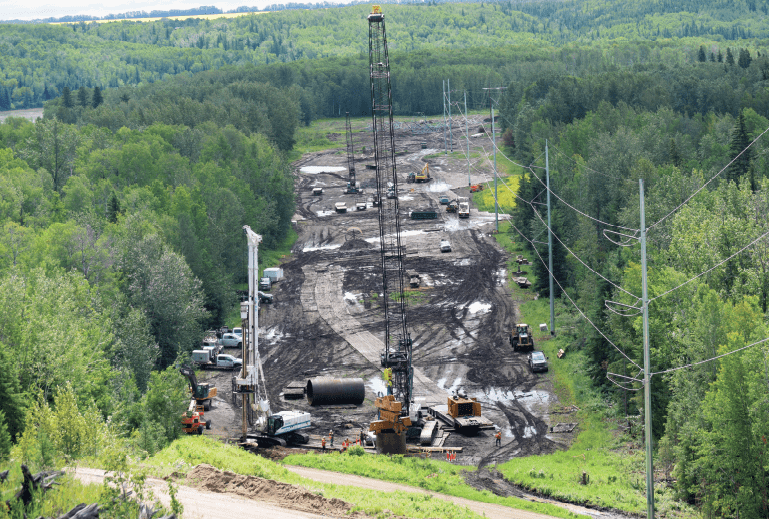
One of the first of its kind in Alberta, the Fort McMurray West 500-kV Transmission Project (WFMAC) is owned by Alberta PowerLine, a partnership between ATCO and Quanta Services, Inc. This is the first project awarded under the newly instituted Competitive Process by the Alberta Electric System Operator.
Working under this partnership, Valard Construction, a Quanta subsidiary, oversaw the full engineering, procurement and construction of 500 kilometres of 500-kV transmission line from the Genesee area west of Edmonton to Fort McMurray in Northern Alberta. Included in this construction were the foundations for two substations that occurred concurrently with the line.
This project required the installation of over 6,500 driven pipe piles, 250 large diameter drilled shaft foundations (requiring over 9,000 cubic metres of concrete) and almost 5,000 helical piles with more than 6,500 extensions being added. All of this work was done in weather that ranged from 35°C during the summer to -45°C in the winter, and in mud, sleet, rain, fog and blizzard conditions. Completed in just 13 months (between September 2017 and October 2018) the bulk of the foundation program was finished over four months early, marking a monumental achievement for Northstar Sharp’s Foundation Specialists.
Unique design considerations
Over the course of 2016, under the direction of Valard and working alongside other Quanta subsidiaries, the project team designed and refined a family of towers and foundations that could accommodate both the stresses of the northern Alberta climate as well as the varied subsurface conditions expected on the project. The focus was on constructability and efficiency in execution.
Then an extensive front-end geotechnical program was initiated under environmental supervision ahead of construction contract execution to help identify critical geotechnical areas. Testing and sampling was completed ahead of the design process to augment the design and procurement phases. This geotechnical process continued alongside the right-of-way (ROW) development and provided geotechnical incite on every proposed foundation site for the project.
Using the data obtained, a comprehensive foundation design package was produced with input from both the transmission line design team and the construction leadership responsible for installations in the field. By involving the field-based teams in the overall design, the Northstar Sharp’s team was well versed with the requirements and project needs prior to construction start.
A team of geotechnical engineers was maintained throughout the project to review incoming site data, assess design applications, assign installation criteria as well as sign off on actual executed installation. The close relationship between design engineering and pile installation allowed for a quick turnaround on technical RFIs, site installation issues or situations where there were geotechnical anomalies that didn’t accurately line up with predicted conditions. The use of field PDAs to confirm design adherence as well as on site QA/QC by engineering helped to ensure the final product met all specifications.
The decision was made to pinpoint critical towers with higher loading, such as the heavy angle or dead-end structures, for caisson construction and develop a simpler, smaller driven pipe pile design for tangent and angle structures. Since tangent and angle towers made up a substantial portion of the required work, the simplified design allowed consistent and low impact daily completion of foundations to keep the project moving at an aggressive pace.
To facilitate this pace, Northstar Sharp’s used an impressive fleet of owned equipment, including eight Junttan units for the driven piles, six excavator-mounted units for the helical piles and five Soilmec and two Watson drilling rigs for the drilled shafts. In addition, two pull-test frames for PDA testing and two Marl AR80 tracked units were used for the program’s geotechnical investigation.
Construction problems and creative solutions
Some of the unique project challenges included river crossings along the path of the powerline. There were three river crossings that needed to be considered: the Athabasca River, Pembina River and North Saskatchewan River. For these crossings, drilled shaft piles with diameters of 3.65 m by 17 m deep were chosen as the preferred foundation type. There were also other existing powerlines to contend with and often the power could only be interrupted for a short duration – in some cases, not at all.
For the large diameter concrete pours, high temperature was a concern in the summer months for the concrete curing process. Therefore, the crew’s start time and end time were changed to be earlier in the morning when temperatures were cooler. Concrete truck routes were also timed to be precise with test drives being performed to discover the most effective and quickest route. This allowed Northstar Sharp’s to maximize all possible options for concrete delivery including using the Klondike ferry to cross the Athabasca River while performing a continuous 170 m3 pour.
Another ongoing test for the team was the various ROW surface conditions experienced along the full route of the project. From wetlands, fine sand and steep terrain, to the river, various pipeline and powerline crossings, structure access by crews and equipment were a continual challenge.
The various foundation designs were optimized through the standardization of material. Regardless of the design selected for an individual site, wherever possible all material and sizes were made to be identical. This streamlined the procurement and execution phases by making it very simple for field crews to load, haul and install nearly identical foundations day in and day out. All the pre-planning and time spent during the design and construction consultation phases ensured that everything fit, was simple to transport and install, and could be replicated quickly from day to day. Through optimizing, the team was able to ensure foundation execution was as efficient as possible.
Design changes
Even with all the planning and geotechnical work, the design and execution phases were not without issues. During the geotechnical investigation of the ancestral Slave Lake Basin, it was determined that roughly 38 sequential structures did not meet any of the established design criteria.
During the initial investigation, it was determined that the muskeg in this area was roughly 20 to 30 metres deep before drilling would encounter a layer of dense clay. A CPT rig was mobilized to complete additional testing in the very weak top zones to refine the design criteria for the foundations. This data was analyzed, and supplementary designs were then issued to the project. The re-design required modifications to the top of the piles, additional piles and splicing, and gusseting of the pile cap to accommodate minimal support in the top 10 metres of the foundation. In addition, tangent structures were switched to a four-pile battered screw pile configuration with gussets and thicker welds on pile caps and tower shoes.
In some cases for the guyed anchors, battered helical piles had to be extended 42 metres before encountering suitable soils to anchor to. Northstar Sharp’s kept trucks and trailers loaded with material and welders on full 12-hour shifts in order to accommodate the changes in design and increased depths encountered during installation – all while working in temperatures as cold as -30°C.
Conversely, there were also instances whereby due to ground conditions, piles could not be driven to the required embedment depths. For these situations, Northstar Sharp’s worked with engineering to provide PDA results to verify the design and further optimise the design as required. Driving shoes were incorporated in some cases and this helped to achieve the required embedment. In other cases, pile testing of driven piles was also completed to verify load effectives on the piles. All this was implemented while still maintaining the required project schedule.
Critical execution
Northstar Sharp’s utilized multiple work fronts with teams of piling units, overseen by senior managers stationed at each area to support the daily operations. Work crews and rotations were set up in an assembly line fashion with survey in the lead followed by the piling crews, welding and splicing crews, cutting and capping crews and finally engineering and QA/QC.
This accelerated schedule also required the ramping of field and office quality personnel – ensuring that daily field installation data was verified, reviewed, passed on to the signing engineer and signed off. This worked in an almost seamless fashion stretched over hundreds of kilometres.
Of specific importance is that in one single winter season starting in January and ending March 26, Northstar Sharp’s installed more than 700 individual foundations, totalling almost 60 per cent of the line foundations, and completed two seasons of winter work in a single season. This effectively allowed the remainder of the project to further accelerate, pushing the schedule almost a full four months ahead from the planned completion date. This was primarily accomplished through consistent and direct communication from all companies and subcontractors and a drive to see the project completed well ahead of schedule.
Conclusion
Through design optimization and constructability reviews, Northstar Sharp’s completed the successful installation of almost 12,000 piles for 1,300 tower foundations over 500 km and two substations in a year and a half.
“The dedicated effort from Northstar Sharp’s, coupled with an innovative design and work process, has been a key component to the WFMAC project’s overall success. The quantity of foundations installed within an 18-month period has been remarkable and is a testament to the commitment of the Northstar Sharp’s team,” said Brett Smit, P. Eng., project director (WFMAC), Valard Construction.
The project has been recognized as one of its greatest successes by the Quanta Group of companies and stands as a testament to what design, procurement and construction can do when integrated under a single roof working towards a common goal.