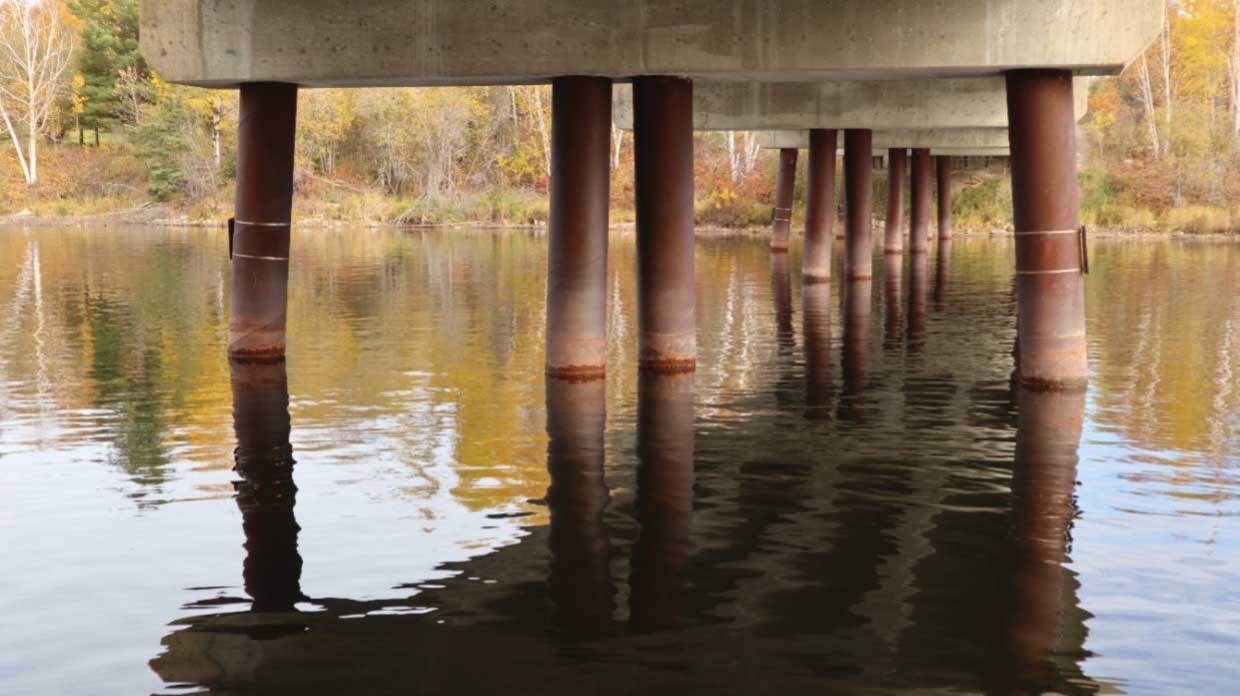
Existing steel support piles
Photo: Denso
In July 2020, Dominion Divers Marine Contractors (Dominion Divers), a sub-contractor to Landform Civil Infrastructures Inc. (Landform Civil), was awarded the construction contract involving structural rehabilitation of the Black Sturgeon River Bridge located approximately 12 km north of Kenora, Ont., on Highway 658. The two-lane bridge, owned by the Ontario Ministry of Transportation, was supported by five piers, each consisting of four 609 mm (24-inch) diameter steel piles and related cross-bracing, for a total of 20 steel piles of varying lengths. The lower two-thirds of the piles, including the cross-bracing, were permanently submerged underwater.
Part of the contract called for the encapsulation of the steel piles for their full height – from river bottom to underside of the bridge deck – with Denso North America Inc.’s (Denso) SeaShield 2000HD pile protection system to protect against future corrosion and increase the life of the steel piles. This system consisted of Denso’s S105 paste, Marine Piling Tape, and HDPE outer jacket for the piles and S105 paste, LT Tape and Glass Outerwrap at the cross connections.
Due to limited space, only a small amount of material was brought out to the barge at a time.






The repairs to the bridge were engineered by Hatch, while the administration of the construction contract was completed by TBT Engineering Limited.
Denso staff provided virtual training to Dominion Divers on the surface preparation requirements and application of the SeaShield 2000HD pile protection system prior to their mobilization to the project site, and also attended the site in-person to provide guidance on the installation for the first pile.
Project requirements and challenges
Prior to ordering the materials, Dominion Divers visited the site to obtain field measurements of each steel pile and the elevation of the cross-bracing at each pier. This step ensured that the appropriate amount of material and jacket lengths were ordered to minimize issues during construction.
Access to the site was limited by space and topography immediately around the bridge. Therefore, Dominion Divers had to access the bridge via boat from an access point approximately 1 km to the southeast. Landform Civil set up safety buoys in the river to inform boaters of the in-water works and appropriate boat traffic flow. Dominion Divers set up floating barges initially around Pier 4 and also had to set up a submerged turbidity skirt around the work area to contain any debris and/or sediment from the cleaning and installation process below the waterline.
Due to limited space, only a small amount of material was brought out to the barge at a time.
Once the appropriate equipment and materials were set up, Dominion Divers started by cleaning the steel surface of one pile at a time, per the contract. This involved scraping off all marine growth, loose rust and other foreign matter by hand with a metal blade following SSPC-SP2 hand tool cleaning. They then proceeded to pressure wash the steel pile using a 4,000-psi pressure washer to ensure the surface of the pile was sufficiently clean. This procedure was followed for the full height of the pile and for each subsequent pile.
After the pile was fully cleaned, all weld splatter from the original installation was removed by grinding. The thickness of each steel pile was measured and recorded at multiple points both above and below the waterline. The engineer then evaluated the steel thickness of each pile prior to the application of the paste and tape corrosion protection system.


The visibility of the spiral weld below the Marine Piling Tape and the lack of folds or imperfections at the tape seams indicates a nice tight application of both the Marine Piling Tape and Glass Outerwrap.
Once the piles were fully cleaned, Dominion Divers proceeded to apply the corrosion protection paste to the pile’s surface. This proved to be challenging and very slow work below the waterline, and after some brain-storming discussions it was agreed to pre-apply the paste to the tape on-deck, and then re-roll the tape to be ready for future use. Dominion Divers established a system where one to two crew members pre-applied the paste to the tape on-deck while the remaining one to two crew members (divers) were applying the tape underwater, with a superintendent overseeing the work and safety of the crew. This approach helped to expedite the work while providing the same corrosion protection results for the customer.
The visibility of the spiral weld below the Marine Piling Tape and the lack of folds or imperfections at the tape seams indicates a nice tight application of both the Marine Piling Tape and Glass Outerwrap.
The HDPE outer jackets were supplied in various lengths, the most common being 3 metres (10 feet). Dominion Divers was required to cut some of the HDPE outer jackets to fit the site conditions, which was easily achieved using an angle grinder. The bolts were installed by hand and tightened with a torque wrench.
While on site, there was some confusion around the direction of the current. The drawings indicated one direction while the divers noted that the sediment underwater was flowing in the opposite direction. Since the team was not able to obtain a clear answer, it was agreed to install the bolted seam of the HDPE outer jacket facing inward on each pile. This would provide some level of protection against ice build-up and potential damage.
The visibility of the spiral weld below the HDPE outer jacket, both above and below the waterline, indicates that the appropriate torque was applied to the bolts to tighten the outer jacket. This system will provide both corrosion and mechanical protection to the steel piles for years to come.
Project timeline

The installation of the pile encapsulation system needed to be completed by Oct. 30, 2020, in advance of the winter season.
Dominion Divers started the surface preparation on the first pile on Oct. 7, 2020. Denso understands that this work was completed by Dominion Divers on schedule and to the complete satisfaction of the engineer and owner, as well as Denso.