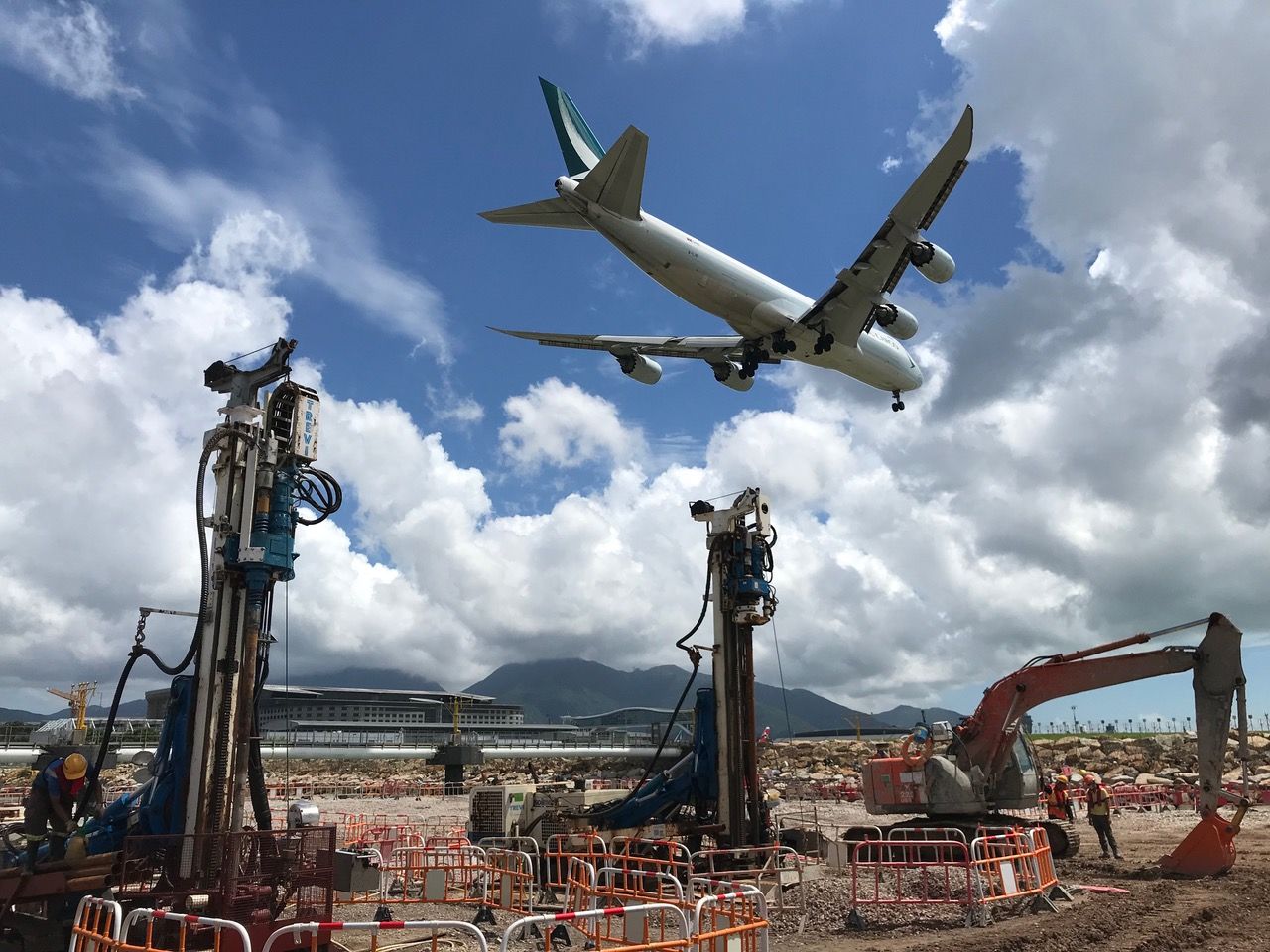
TREVI Construction Co., Ltd. (TCHK), a part of the TREVI Group that operates in Hong Kong and Far East Asia, is working on the Hong Kong International Airport (HKIA) Three Runway System Project.
- TCHK is doing deeper ground consolidations with jet grouting technology for the main reclamation works in some of the areas of the HKIA project. In this project, TCHK has been working with three different main contractors:
- ZHEC-CCCC-CDC Joint Venture (main reclamation works)
- Gammon (Automated People Mover [APM] and Baggage Handling System [BHS] Tunnels and related works)
- China State Construction Engineering (Hong Kong) Ltd. (North Runway Modification Works)
Main project description
To strengthen Hong Kong’s status as an international aviation hub and cater to the city’s long-term air traffic demand, the HKIA is developing into a three-runway system (3RS). The scale of the 3RS project is almost equal to building a new airport next to the existing one. It involves seven core projects:
- Reclaiming approximately 650 hectares of land north of the existing airport island using non-dredge methods, including deep cement mixing.
- Building the Third Runway Passenger Building and an associated apron.
- Building a new, 3,800-metre-long runway and its supporting taxiway systems. The existing North Runway will also be reconfigured.
- Expanding Terminal 2 to provide full-fledged passenger services, including arrivals and departures facilities.
- Building a new, 2,600-metre-long APM system that will connect Terminal 2 with the new passenger building. The new APM system will transport up to 10,800 passengers per hour.
- Building a new BHS linking Terminal 2 with the new passenger building. The new BHS will be capable of handling 9,600 bags per hour.
- Building other associated airport support infrastructure, road network and transportation facilities.



The scale of the Hong Kong International Airport 3RS project is almost equal to building a new airport next to the existing one
Major resources used
There was a peak production period when TCHK worked with 11 jet grouting teams in different areas/contracts. There were about 100 workers engaged in these projects at the same time. The equipment at the site was:
- 11 Soilmec microdrilling rigs SM14 and SM20
- 11 high-pressure pumps
- 11 backhoe excavators
- 11 Atlas air compressors
- 6 agitators
- 2 grout mixers
- 4 cement silos
- 2 Pemo pumps
- 1 40 ton crane lorry
Main reclamation works
ZHEC-CCCC-CDC Joint Venture is the contractor appointed to undertake the main reclamation works, reclaiming approximately 650 hectares of land north of the existing airport island, using non-dredge methods, including deep cement mixing (DCM).
One of the DCM technologies used in this project is jet grouting, which improves soil mechanical and permeability properties by using high-speed jets of water/cement mixtures injection treatment. Jet grouting can be advantageous in difficult logistic conditions and confined spaces, when there are obstacles to cross and in high-depth treatment with the crossing of voids.
The jet grouting technique improves a wide range of soil types. As it is based on soil erosion, soil erodibility is crucial to the result. The more consistent the soil to be treated, the smaller the column diameter. Therefore, larger columns can be used in loose soft soils and smaller ones in cohesive soils.
Depending on the number of fluids used, there are three main techniques:
- Monofluid (TREVIJET T1): a water/cement mixture is injected to break up and simultaneously mix the soil in situ. Diameters usually range from 0.4 to one metre.
- Bifluid (TREVIJET T1/S): a combination of water/cement mix and air is injected to break up and simultaneously mix the soil in situ. Diameters usually range from 0.8 to 2.5 metres.
- Triple fluid (TREVIJET T2): a combined water/air jet is used to break up and partially remove the soil in situ, whereas a lower water/cement injection ensures soil mixing.
TCHK has been awarded the major part of jet grouting works
Jet grouting has been underway in this project since October 2019 and is still in progress. So far, the TCHK team has consolidated and grouted about 311,000 cubic metres of soil in 6,900 columns of different diameters, from 1,200 millimetres (mm) to 2,500 mm (majority are 2,500 mm diameter columns), for a total length of 73,000 metres of soil grouted.