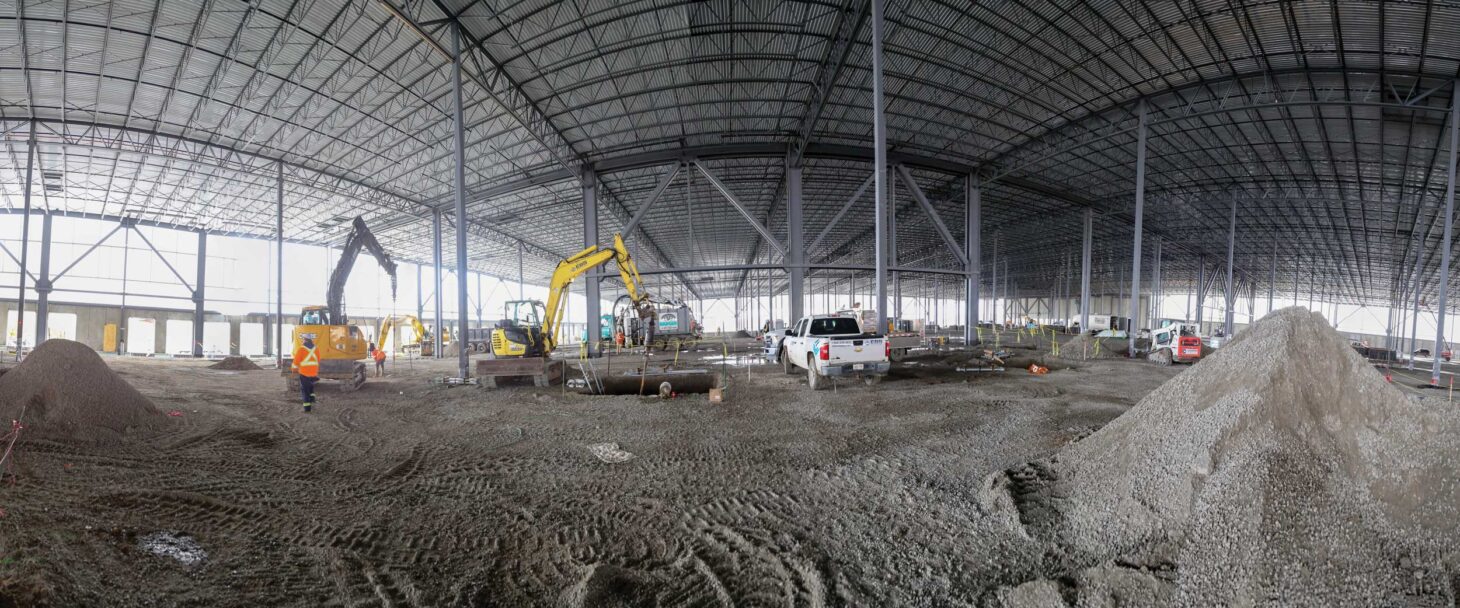
Photos: EBS Geostructural, Inc.
In the 1830s, a blind Belfast engineer named Alexander Mitchell had a vision that would transform foundation construction. His invention, the helical screw pile, has supported countless structures since he patented the design 188 years ago.
Initially, Mitchell devised cast or wrought iron screw piles with a wooden shaft to permit the construction of lighthouses, beacons and marine moorings where traditional foundation construction was not feasible. The idea behind the screw pile was simple: rather than hammering piles into soft soil, they were screwed in with the help of helices that sliced into the sandy earth with minimal disruption, allowing the pile to be installed in dense soil.
Eventually, the technology was adopted for land-based applications such as fence posts, tower legs, decks and additions to residential structures. Screw or helical piles have changed with the times; today, they are typically made from high strength steel and feature round hollow shafts or solid square shafts. Often, they incorporate multiple steel screw threads – or helical bearing plates – that allow the pile to be screwed into the soil. Sometimes, helical piles are installed with cement grout surrounding the shaft to increase vertical and lateral load capabilities.
The energy required to install a helical pile or anchor is typically called installation torque. The torque is measured in foot-pounds or Netwon-metres at a regular installation interval to confirm capacities in both compression and tension applications. Monitoring and recording the installation torque is the main portion of the quality assurance/quality control process required to ensure capacity of the helical piles or anchors. The greater the resistance (torque) during installation, the denser the soil that is being penetrated and the higher the load carrying capabilities of the pile.
A particular area of concentration is improving the grouting techniques around square shaft helical piles.
“Helical piles are an end-bearing deep foundation system that has applications in compression, tension and lateral load situations,” said Dino Vito, president of EBS Geostructural, Inc., in Breslau, Ont. “By applying torque to the shaft, this action installs the helical pile with minimal displacement or disturbance.”
This is beneficial because no vibrations or spoils are created during installation. Loads are transferred down the shaft to the helical bearing plates and the minimally-disturbed soil beneath or above each plate.
Vito, who joined EBS in 1995, says the Kitchener-area company started using helical piles in the early 1990s. Initially, they were used to support residential structures that had settled.
“Then we started using them more for new construction, supporting residential units three storeys and less,” he said. “Here at EBS, we’ve completed over 450 load tests on helical piles for compression and tension. As we built the database on our website (accessible to anyone) of the capacities and what we can achieve with helical piles, we were able to prove to the industry that they can be used for higher loads.”
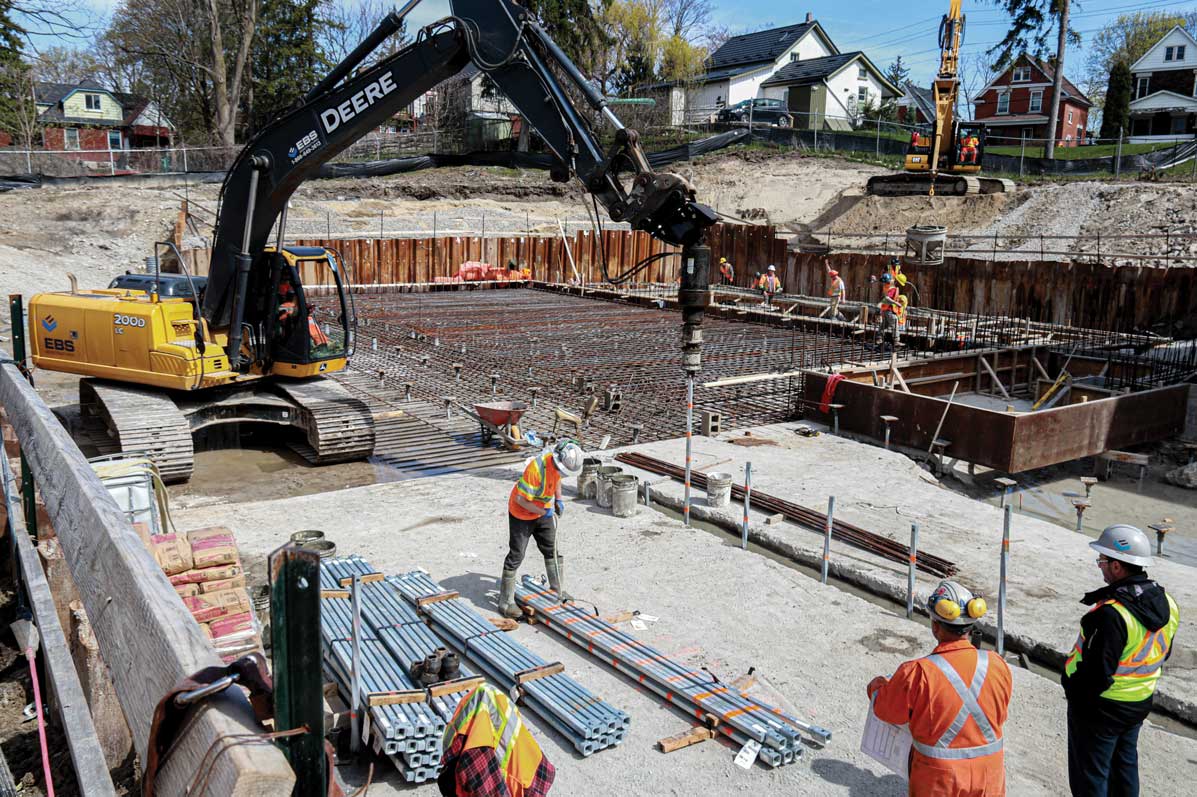
EBS Geostructural is a design-build deep foundation construction company specializing in helical piles, micropiles and geotechnical grouting for industrial, commercial and institutional applications. Vito says that EBS typically uses grouted square shaft helical piles and often designs for an Ultimate Limit State capacity of 1,000 kilonetwons (225 Kips) or greater per helical pile.
“You’re not stripping the soil; you’re slicing through it. You still have the bearing capacity of the denser soil underneath, as it is minimally disturbed. A high water table does not affect these piles during installation. Helical piles are a versatile tool in the deep foundation industry,” said Vito.
In 2019, EBS was involved in building one of the tallest structures on helical piles: One Richmond Row in London, Ont., a 32-storey residential tower. With a high water table, deep loose sand deposits and limited access for construction equipment, helical piles were selected over driven piles because of the potential vibration issues to surrounding structures, not to mention the noise disruption in the city’s downtown core.
EBS performed extensive compression and tension load tests at the London site to determine the load capacities and to value engineer the foundation with the owner of the tower.
“We have been brought into more projects because helical piles can be cost effective for developers in certain situations,” said Vito. “Helical piles are good when it comes to projects where there is some difficulty, where access is limited or the water table is high. We’ve worked in parking garages, etc. It depends on the site and the application. [In London,] they saved the owner money over traditional deep piling foundations.”
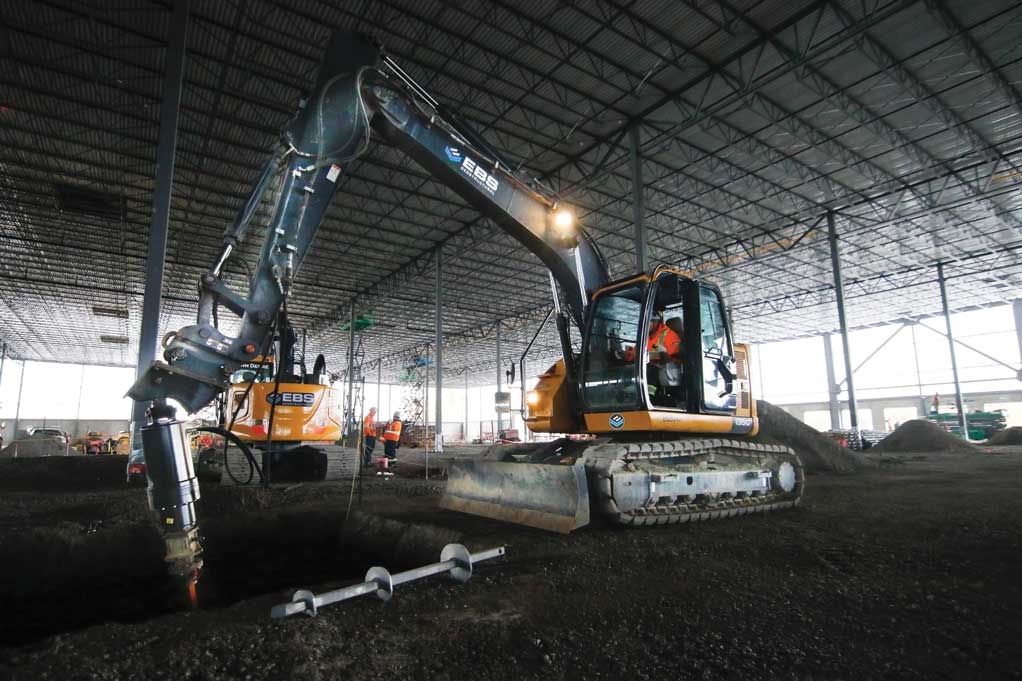
To date, EBS has installed more than 60,000 helical piles, mostly in Ontario. Vito is a fan of their flexibility and benefits.
“Helical piles are modular. They can be shipped to remote locations or down the street, and installed in almost any type of weather. You can keep adding extensions to reach dense load bearing soils; we have installed helical piles to depths of 55 metres. You can use all sorts of equipment to install helical piles, from portable equipment like skid steers and mini-excavators to large excavators – you can tailor the equipment to what’s required,” he said.
More has happened with helical piles over the last five years than in the previous 20, says Vito. It all comes down to increasing the helical pile load capacity while remaining cost effective. A particular area of concentration is improving the grouting techniques around square shaft helical piles. About 10 years ago, EBS worked with the University of Western Ontario to research how helical piles respond to seismic events. Those studies have been used to further today’s screw pile applications.
However, Vito notes that helical piles are not the answer to every foundation.
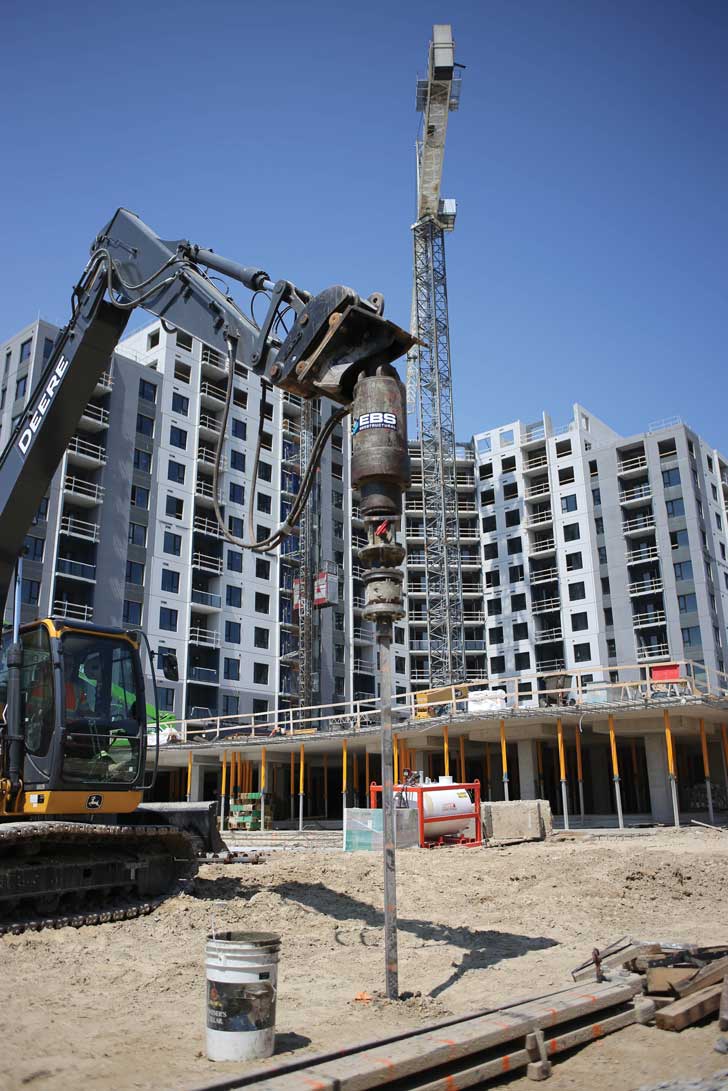
“Helical piles aren’t the cure-all for everything. We like the square shaft helical piles because they can penetrate denser soil and be installed through cobble; we’ve proven it on projects. But if there is large, buried concrete rubble or slabs, or large boulders, helicals are not the deep foundation system to use. We try hard to help our clients identify the right solution, even if it’s not ours.”
He credits the team at EBS for pushing the envelope when it comes to alternative deep foundation solutions.
“We have fantastic, hardworking and innovative people in the field and in the office. I’m very proud and humbled by this group.”
As helical pile technology continues to develop, new methods and applications will be discovered to realize even better performance from this deep foundation system. The screw pile isn’t confined to lightly loaded applications such as wharves or residential support anymore. In fact, there’s clearly an exciting future in store for Mitchell’s revolutionary design, even as it closes in on its 200th birthday.