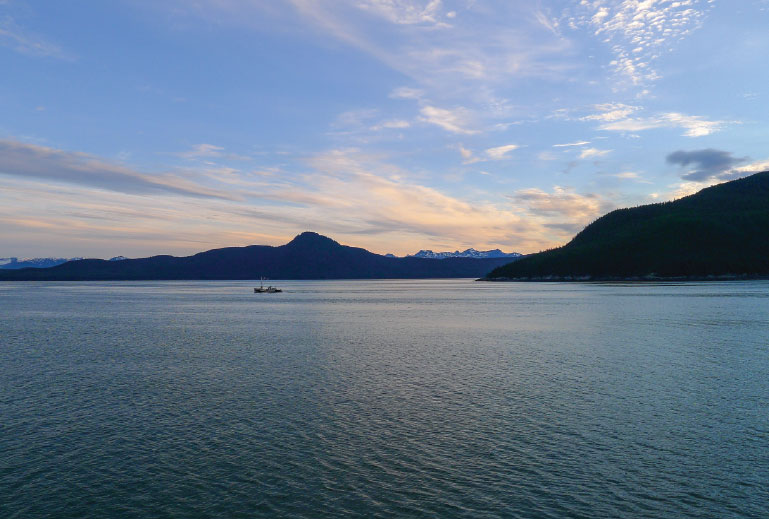
Help protect both the environment and workers by selecting the safest products on the market
We all want to be safe. Safety regulators want us and our employees to return safely home from a day’s work. Both governments and non-governmental organizations (NGOs) press for more regulations that mandate less environmental impact as we operate pile driving equipment in marine or estuarine environments.
What is a “safe” fluid for pile driving projects? In a nutshell, it’s a grease, oil, hydraulic fluid or cleaner that has less potential for environmental impact than a traditional lubricant (or cleaner). Until recently, many of these safer products all came with serious technical flaws. Today, there are better choices with fewer – if any – unacceptable tradeoffs.
What are our options today? Opinions differ, so your best bet is to do your homework and use the Internet to look for options. Reputable manufacturers release test data based on recognized test methods published by ASTM International or the OECD. Also, talk to suppliers and ask for technical data. What questions do you need to ask? What is safe, sustainable, biodegradable and reliable?
A good place to start is with fluids that meet the requirements or standards accepted by the marine industry and the NGOs. One such requirement is outlined in the United States Environmental Protection Agency’s Vessel General Permit (VGP) regulations that specifies high biodegradability, low toxicity and low bioaccumulation requirements for Environmentally Acceptable Lubricants (EAL) used on vessels within certain U.S. waters. While the EAL requirements are not binding for industries operating outside U.S. waters, the requirements of the VGP are a good starting point to help us define what constitutes a “safer fluid” for pile driving applications. When a fluid, oil, grease or cleaner meets VGP requirements, it is considered a safer material for the environment if spilled or leaked. Liability for user cleanup still exists, but the cleanup costs and fines are expected to be less for VGP-compliant fluids.
Use of VGP-compliant products can also help minimize negative press coverage in the event of a spill. VGP compliance does not address performance issues. There are excellent and poor VGP-compliant products. Review the technical data supporting VGP compliance and request data on product stability, wear characteristics, foaming and demulsing to help make an informed decision. Confirm that the fluids indeed meet all three requirements of the VGP. Some lower-quality fluids sold today claim biodegradability when they in fact do not meet the “readily biodegradable” requirement of the VGP. A “readily biodegradable” fluid degrades in the environment more rapidly than an “inherently biodegradable” fluid. Only readily biodegradable fluids can be VGP compliant. When in doubt, ask for supporting documentation, preferably from an independent, third-party laboratory.
A low-cost, unstable lubricant, regardless of base oil technology, will ultimately cost the user more than a higher-quality EAL when product lifetime and spill costs are considered.
There are four EAL technologies, and each has advantages and disadvantages. EALs can be based on triglyceride base oils like canola oil or esters, polyalkylene glycols (PAG) or readily biodegradable hydrocarbons. Ester and PAG products pose the most problem with seal compatibility. The most stable technologies are the EALs based on polyalphaolefins or related readily biodegradable hydrocarbons that offer stability in service and ready biodegradability in the case of the spill. Some EALs offer this type of hydrocarbon base oil stability, but they use a biobased hydrocarbon – also known as biohydrocarbons – that gives the stability of a mineral oil lubricant while using renewable technologies to create the base oil. These EALs based on biohydrocarbons also have the chemical seal and pump compatibility needed to work with equipment originally designed to run traditional mineral oil based fluids.
The best choice is to use a low toxicity biohydrocarbon hydraulic fluid, gear oil or water repellent extreme pressure grease – such as EnviroLogic 2 WREP grease – that readily biodegrades, performs like a high-quality, stable mineral oil, offers a long service life and is based on sustainable technology. These products are now a reality, but at an increased acquisition cost over other EAL technologies. For companies whose policies demand the highest performing, safest options, these hydraulic fluids based on biohydrocarbons are the most reliable and longest-lasting sustainable option.
No one wants to give up performance when they consider new fluid choices. Initial acquisition cost should be considered, but overlooking the long-term costs – and often savings – associated with the newer EAL technologies is a mistake. A low-cost, unstable lubricant, regardless of base oil technology, will ultimately cost the user more than a higher quality EAL when product lifetime and spill costs are considered. It is also important to remember that while base oil type impacts product performance and service lifetime, it’s often the additive packages specified by the fluid designer that stabilize and bring the final stability, lubricity and wear characteristics to the finished product. For pile driving applications, a high-performance triglyceride formula with a high-quality additive package designed for marine applications is often the best value to minimize total cost of ownership. A different product type may need to be considered based on the project. For example, building a marina may call for a product that is most stable when it comes into contact with water such as a bio-based hydrocarbon.
When we think of VGP-compliant products, hydraulic fluids, oils and greases come to mind first. An often overlooked category is the cleaner technology used for equipment wash-down and maintenance. Cleaners are typically 100 per cent loss products and are released partially – and often fully – into the environment. Once again, the VGP specifies cleaner characteristics that simplify the selection of a safe, effective and sustainable cleaner. The best cleaners are effective, readily biodegradable, phosphate free and are designed to minimize hazards to the workers using them. This user safety aspect is often overlooked when selecting a cleaner technology. Always consult the product safety data sheet (SDS) to determine product hazards prior to specifying and/or purchasing a cleaning technology. Also, know the application equipment that will be used to apply the cleaners as that can influence choice. For instance, some cleaners pose inhalation hazards when atomized during spray application. As with the EAL, there are effective, safe and sustainable cleaner technologies available. The best cleaners use readily biodegradable bio-based surfactants at a near-neutral pH (again, always verify this with the SDS prior to purchase and use) to effectively clean surfaces without exposing workers to caustic or acidic solutions and fumes.
Choosing the right fluids based on total lifetime cost and liability concerns is the new normal for our industry. In pile driving operations, oil and lubricant spills and release of cleaners are unavoidable. We must select fluids that offer the best performance and the least liability to minimize long-term lifetime costs. While price and performance are often linked, the market paradigm is shifting focus to total cost of ownership over the service life of the products.
Dr. Larry Beaver is vice president of research and development at RSC Chemical Solutions. He oversees research and development, regulatory and environmental functions for all divisions of the company.
For more than 30 years, Beaver has been actively involved in the commercialization of safer consumer and industrial chemical products. His experience ranges from developing low-VOC waterborne coatings to creating safer alternatives to replace arsenic-based wood preservatives. His current research efforts focus on safer, sustainable cleaners, degreasers, specialty lubricants and functional fluids for both DIY and commercial use.
Beaver has spoken on various regulatory topics at the international, national and regional levels. He is considered an expert in VOC regulations (CARB, SCAQMD, OTC, LADCO) and formulating products to meet those requirements.