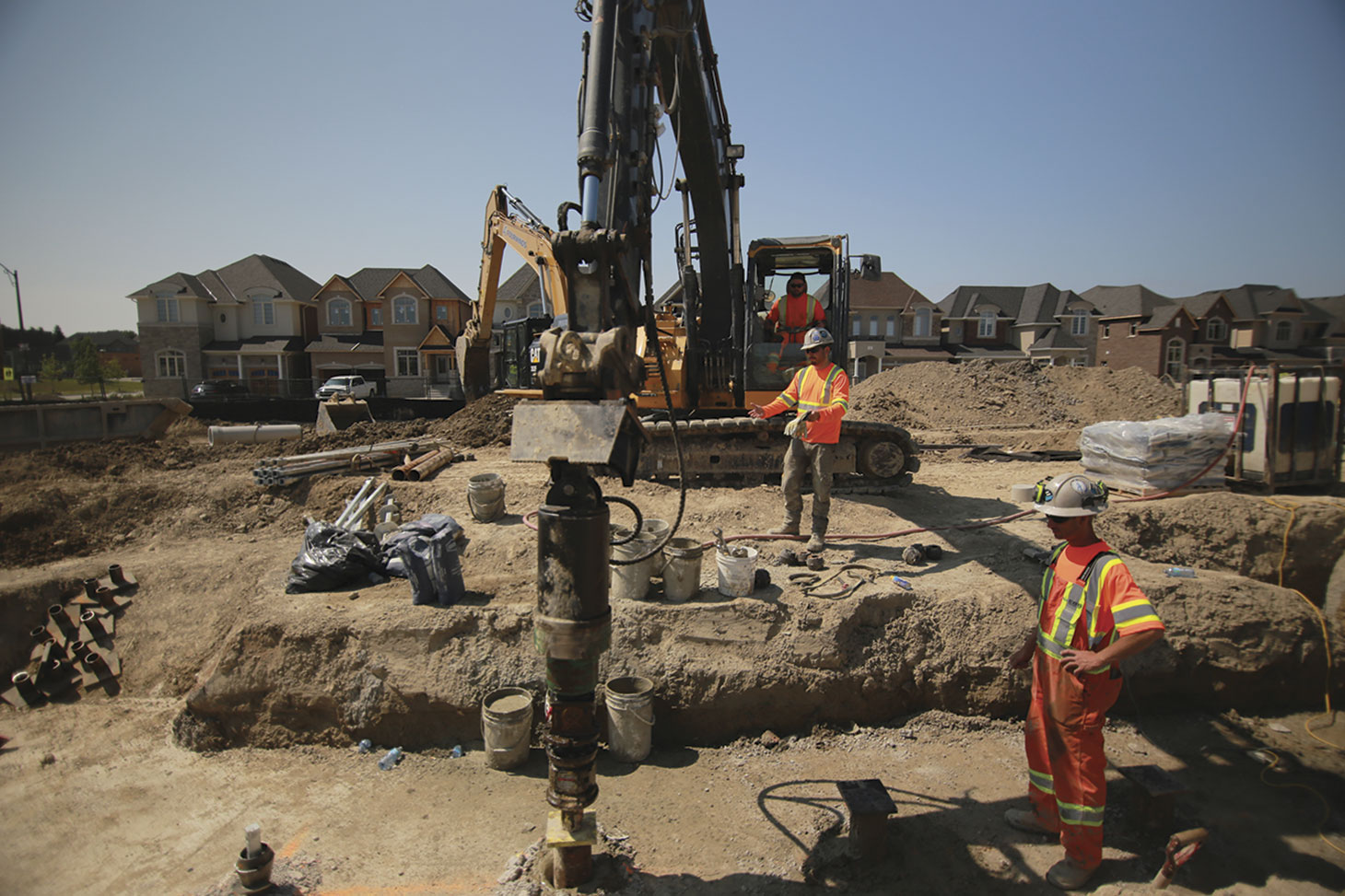
Developers and builders used to have a simple solution when they ran into poor soil conditions: move to a more suitable location.
But urban sprawl, its corresponding demand for public infrastructure and the soaring cost of real estate have all combined to change the conversation, according to Brian Huber, senior project manager at EBS Geostructural in Breslau, Ont.
“For years and years, development all over the province was stopped when they went from good soil bearing to poor soil bearing,” he said. “They would do their geotechnical investigation out of the gate to determine the soil conditions.”
He says that if testing showed eight lots were solid and two were unsuitable, the developers would leave 20 per cent of the site undeveloped. Not anymore. “Even with the additional costs of construction, it’s better to have something on that land than to have it sit vacant, because really, those are the two options,” said Huber.
Shaky ground in East Gwillimbury
The company was recently involved in the construction of Sharon Public School in East Gwillimbury, Ont., for the York Region District School Board. “They identified that as a need in that district and identified that site in their project planning stages – however many years ago – that it would be a great spot for a school,” said Huber.
The site is surrounded by fast-growing housing developments and is located right in the heart of the community it will serve. However, when Patriot Engineering conducted a geotechnical investigation of the site, problems arose. The subsurface conditions were unsuitable for conventional spread footings due to a high water table and soil N values hovering around 10.
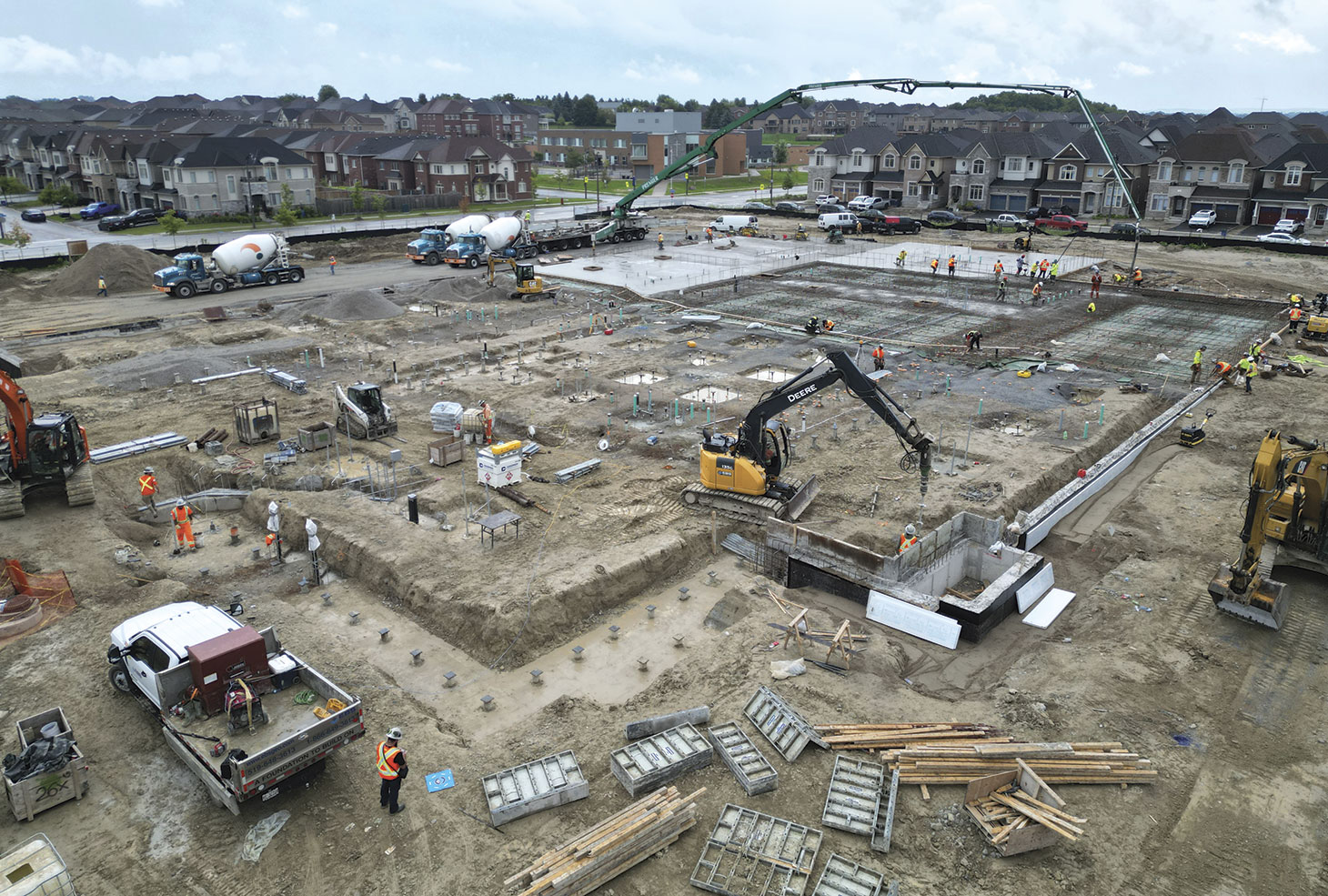
Huber says engineers digging boreholes determine the N value, or a “blow count.” They use a carefully calibrated split spoon and drop it, and the N value is how many times they must hit the soil sample to penetrate one foot. “If you hit it once, and it drops a foot, you’re in very soft soil,” he said. “If you have to hit it 50 times to get it to advance a foot, you’re in harder material.”
Moving the school to another site wasn’t an option, so Patriot Engineering recommended helical piles as a foundation method with compression load testing to confirm the design and on-site capacity of the helical piles.
Helical piles
“A helical pile is essentially a screw,” said Huber. “It consists of a lead section that has helical plates on; there’s a three-inch pitch, so as it’s rotated each revolution, the pile pulls into the ground three inches at a time,” said Huber.
It’s like taking an impact driver at home and putting a wood screw into a two-by-four, he says. “It’s going to go in relatively easily. Now, take that two-by-four and put it on top of a piece of hardwood – maple or oak – and as soon as it gets to that hardwood below, it will still go, but it’s much harder,” said Huber. “It takes a lot more torque to get it in.”
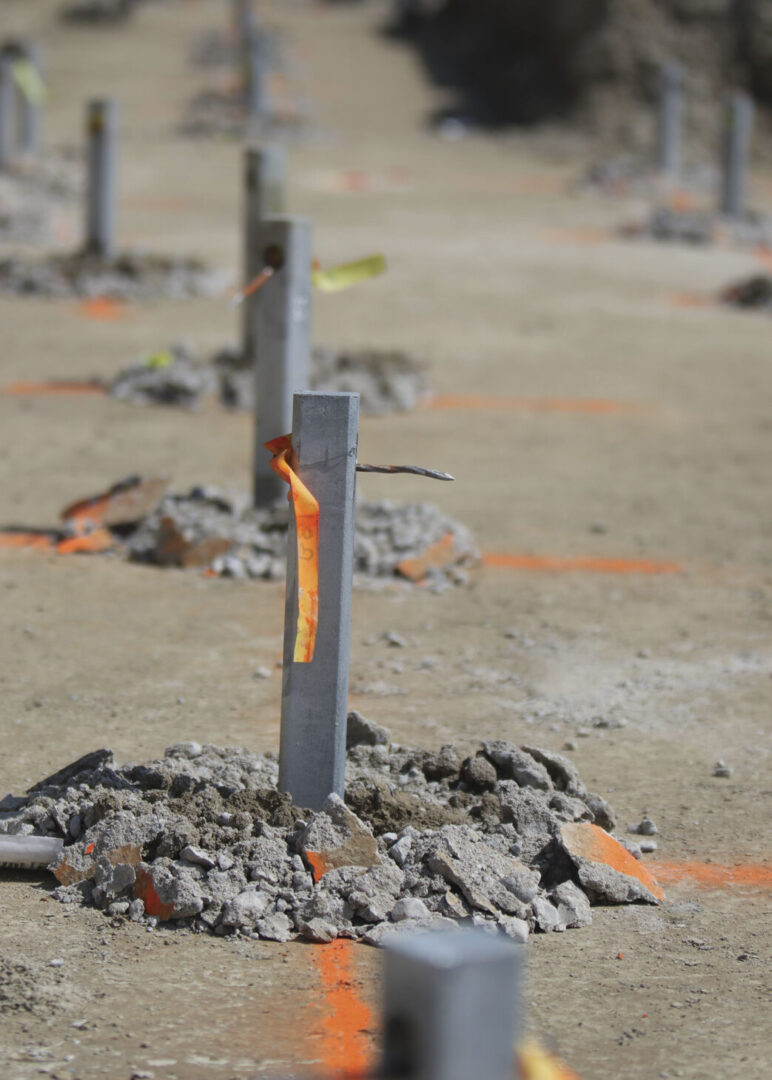
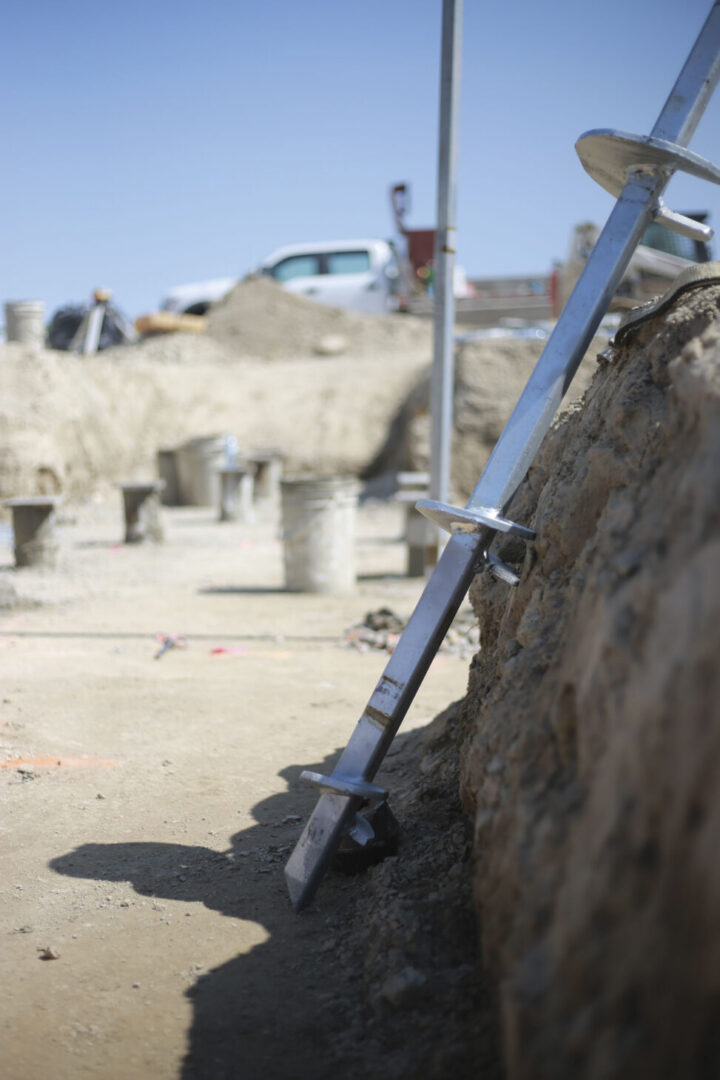
He says that’s what the helical pile is doing – slicing through the soft material at the top until it finds denser soil that can carry the structure’s load. “Then the loading is transferred down that pile shaft and through those helical plates into that competent material at whatever the bearing depth is – 20 feet, 50 feet, 100 feet,” he said.
Huber says helical piles have been a trusted solution for decades. Though not new, the technology is still gaining traction in modern construction as developments are forced to contend with less-than-ideal soil conditions.
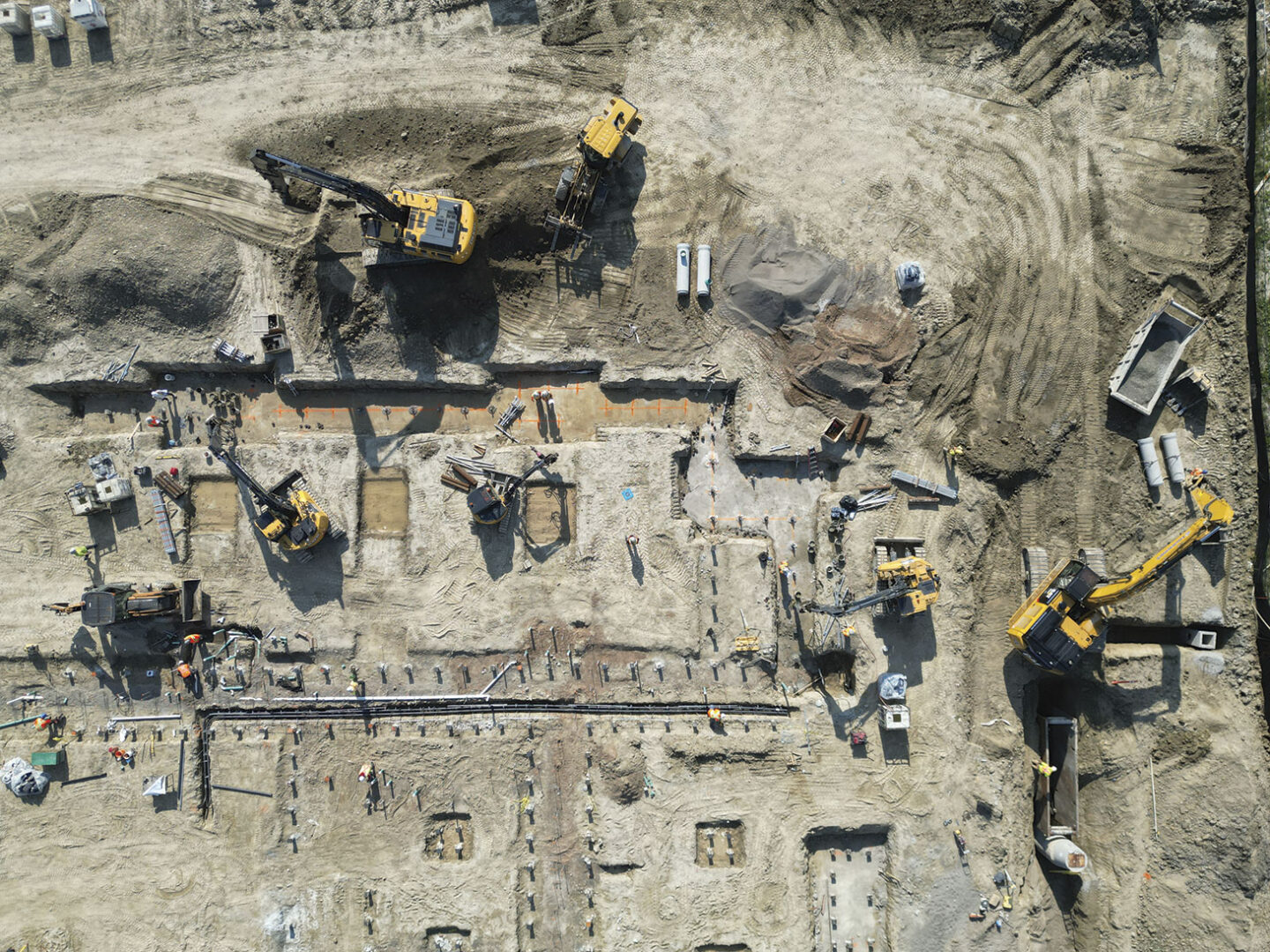
“You might as well optimize it and go big or go home, right?”
Brian Huber, EBS Geostructural
The project at Sharon Public School required 739 helical piles, varying in size depending on the specific loads they were meant to support. Three sizes were used on the job at the school: the SS5 (270 kilonewtons), SS175 (500 kilonewtons) and SS200 (670 kilonewtons). Engineering work is critical to ensuring the size of the piles is optimized based on the soil and load requirements. While there is no harm in using a pile with a bigger capacity than needed, says Huber, it can add significant unnecessary costs to a project.
“If an average helical pile costs, say, $3,000, that’s not a small number when you start doing the math on that quantity,” he said. “So, especially on the bigger projects, we’ve seen a lot of value in being involved from the beginning as part of the design process.”
Varying depths and scheduling conflicts
One of the complexities of the Sharon project was dealing with varying soil conditions across the site, leading to different depths for the piles. “We averaged about 75 feet per pile, but we had some as shallow as 56 feet and others that went as deep as 120 feet,” Huber said, adding that depth isn’t the critical factor – torque was. “It’s the torque that matters. You can’t expect the same performance out of the piles unless the correct torque is achieved.”
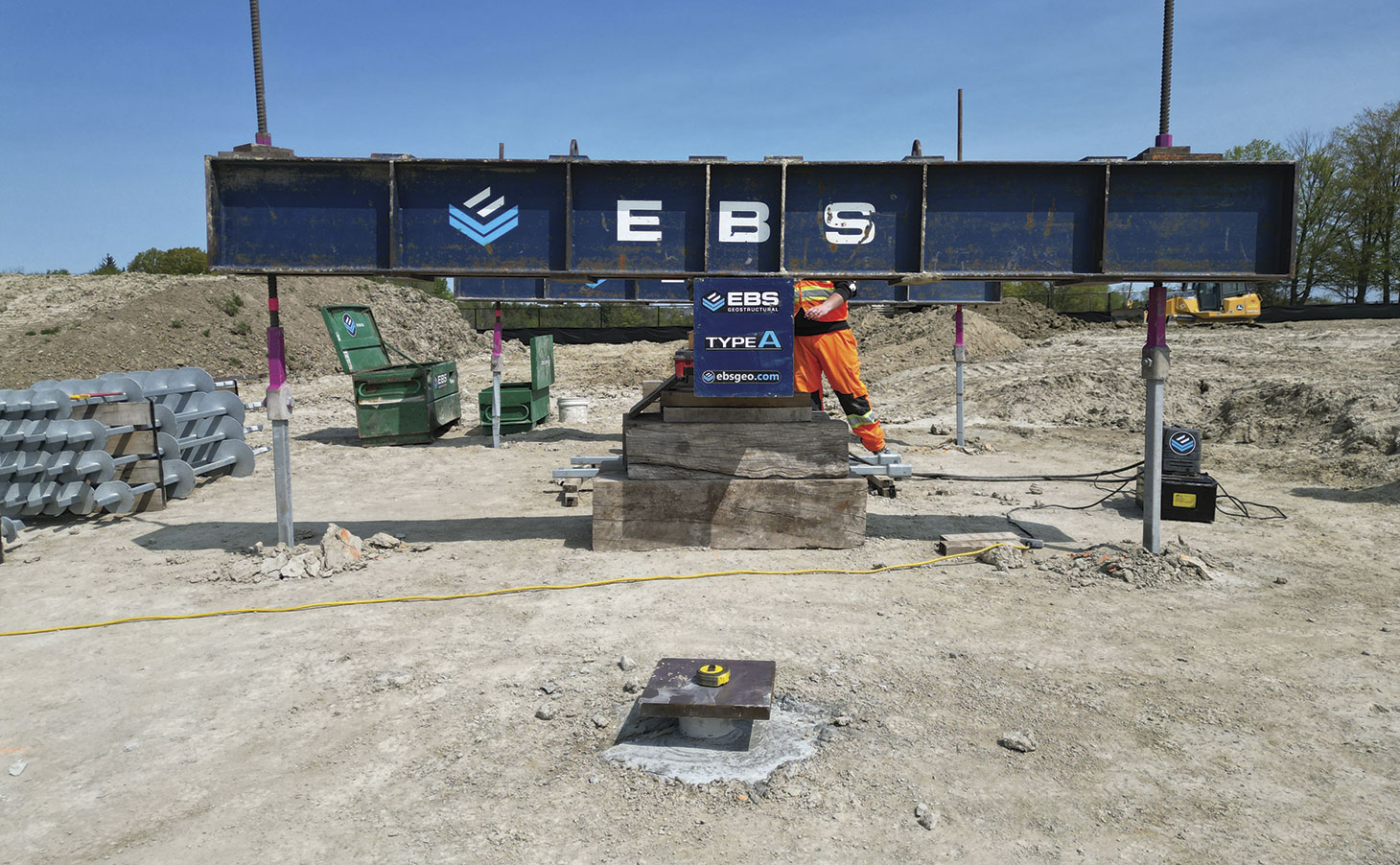
Another challenge was scheduling. Construction sites are often chaotic, with multiple trades working simultaneously and tight deadlines to meet. Huber credited EBS’s long-standing relationship with Chance, the manufacturer of the helical piles, with allowing it to meet the project’s aggressive timelines, despite a 50 per cent increase in material requirements than what was originally anticipated.
“They were able to manufacture the material and have it on-site before we ran out of the material that we originally ordered – which was fantastic,” he said, adding that a lot of trades would quickly run into supply chain or labour issues if their work was suddenly increased by half.
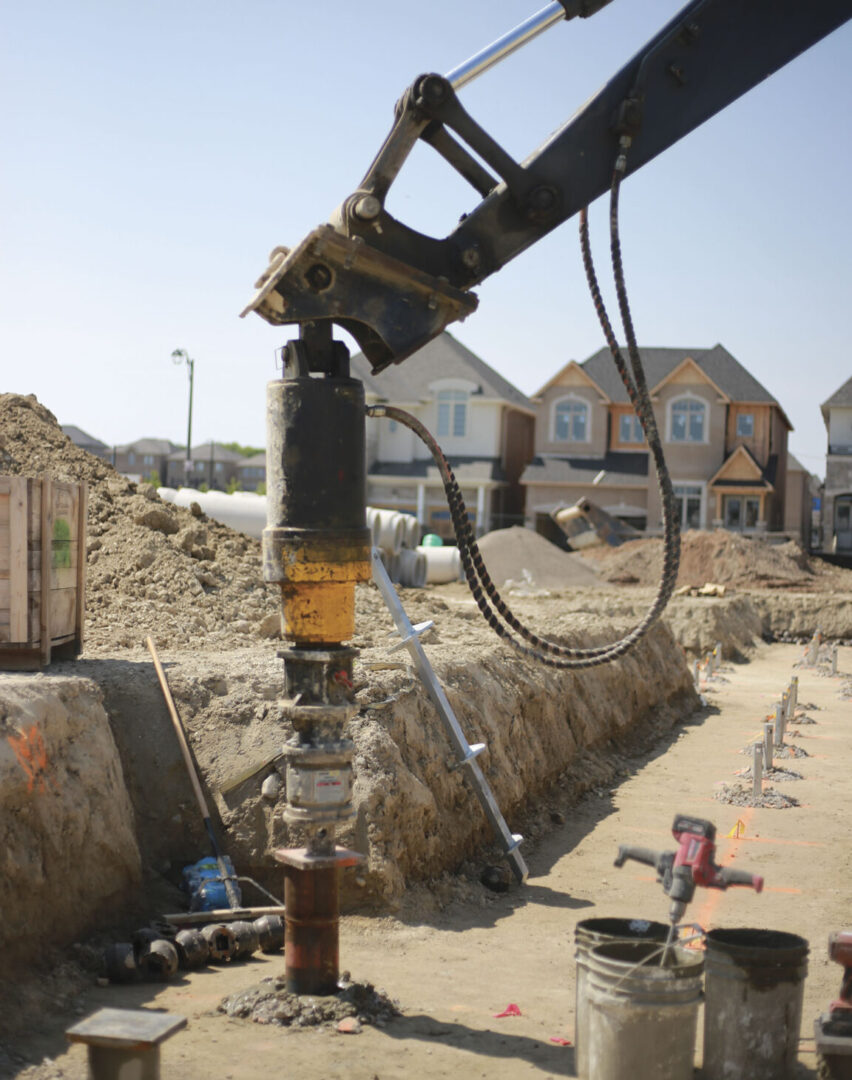
“Even with the additional costs of construction, it’s better to have something on that land than to have it sit vacant.”
Brian Huber, EBS Geostructural
To keep the project on track, EBS also deployed additional crews and equipment as needed. They have 12 crews across the province and a fleet of equipment. Huber says he is proud that they avoided the “domino effect” of delays in the construction schedule. “We were able to keep guys on site, add more guys when available and assist the general contractor (Aquicon) in maintaining their overall project schedule,” said Huber.
More use in the future
Huber expects to see more use of helical piles in future jobs, given the need to build more infrastructure and the lessening availability of land.
“For a number of years, development was stopped on these big sites where the soil conditions went from good to poor because it wasn’t cost-effective to build,” he said. “Regardless of whether you do a single story, two story or 10 story, you need a deep foundation. You might as well optimize it and go big or go home, right?”