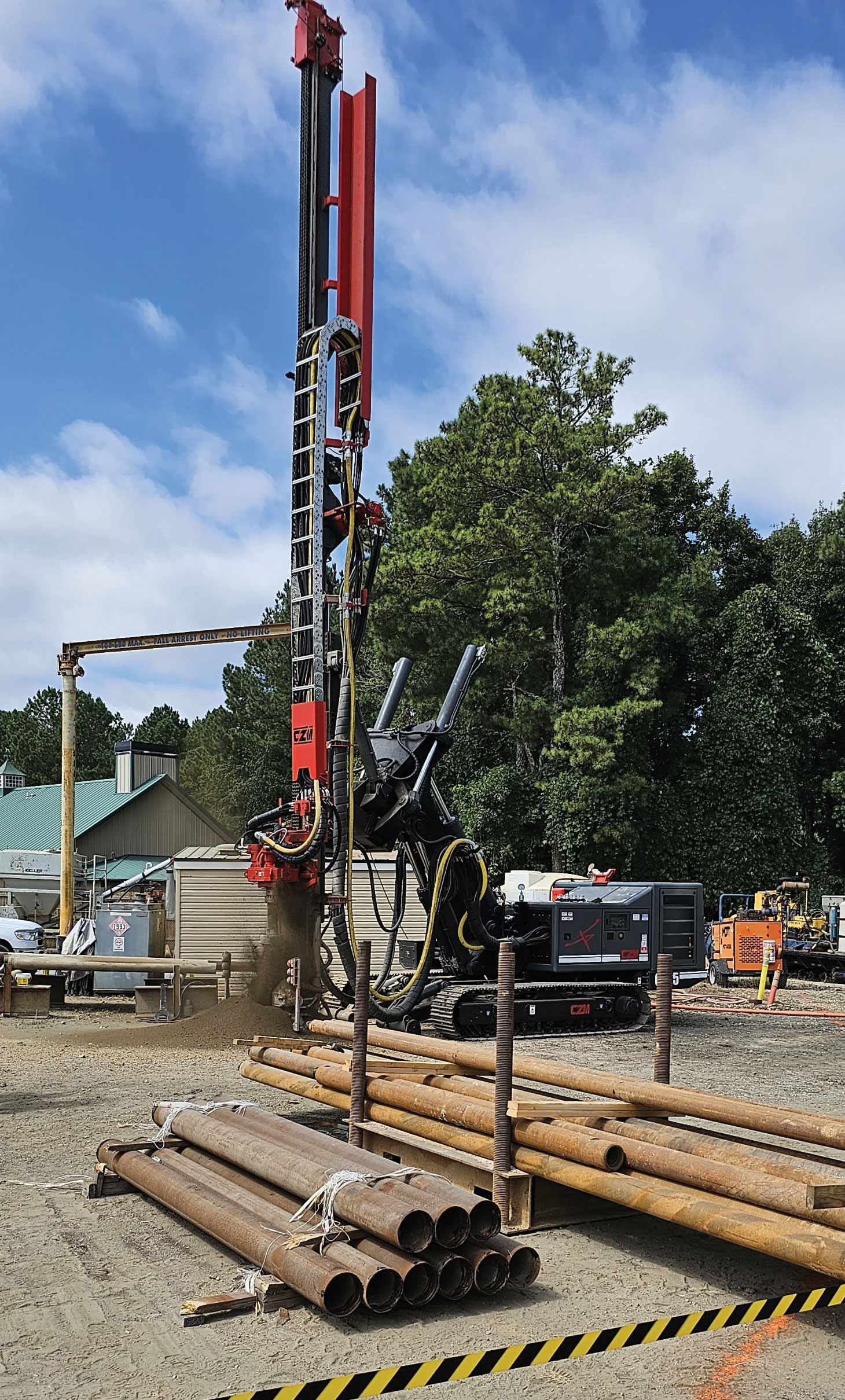
In March, CZM Foundation Equipment (CZM) released its advanced micropile drilling machine, the CR25, specifically developed to fulfil the needs of the North American piling industry. Manufactured in the United States on a Cummins B6.7 base, the robust CR25 was designed to be the most productive and reliable in the market, the latest in CZM’s comprehensive line of drilling rigs engineered for various foundation applications.
One of the largest micropile machines on the market, coming in at 31,751 kilograms (kg) (70,000 pounds [lbs]) operational weight, the CR25 can perform micropiles, tie-backs and jet grouting in the toughest soil conditions. The extendable undercarriage delivers extreme stability, especially with large diameter micropiles on long mast configuration. The engine’s power management system along with an optimized hydraulic system means reduced fuel consumption by up to 30 per cent, guaranteeing very high productivity.
Innovative design from the beginning
The CR25 is the first in a line of new micropile machines, the product of decades of design experience and innovation.
“CZM was started in 1976 by my grandfather who was working as a mechanic for a construction company,” said Guiliano Clo, president of CZM. “He acquired some machinery and eventually started an equipment rental company. Later he began designing and making his own foundation equipment.”
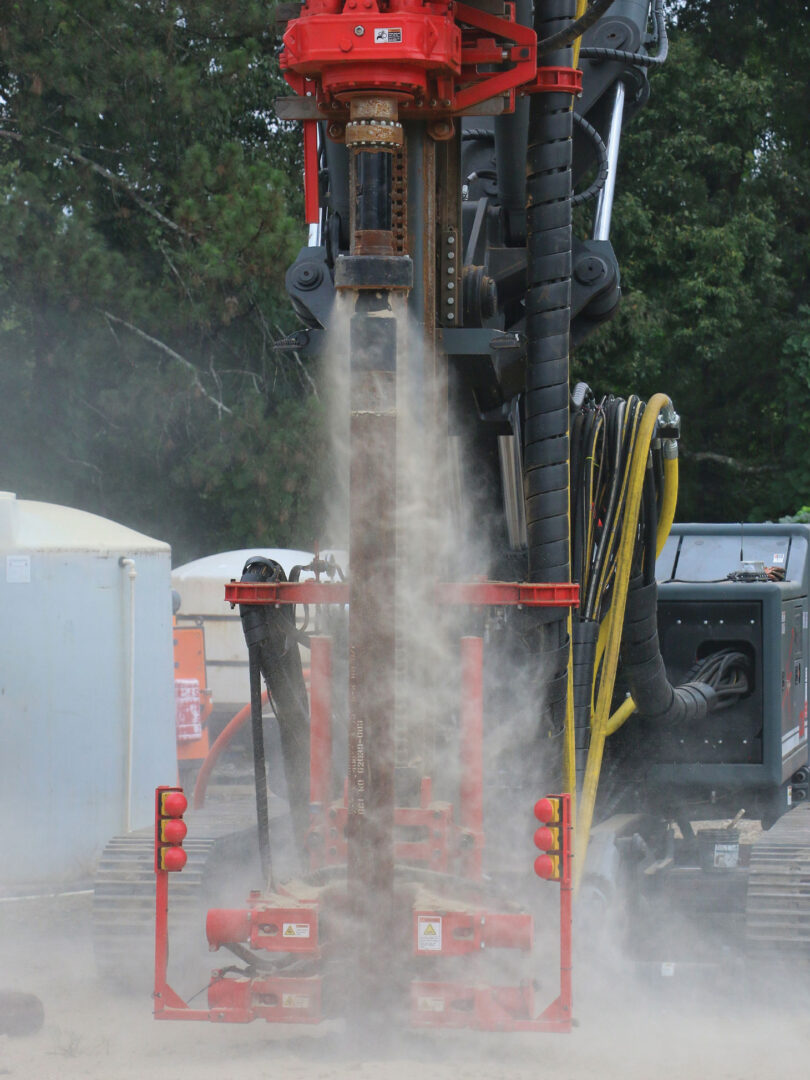
That first piece of equipment was a crane attachment rotary table designed to drill to 260 feet (ft.) in depth. From there the company grew and eventually changed the focus from crane rentals to foundation equipment manufacturing. Today CZM has three design teams: one in the U.S., one in Italy and one in Brazil. In 2012 CZM USA was incorporated to better serve the North American market, and between 2014 and 2019 expanded the product line to include all types of foundation applications, such as drilled shafts on a long or short mast configuration, cylinder crowd and cable crowd, long reach, continuous flight auger, micropiles, hydraulic hammer pile driving and more.
“It’s a robust machine, hugely effective with very high horsepower – a lot of pull-back force for larger and deeper micropiles.”
Guiliano Clo, CZM Foundation Equipment
The CR25 is the company’s latest response to market needs as the CZM expert designers worked to develop an advanced drilling rig, the evolution of technology for micropile drilling machines. In the design phase, they paid particular attention to the machine’s stability during both the transition and the drilling phase, and above all, during the execution of tie-backs with the mast transversal to the undercarriage.
“It’s a robust machine, hugely effective with very high horsepower – a lot of pull-back force for larger and deeper micropiles,” said Clo. “Like all our micropile machines, it has expandable crawlers to give it more stability, especially when doing tie-backs.”
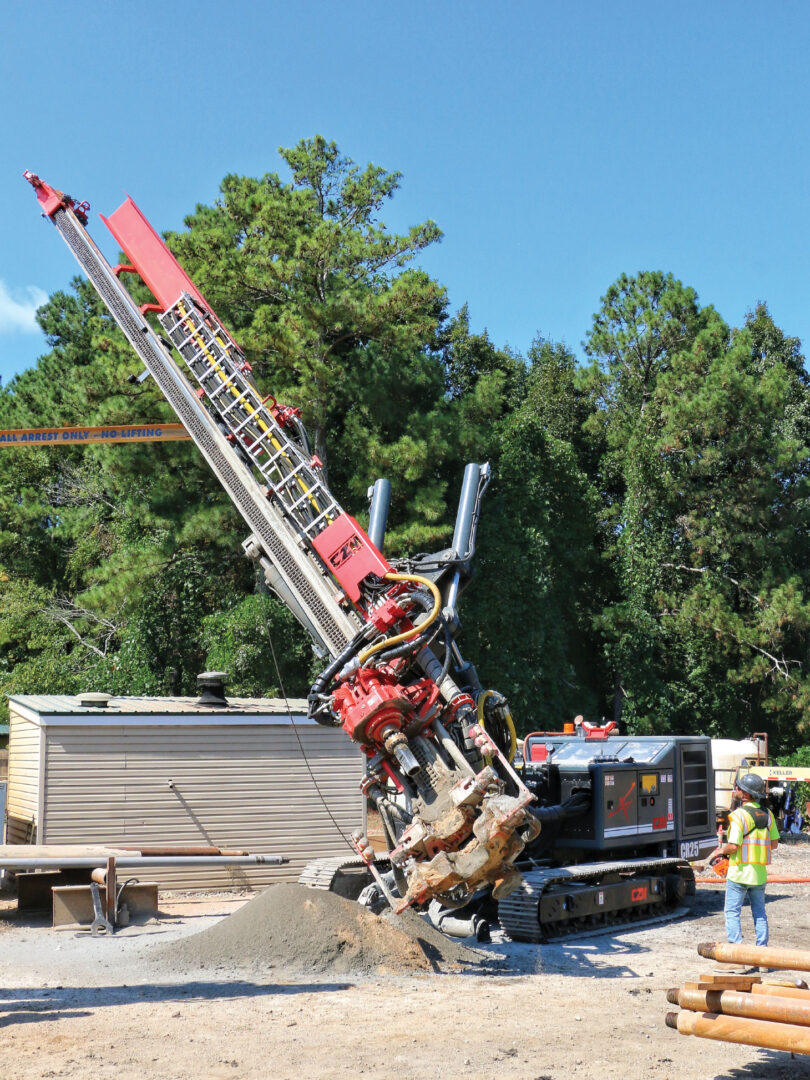
Maximum size for strength and stability
With its generous larger dimensions, the CR25 is extremely robust with double boom cylinders to ensure safety and efficiency in more challenging articulation positions. The undercarriage consists of a wheelbase of 10 ft., a length of 12 ft. 6 inches (in.) and a retracted width of 8 ft. 2 in. with 11 ft. 6 in. in the extended work position. All parts, including the modular mast, are made with high-yield strength Weldox steel to guarantee ultimate safety in all working positions.
Front-of-the-wall kinematics allow the machine to drill parallel to the tracks, guaranteeing a continuous movement of approximately 93 degrees. Integrated into the base mast and driven by a motor reducer and chain with an automatic tensioner, the crowd/pull-back system can deliver up to 18,000 kg (39,680 lbs) force to a maximum stroke of 10.5 metres (34 ft. 5 in.), enabling it to work with long sections of drilling rods.
Telescopic expandable tracks guarantee safety and manoeuvrability even with lattice extensions for the execution of jet grouting injections for useful depths of 30 metres during transition, positioning and operation movements.
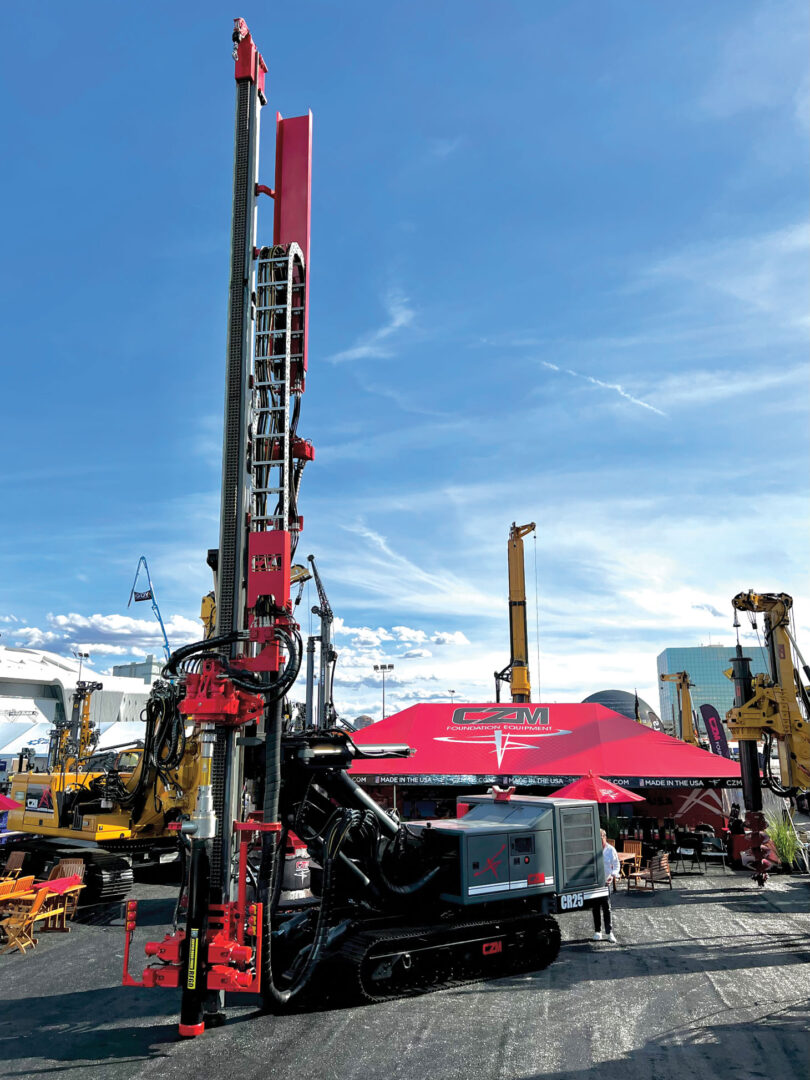
Efficiency for productivity and the environment
Equipped with a powerful Cummins B6.7, Stage V engine delivering 231 kilowatts (310 horsepower), the CR25 drilling rig maintains fast and precise mobility. The power management system along with optimization of the hydraulic system ensures the ideal use of engine power, reducing fuel consumption by up to 30 per cent and decreasing emissions. This maximizing of the system efficiency guarantees a result of very high productivity.
Everything under control
“The CR25 has a lot of technology on it,” said Clo. “Its unique computer system is designed to be easy for the driver to customize.”
“Being manufactured in the United States means parts and machines are available and more easily delivered and affordable.”
Guiliano Clo, CZM Foundation Equipment
The latest generation radio command allows the operator to manage the entire machine through the 11-in. colour touch screen. The state-of-the-art electronic system manages all machine setting operations such as: general telematics, fault diagnosis, speed customization, operational security, passive safety, real-time remote control and remote control management.
Special capabilities for versatility
The CR25 can accommodate a range of accessories, including a variety of carousels, cranes, water pumps, etc. The innovative servo-assisted proportional hydraulic circuit and the high hydraulic oil flow guarantee flexibility for installing different types of rotary heads and rotary drillers, including double rotary while delivering the declared power without performance reductions.
The CR25’s jet grouting application can drill up to 30 metres deep (100 ft.) with integration into a treatment monitoring system for quality control. As a standard feature, sliding clamps with a stroke of 1,000 millimetres and pull-back force of 20 tonnes (33,000 lbs) can install double or triple clamps with 14- to 18-in. maximum diameters.
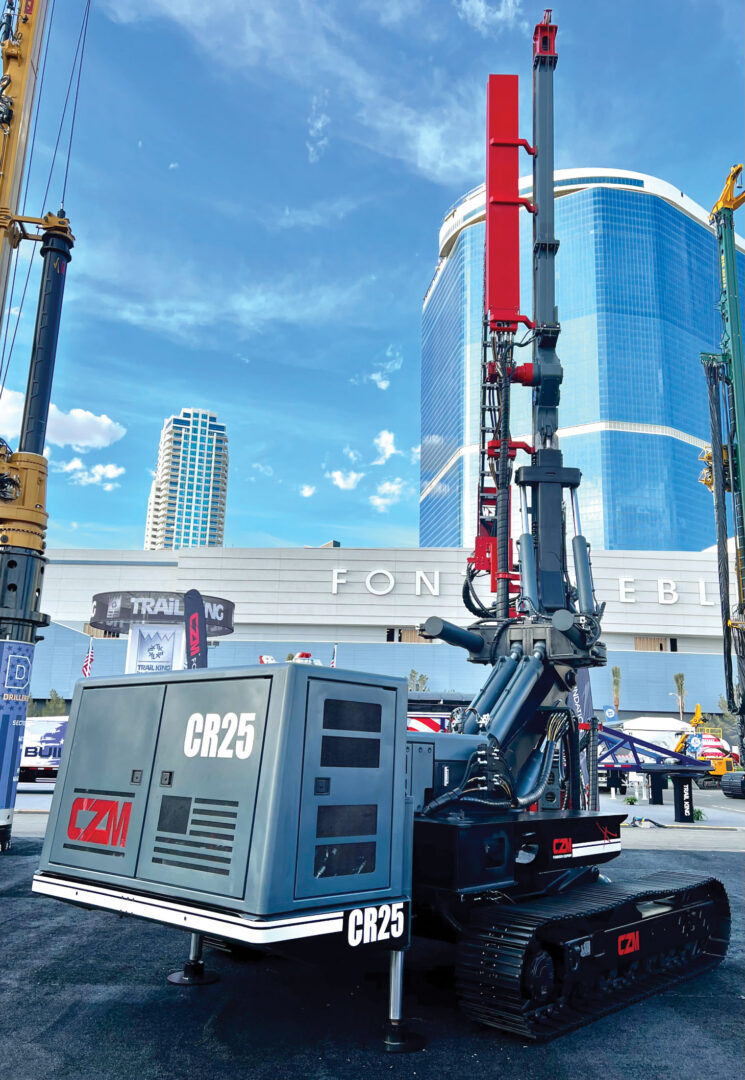
Reliability and reduced maintenance costs
“We’ve selected very high-end components, parts and gauges, and have put a lot of thought into the filtration of the hydraulic system to make the components last and also to extend the length of time before changing the hydraulic fluid,” said Clo. “It’s our only machine that has been completely made in our new factory of 48,000 sq. ft. outside Savannah, Ga., which is also the location of our North American headquarters. Being manufactured in the United States means parts and machines are available and more easily delivered and affordable, shortening any wait time for maintenance and repairs.”
CZM is working to extend their micropile machine line, and next up is the CR18 to be ready for the International Foundation Congress & Equipment Expo in Dallas, Texas, in May. Meanwhile, the CR10 should be available by the end of 2024. These machines are smaller in size, but with all the capabilities of the CR25. The company is also looking into making more attachments for tie-backs.
“Since 2012, we have been designing new equipment and making modifications to specifically serve the North American market and now can offer three models made in the United States. Our plan is to extend that to over 30,” said Clo. “We may not be the least expensive machine on the market, but we believe we offer one of the lowest ownership costs and our designs are a very good investment for the North American piling industry.”