern Ontario, some as far away as 1,000 kilometres or more from parent company Bermingham’s Hamilton office, would ask if there was anything the company could do to lower their costs. Company representatives would often explain that the cost of the work was relatively minor compared to the cost of getting the equipment to remote sites.
The costs associated with transporting a crane to the remote locations were significant. Some cranes that would complete similar work require as many as three or four truckloads to transport them to a construction site, meaning transportation costs could total more than $100,000 to set up a single project.
The beauty with the EML30, Zanchetta says, is that it can be transported anywhere in just a single load. That means mobilization costs of as little as $5,000 compared to the six-figure cost associated with using a crane-mounted system.
“The EML was designed so that it can go as one load already attached to the excavator. You can take it from your yard or its last job and bring it to the site in one load. That’s what it was designed around,” he said.
“If you have a situation where your transportation savings are in the magnitude of $100,000 for a single trip, that’s a huge savings and quickly justifies the purchase of the EML30.”
Another advantage the EML30 offers is that it requires far less room to operate than crane-mounted systems. That’s critical in areas where the footprint is so small that a crane system can’t easily access it.
“That’s very advantageous in areas where you are looking to do something like roadway protection,” Zanchetta said. “You might be right beside a river or between lanes on a highway and getting a crane into that area and creating a crane pad can cost a significant amount of time and money. With an excavator, you can get into a lot tighter spots.”
Not only does the EML30 help simplify some of the logistical challenges associated with deep foundation projects, it’s also pretty simple to operate. Most excavator operators can learn how to properly use the system within a couple of days.
“If you can operate the shovel and have a feel for that, you can operate our system once you have a little guidance,” Zanchetta said. “One of the nice things is everything is integrated. You don’t really have to change anything in your base machine. You hook up hydraulic lines and all of the valves that control the lead and hammer are on the lead itself. An electronic control line runs into the cab for the operator to control the device. It’s a pretty slick set-up.”
The EML30’s specs lend credence to the notion that big things can come in little packages. Weighing in at just under 18,000 pounds, excluding pile and excavator, the shipping length of the lead unit is just 37 feet, while the height is six-feet, nine-inches. Depending on the model of excavator used, the system offers an approximate maximum reach of 20 feet and minimum reach of 15 feet. It provides 56,055 ft lb of potential energy from a seven-foot drop. It can handle piles of 30 to 35 feet in length and can accommodate deeper requirements using spliced piles.
Design work on the EML30 began about two years ago and the first unit was built this past spring. However, the inspiration for the unit dates back nearly a decade. In 2008, Berminghammer developed a small, crane-mounted semi-fixed pile driving unit for the U.S. Army and manufactured 130 of the units. The first prototype EML utilized the lead components of this army system and attached them to an excavator.
“The new system is very different from the prototype system. One of the major differences is that we have side levelling now available, which means the excavator doesn’t need to be perfectly level in order to drive a straight pile,” Zanchetta said. “It also has a significantly more robust lead with a deeper section.”
One of the biggest challenges with developing the new system, according to Zanchetta, was trying to meet as many customer needs as possible while still offering a compact package. Some potential buyers wanted the lead to be capable of everything while others were adamant that it needed to have some kind of drilling application.
To address those disparate needs, Berminghammer separated the two conflicting needs into two different models of EML, the EML30 and the EML45. Berminghammer designed the EML30 to essentially be a dedicated piling rig, although it can take a very small drill. The EML45, which is being put into production now, will have additional drilling capacity and will be available for sale later this year. A 60-ton model is also ready for production.
The early reviews for the EML30 have been largely positive. It was first used this summer as part of road repairs to Highway 11 near the town of Hearst, Ont. As part of the project, three existing culverts underneath the highway had to be removed and replaced.
BOT Construction (Ontario) Ltd., the first buyer of the EML30, had to shore up the ground beneath the highway where the culvert work was being done to allow traffic to continue to use the roadway. The EML30 was used to drive a combination wall, or combi-wall, featuring both H-piles and sheet piles that interlocked and helped support the ground and road above.
“As far as I know, no one had done an installation this way before,” Zanchetta said. “The H-piles had to be driven precisely. We needed to get them in place within a couple of inches to make sure the sheets would spread nicely between (the H-piles). It was a little different methodology…but it worked out really well.
“The EML unit performed really well for us. One of the advantages with it is you can go a lot deeper than you can if you vibrate the piles in, especially in areas where you are unsure if you might run into boulders and such underground. We definitely ran into some boulders and the EML’s 8,000-pound drop hammer pushed them out of the way, whereas if you were vibrating, you would just be stuck there and have to figure something else out such as a redesign.”
Zanchetta says the Highway 11 project backed-up Berminghammer’s assertion of how simple the EML system is to use. BOT Construction had never driven piles before, but was able to do so after its operator received on-site training from Berminghammer staff.
The EML30 is also pretty versatile. In addition to driving vertical piles, it can also drive batter or angled piles. Battered piles provide a distinct advantage in terms of their ability to carry lateral loads.
“Having the ability to do batters is a real advantage,” Zanchetta said.
Zanchetta has no doubts that the EML30 is well positioned to become one of Berminghammer’s most popular products as word of it spreads throughout the industry.
“I think it’s especially pertinent for two types of buyers: foundation contractors that want to have a compact mobile unit in their arsenal and general contractors who want to be able to do their own small piling projects. Most general contractors already have excavators. It’s just a matter of adding this unit to be able to drive piles themselves. That’s a pretty attractive idea.”
Although the EML30 is still relatively new to the market, its manufacturer and parent company have both been around for some time. Bermingham Foundation Solutions was established in 1897 and constructed some of the first foundations for Canada’s railways. The Berminghammer equipment division was created in the 1970s and its products are now sold all around the world.