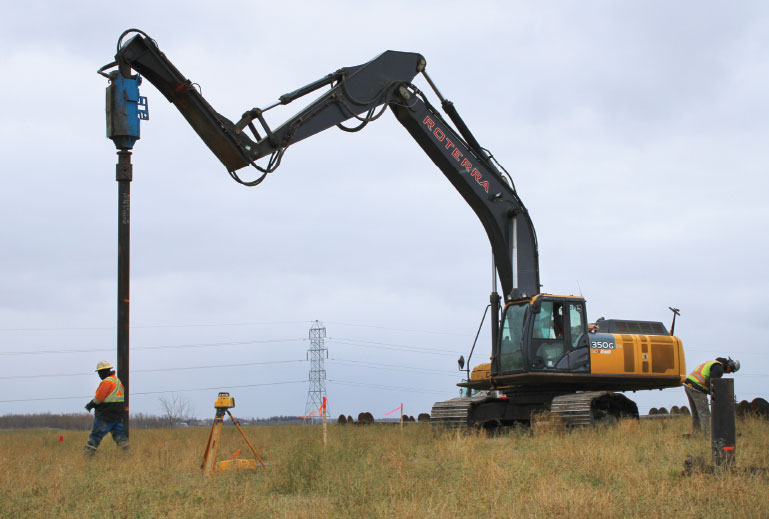
The Manitoba-Minnesota Transmission Project strengthens Manitoba’s electricity supply and improves access to U.S. markets, while supporting export sales to keep rates lower for Manitobans. Roterra Piling Ltd. is doing its part to make it happen.
After being given the green light by the federal government last year, Manitoba Hydro is now constructing the Manitoba-Minnesota Transmission Project (MMTP), a 500-kilovolt AC transmission line that runs 213 kilometres from northeast of Winnipeg to the U.S. border in southeastern Manitoba, where it connects with Minnesota’s soon-to-be completed Great Northern Transmission Line.
This $453-million project also includes upgrades to the Dorsey, Riel and Glenboro converter stations.
For the northern Section 1 portion of this project, Manitoba Hydro sought a contractor that could easily partner with its in-house engineering team to complete the helix weld engineering and pile cap analysis and engineering, while providing a turnkey solution from survey and manufacture, to installation and pile cap welding. Roterra Piling Ltd. was selected for the task by Voltage Power (purchased in early February by Aecon) and arrived on site last September.
Roterra is a solutions-focused contractor with high safety and quality standards backed by industry-leading engineering. This Alberta-based company has been involved with helical screw pile technology through its parent company – Genax Metal Manufacturing Ltd. – since 1992 and has been active in the transmission and distribution space over the last 15 years. Its engineering team brings decades of piling solution design experience and utilizes sophisticated numerical modelling to analyze any installation anomalies and refine the cap plate design.
“We are able to self-perform the engineer, manufacture, supply and install of helical screw piles of large scale and high volume,” said Garrett Axani, vice president at Roterra. “Roterra supports the execution of projects with sound project management and are capable of adding geotechnical investigations and survey in our scope to complement the pile design, pile install and pile cap install.”
Roterra was initially brought on the project as an alternate to the base foundation design with a scope of 50 lattice tower structures. Based on the performance, time savings and financial considerations of what Roterra’s team was able to bring to these first 50 structures, the company’s scope of work was expanded for MMTP and they were able to take on a total of 116 structures.
“We are all extremely proud to have been considered as one of the solution providers for this project and we are pleased with what our team was able to contribute,” said Axani. “I would personally like to commend the work of our employees on this project who bring more than 300 person-years of experience from the helical pile industry. The fact that our scope increased significantly after our initial mobilization is a testament to the value proposition of our team, our services and our product.”
For the installation of the structures in Roterra’s scope, the company used two helical pile install units built off of excavator base machines. A John Deere 350 unit is able to install piles up to 33 feet in length, which is a fairly standard top-out capacity for a helical piling unit. However, Roterra’s Volvo EC460 unit is equipped with an in-house engineered and manufactured custom arm to allow for the installation of piles up to 48 feet in length. In addition to the custom-built excavator arms, Roterra is also one of the early pioneers of mounting large-capacity drive heads on excavators.
“For us this means that instead of installing a pile lead section and extension afterwards, we are able to install the piles in a single section, which is significantly faster and more effective from an install perspective,” said Benjamin Luu, field operations manager at Roterra.
The 2,120 Manitoba Hydro-designed, job-specific piles – combined with Roterra engineers’ welding design that was used in this project – were fabricated by the company and then shipped direct to the job site. The helical screw piles range from 30 to 40 feet in length and have up to three helixes, one-inch thick and 36 inches in diameter. Roterra was proud to showcase the quality of its manufacturing from its ISO 9001:2015 certified, quality management program and facility at Acheson, Alta.
“There are not a lot of companies that can perform the internal engineering, manufacture and install of large diameter, large-capacity helical piles at scale,” said Axani. “Roterra is excited to have started offering our services throughout North America with the opening of our Houston, Texas, location in 2019. We are now focused on expanding our service offerings geographically, and are excited for what the future holds.”
The right-of-way required for the transmission line depended largely on the design of the tower structures, which are either guyed or self-supported. The towers are spaced an average of 400 to 500 metres apart and range in height from 40 to 60 metres.
The self-supporting steel lattice towers, for which Roterra is installing the foundations, have a smaller overall footprint compared to guyed towers supported by cables. The right-of-way width for the self-supporting towers is 80 metres; an added benefit to reduce the impact on farming operations as the towers are being erected in cultivated and agricultural areas.
One of the more unique aspects of this project has been related to the uneven topography along the berm of the Red River Floodway, where much of Roterra’s work has been focused. The grade of the steep hills in this area can be markedly different from one side of the tower foundation to the other. In places where the tower legs are located on the higher elevation side of the berm, Roterra often used a three-pile foundation group per leg. Then, for the legs that are on the lower side of the berm – which have a much higher stick-up of approximately two metres – engineers used five-pile groupings to account for the legs standing significantly higher and not having the supporting earth around them.
“These pile groups look really neat and are not something we see very often,” said Laili Abolghasemi, project coordinator at Roterra. “It’s been tremendously interesting to witness how the design was accomplished in order to accommodate the tower just for that specific project location.”
Manitoba experienced uncharacteristically wet weather throughout the fall of 2019, seeing more than three times its monthly precipitation average for September. For the first time in the floodway’s history, the Province of Manitoba opened the floodway during the fall to lower the threat of a fall flood to Winnipeg. This created a number of challenges for the project as the ground surrounding the floodway became over-saturated with rainwater.
“Our initial planning for this project was to be able to access everything with all of our equipment,” said Roterra project manager, Kendall Fahey. “But when it rains without any respite for a number of weeks, it means that a very large, very beautiful, man-made berm that is composed of clay becomes more than a little mucky to work on.”
Due to these wet conditions, for approximately three-and-a-half weeks Roterra was only able to access the right-of-way with tracked equipment and was unable to bring in its welding or crew trucks. The company ended up using additional skid steers to move gear into the project site and its project client, Voltage Power, was able to secure Nodwell tracked carriers to transport Roterra’s crew and welding equipment.
Then, as temperatures dropped in October, a heavy snowfall over the Thanksgiving weekend would prove devastating for power lines across the province, pulling Manitoba Hydro resources away from the job to restore electricity to a number of rural communities. Fortunately, Roterra’s piling crews were on off days during this blizzard; although that was small comfort since the hotel they were staying in lost power for approximately 12 hours.
“Luckily Roterra vehicles all have power outlets, so we could catch up on some administrative paperwork while we watched the snow fall from the inside of the trucks,” said Abolghasemi. “There were really just a couple days there where we didn’t feel it would be safe to have our crews driving but, by the following Sunday, we were back on site laying the piles, cutting and setting out caps.”
Given the challenges that Roterra faced with the notoriously inclement Manitoba weather last fall, the company’s helical screw pile technology proved to be a distinct advantage for use on MMTP as steel doesn’t care if the conditions are wet or dry.
“And unlike concrete, with helical screw piles, we aren’t required to bring in wheeled equipment to get the job done,” said Luu. “If needed, we could do all of our work on tracked equipment which – in incredibly muddy and rainy weather like we faced – is significantly more effective than other methodologies and allows us to keep going.”
In the places where Roterra was operating on the man-made berm, it was considered to be a no-risk zone, which meant that there was little-to-no risk as it related to any environmental impacts. However, as the company proceeded west or east down the line, environmental assessments conducted by Manitoba Hydro identified the presence of both low- and high-risk zones along the project’s path. Therefore, wherever Roterra crews were required to enter or exit higher-risk zones, all of their equipment needed to be maintained at a high level of cleanliness.
“This also pertained to anyone who might be walking in and out on foot; we needed to make sure that there weren’t any invasive seeds or foreign debris coming along with them,” said Abolghasemi. “For the highest-risk zones, we were required to have wash trucks on hand so that we wouldn’t be transporting anything hazardous from one location to another.”
The right-of-way for the self-supporting towers proved to be a safe area for the foundation work being done by Roterra. A safe working platform – such as rig matting – was used in select locations to allow rig access up steep hills. The company also installed rig mat bridges across aqueducts to ensure that they were not excessively damaging the right-of-way or putting workers in any danger.
Maintaining a high level of workplace safety has always been a key value for Roterra, and the company works closely with its clients to ensure that everybody who comes on site is on-boarded safely. Safety orientations ensure that everyone is fully aware of the work that is going on around them, as well as the risks associated with that work.
“Safety is paramount at Roterra and is the thing that we prioritize over all else,” said Axani. “We are very proud of the work being done by our team and the care that they take to ensure that they are capable and comfortable in doing any of the tasks that they are required to do.”
The anticipated in-service for the MMTP is June 2020.