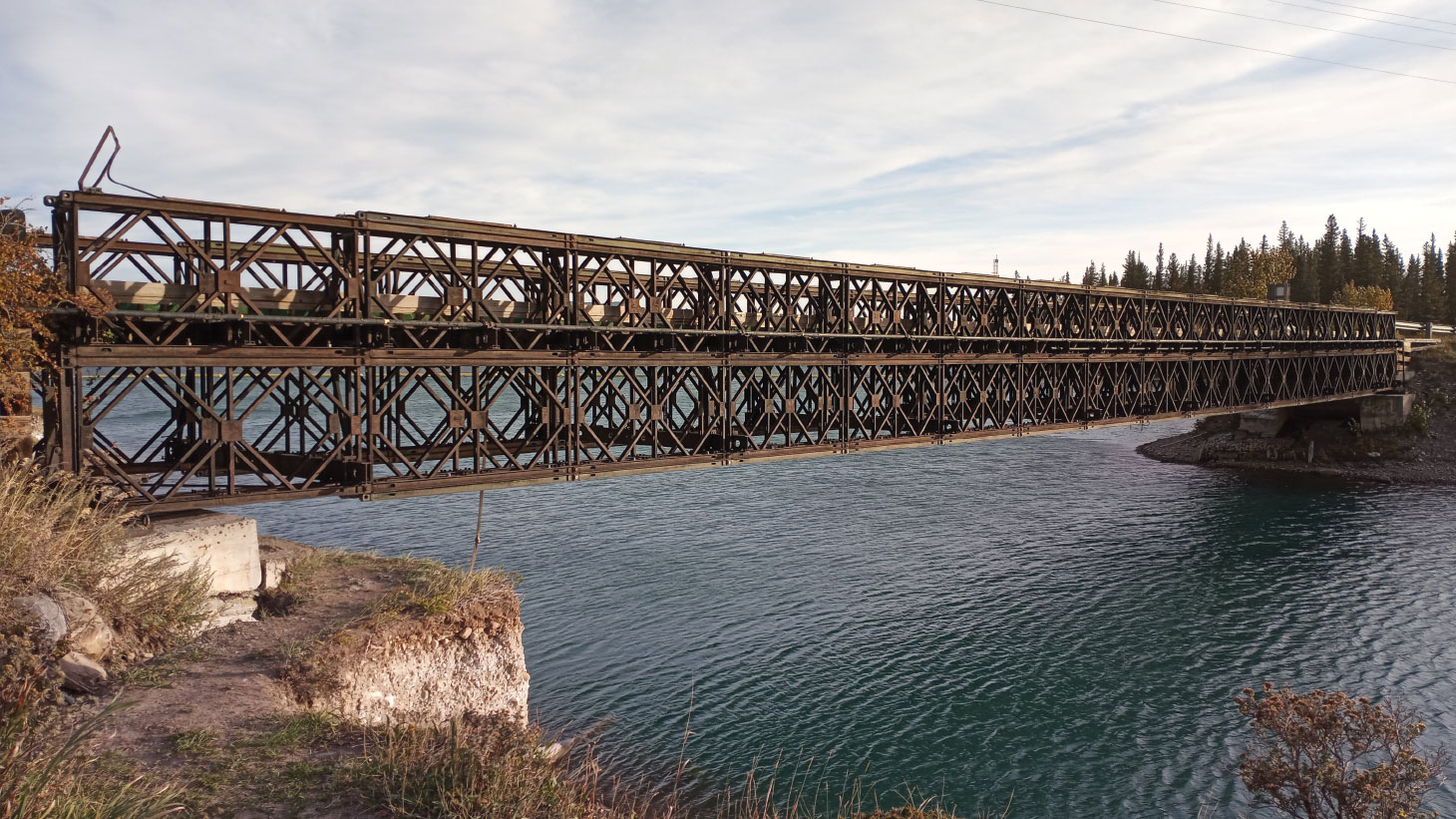
During the Second World War, retreating Axis forces destroyed almost all the bridges behind them to prevent the Allied forces from advancing. Replacement bridges had to be capable of supporting live loads ranging from troop-carrying vehicles to heavily armoured tanks, but First World War bridging equipment could not be scaled up to provide the necessary load capacity.
Donald Bailey, a civil engineer and model bridge enthusiast working for Britain’s Royal Engineers Experimental Bridging Establishment and the War Office, developed his new modular bridge design in 1936. By 1940, Bailey’s modular design was considered the superior choice for temporary use as the war progressed. Full production began in July 1941, and the Royal Engineers carried out the first operational deployment of a Bailey Bridge in Tunisia only months later during the North African Campaign in 1942.
Key to the design’s success was its flexibility, simplicity of manufacture and ease of assembly, says Linda Newton, retired military engineer, infrastructure asset management professional and member of the Canadian Society of Civil Engineers National History Committee’s Historic Bridge Task Group.
“To the average Canadian, ‘double-double’ conjures up the image of a cup of coffee, but to military engineers, it means something completely different.”
Linda Newton, Canadian Society of Civil Engineers
Eventually, up to 25,000 bridge panels a month were made in hundreds of factories, including by local industries in captured areas. Manufactured to be interchangeable, components also had to fit into standard General Service Vehicles, be made of standard steel alloys since light-weight materials such as aluminum were scarce during the war, couldn’t exceed 272 kilograms because they had to be lifted and assembled by four to six men without machinery or cranes; and had to be simple and quick to assemble and dismantle with no on-site fabrication or modification – a bridge had to be built under any conditions, including in darkness or under enemy gunfire.
Accommodating extraordinary loads over impressive distances
Multiple configurations were possible – single-, double- and triple-trussing to support a single storey and double- and triple-trussing to support two or three storeys. “To the average Canadian, ‘double-double’ conjures up the image of a cup of coffee, but to military engineers, it means something completely different,” said Newton.
The modular design allowed engineers to build each bridge as long and as strong as needed, doubling or tripling the supportive side panels or on the roadbed sections.
The primary bridge consisted of three main parts, with its strength provided by the side panels, which were cross-braced welded-steel rectangles three metres long and 1.5 metres high. The bridge’s floor consisted of 5.8-metre-wide cross girders or transoms that rested on the lower chord of the panels and ran across the bridge, with three-metre-long stringers running between them on the bottom, forming a square, and clamps holding them together. Stringers were placed on top of the completed structural frame, and wood planking set on top of the stringers provided a roadbed. Flat rails bolted the planking to the stringers. Steel plates could cover the planking to resist being damaged by tank tracks.
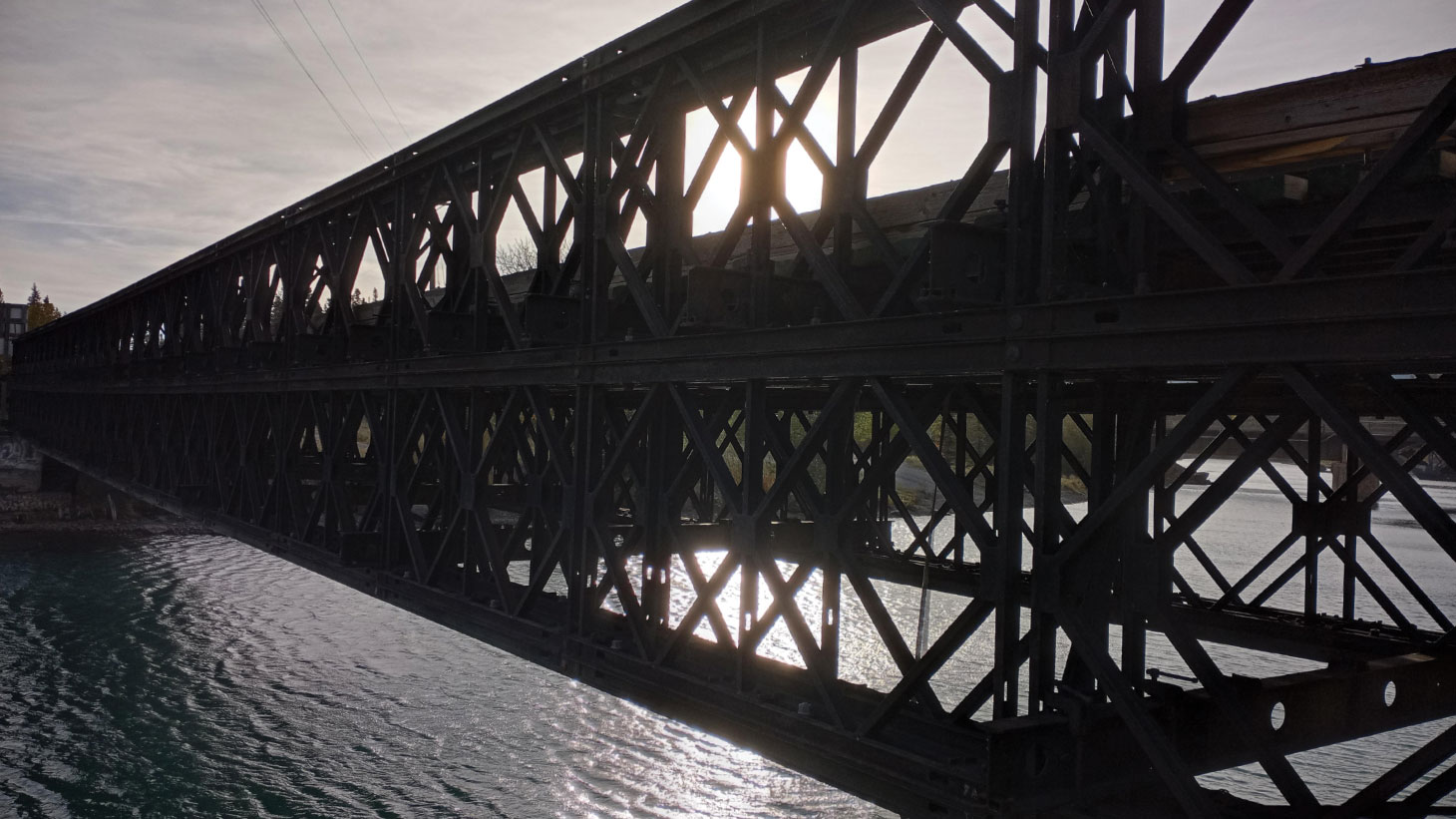
After each three-metre-long section of the bridge was complete, it was typically pushed forward over rollers on the bridgehead, and another section was built behind it, connected to the first by pins pounded into holes in the corners of the panels. A Bailey bridge could be launched from one side of a gap by using wedges to angle the front-most portion of the bridge skeleton (still without its roadbed and flat rails) up into a “launching nose,” pushed across the gap on rollers using the workforce or a vehicle. The rollers would be removed with the help of jacks, and the rails and roadbed would be installed along with any additional panels and transoms.
Depending on the spans and configurations, the bridges could accommodate extraordinary loads over impressive distances, including heavily armoured tanks over 60-metre spans. Footways for pedestrians could also be installed outside the side panels, forming an effective safety barrier between foot and vehicle traffic.
“It is a testament to their robust design that many of these ‘temporary’ bridges remain in use after so many decades.”
Linda Newton, Canadian Society of Civil Engineers
“Under average conditions, an engineer troop of 40 men could assemble a 24.3-metre double truss single-storey bridge in four hours by day and eight hours at night,” said Newton.
She also says the Corps of Royal Canadian Engineers (RCE) built one of the first bridges while under enemy fire, the 15-metre Leonforte Bridge over Sicily’s Dittiano River, in 4.5 hours. Soon, floating bridges incorporating pontoons, suspension bridges and lift bridges were also introduced, including two 10-metre-long lift-bridge versions constructed by the RCE over canals in Belgium, one of which could be raised in 14 minutes and lowered in four. Multi-span bridges often use existing piers to span more significant gaps.
In 1945, to support the advance into Germany, the RCE built the high-capacity Blackfriars Bridge across the Rhine River, which opened for traffic only two days after construction began. At 558 metres, it was the longest Bailey bridge at the time, designed to carry military Class 40 loads. Its fully floating pontoon section comprised 34 connected spans of almost 13 metres each and one span of nearly 10 metres long.
During the war, the Allies erected more than 4,500 Bailey bridges – more than 200 miles – which came to be considered among the most important engineering contributions to victory. In 1946, Bailey was knighted for his bridge design.
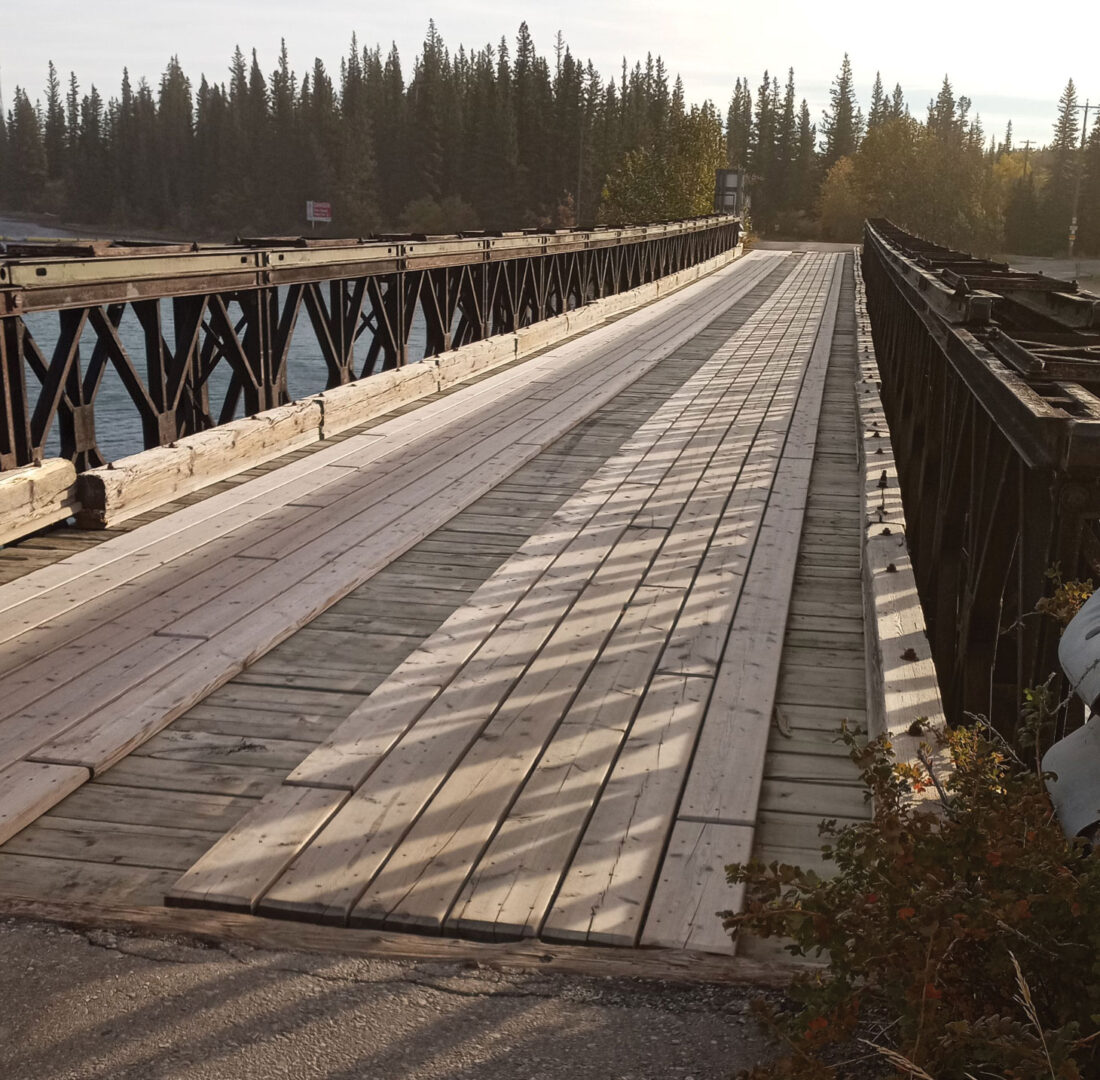
The bridges were crucial for the Allies’ victory
Newton says some of the oldest Bailey bridges still in use can be found in Canada. The Ontario government, which purchased huge amounts of war-surplus Bailey bridging following the war, used some of it to construct replacement bridges in the Toronto area after Hurricane Hazel in 1954. One of those, the Old Finch Avenue Bailey bridge, is still being used today, as is a 72-year-old pedestrian bridge over Toronto’s Lakeshore Boulevard, built by Dominion Bridge Company to connect Exhibition Place to the Lake Ontario waterfront.
“It is a testament to their robust design that many of these ‘temporary’ bridges remain in use after so many decades,” she said.
Bailey’s legacy of modular bridges has been emulated by companies such as Mabey and Acrow, which produce modified versions of the Bailey bridge. China still produces a large volume of the original Bailey design, says Newton, and Bailey bridges are in regular use worldwide, particularly as a means of bridging in remote regions and as a temporary or emergency solution to reconnect communities after natural disasters or during construction. Canada’s most recently built Bailey bridge is the 85-metre double-double Chedoke Radial Trail Bridge, built in 2020 near Hamilton, Ont.
During the war, the Allies erected more than 4,500 Bailey bridges – more than 200 miles – which came to be considered among the most important engineering contributions to victory.
Although the newer modular bridges might look like the original Bailey and even be called Bailey bridges, Newton says that advances in high-performance steel and composite materials have led to modifications to the panels, decking and beams, making manufacturing quicker and improving precision and performance in terms of load-bearing capacity and reduced maintenance. For example, decking is no longer wood and bridges can be adapted ahead of time to meet specific requirements.
But although such bridges still retain the concept of modular design and interchangeable components, few can be built and disassembled by hand and reused like the original Bailey bridge, Newton says.
“The legacy of Donald Bailey cannot be overstated. Developed as a simple bridge to support the war effort and the mobility of Allied troops in (the Second World War), the Bailey Bridge has become ubiquitous around the world.”