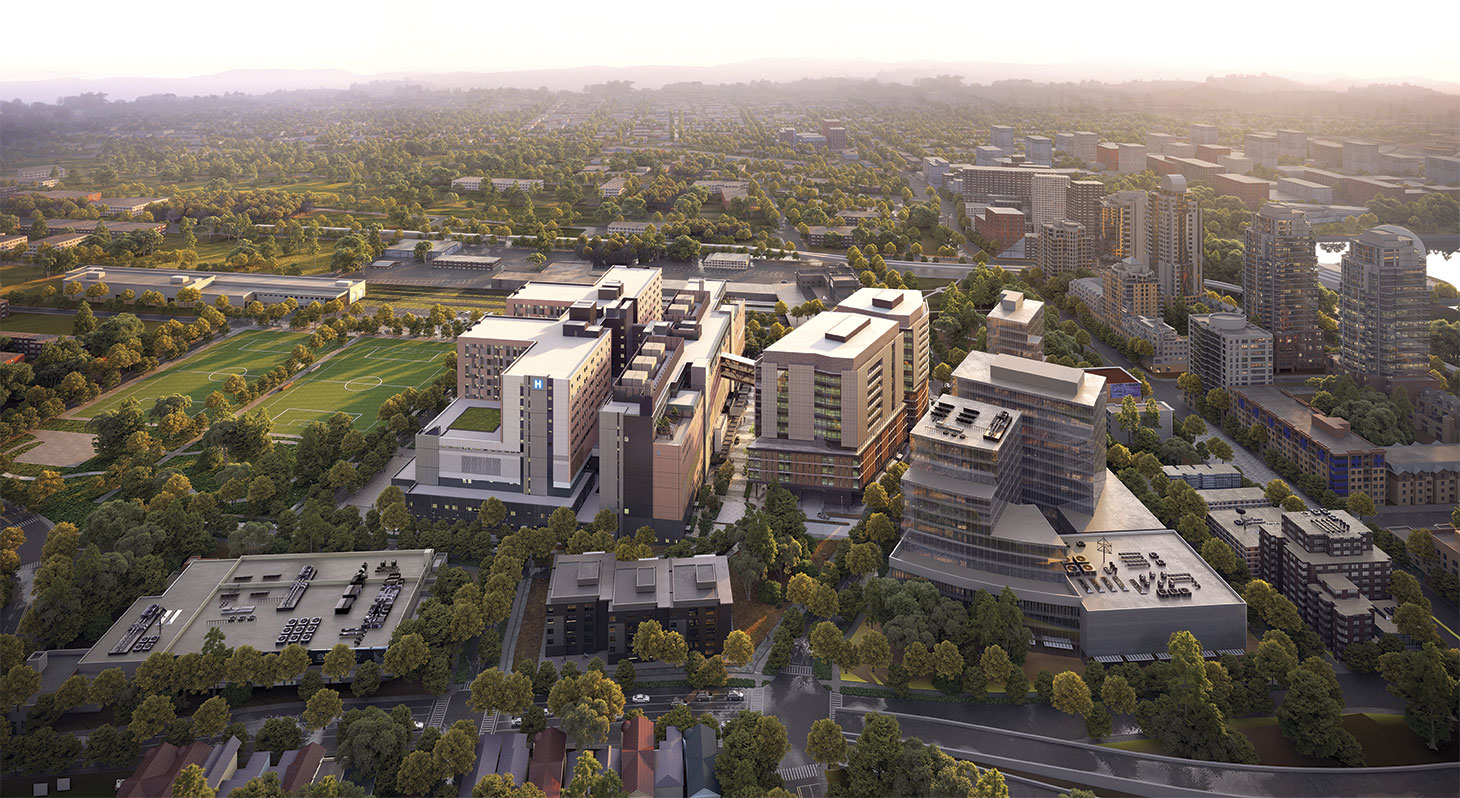
British Columbia’s continuing mission to improve health care in the province keeps growing with the inclusion of the new St. Paul’s Hospital in Vancouver – one of the largest, and most ambitious, health care capital project in Western Canada.
This state-of-the-art facility will transform the future of health care, not just for today, but for the next 125 years – or more. Strategically located on the sprawling 18.4-acre Jim Pattison Medical Campus on Station Street, the new St. Paul’s Hospital is just three kilometres from the current hospital on Burrard Street in Vancouver’s False Creek Flats neighbourhood.
The large size of the land parcel is such that there is also an opportunity to expand the hospital’s programs, services and facilities as future health care needs evolve in the province. The site is also at an intersection of major transportation arteries and is close to key public transit connections such as SkyTrain and several bus routes, as well as near the Pacific Central Station, which connects to many train and inter-city and cross-border bus routes.
PCL Construction and its architects, HDR Architecture Associates, Inc. and Stantec Architecture Ltd., were awarded the design-build contract for the new hospital. Construction on the project started in March 2021.
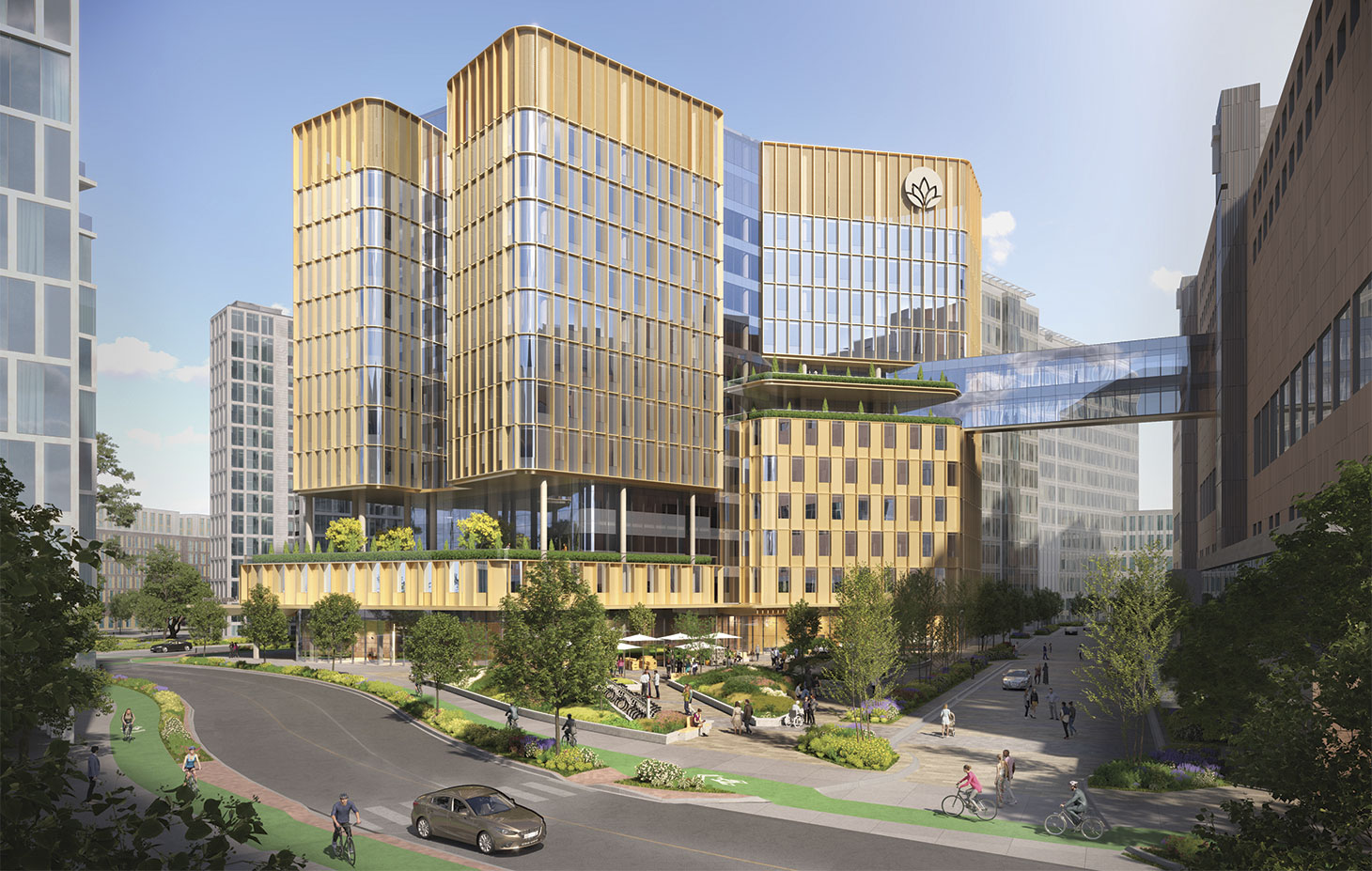
Challenging soil conditions
The new St. Paul’s Hospital project needed little in terms of deep foundation work, which was largely limited to supporting some of the hospital’s infrastructure, such as oxygen tanks. However, the entire project site required extensive secant pile shoring to support excavations and provide groundwater cutoff. The scope of the piling included more than 800 secant piles of one-metre diameter installed at an average depth of 14.5 metres. The piles were installed by Henry Foundation Drilling Inc. using a total of five BAUER BG36 and BG40 drill rigs.
The land under the False Creek Flats neighbourhood was historically a tidal zone. Over the years, however, the land has been reclaimed from the ocean using a variety of fill materials sourced from different locations across Vancouver. This gave PCL and its team varying, poor and challenging soil conditions for the first five metres or so from the surface.
“However, once we hit the natural soils – the marine clay – and found the glacial till that our footings are based on, everything went smoothly,” said René Horn, project manager at PCL Constructors Westcoast Inc.
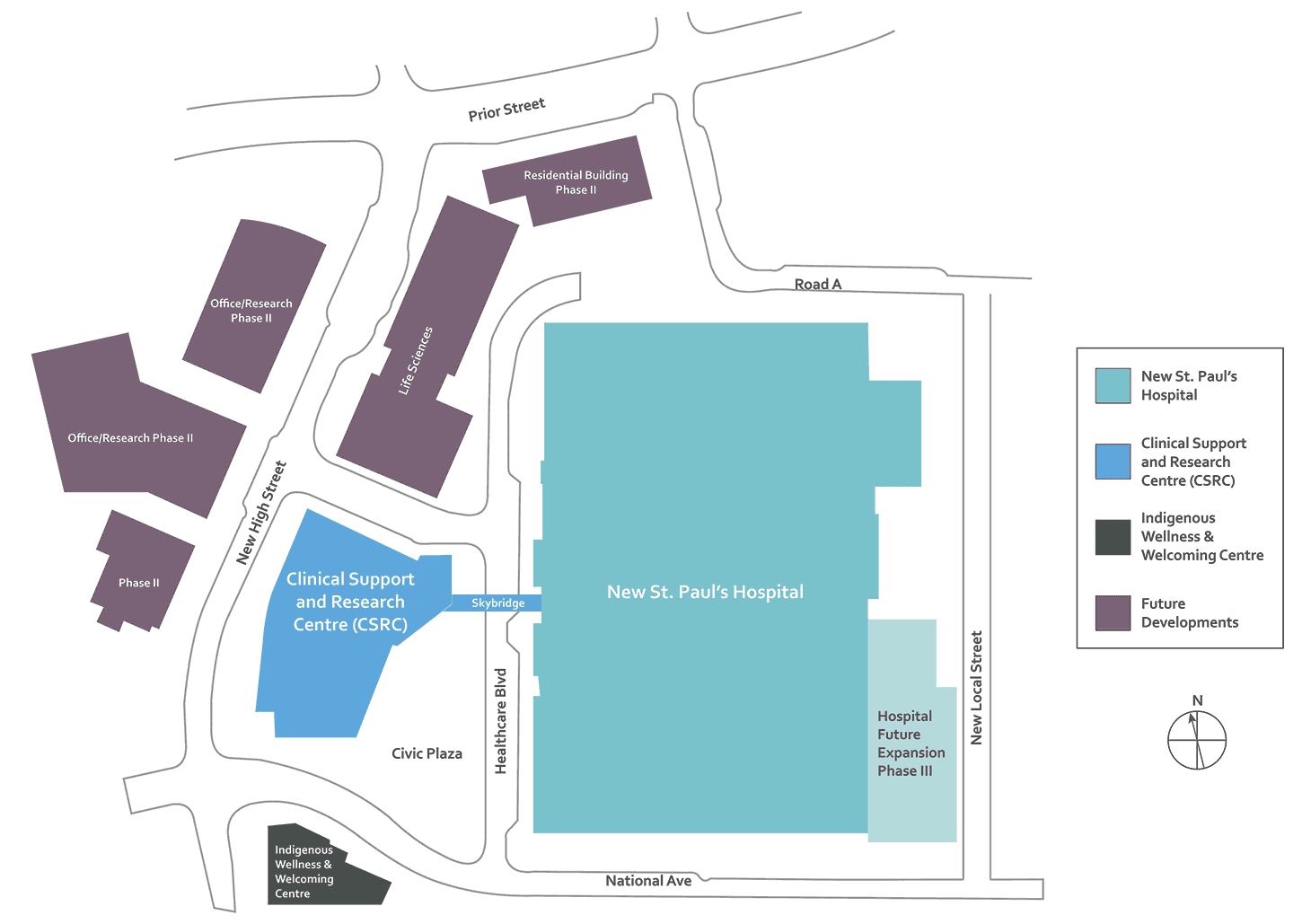
The excavation of the site was then done in stages, which needed to be very detailed as different soil contamination levels were being discovered and removed. Fortunately, because there were several site investigations conducted in the past and many boreholes previously drilled, PCL had a heads up on the soil conditions ahead of time.
“Of course, there’s always going to be some unknown variables, like groundwater conditions that change over time,” said Horn. “But we knew for the most part where the groundwater table was and we knew whether or not it was influenced by the tidal water, so there wasn’t anything that really surprised us. In addition, even before we started digging or installing piles, we drilled 250 boreholes of our own and had the soil analyzed to give us a soil classification report. This allowed us to create a 3D model of all the different contaminated soil conditions to give us a better idea of what we were up against, and we transferred that information to the excavators in the field.”
The intersection of technology and collaboration
For this project, PCL implemented significant measures with its automated monitoring system on each of the soldier piles connected to the anchors. This sophisticated system provided 24/7, real-time monitoring of all the soldier piles to show how they were behaving so that, if they move out of tolerance, an alert is sent out to the team.
“Our superintendents would get alerts and be able to react to them immediately – even during the nighttime hours – and there were a few instances where we were required to call engineers in to assess the situation and had to make decisions on what to do,” said Horn. “We also used shape arrays, which are more commonly used in the mining industry, to monitor in-ground movements. We implemented these arrays so that we could more precisely know what was happening underground.”
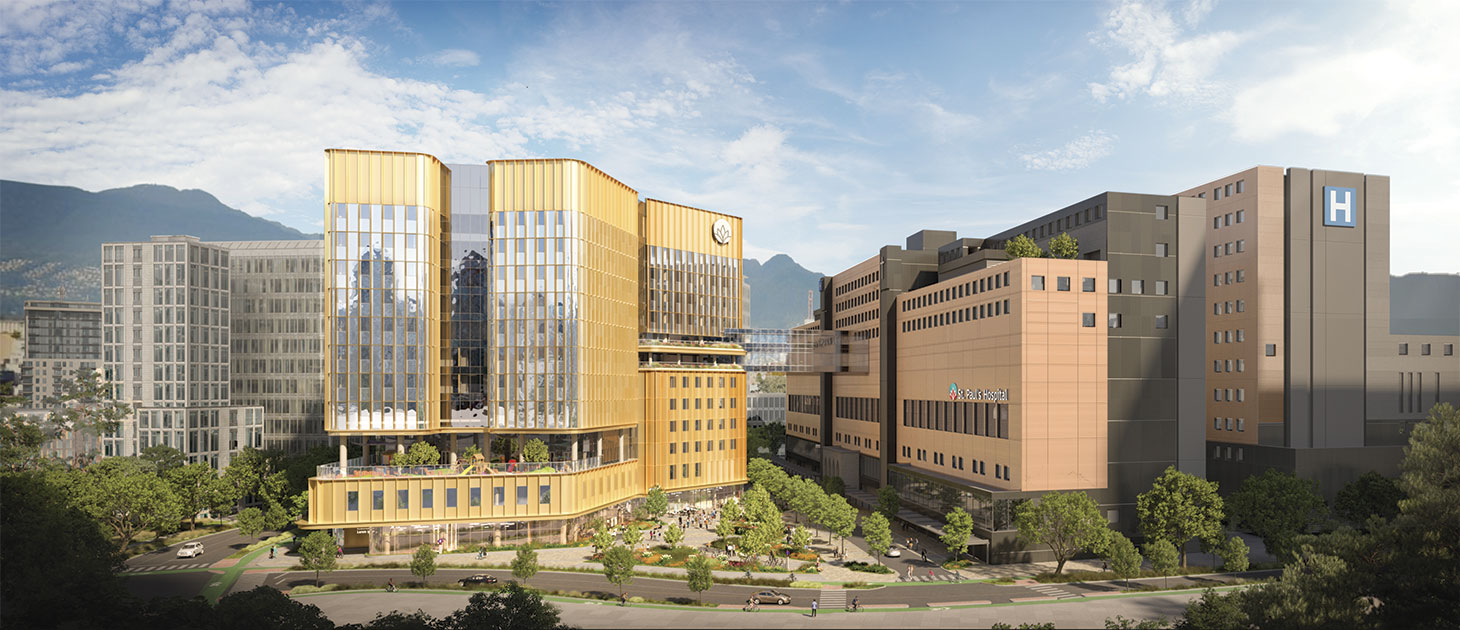
Success on a project as large as the new St. Paul’s Hospital does not happen by accident; it requires significant preparation and collaboration. Just as it does with all of its projects, PCL employed a full auditing process of all contractors and looked at elements such as experience and reputation in and around the industry to ensure it was getting quality contractors who completely understood the scope of the project, as well as what was expected of them. As a design-build project, PCL also strived to maintain open communication with the owners and the company was very involved with the initial design process, in addition to subsequent reviews of the design.
“We made sure to have regular reviews with Providence Health Care to provide input on the design, offering alternate proposals based on what we would have included or what we could provide based on the expertise of our own geotechnical consultants,” said Horn. “During the project, Providence had their own geotechnical and compliance consultants who would come to the site and review our work, so there wasn’t anything we were doing that they weren’t involved with in some way.”
Built to last
The new St. Paul’s Hospital has been designed to be climate resilient and withstand rising temperatures, extreme weather, earthquakes, flooding and whatever else Mother Nature might throw at it. As a post-disaster facility, the hospital will operate self-sufficiently during and after a potential event, with emergency power and fuel supplies that can support the entire hospital off the grid for up to 72 hours.
“We are looking forward to seeing their reaction when the clinical users finally get to experience a workplace where they’ve had input into how it was put together and how things should be set up.”
Kevin Little, Providence Health Care
The fourth floor of the facility houses its 200,000-square-foot mechanical room, with the fifth floor of the left tower also serving as a mechanical room that contains the hospital’s electrical equipment.
“The Flats are located on a potential floodplain, which is part of the reason we put the mechanical and electrical where it is,” said Kevin Little, senior manager, design and project delivery at Providence Health Care. “This way, during a post disaster event like a flood, all of our critical infrastructure that keeps the hospital up and running remains completely functional on the fourth and fifth floors.”
A new model for care
Using pioneering design and next-generation technology, the new St. Paul’s Hospital will focus on treatment through teamwork with patients and their families and will provide a seamless level of care – from primary and community to emergency – offering the right care by the right provider, in the right place at the right time.
The benefits of this integrated approach to health care delivery are many, and aim to significantly reduce wait times, provide a higher quality of care and produce better health outcomes and experiences for the residents of British Columbia, as well as provide improved value for health care dollars spent. The new $2.18-billion facility is almost double the size of the current St. Paul’s Hospital, with doors expected to open in early 2027. The new acute care hospital will be home to several leading provincial programs and referral centres, including space for heart and lung care, renal, eating disorders, specialty surgeries and transplants.
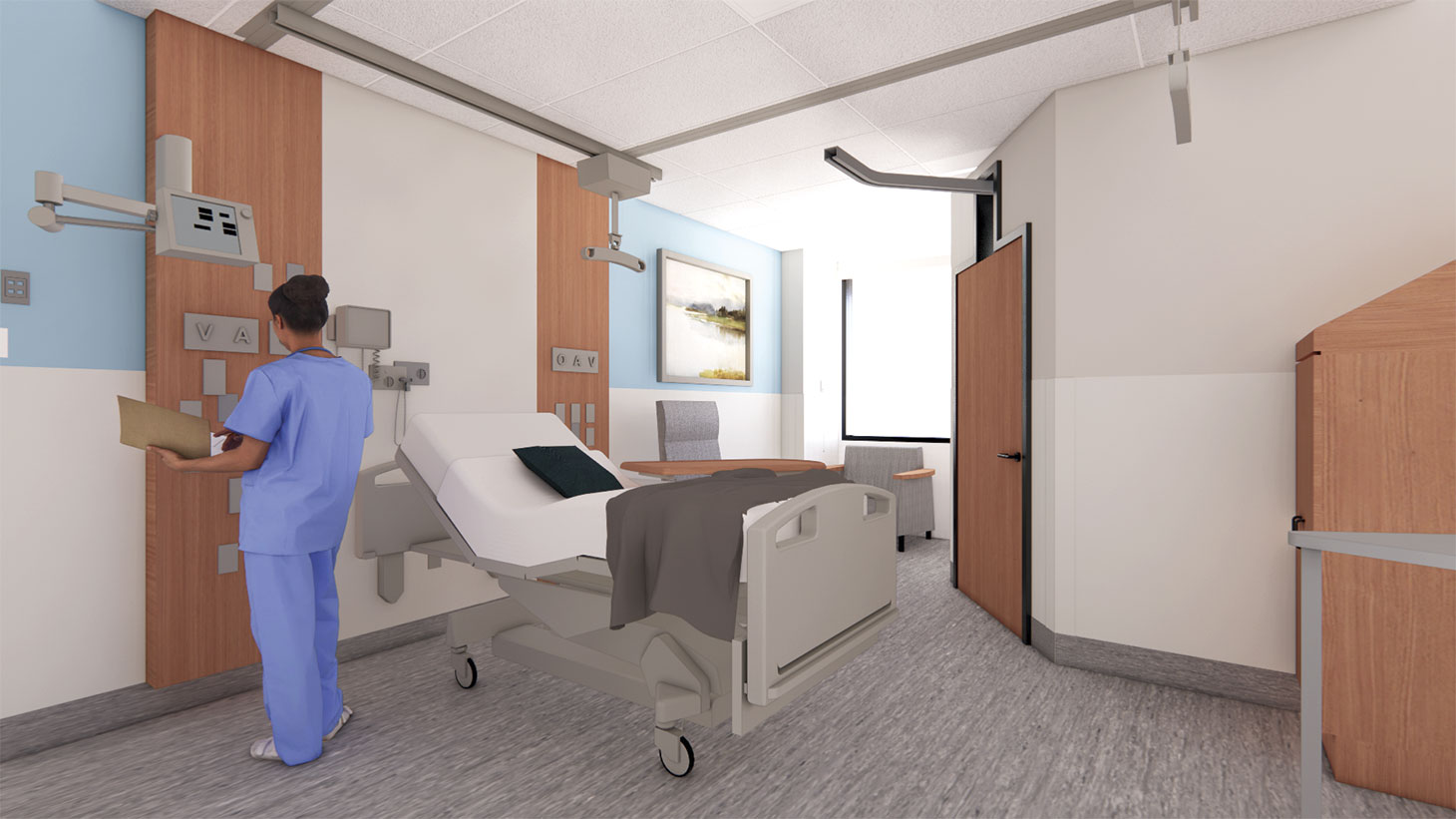
In addition, the new St. Paul’s Hospital will offer a long and diverse list of general and specialized care, including chronic disease management services, emergency and critical care, mental health and addictions’ beds and programs, ambulatory services and outpatient clinics, end-of-life palliative care, Indigenous health, maternity, colorectal and gastrointestinal services, community care, outreach programs and a first of its kind Centre for Healthy Aging.
The new hospital will feature 548 rooms, which would provide 115 more beds than found at the current hospital. Each of these modern and private rooms offer additional space for family and supports to stay with the patient overnight, which will minimize infections and maximize privacy.
“At the new St. Paul’s [hospital], every room is going to be a private, single patient room with its own washroom, bedpan, washer and a very quaint seating area with a chair that can fold up so patients can stay with their family,” said Little. “This facility has been designed to be purposeful so, even with each patient having a private room, we still expect to be able to serve up to 30 per cent more patients than we can at the old hospital.”
“Even before we started digging or installing piles, we drilled 250 boreholes of our own and had the soil analyzed to give us a soil classification report. This allowed us to create a 3D model of all the different contaminated soil conditions to give us a better idea of what we were up against.”
René Horn, PCL Constructors Westcoast Inc.
Other elements of the hospital that optimize wellness include access to natural light and views, a seniors-friendly campus layout, digital wayfinding to allow easy navigation around the campus, outdoor and other spaces for wellness and rejuvenation, a variety of sacred spaces and public art that incorporates an Indigenous perspective into campus design.
“It’s really been a treat working with our clinical users to influence the design and functionality of the new St. Paul’s Hospital and it will be awesome to see them inherit the building,” said Little. “We are looking forward to seeing their reaction when the clinical users finally get to experience a workplace where they’ve had input into how it was put together and how things should be set up.”
A home for research
The new facility will continue to be an adult academic health sciences organization, building on St. Paul’s Hospital’s reputation as a globally renowned care, research and teaching hospital that ensures excellence in acute, emergency and critical care and serves patients from throughout the province. As part of this, a 370,000 square foot, state-of-the-art research, technology and medical complex – the Clinical Support and Research Centre (CSRC) – is being built just steps away from the new St. Paul’s Hospital. When complete, the $638.3 million CSRC will be home to a full spectrum of spaces, from core research facilities including wet labs, specimen biobanks, a 49-space child care centre and more.
“This new research centre will help define the future of medicine,” said Premier David Eby at the announcement of the new centre. “We are going to see scientific breakthroughs translated into real-world health care, delivering better services and treatments for patients. British Columbia is becoming a global hub for life sciences and today’s announcement will help us to continue to attract the best scientists and researchers to our province, as well as doctors, nurses and other health care professionals.”