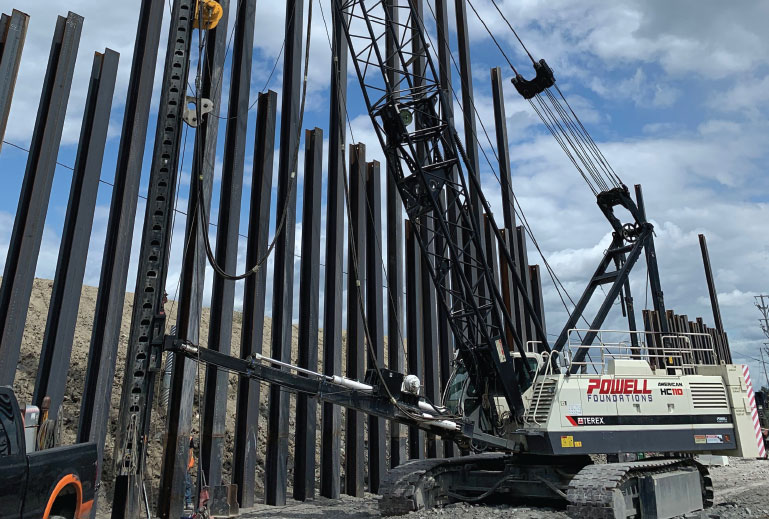
Powell Foundations’ work on the Highway 427 expansion in Ontario
In May 2018, the province of Ontario broke ground on the expansion of Highway 427 through York Region as a way to help improve traffic flow, create jobs and support economic growth in one of Canada’s most populous regions. This $616 million investment includes a new 6.6-kilometre extension from Highway 7 up to Major Mackenzie Drive, with eight lanes from Highway 7 to Rutherford Road and six lanes from Rutherford Road to Major Mackenzie Drive. In addition, there are three new interchanges at Langstaff Road, Rutherford Road and Major Mackenzie Drive.
There is also a four-kilometre road widening component to the mega-project that extends from Finch Avenue in the north end of Toronto all the way to Highway 7; from six to eight lanes between Finch Avenue to south of Steeles Avenue and from four to eight lanes south of Steeles Avenue to Highway 7.
Once complete in 2021, High Occupancy Toll (HOT) lanes with electronic tolling will be installed on Highway 427 in both directions, from south of Highway 409 to north of Rutherford Road. No existing general-purpose lanes will be removed to accommodate these HOT lanes.
The scope
LINK427 was selected to undertake this Public-Private-Partnership Design-Build-Finance-Maintain project by the Ontario Ministry of Transportation and Infrastructure Ontario. The LINK427 team includes developers ACS Infrastructure Canada Inc. and Brennan Infrastructures Inc., with construction being carried out by Dragados Canada Inc., Brennan Infrastructures Inc. and Bot Infrastructure Ltd. The project design was handled by WSP, headquartered in Montreal, Que.
Roughly 1,000 jobs will be created throughout the course of this massive project, with the majority of work being completed by companies with main offices within the Greater Toronto Area. One of those companies is Aurora-based, Powell Foundations.
Powell was established in 2017, and has quickly carved out a reputation for offering its clients total expertise in the design and installation of shoring, foundation and noisewall systems.
“Our service is what sets us apart,” said Carmine Gizzo, senior project manager at Powell Foundations. “We are a one-stop-shop that can handle every aspect of a shoring and foundation project. And we take great pride in the way that we work with our partners in helping them figure out the most cost-effective and advantageous ways of doing things.”
For the Highway 427 expansion, Powell installed 804 piles and completed 18 structures, which included two cofferdams and six roadway protections, as well as shoring and scour protection for the structures. The company began work on the project in September 2018, and is looking to complete the job ahead of schedule.
“The thing that we are most proud of in regard to this project was in being able to do all of those structures with only a few machines and a small – but skilled – workforce, and never once falling behind or delaying the general contractor in the building of their structures,” said Gizzo.
Powell used a Terex HC 110 crane equipped with a Berminghammer B32 hammer to drive the piles and, for several of the structures, the company also made use of an RTG RM 20 pile driver. Powell also had a Kobelco 80-Ton crane on hand that installed the protection systems in the culverts at the cofferdams, as well as the scour protection. The roadway protections were completed with the help of a Bayshore Hitachi 470.
The project primarily used 12-inch by 74-foot-pound (310-millimetre by 110-kilogram per metre) H-piles and, on certain bridges where the design called for it, Powell utilized 14-inch by 117-foot-pound (360-millimetre by 174-kilogram per metre) H-piles. When installing the shoring protection, the company used ZZ sheet piles, relying mainly on Samuel Roll Form and steel from North America for the H-piles and sheet piles.
For any project of this scope and scale there are bound to be a number of obstacles to overcome, yet none were seen as being insurmountable for Powell Foundations.
As they were working within the Hydro Corridor, one of the more significant challenges the company faced was determining how to lower the leads on the machine and excavate at Major Mackenzie and West Robinson Creek to drive the bridge foundation. To accomplish this, Powell built a frame that enabled operators to keep the piles in location while being driven.
“This was one of the more complex parts to the project,” said Gizzo. “We pre-drilled the hole and were able to pound the pre-drilled hole with a frame built up to ensure that everything stayed in line as we drove [the pile] into position. This was certainly one of the biggest challenges that we had to solve.”
Another challenge was related to the work done at West Robinson Creek after the Highway 427 northbound lane and the southbound lane at Robinson Creek bridge, and retaining wall were poured. Prior to the girders being placed, Powell was required to install scour protection – mostly blind – to protect against the washout of the pier from the creek that it was situated next to; all within a tight three-day schedule.
“So we ended up double shifting [our] crews working at night and basically had three guys communicating between themselves – a guy on the ground, a guy standing up top and the crane operator – in order to get this job done successfully and on time,” said Gizzo.
The obstacles
For the deep foundation portion of the project, the company was required to complete multiple shoring systems as per the structural footing for the bridge abutment, which the company had designed by Safe Roads Engineering Inc. to ensure that the footing was not obstructed. Certain shoring systems featured a structure with a brace coming off the existing footing that allowed the contractor to excavate, pour the footing and then remove the structure, after which they were able to continue erecting their work.
The work done by Powell was also impacted because they were installing structures along an existing roadway in a heavily populated area. Fortunately, the majority of the project was off the main railway tracks and traffic rarely posed an issue, aside from crossings that were more sensitive sites, such as at Langstaff Road & Rainbow Creek Precast Culvert and at Major Mackenzie Drive over West Robinson Creek.
“Whenever a freight train would pass, we would have to stop, stand down and sit so to not impede the tracks and to give the train the right of way,” said Gizzo. “We had to demonstrate that we could listen while we worked and were able to stop immediately as soon as the trains needed us to. Over time, we were granted some leniency and were able to get to the point where we would only have to stop for a matter of few minutes, which sped up the process considerably.”
Protecting species
In 2016, LINK427 confirmed the presence of threatened Barn Swallow nesting in two barns in the path of the project. In addition, field investigations also uncovered the presence of four endangered bat species in the area. As the habitat of these species at risk (SAR) could be impacted by the work being done, a number of mitigation efforts were undertaken. During the bird breeding season, an avian specialist was brought on to help identify active nests (which were not disturbed) and LINK427 was committed to habitat restoration for the SAR, which included the creation of forging space and the installation of new alternate nesting structures, or kiosks, for Barn Swallow. For the SAR bats, a 30-metre buffer zone around nesting trees and a strict, two-month ‘no vegetation removal’ period for woodlands identified as being SAR bat habitat were implemented measures.
The safety
On any project, Powell’s No. 1 goal is to ensure that everyone returns home safe each and every night after work. As such, the company goes well beyond the industry standard to ensure their people use safety best-practices on the job site at all times. Powell accomplishes this through daily job site hazard analysis, regular safety meetings and posting signage that identifies specific hazards, such as requiring double hearing protection when close to machinery.
“Safety is the top priority at Powell; as it should be for all companies,” said Gizzo. “Before we start any work for the day we have a safety meeting and [discussion] about what to watch out for and talk about how we want to work through the day. And each time we change an operation, we get our guys to stand down and conduct a new hazard analysis before we even commence additional operations.”
The 427 expansion allowed Powell Foundations to showcase its dedication to safety, innovation and hard work that it puts into each of its deep foundation projects, and the company is honoured to be recognized by Piling Canada as part of its 3rd Annual Great Canadian Projects issue.
“We wanted to be part of this issue because of the great pride we feel in successfully completing this very complex project faster [than] the original timeline called for,” said Gizzo. “To be recognized by Piling Canada for what we achieved is good for the company and shows how good we are at what we do; as well as how much we have grown since 2017. We are just getting better and better all the time at Powell Foundations.”
Photos courtesy of Powell Foundations