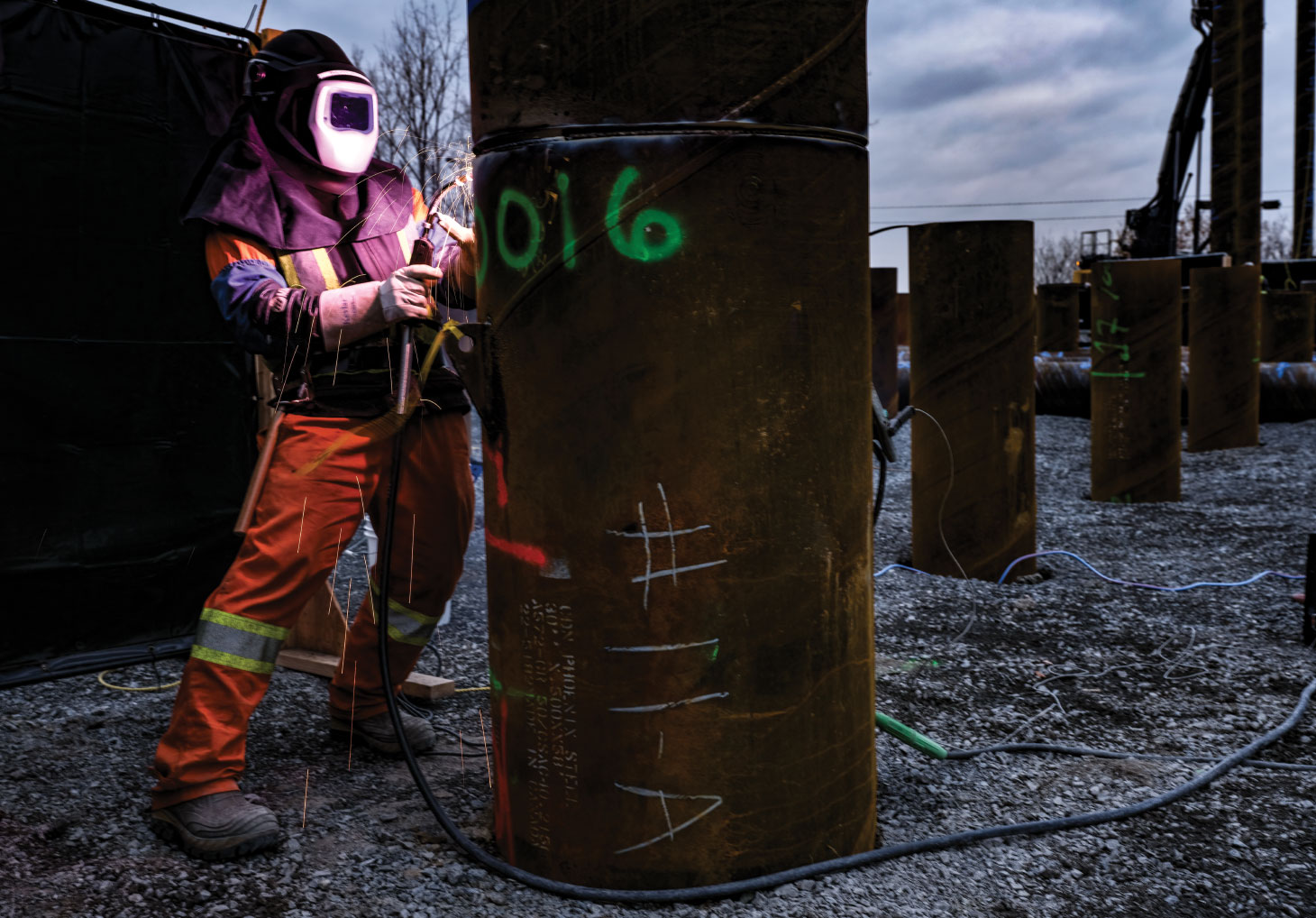
When it opens in 2026, Quebec’s first biomethanol plant will produce biofuel from non-recyclable waste, residual biomass and green hydrogen.
Recyclage Carbone Varennes (RCV) is perched on the south side of the St. Lawrence River, northeast of Montreal, on land that was once home to a petrochemical plant. It represents a $1.3 billion investment in the province’s transition to greener energy; over time, it aims to become Quebec’s leading producer of green methanol through a unique process developed by technology provider Enerkem.
The facility will also be home to the biggest electrolyzer in North America, using Accelera technology. Project funding is being contributed by Shell, Suncor, Proman, Investissement Quebec and the governments of Quebec and Canada.
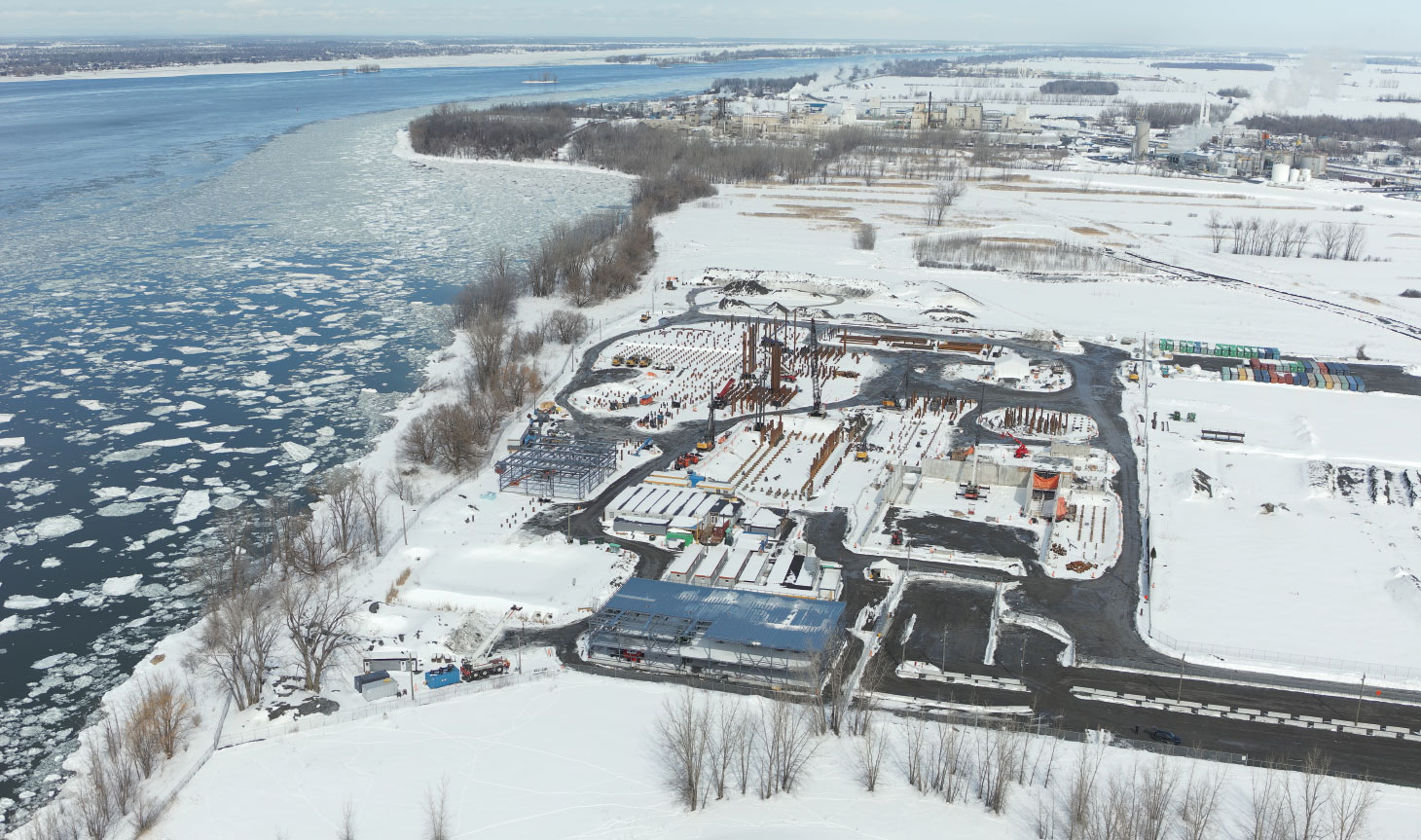
Biofuel is critical to reducing the carbon footprint of industries where electrification is difficult or simply not possible. As a fuel for ships, biomethanol generated in Quebec will help reduce greenhouse gases (GHGs) worldwide. According to the RCV website, this reduction is equivalent to taking nearly 30,000 vehicles off the road every year. RCV is expected to upcycle 200,000 tonnes of waste and residual biomass per year, creating 125 million litres of biofuels.
The plant’s future is bright, in part because it is built upon a solid foundation – in a literal and technological sense.
Dig, drive, splice
In August 2022, Black & McDonald, general contractor for the RCV plant, selected another Canadian firm, Pomerleau, as the deep foundation subcontractor for the project.
Accordingly, Pomerleau was responsible for foundation planning, selecting and sourcing material, driving piles to bedrock, pile splicing, excavation, pile trimming and top plate welding. Pomerleau’s expertise in deep foundations was used in this project, which was executed in an own-force model. The company worked on the RCV foundation for nine months, from September 2022 to June 2023.
“RCV is a project that perfectly aligns with Pomerleau’s values,” said Damien Lamblot, Pomerleau’s project director, deep foundations – civil & infrastructure. “It’s a collaborative execution method that allows us to achieve high standards in environmental performance, health and safety, and quality, while respecting the client’s budget and timeline.”
Mathieu Catonné, senior project manager – civil & infrastructure at Pomerleau, describes the job in more detail. “The deep foundation scope included 17,500,000 pounds of steel ordered for 1,800 driven piles – these ranged from 12 to 30 inches in diameter and were mainly going to the bedrock at a depth of 100 feet,” he said. “The mean diameter of the steel piles was about 20 inches. Piles were provided in two pieces, and we had to splice them. We installed the first section, driving through the ground, then spliced the next part.”
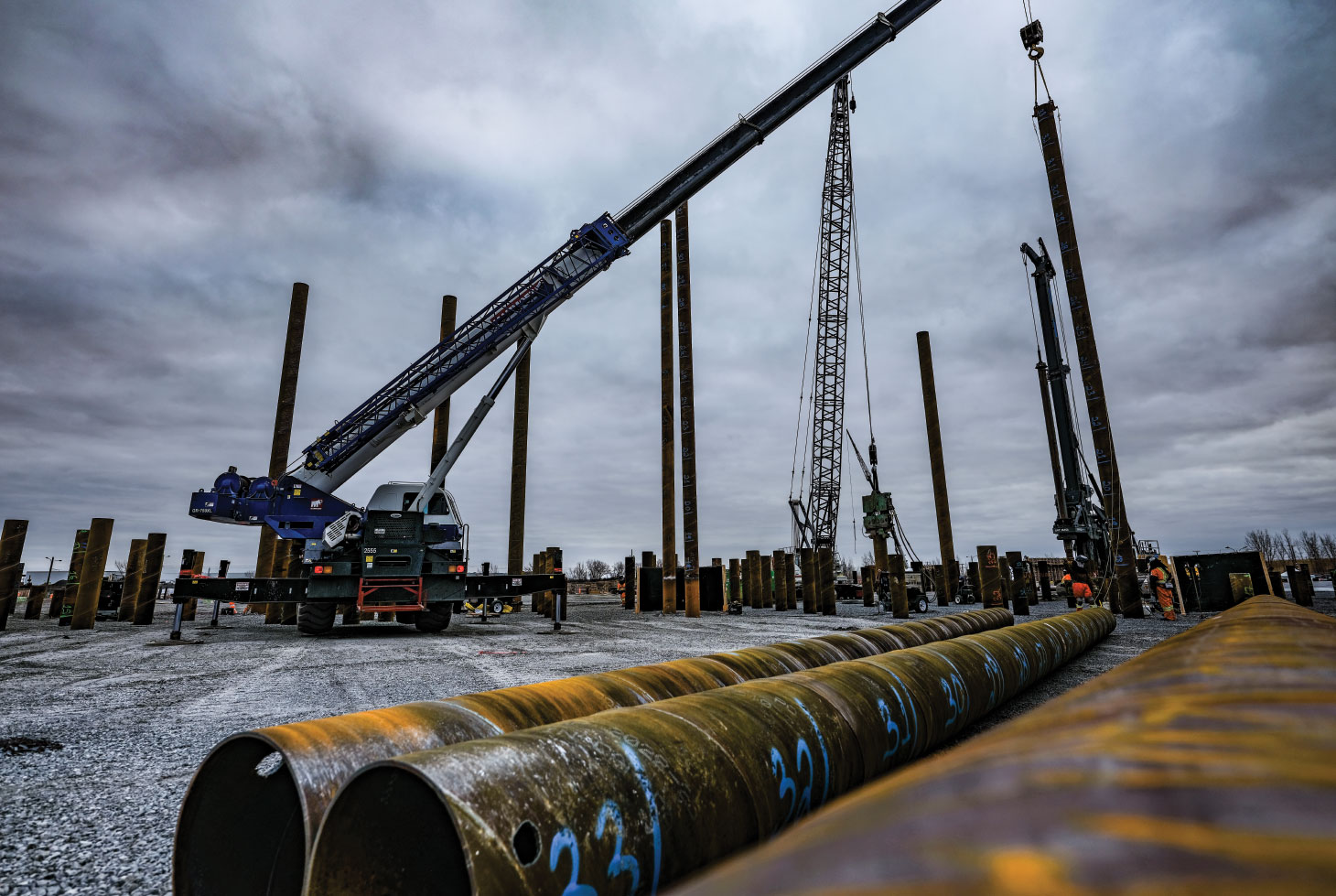
Catonné says 3,300 pile sections were spliced, with 20 welders on the job at peak times. He says the open steel pipe piles were driven through conventional clay until they reached bedrock, with “no big surprises” encountered along the way. Equipment used on the job included two Liebherr LRH-100 piling rigs, a 110-ton service crane and three pickers from 60 to 80 tonnes each.
“We also had to mobilize a Liebherr LB 36 drilling rig to carry out the excavation of the ground inside the open 30-inch piles because these were reinforced concrete elements,” said Catonné. “We also used an ICE 50B vibro driver to assist with the installation of the bigger piles.”
Pomerleau handled the excavation for the project, removing up to six metres of soil to commence top plate installation. Once the piles were situated, the team had to prepare them for connection to the plant’s infrastructure. “We installed the top plates by welding steel plates on top of the piles, cut at the right level. On the plates, there was some protrusion rebar attached. So, the finished product was a pile with some rebar welded on top of it,” said Catonné.
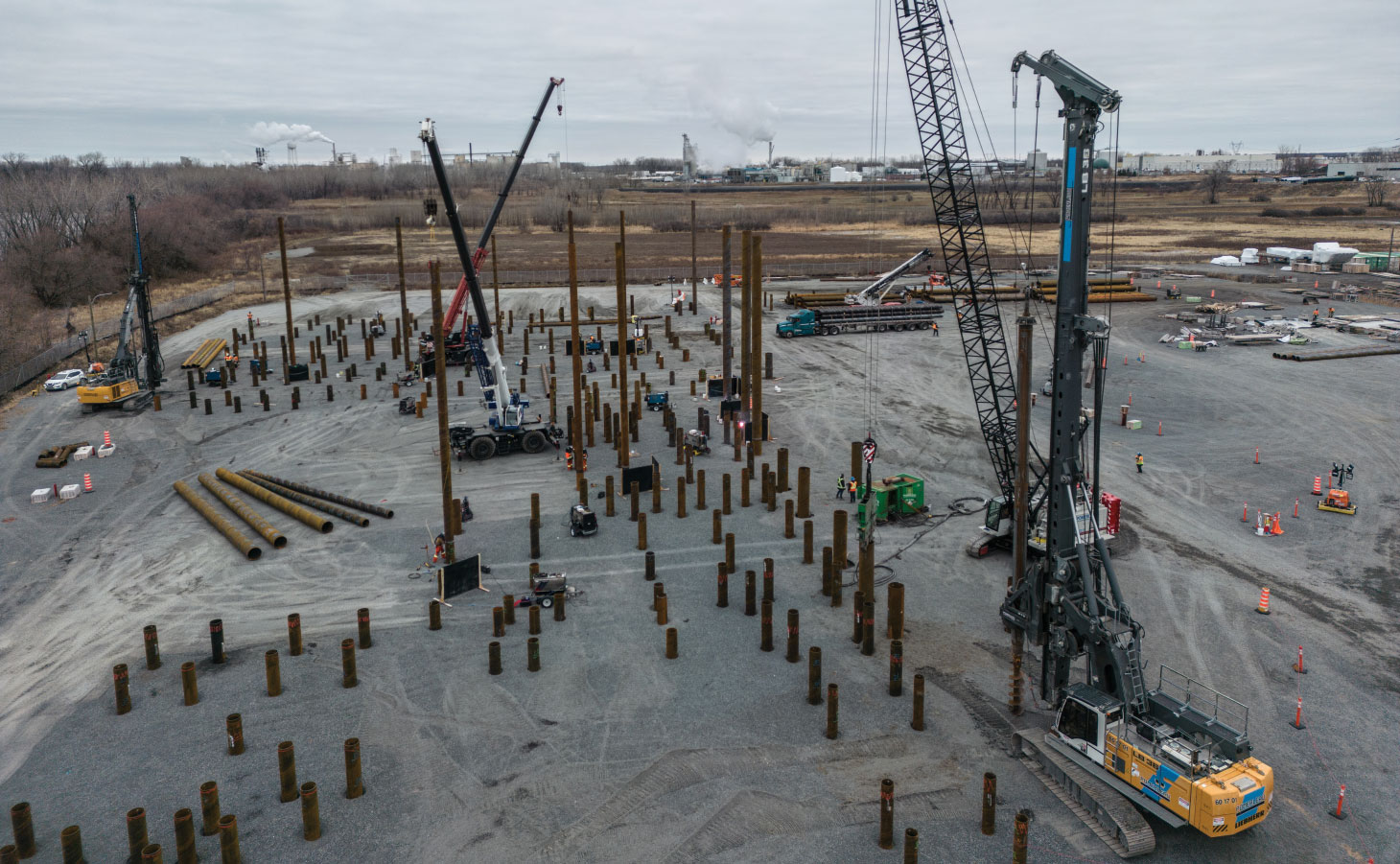
To control costs while ensuring maximum order flexibility, Pomerleau selected Pipe & Piling Supplies Ltd. of Quebec, a local piling provider.
“It was cost-effective, but also provided us with good flexibility for the length of the piles,” said Catonné. “We weren’t 100 per cent sure of the rock stratigraphy. The good thing with the local supplier is they could change the plan with us and provide the necessary agility to help with a change in the sequence of work, depending on site conditions. We tried to store as much pile on site as we could to provide a buffer, but with three fabrication plants, this supplier had the capacity to deliver even if there was a breakdown at one plant. The client was satisfied.”
Environmental precautions
Due to the plant’s location alongside the St. Lawrence River, the environment was naturally a concern. While Pomerleau already uses organic oil in all its equipment, Catonné says they employed additional precautionary practices. These included using dedicated containers to segregate waste products and prevent spills, weekly support visits from Pomerleau’s environmental department, and less pile wastage due to the local supplier’s flexibility.
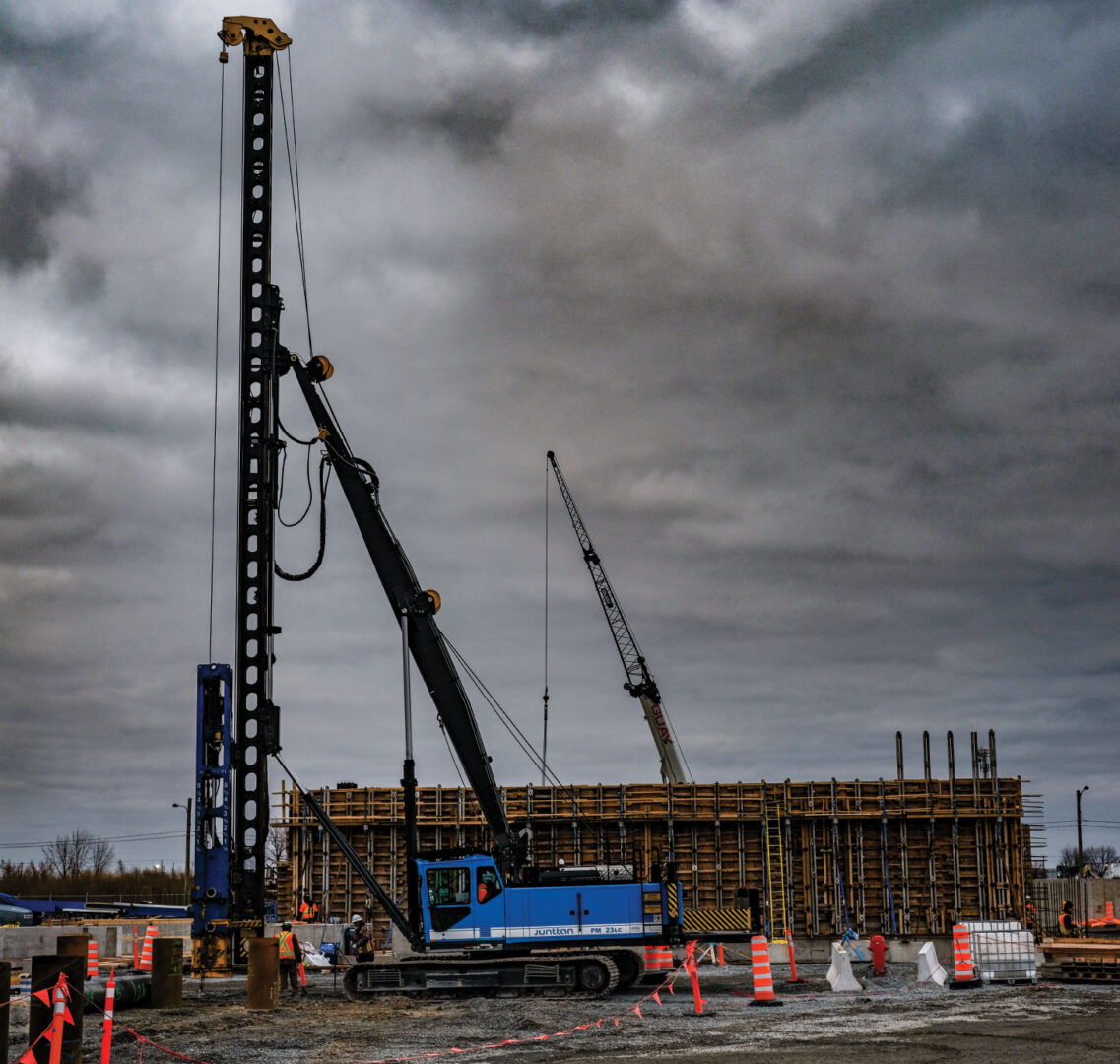
During the project’s peak, Pomerleau had about 60 people working on the RCV site, running a single day shift. The company is very proud of its safety record for this project, with not a single long-term injury reported over 60,000 hours of work. “Safety is paramount for Pomerleau,” said Catonné. “When safety works, everything works. We are happy to report that the few incidents observed over the course of the foundation scope required first aid only.”
The company launched several initiatives to keep workers healthy and safe. To support proper ergonomics for welders, Pomerleau over-excavated around the base of each pile, bringing the welders to the right level so they could stand up while securing the top plates to each pile.
“Our client, Black & McDonald, along with the owner, RCV, supported us on this,” he said. “We also provided welders with Versaflo™ masks that provide a continuous flow of filtered air, which helps keep workers comfortable throughout their shifts in any weather conditions. So, you are always breathing fresh air while you’re welding. This is an investment that reduces the possibility of an on-site incident and preserves the long-term health of our employees.”
“The deep foundation scope included 17,500,000 pounds of steel ordered for 1,800 driven piles – these ranged from 12 to 30 inches in diameter and were mainly going to the bedrock at a depth of 100 feet.”
Mathieu Catonné, Pomerleau
Pomerleau crews completed the job throughout a Quebec winter, which brought its own challenges. “We went through a full winter. It’s not uncommon to work in winter conditions in Quebec; we just had to deal with it and plan accordingly, with the right gear for the workers,” said Catonné.
Reflecting upon the RCV job, he is pleased with the result. “It was a very successful project. Every construction site has its share of problems to solve, but overall, it went very smoothly. Here at Pomerleau, we have a 60-year history. In recent years, our deep foundation department has grown significantly, and our project portfolio is expanding rapidly. The Varennes plant project aligns perfectly with the direction Pomerleau aims to take. Additionally, the jobs we are being awarded are becoming increasingly complex, showcasing our capability to handle more challenging projects.”