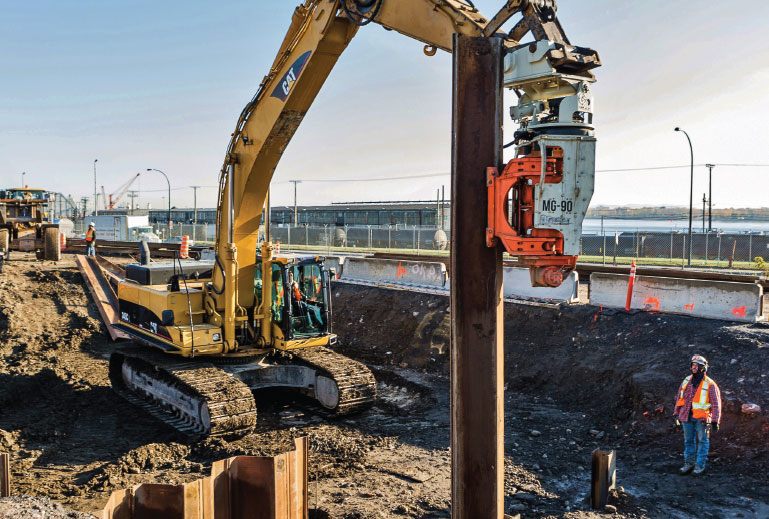
New equipment helps Alva Construction drastically cut time to complete project component
As part of a project to replace a deteriorated wharf at the Little Dover small-craft harbour in Guysborough County, N.S., Alva Construction was required to install 272 fender piles. This work was undertaken upon completion of construction of a new hybrid cribwork and timber pile fishing wharf with a cast-in-place concrete deck, as one of the final components
of the overall project. (Earlier work on this project is described in the article “Precision Positioning,” published in the Q2 2017 issue of Piling Canada.)
Alva Construction, based in Antigonish, N.S., was in “uncharted territory” with the fender piling work, says Reg Tramble, the company’s engineering manager.
“Most of our wharf projects don’t have fender piles,” he said. “This was the first fender pile application that we had worked on in over 20 years.”
For that reason, Tramble decided to explore options for the installation, looking for the best possible equipment and processes to efficiently complete the work. Through his research, Tramble talked to Gilbert Products in Roberval, Que., and learned of the Grizzly MultiGrip™, a side-grip vibratory pile driver. This tool comes in two sizes – the MG-60 and the MG-90 – and promised to deliver the power and speed Alva needed.
Choosing a vibratory hammer for the job
Tramble spoke with Alex Gravel, sales and marketing director for Gilbert Products. Tramble described his company’s needs related to the wharf project specifically and other projects generally. Gravel recommended the Grizzly MultiGrip excavator-mounted vibratory hammer for several reasons.
First, the tool can drive sheet piles, H-beams and timber or steel tubular piles with its standard configuration, making it versatile on a work site and for a variety of projects. This feature meant that Alva would be able to use the tool on multiple projects going forward, an important consideration in Tramble’s purchase decision.
Its side grip has a three-point arm system – for which Gilbert has a patent pending – designed to optimize energy transfer from the vibrator to the pile. This power optimization is intended to reduce the time needed for driving. The increase in efficiency this feature is designed to enable was another selling point for Alva. The side grip’s capacity to drive long piles and to position them easily – thanks to its rotating 360-degree system and tilting range of 40 degrees – was the major reason, says Tramble, for his choice to purchase it.
Quick-Change technology allows an operator to remove and replace the MultiGrip’s side jaws for a different application in less than five minutes. Gravel says this “innovation is a unique feature of the tool.” It not only provides for “quick changes” that keep a job moving; it also means that the company does not need several different types of attachments for different pile types.
The clinching factor for Tramble was that Gilbert Products is a Canadian manufacturer, and the only manufacturer in Canada, says Gravel, of this type of pile driving equipment.
Tramble ultimately chose the MG-90, the larger of the two MultiGrip tools, for installation of the fender piles and future company needs.
Putting the new equipment to work
The Little Dover wharf construction project began in January 2017. The fender pile installation, one of the final components of the project, was expected to take six weeks in November and December last year. Alva Construction worked on a second project during that period, just 500 metres away from the wharf, replacing a bridge. The Grizzly MG-90 was used on both projects.
On the wharf project, Alva found that its use of the MG-90 in installing the 35-foot, 300-mm-diameter timber fender piles led to the desired outcome: a shortened schedule.
“The time for this component of the work was dramatically reduced, by about 50 per cent,” said Tramble. Rather than the allotted six weeks, the fender pile installation took just three. While the somewhat loose material on the seabed made it “relatively easy to drive the piles,” said Tramble, that condition was accounted for in the project scheduling and was not the reason for the rapid installation. The MG-90 was useful, Tramble points out, in providing “control over the driving to prevent driving past the design elevations in the variable foundation material.”
The requirement for temporary falsework was eliminated, says Tramble, as the equipment served to hold the piles in place as they were driven.
Down the road at the bridge project, the presence of bedrock made the driving much more difficult. Pipe pile casings were driven for the foundation and sheet piling for the temporary shoring. The MG-90, removed for a time from the wharf project, efficiently handled the conditions and requirements.
Tramble anticipates using the MG-90 on numerous jobs in the future, but looks forward, as well, to renting out the tool when it’s not required by Alva. This likelihood has made the investment even more worthwhile.