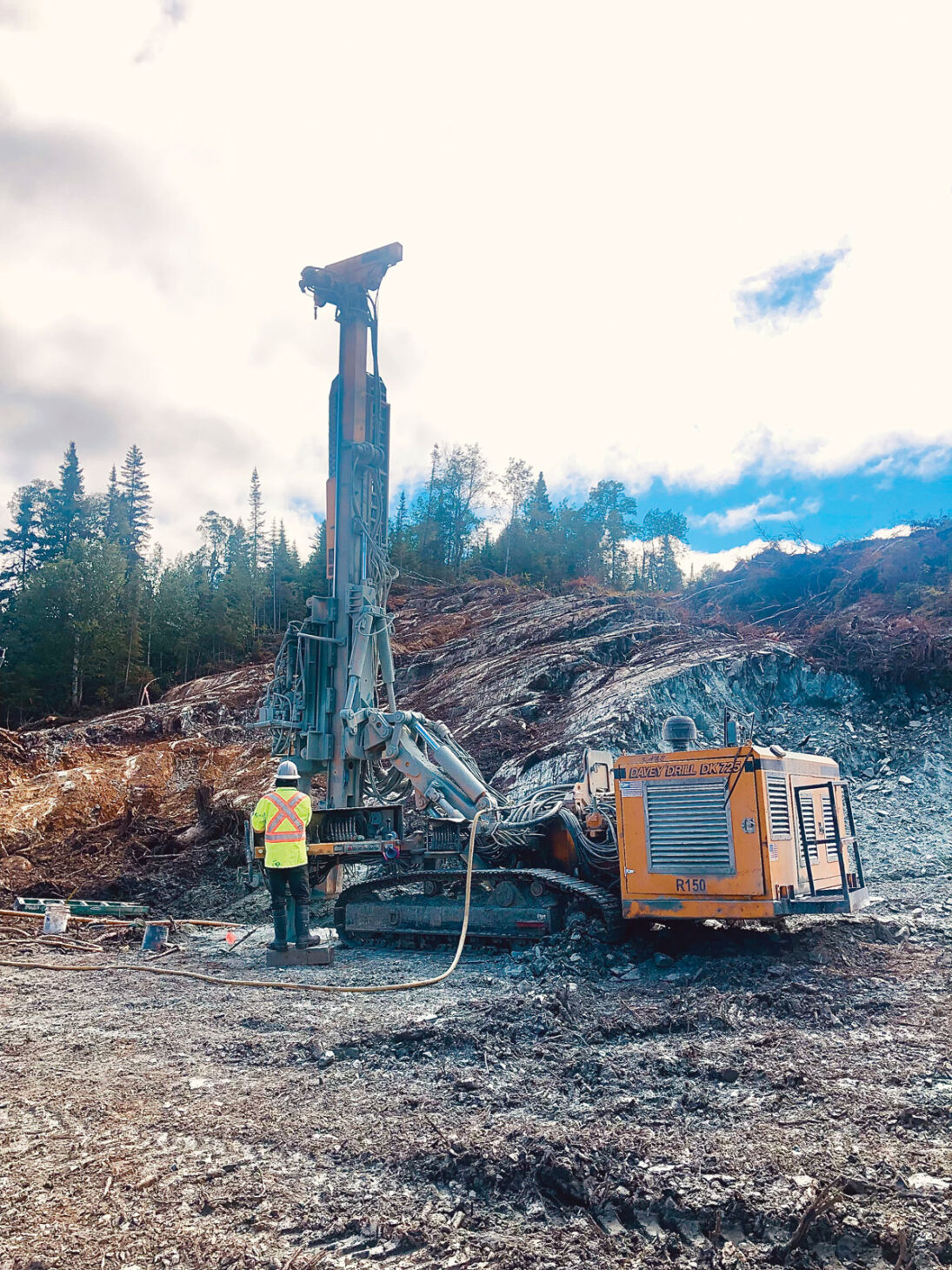
The Canadian Shield is notoriously hard; with granite formations in the range of 150 megapascals in some of Canada’s most dramatic landscapes, it has all the ingredients of a challenging project on an incredibly beautiful backdrop. When a major transmission line contractor approached Doublestar Drilling to partner up with them to build over 450 kilometres of power transmission line with most of the foundations on piles, the answer was immediately, “Yes.”
The Ontario East West Transmission Line (OEWTL) spans from Thunder Bay to Wawa in Northwestern Ontario, ranging across remote locations, deep geological rifts and the very edge of the fabled and mysterious Lake Superior. This type of landscape can be unforgiving and requires many access points to get to a piling location. Just because the next work area is only 300 metres away, does not mean it will take 300 metres to get there.
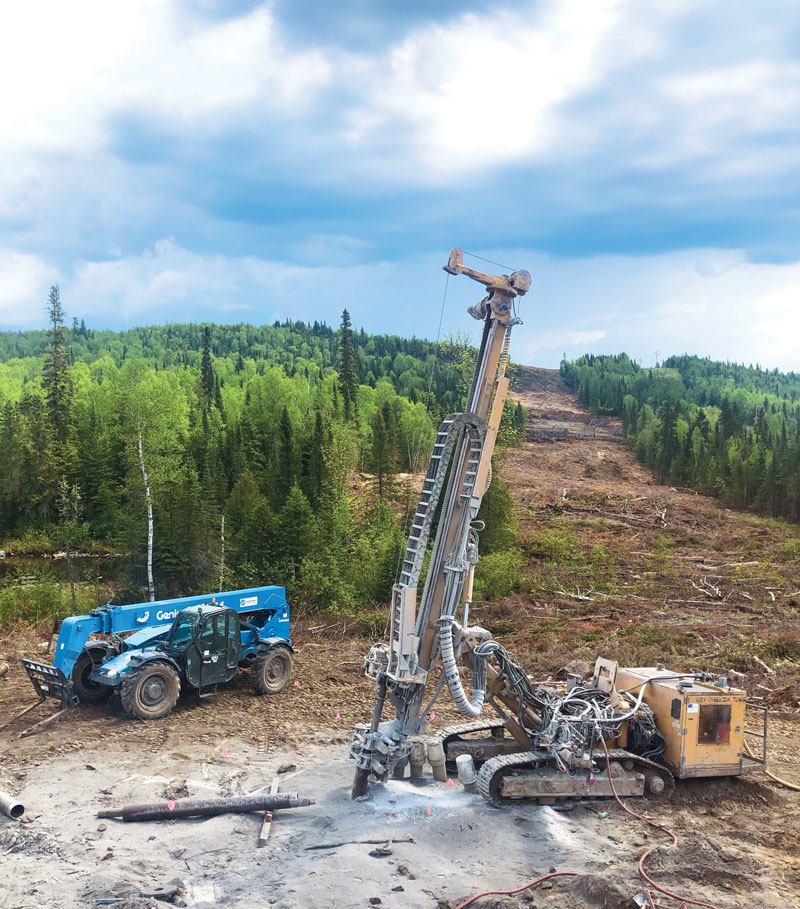
The biggest challenge over the two-year project was unarguably the access to work locations. In many areas the topography was very steep and required pulling equipment in with dozers and excavators due to the grade. Other times, soft areas were prone to deteriorating when inclement weather hit, which was a common occurrence. Working in these remote and challenging locations can be hard on not only equipment, but also people.
Doublestar Drilling equipped up to seven drill rigs and upwards of 70 skilled people worked on rotational shifts, with select crews working 24 hours per day to accommodate winter closure schedules and production targets. The crews consisted of drilling, grouting, logistical and plate installation crews, alongside their safety and project management team. Much of the work was completed using Davey Kent 725 single and dual rotary rigs using a drill-through casing system which left the casing embedded in bedrock to a maximum depth of 2.2 metres. The bond length was then drilled to a length ranging from three to 4.5 metres. All micropiles were vertical or battered at 15 degrees, in groupings of three, four, six or 10 micropiles per leg of each structure.
Before the four-leg lattice tower structures were installed, Doublestar was tasked with installing all thread bar anchors, grouting, pull testing, and cutting and capping each leg. This required a four-step approach to each tower, which needed to be in sequence with the client’s overall schedule, that reflected environmental closures, fire season restrictions, winter roads and a host of other challenges.
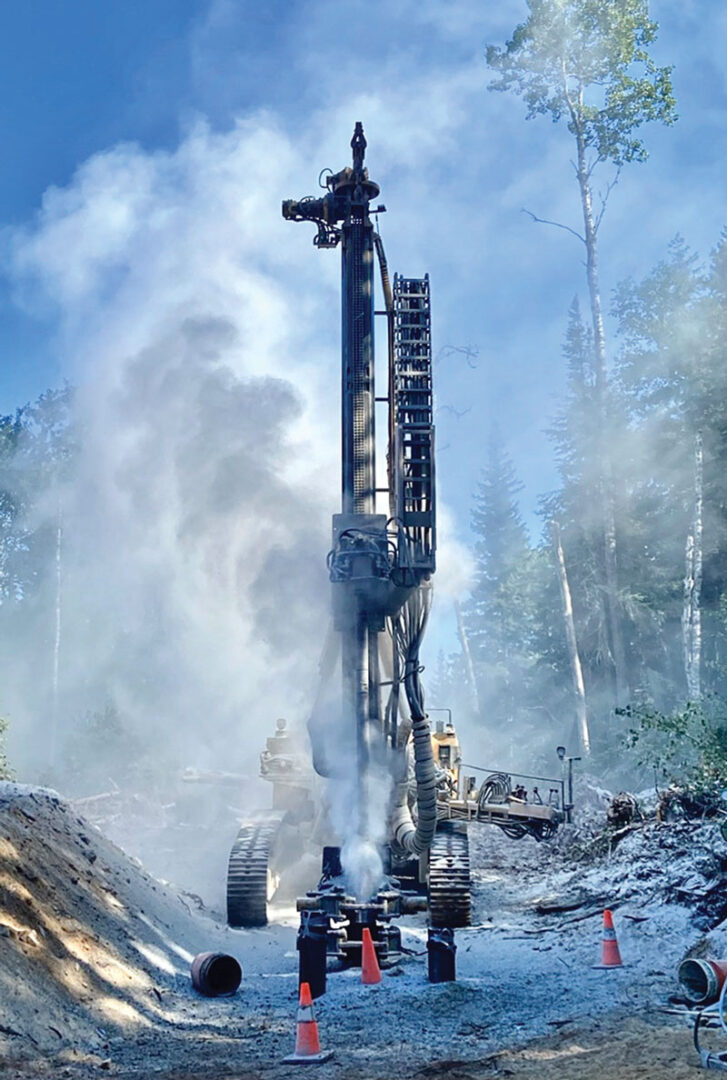
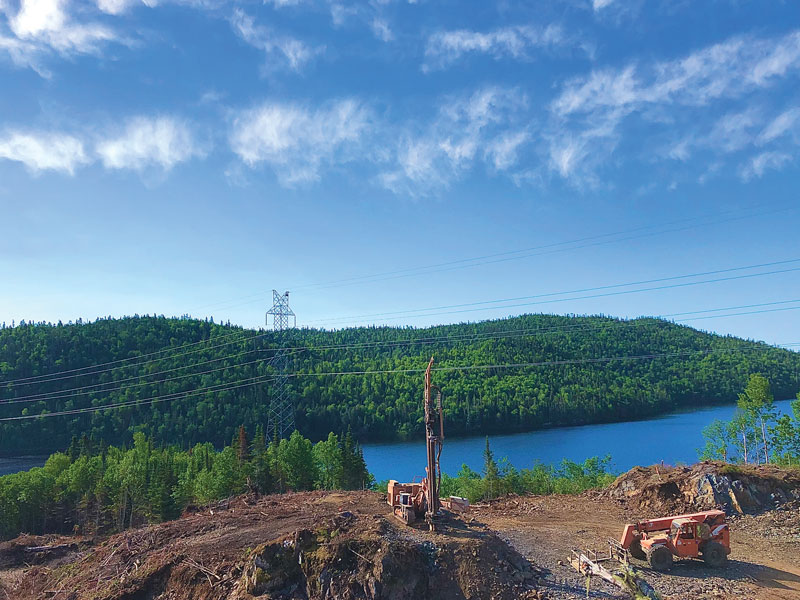
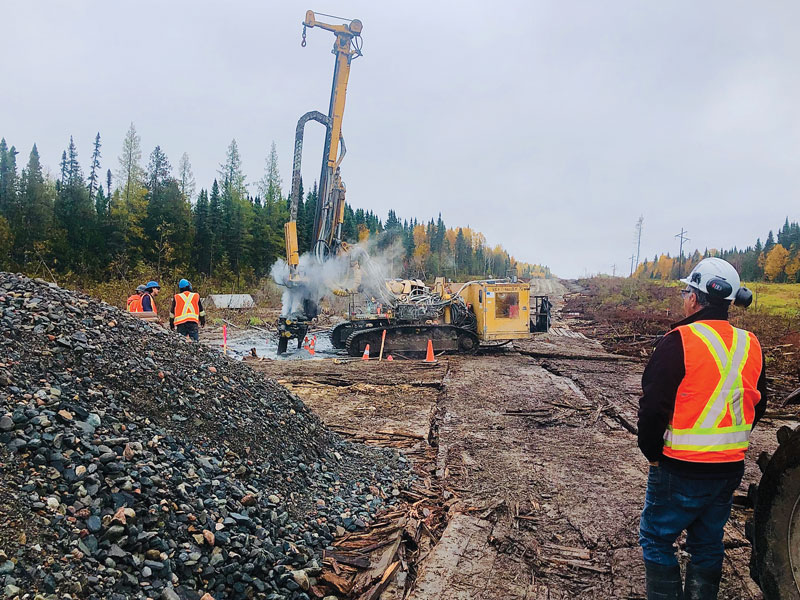
The structures with 10 micropiles per leg required careful measurement of each installation to ensure all battered angles corresponded with the overall design and cap connection. This was no easy feat from a drilling perspective as many locations had variable rock formations, which added to the challenge of maintaining proper angles among groupings of piles.
Doublestar’s project manager, Jillian Thornton said, “[OEWTL] was no ordinary project and Doublestar knew from the beginning it would be a challenging one to undertake. The drilling portion turned out to be the easy part, the hard part was working in remote areas with rough terrain and the logistics and planning that coincide with that. Working closely with our team at Doublestar and our client were key to having an effective work plan and keep the ball rolling.”
Just because the next work area is only 300 metres away, does not mean it will take 300 metres to get there.
The conditions were so tough that Doublestar’s equipment often had to be towed in using large, tracked excavators and dozers. On other occasions, retired army vehicles with oversized six-wheel drive tires as well as flat-deck rock trucks and nodwells were used to get materials to the site, and sometimes even to transport people. One thing that goes hand-in-hand with the limited and challenging access is the inability to efficiently communicate with crews. Cell phones, two-way radios and satellite phones often did not have the service coverage to reach crews.
“Each day we had a daily meeting call where our supervisors made sure to find a spot with service at a specific time where we discussed the activities going on for the day, and where we could plan for the next day activities as well,” said Thornton. “Most times, I would touch base with our crews prior to the work shift or at the end of the shift for communication. They had a means to reach me during the day, but reaching them wasn’t always easy. It wasn’t as easy as just simply driving to structure locations to relay information for status updates either when there are multiple crews working hundreds of kilometres away from you and also hundreds of kilometres away from each other.”
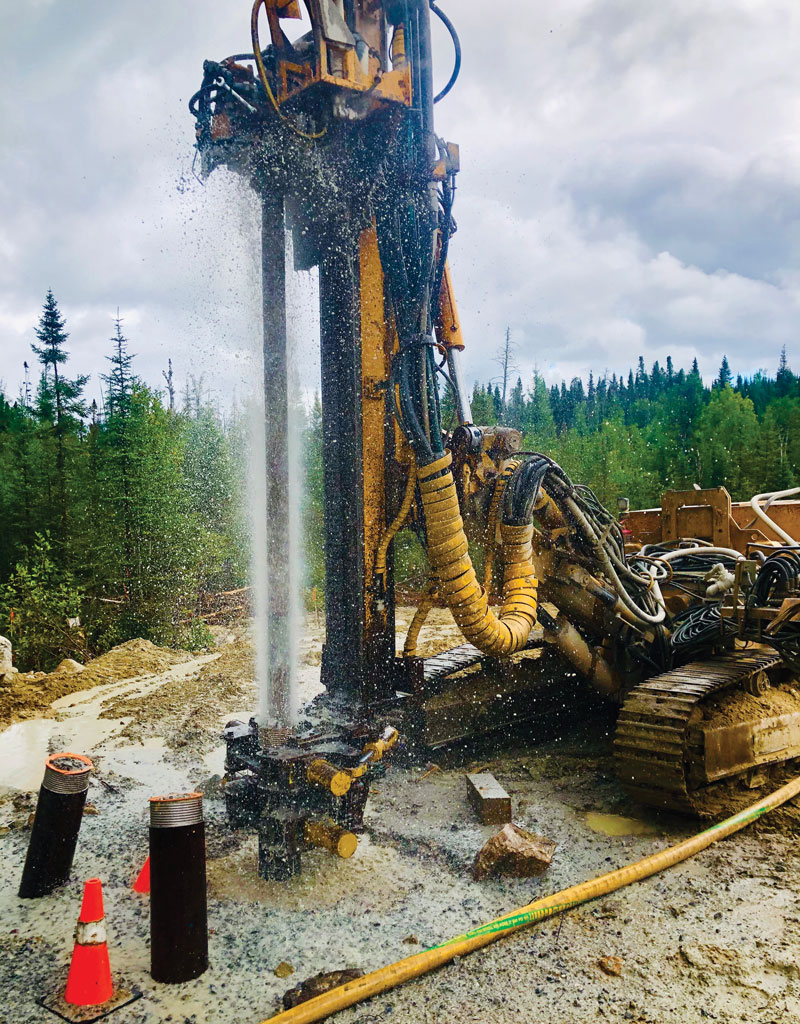
Aside from the toll taken on the rigs and support equipment with the difficult drilling conditions, Doublestar’s most important resource, its people, had their hands full with the remoteness of the work. This made for long days in the field to maximize production hours, on top of the travel required each day to and from site. Each crew worked a 12-hour day to ensure the drive to and from the remote areas resulted in enough production to make the travel cost effective. Having crews work a 20-and-8 rotation, 24-hours/day also took very careful planning to ensure that fatigue management was top of mind.
“Our project staff came from all over Canada, and travelled primarily from Alberta, New Brunswick, British Columbia, and Manitoba to work on the project. Adhering to the rotational schedule was always top of mind for us as they needed rest to ensure a focused approach to the next work shift,” said Thornton.
Each crew worked a 12-hour day to ensure the drive to and from the remote areas resulted in enough production to make the travel cost effective.
Doublestar considers a project of this complexity spanning over two years, a success with over 2,700 piles installed in the rock, adding up to 29,000 lineal metres of micropiles in some very harsh and difficult conditions. In the shadow of Lake Superior’s wind and snow, a total of over 145,000 manhours were worked to complete this massive project, and it shows in the quality of work. Between the weather, wildlife, forest fires and a global pandemic, many challenges were overcome to bring this project to the finish line, meeting their client’s strict schedule timelines.
In addition to the beautiful backdrops and scenic work locations, OEWTL was a great experience for all Doublestar employees and their support contractors. Thornton said, “Managing this size of scope of work unquestionably added a new level of competency for all of us here at Doublestar Drilling and also showcases our expertise in the foundation and piling industry.”
This was important to Doublestar, allowing them to support one of their biggest partners in a major power transmission project; ultimately helping to improve the infrastructure for Ontarians who call the breathtaking shores of Lake Superior and the Canadian Shield their home.