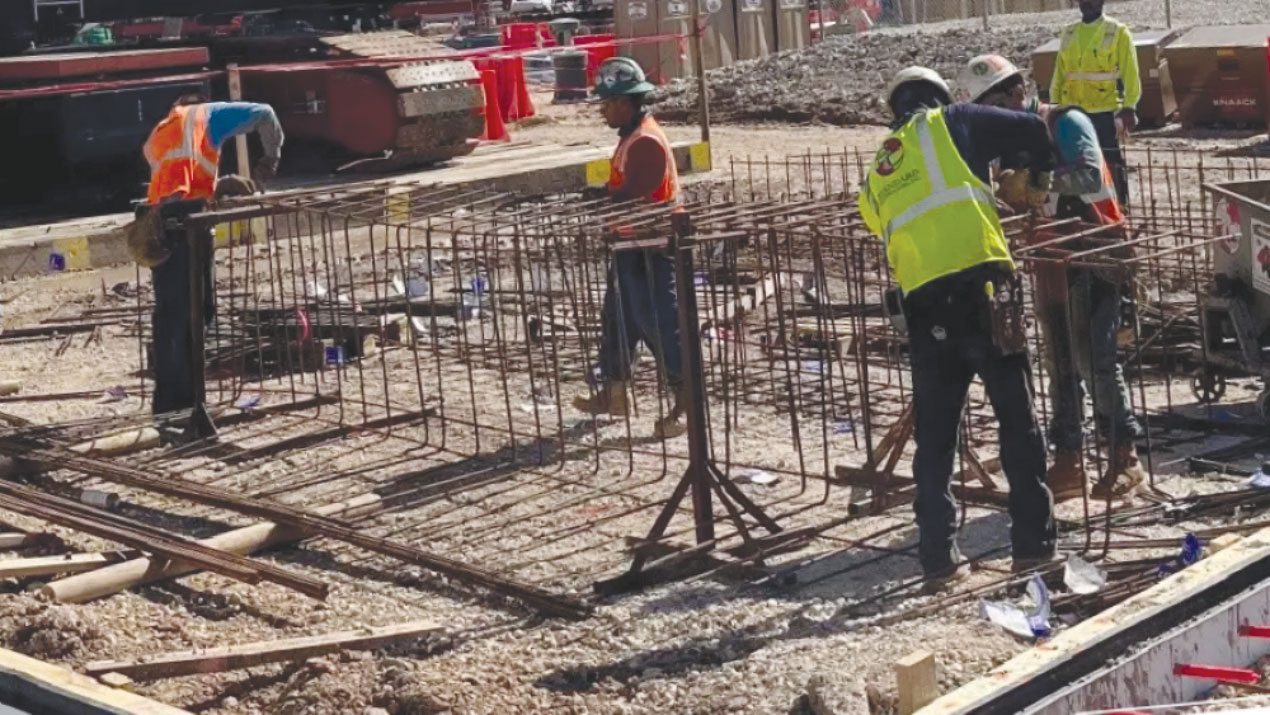
Due to pouring concrete in stages, the formation of construction joints is inevitable when building large concrete structures. These joints form potential weak spots where water might infiltrate the structure.
Waterstops – which are extruded plastic, formed metal or hydrophilic rubber internal seals – prevent water from seeping through moving and non-moving concrete joints and damaging structural integrity.
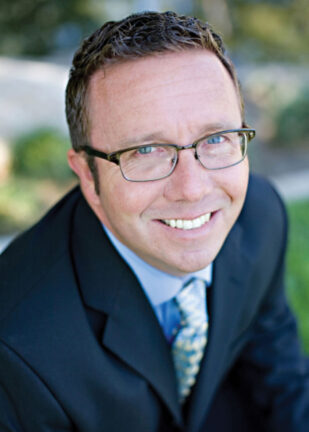
“A waterstop’s primary function is to prevent water leakage and ingress or egress in concrete joints and other areas where concrete structures are susceptible to water penetration,” explains David R. Poole, president and owner of JP Specialties, which manufactures Earth Shield® waterstops for chemical, industrial and environmental applications.
The company also manufactures a line of waterstop installation tools and accessories to thermo-weld plastic waterstops.
Important considerations
When selecting waterstops for a project, important considerations include chemical resistance, application temperature, head pressure resistance, size and the ability to move. There are a variety of options that include thermoplastic vulcanizate (TPV), polyvinyl chloride (PVC), stainless steel (SS) and modified chloroprene rubber (MCR) waterstops – each with a unique functionality. For example:
- TPV waterstops can dramatically expand the scope of conventional waterstops by resisting a broad range of aggressive chemicals, solvents and hot petroleum oils.
- PVC waterstops are manufactured from prime virgin resin and are generally used in water and wastewater projects.
- SS waterstops can stop strong corrosive fluids, even at elevated temperatures. Various metals, grades and gauges can be used depending on the project.
- MCR waterstops are a modern hydrophilic chloroprene rubber waterstop exceptionally durable with water sealing capabilities. When exposed to water, it more than doubles in size and can create an effective seal with joints of limited to no movement.
“Generally, most waterstops are supplied in 50 linear foot coils,” said Poole. “Some waterstops – retrofit and EB Cap profiles – are only 10 linear feet straight due to their non-symmetrical geometry.”
A Keycup® is a multi-function reusable concrete that securely holds a waterstop in place while simultaneously creating a keyed construction joint. It is an accessory that ensures the waterstop is securely embedded in the concrete, enhancing its ability to prevent water passage through the construction joints. Typical applications include slab-on-grade, wall joints, lumber replacement and labour savers.
“The Keycup attaches to the form board and holds the waterstop in a perfect centerline within the keyed joint when the forms are stripped. Waterstops are the most effective when they have an equal centerline seal. Keys are used to limit the concrete movement at the concrete joint,” Poole said.
Project challenges
There can also be challenges associated with installing waterstops. To overcome some of these challenges, Poole suggests the following:
- Position the waterstop in the joint.
- Centre the waterstop on the joint, with approximately one-half of the waterstop width to be embedded in concrete on each side of the joint.
- Allow clearance between the waterstop and reinforcement steel of at least one-and-a-half times the largest aggregate size. Properly vibrating the concrete prevents rock pockets and air voids caused by aggregate bridging.
- Ensure the centre bulb is not embedded at expansion joints.
- Secure the waterstop in correct position using optional factory-installed brass eyelets.
- Carefully place concrete without displacing waterstop from the proper position.
“Thoroughly and systematically vibrate the concrete in the vicinity of the joint and to maximized intimate contact between concrete and waterstop,” Poole said. “After the first pour, clean the unembedded waterstop to ensure full contact of a second concrete pour. Remove laitance, spillage, form oil and dirt.”
Best practices
To ensure best practices for the long-term effectiveness of waterstops in construction projects, Poole says it is vital to choose the correct polymer or metallic waterstop for your project and install it properly. “Install the Earth Shield® waterstop in all concrete joints. The waterstop should be centred in and run the extent of the joint. All changes of direction should be prefabricated, leaving only butt-welding for the field.”
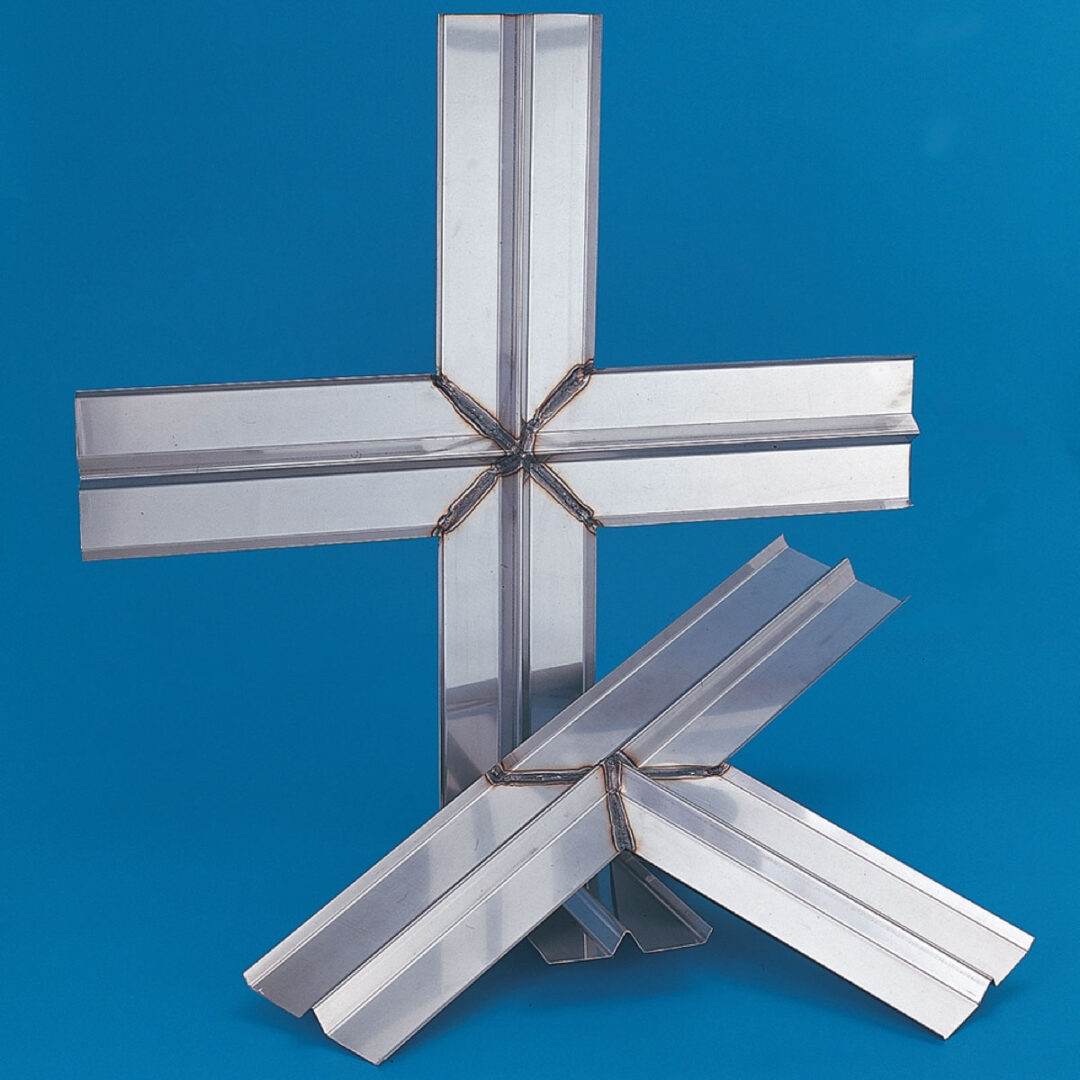
If installing in an expansion joint, he says the centre bulb must be kept unembedded to accommodate movement as designed. “Use optional factory-installed brass eyelets (or #3 hog rings) and tie wire to secure the waterstop to reinforcing steel to avoid displacement during the concrete pour. Splice straight lengths of the waterstop and shop-made fittings to straight lengths with an ST-10® in-line waterstop splicer with the iron temperature set to 350°F to 380°F for PVC waterstop, and 410°F to 430°F for TPV.”
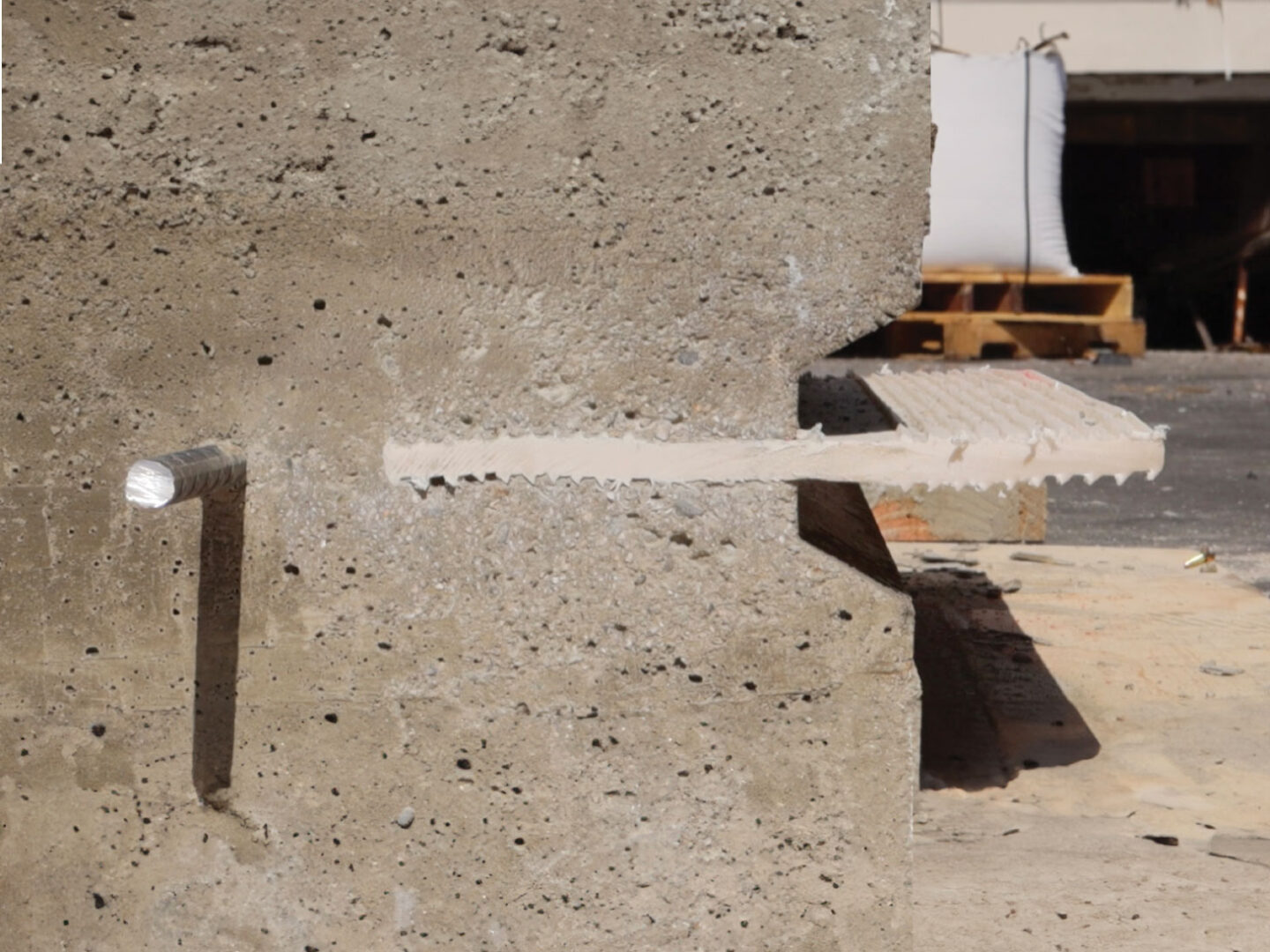

When asked about innovations or future trends that in waterstops and construction joint sealing, Poole says that waterstops don’t evolve very often and that changes over time are minimal.
“However, the Keycup is the first innovative accessory in a long time. The Keycup won the Most Innovative Product (award) at the 2024 World of Concrete, which was held in Las Vegas. We are incredibly happy about this,” he said.