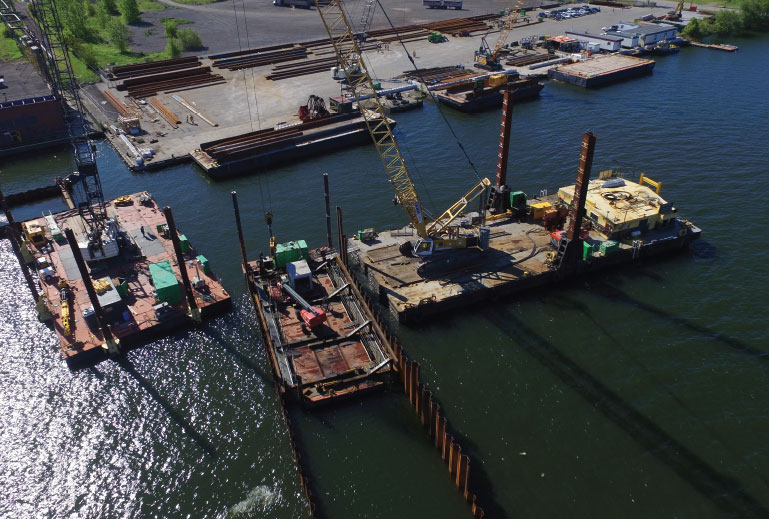
For more than 150 years, Hamilton Harbour, the largest harbour on the western side of Lake Ontario, has played an important role in the course of Canadian history. Heavy industry, including textile factories, meat-packing centres and steel mills, flourished along its shoreline long before the concept of environmental protection.
As a result, Hamilton Harbour now contains the largest toxic sediment site on the Canadian side of the Great Lakes. Randle Reef, located in the harbour’s southwest corner, carries an estimated 675,000 cubic metres of sediment loaded with over 100 years’ worth of deadly chemicals from industry and local wastewater plants run-off.
In the later 1980s, when Canada and the U.S. identified 43 Areas of Concern (AOC) in the Great Lakes, Hamilton Harbour was at the top of the Canadian list.
In response, a coalition of governments, corporations and local organizations moved forward with the Hamilton Harbour Remedial Action Plan (HHRAP). Today, seven funding partners have committed $138.9 million to the Randle Reef Sediment Remediation project: Environment Canada, Ontario Ministry of Environment, City of Hamilton, Hamilton Port Authority, City of Burlington, Regional Municipality of Halton and Stelco (US Steel).
Riggs Engineering Ltd. developed and designed the solution: an engineered containment facility (ECF) placed over the densest area of contamination. Covering 6.2 hectares (equal to nine football fields), the ECF consists of double steel sheet pile walls driven into the harbour floor. Any remaining contaminants would be dredged and placed inside, the entire structure then permanently capped to isolate the toxins from the harbour ecosystem.
In May 2016, subcontracted to McNally Construction, Bermingham Foundation Solutions began Stage One of the project: installing the steel sheet piling for the massive double-walled enclosure.
“The ECF is essentially two sheet pile walls tied together with walers and tie rods, then backfilled with rock in between so they act as one stable structure,” said Jeff Thomson, Bermingham’s project manager for Randle Reef. “The outer or face wall acts essentially as a structural wall, driven deep for strength, while the inner anchor wall is made up of a very low permeable steel environment wall to hold back the sediment.”
These walls were all cold rolled sheet piling coming through the Roll Form Group, a division of Samuel. The inner wall consists of Waterloo Barrier® sheet piles featuring an enlarged interlock system that will later be sealed with an epoxy grout, ensuring an impermeable barrier. For this purpose, Bermingham used WEZ95: 0.375 inches (9.50 mm) thick, 25 inches (635 mm) wide, each sheet weighing in at 50.5 lbs/lineal foot.
“ While we were driving the sheet piles, we also had to consider disturbing the contaminated lakebed as little as possible.”
Jeff Thomson, Bermingham Foundation Solutions
“The lengths varied slightly depending on the ground conditions around the perimeter of the structure, averaging about 70 feet,” said Thomson. “But in some places along the outer wall, we were looking at 100 feet, making it very challenging at times.”
And then there was the danger of the wind coming off Lake Ontario catching a 100-foot sheet pile and turning it into one very big sail.
“We had to plan our work each day according to wind and weather forecasts,” said Thomson. “Environment Canada was a big help, sending us specialized forecasts specific to the Public Works project.” Large equipment barges provided by McNally also played an important part in ensuring the stability of the operation. But what was beneath the water posed its own unique challenge. As Thomson put it, “While we were driving the sheet piles, we also had to consider disturbing the contaminated lakebed as little as possible.”
The solution was to implement a floating template system that would minimize the amount of falsework. Mounted on a smaller sectional barge held in place by temporary spuds, the falsework was moved along the wall as it was being installed. But then that made it more difficult to brace against and stay on location at the same time. The workhorse cranes out there on the barges were a Liebherr 895 and a Terex 165 Ton.
“The main tools we used to install the sheet piling were large, high frequency vibratory hammers to set the two walls and diesel impact hammers to make the final grade,” said Thomson. “The B-5505 diesel hammers are Bermingham designed, produced and sold by our manufacturing division. And we developed a sheet pile adaptor that helped us drive the longer, heavier face wall sheet piles. It’s a big advantage for us to be able to modify our own equipment to fit the needs of the job. When it gets into challenging situations like this, not everything works all the time,” said Thomson. “You have to stay on top of it, monitor and adjust accordingly.”
Bermingham completed the western half of the ECF and sealed it off by driving a 300-metre internal wall across what will be the middle of the final structure, cycling four shifts from May to the end of July.
“That allowed enough time for McNally to finish and secure the cell by December so there would be no detrimental effects from the coming winter conditions,” said Thomson. Beginning again in April 2018, Bermingham will accomplish its sheet pile installation scope of work by the end of summer and turn completion over to McNally.
“We had a good team out there in terms of working with Riggs Engineering and McNally, the general contractor,” said Thomson. “McNally was the marine support, providing tug boats, relocating barges around the work areas, bringing materials out to us. It made for a very good partnership, allowing us to focus on our job – installing the sheet piles.”
In the final count, Bermingham crews drove 1,650 pairs of sheet piles, with the face wall extending a little over one metre and the anchor wall about three metres above the waterline. By 2020, most of the contaminated sediments from the harbour floor will be inside the ECF; by 2023 any water will be removed and the contained sediment compacted, weighed down and sealed in with an impermeable cap. At that time, the Hamilton Port Authority will accept ownership.
It is a job well done, on many different levels. Using generations of field experience and its capability to adapt to changing situations, Bermingham Foundation Solutions has contributed to the elimination of a significant source of contamination in the Great Lakes for the benefit of today and into the future.