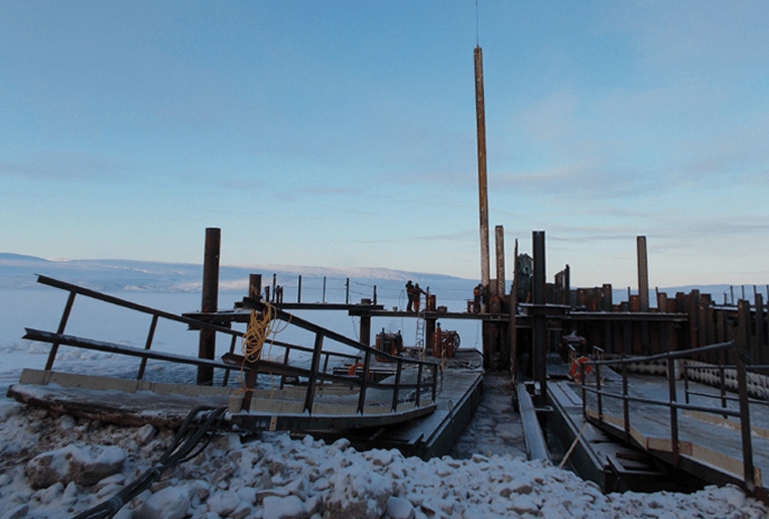
Ruskin Construction is currently completing work on an iron ore dock at Canada’s northernmost producing mine – the Mary River site on the northern end of Baffin Island – for Baffinland Iron Mines Corporation.
This is quite a feat since this remote location is 500 kilometres north of the Arctic Circle in Nunavut, and has an average winter temperature of -30 degrees Celsius with several months of 24-hour darkness. Awarded this $37-million contract in April 2014, Ruskin Construction, a privately held company with offices in British Columbia, Alberta and Alaska, offers specialized bridge, foundation, marine, aerial pipeline and heavy civil construction services to clients in the transportation, energy, mining and for-estry sectors.
As the design-build contractor for this mega project, Ruskin’s scope of responsibilities included the assembly and construction of Open Cell™ marine structures for the ore dock, mooring facilities, shiploader and material han-dling conveyor system foundations, and the installation at Milne Inlet capable of supporting ship-loading equipment sized to load ocean-going ore carriers ranging in size from Supramax to Post Panamax vessels.
Both the remote location – in the Qikiqtani Region of Nunavut – and ship-ping logistics played a major role in this project. With a short shipping season from August to October, and with Ruskin only signing on four months prior, project manager Dan Homeniuk knew they had their work cut out for them.
“Planning for a project in such a cold and remote location limited the access tremendously,” he said. “We needed to work very closely with all parties to ensure our equipment, materials and supplies would arrive to port on time. We also had to bring duplicates of all our equip-ment, parts and tools to mitigate any breakdowns.”
From a pile driving perspective, Ruskin’s role on the project was essen-tially three-fold:
- Install 118 pipe piles with diameters from 24 inches to 36 inches
- Install 118 pipe piles with diameters from 24 inches to 36 inches
- Design, supply and install founda-tions for the 800-metre-long reclaim conveyor, feed conveyor, drive house, electrical house, moorings and ship loaders
- Design and install the 140-metre Open Cell™ dock consisting of 14 cells with 923 sheet piles that were 85 feet longDesign and install the 140-metre Open Cell™ dock consisting of 14 cells with 923 sheet piles that were 85 feet long
Additionally, for onshore piles, the team hit permafrost within the first couple meters, but mitigated this by drilling and steaming the holes prior to pile installation, creating an ad freeze pile. “The procedure for the 24-inch pipes is as follows,” said Homeniuk.
“We would drill and case down to the permafrost with a 22-inch auger bit, and the bring in the eight-inch drill with an Air-Lift Reverse Circulation System on it and drill this down. next, steam probes were installed and the holes were steamed for 12 hours. We then removed the casing prove and started driving.”
Dan Homeniuk, Project Manager, Ruskin Construction
“We would drill and case down to the permafrost with a 22-inch auger bit, and then bring in the eight-inch drill with an Air-Lift Reverse Circulation System on it and drill this down. Next, steam probes were installed and the holes were steamed for 12 hours. We then removed the casing probe and started driving. The procedure for the 36-inch holes was similar except we would carry on past the casing with the 22-inch auger down to the design depth. This process took time to plan and prepare, but made the installation very seamless.”
Not to be outdone, installation of the sheet pile wall also posed great challenges such as inconsistent soft soil, the open sea and the long flat sheets. “To get our men and templates out for initial construction of each cell, we utilized Flexifloat sectional barges so we could be safe and get precise loca-tions for each template,” he said. “Once the construction process started going, the Flexifloats became a critical tool for construction. With the possibility of winds reaching up to 50 miles an hour, we worked closely with design engi-neers, PND Engineers Canada, Inc., to design extra batter pile cap supports that could be added to our template structures in case of any high winds in the forecast.”
Of the numerous site challenges, Homeniuk says that one challenge par-ticularly stands out. “Our biggest challenge on site was reaching capacity with the 36-inch diameter ship loader piles,” said Homeniuk. “Because these piles were located out on the dock, there was no permafrost. We drove past design depth and still received very low blow counts and PDA readings.”
The team, in conjunction with PND Engineers, designed and installed four-inch vented pile plug plates. They filled the piles with six-inch minus aggregate prior to the installation of the steel plug plates to induce the plug sooner. “This method worked fantastic,” said Homeniuk. “Logistics also played a critical role in this fix as this work occurred in November and supplies could only be flown in.”
The team worked 24 hours a day accompanied by sharp winds and frigid temperatures that often dipped below -30 degrees Celsius (-70 degrees Celsius with the wind chill (-22F and -94F, respectively)), with near 24-hour darkness for several months. Temperatures that average between -35 degrees to -40 degrees Celsius in the winter months take extra time and preparation in the project planning stage,” said Homeniuk. From November to January, when the team experienced 24-hour darkness, “we had to have many lights, heaters and equip-ment running all the time to keep the crews able to work. Warm-up shacks were set up around all the work sta-tions so no employees were far from a heat source.”
He also adds that in order to keep the equipment warm and running continuously, Ruskin utilized many customized sea cans for hoarding to keep it from freezing. “The equipment needed many alter-ations to keep it going in such extreme temperatures, so Arctic packages were installed in all our equipment, from power packs to cranes. We also had designated fuelers and mechanics to keep everything working 24-hours a day.”
In the end, with all of the challenges the team encountered – including delayed shipping and inconsistences in the geotechnical (reliance) data – the substantial completion date was moved from December 2014 to early February. Impressive, by any measure.