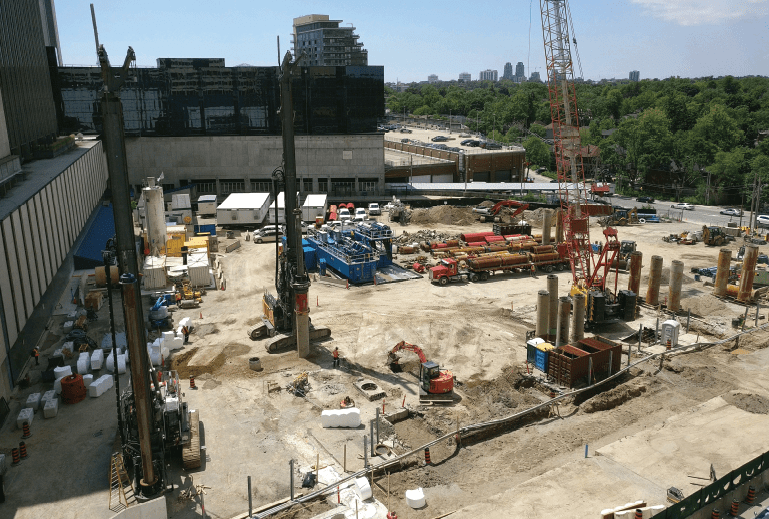
The $5.3-billion Eglinton Crosstown light rail transit (LRT) line is the largest transit expansion project in Toronto’s history; running 19 kilometres east to west with a 10-kilometre underground stretch. The transit line will have up to 25 stations and stops and will link passengers to 54 bus routes, greatly improving Toronto’s public transportation system.
The Eglinton Crosstown LRT is the largest project financed by Infrastructure Ontario’s Alternative Financing and Procurement model. Infrastructure Ontario and Metrolinx, formerly known as the Greater Toronto Transportation Authority, awarded the contract in the summer of 2015 to Crosslinx Transit Solutions (CTS), a design and construction consortium comprised of infrastructure heavyweights including ASC-Dragados, Aecon, EllisDon and SNC-Lavalin. In addition to designing and constructing the project, the consortium will maintain the line for 30 years.
Currently under construction, the Eglinton Crosstown LRT project is slated to be complete in 2021. Keller Foundations Ltd., formerly Geo-Foundations, was awarded Eglinton Station and began work on the project in April 2017. Although Keller has worked on other LRT projects across Canada, the Eglinton Crosstown is the largest and most logistically challenging project to date.
Keller rises to challenges with adaptability
The scope of Keller’s work involves providing excavation support adjacent to and underneath a live subway line. The surface works include a 30-metre-deep secant pile wall, soldier piles and lagging, 40-metre-deep structural caissons and jet grouting where utilities intersect the secant pile wall. The team must also install a traffic deck to maintain vehicle flow throughout the project duration. Most of the design work was provided to Keller by SOE Yonge Ltd., a member of the Isherwood Group of Companies.
“The Yonge line will remain in operation throughout the entire project duration,” said Sean Morrisroe, project manager, Keller Foundations. “In addition, by installing a traffic deck, we will be able to keep two lanes of traffic in operation to mitigate the impact to the public.”
Once the surface work is complete, four lanes of traffic will open back up to the public while construction of the station box advances below. The worksite is 300 metres long and 18 metres wide. The flurry of activity around the worksite demands painstaking staging and sequencing. “It is probably one of Toronto’s busiest intersections in terms of pedestrian and traffic flow, so that brings its own challenges with respect to how we plan and execute our work in a safe and efficient manner,” said Morrisroe.
Keller brings innovative techniques to the project
Keller’s 30-metre-deep secant pile wall composed of 8 MPa concrete provides excavation support to facilitate the construction of the station. The secant pile wall will also function as a water cut-off wall which will significantly reduce the need for dewatering across the entire site.
Deviation control monitoring devices have been outfitted to each of the Liebherr LB 36 drill rigs used for constructing the secant pile wall. Developed by Jean Lutz, the deviation control monitoring device measures the verticality of the holes. The sensor measures the rotational trajectory of the auger throughout the depth of a cased hole to generate three-dimensional coordinates for analysis.
“After we measure the verticality, we use that information to develop a 3D model in order to ensure we have sufficient interlock along the full depth of the pile,” Morrisroe said. “If there’s a case where we haven’t achieved that interlock, we will install supplemental jet grout columns along the secant pile wall to bridge any gaps.”
Locations where existing subgrade utilities intersect with the secant pile wall, jet grout columns will be installed to eliminate the need for relocating the existing utilities and maintain water cut-off. “Jet grouting is considered the most versatile ground modification technique in the world, yet it is still fairly new in Canada,” said Morrisroe. “It’s been used in the U.S. and Europe for many decades, but since it can be effective across a wide range of soil types, including silts and clays, more and more owners and consultants in Canada are beginning to recognize its versatility in solving a wide range of geotechnical challenges.”
The team will use the double-fluid jet grouting process whereby high-velocity, high-pressure cementitious grout erodes and mixes the soil to create a high-strength, low-permeability soil-cement matrix. A pre-production test program was performed on sacrificial elements to verify design strength, geometric properties and permeability of the soil-cement matrix. Keller uses a proprietary data acquisition system during installation as a key element of the quality control program to monitor and control the jet grout construction parameters. The jet grout columns extend from the founding elevation to approximately one metre above the existing water table. Above this, timber lagging is installed from existing grade during excavation.
To provide structural support for underpinning the existing subway station, six 1,500-mm-diameter structural caissons will be installed 40 metres deep. A welded wide flange beam and rebar cage will be installed to reinforce the caisson, allowing connection of the underpinning beams to the caisson foundations. CTS will self-perform the entire underpinning operation.
Once all of the vertical drilling scope on the south side is complete, the team will install a traffic deck consisting of steel deck beams welded to the piles within the south side secant wall and founding on a temporary strip footing installed on the north side. Lateral bracing welded to each adjacent deck beam will facilitate load transfer while in operation. An engineered timber mat will be secured on top of the deck beams to complete the deck. Traffic will then be diverted to the south side while the surface work begins on the north side.
Finally, when the north side is complete, the north deck beam will be bolted to the south deck beam installed earlier, allowing four lanes of traffic to open back up to the public while excavation advances below. With excavation performed by CTS, Keller will install soil anchors, walers and struts to provide lateral support of the excavation.
After reaching the underside of the TTC subway tunnel, the team will continue excavation and lateral support work towards the west and east ends of the station while CTS completes the underpinning of the existing subway station. A panel excavation sequence will then be carried out to allow for the installation of a shotcrete wall with soil nails to provide excavation support directly below the existing subway station.
Shotcrete installation will advance for successive excavation lifts until there is sufficient headroom available for a low headroom jet grout drill rig. Vertical and inclined jet grout columns will be installed to provide a continuous water cut-off wall, connecting the secant walls on both the east and west sides of the existing subway which were previously installed during the surface work. “The jet grout is being installed to ensure adequate water cut-off and the shotcrete is to provide lateral support of the soil,” said Morrisroe. The team will be using one of Keller’s propriety drill rigs, the KB0, as the low-headroom jet grout drilling rig.
Although the project is complex and logistically challenging, Keller has maintained an exemplary safety record. The client has given Keller the highest safety audit score out of all contractors on the Crosstown line project, including two scores of 98 per cent. The team received a letter of recognition and a prize from CTS, praising Keller’s “outstanding job” and thanking everyone for their commitment to the company’s Life Saving Rules initiative.
The safety scores show that when it comes to complicated, high-profile projects, Keller has the expertise, flexibility and breadth of techniques to get the job done safely.