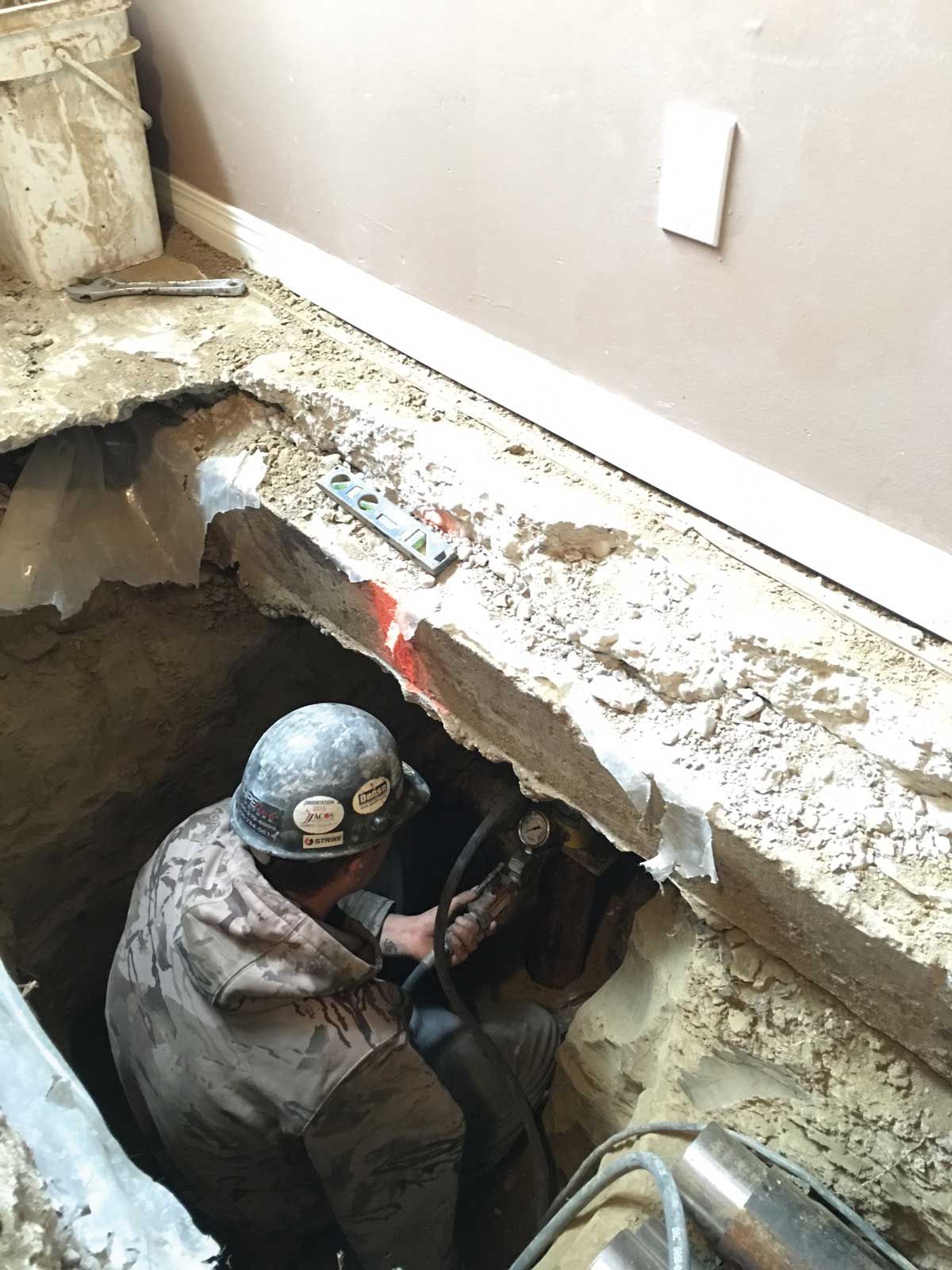
HC Matcon Inc. is a geotechnical excavation, shoring and foundations firm based in Ayr, Ont., a small community near Kitchener-Waterloo that is about an hour’s drive west of Toronto. As some of their work is done in the crowded urban confines of downtown Toronto and its surrounding municipalities, the company specializes in underpinning of existing building foundations.
Jason Weck, president of HC Matcon, says the underpinning jobs performed by his company are typically to repair, strengthen or deepen foundations, work that generally requires someone who possesses not only a strong pair of hands, but smarts as well.
“It is heavy, hard work. It’s a lot of hand digging, a lot of small excavation work, so it’s very difficult labour,” he said. “You need someone who is careful and understands the technical components of the job. You have to follow very strict guidelines, but you also have to make decisions on the fly sometimes because not all engineering drawings are perfect. It’s a skilled labour, for sure.”
Underpinning has been going on for at least 100 years and is becoming more common as more and more buildings are repurposed. One of oldest techniques is to mass pour, which starts with excavating soil from beneath a foundation in controlled stages or sequences called ‘pins’ and replacing the soil with mass concrete. “This method is typically used when it is required to lower the existing foundations and where the existing footing footprint can be maintained,” said Weck.
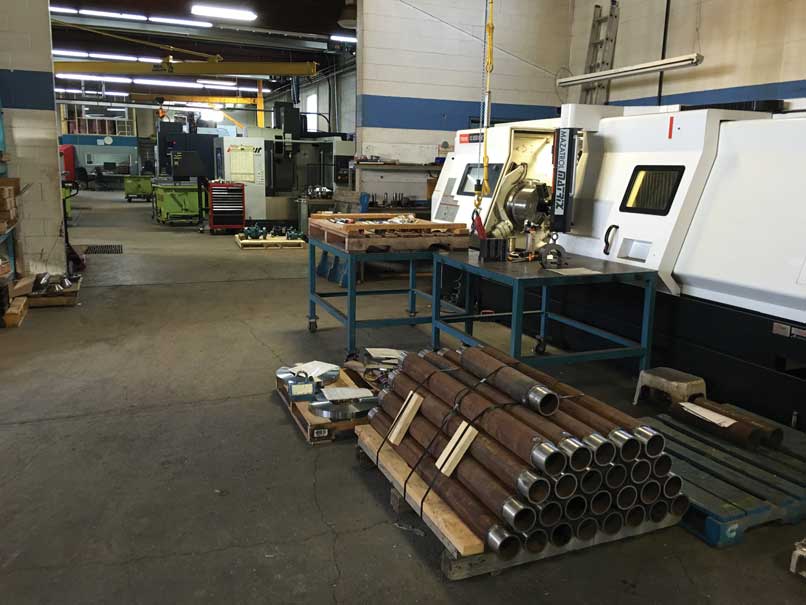
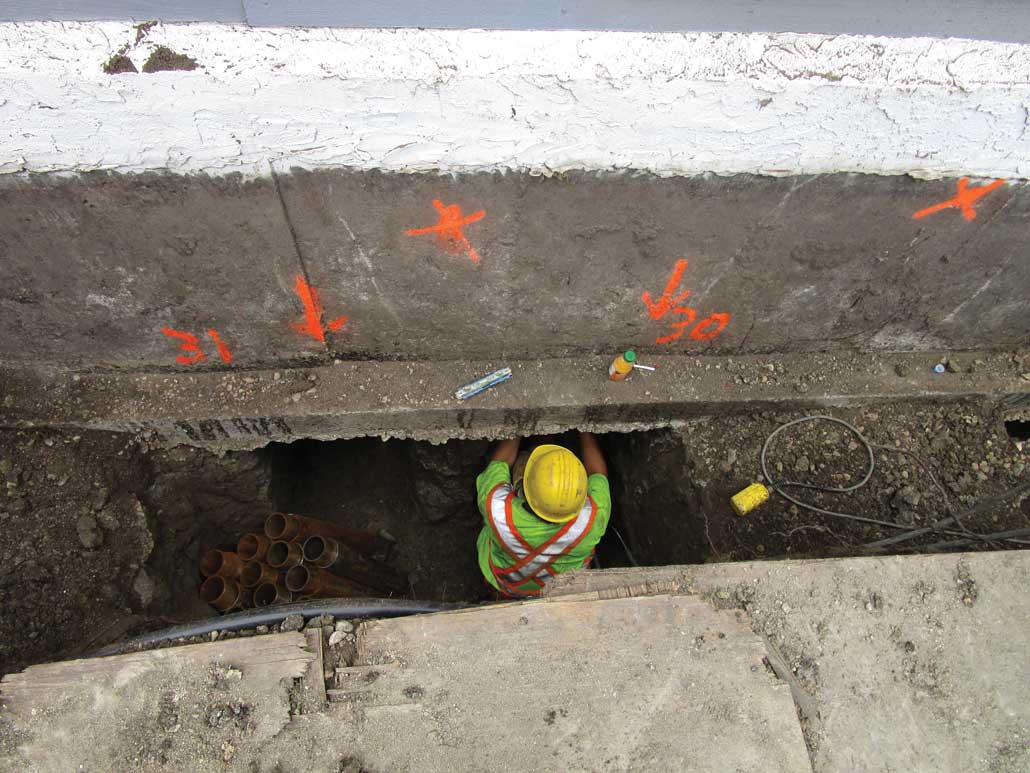
“Where existing foundation footing footprints cannot be maintained or the depth of the underpinning exceeds lateral stability allowance, mini/micropiles can be introduced to pick up the additional vertical loads and tiebacks to retain it laterally. These techniques require specialized engineering and special equipment and expertise to work in these usually confined workspaces.”
Another type of underpinning, known as beam and base, is the most technically advanced. Here, a reinforced concrete beam is constructed below an entire foundation to replace the existing footing. The new beam rests on large concrete bases that are also constructed, and this transfers the building load more evenly across the soil. This method is the least common, and the feasibility of the beam and base technique depends largely on the structural configuration of the building above the foundation.
“It is heavy, hard work. It’s a lot of hand digging, a lot of small excavation work, so it’s very difficult labour.”
Jason Weck, HC Matcon Inc.
Design/build underpinning projects
Weck says about half of the underpinning work HC Matcon does is mass pour and the other half is mass pour combined with mini-piles and tiebacks. He notes the underpinning method for a project is usually determined by the requirements set out by structural and geotechnical engineers, and the load bearing capacities that they’re trying to achieve.
“We’re a specialty contractor that does design/build underpinning projects. We deal with almost all the engineering on our own and the design component of the project is done by us,” said Weck. “Usually what happens is we bid the job with a general understanding of what the structural engineer wants. If we get it, we’ll do our own engineering shop drawings and submit them for review, and then we install.”
Weck says much of the underpinning work HC Matcon does is in the older parts of Toronto, “where buildings are basically touching each other” and there’s really not much room for digging. In those instances when mini-piles need to be installed, Weck says his underpinning team will drill down as much as 100 feet if needed.
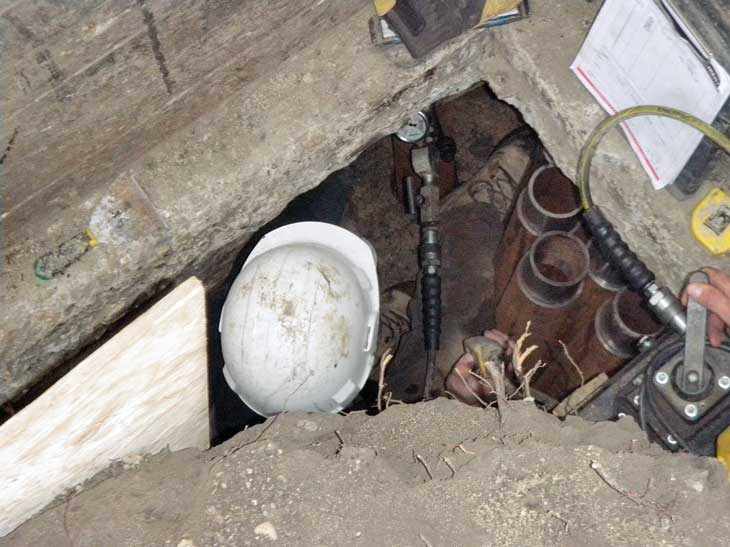
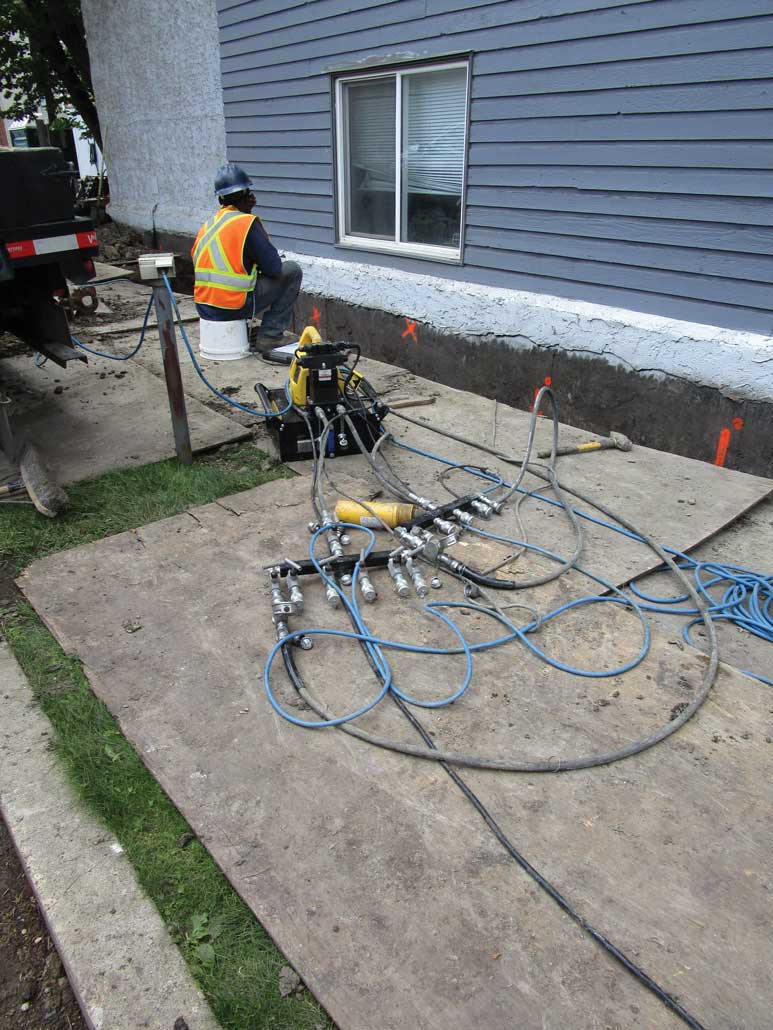
“It really depends on the project, but at the end of the day, you drill them as deep as you need to go,” he said. “You’re trying to establish that pile in a soil that has the ability to carry the additional load of the building.” However, Weck says that the conditions in the Toronto area are often quite favourable for underpinning because the ground typically consists of fairly cohesive materials. “They’re not like a sand or something like that,” he said.
Weck says the most common type of underpinning job performed by HC Matcon is lowering the depth of the existing foundation in a commercial building to create a floor with taller ceilings – a task which, depending on the size of the project, can take two to four months and require up to six people.
“We do a lot of big commercial underpinning,” said Weck. “Many times, what they want to do is make that main floor space more attractive by giving it a 12-foot ceiling height versus, say, a nine-foot ceiling.”
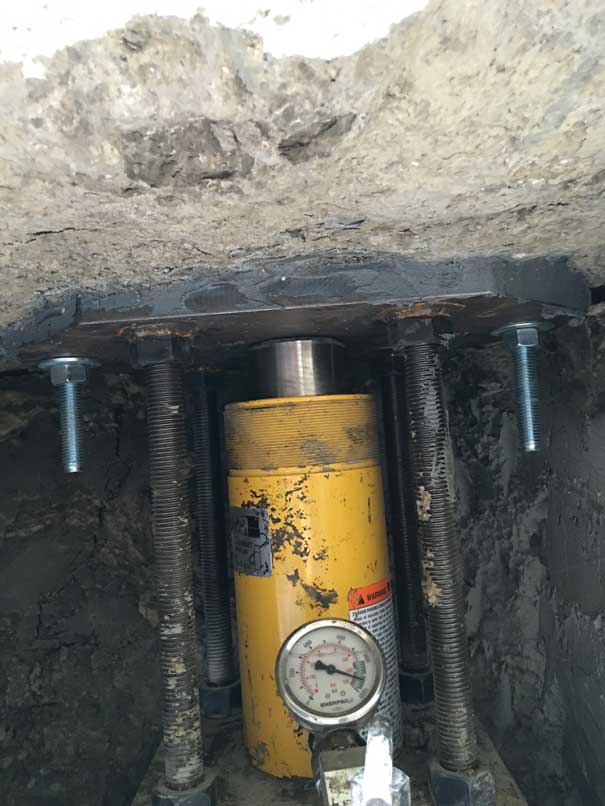
Weck says his underpinning teams will typically create larger footings for the deeper foundation at the same time. This increases the load bearing capacity and the ability of the foundation to support additional storeys, which is why many of HC Matcon’s commercial customers choose to have one or several storeys constructed on top of the building once underpinning is complete.
There are a number of other reasons for underpinning besides retrofitting and repurposing buildings. It’s often used to remediate unstable or failing foundations. Underpinning is also used to stabilize the foundations and/or footings of a building in a couple of different situations: 1) when soil around the foundation has been excavated due to the construction of nearby structures and 2) when a building has moved due to natural causes such as slope slippage, flooding or earthquakes.
Push pier underpinning
Abarent Construction Ltd. is a foundation repair contractor and engineering firm with a head office in Edmonton, Alta., that often uses a micropile application called “push pier underpinning.” In this application, pile sections called “push piers” are hydraulically driven into the ground beneath a foundation by using the weight of the building to push against the piles.
Company owner Kevin Braddell says Abarent has taken the technology further by devising a system that provides added stability and strength by installing push piers in a concentric fashion directly beneath the foundation walls.
Abarent’s piers are 24-inch-long sections of tubular steel pipe that are pushed by a hydraulic ram straight down from the centre line of the foundation above them, rather than at an angle like some other push pier systems. Braddell says this prevents the creation of eccentric or twisting loading on the existing foundation structure, which in many cases was never designed to withstand eccentric loading. According to Braddell, a coupling system and bolted brackets eliminates any need for on-site welding.
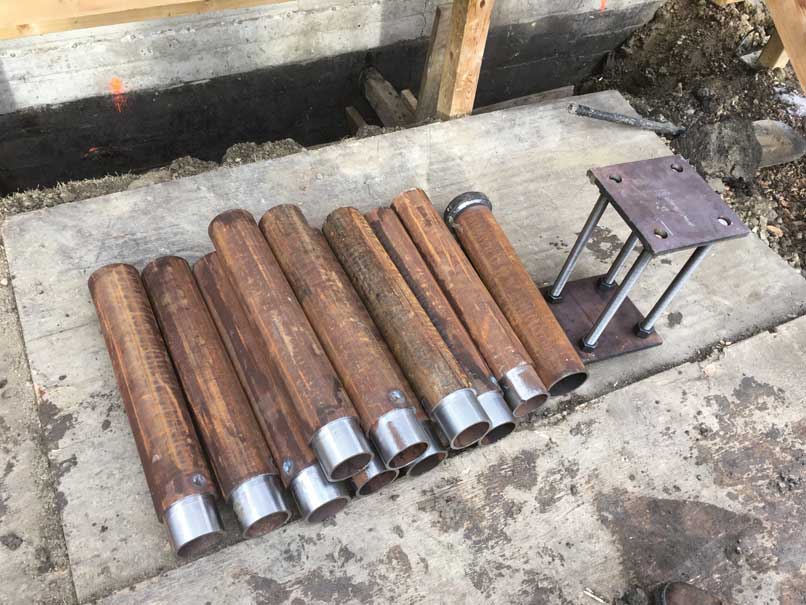
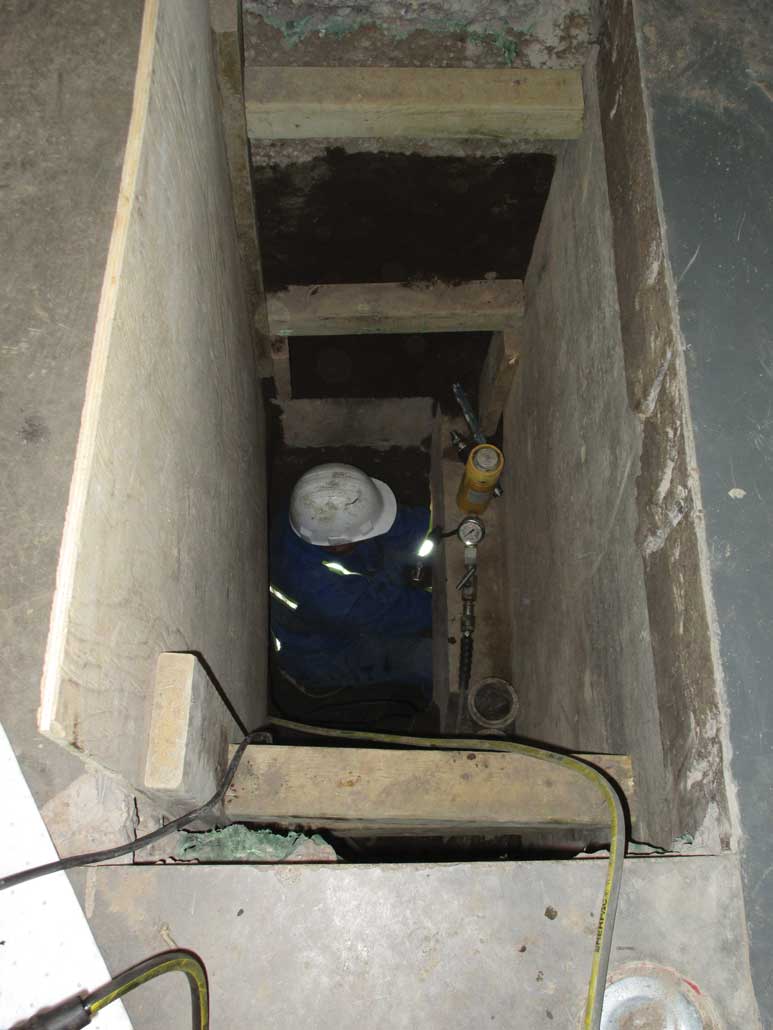
“All pipe, coupling and bracket components have been fully tested in a testing laboratory at an Alberta research facility,” he said. Braddell says the diameter of the push piers will vary according to the project. “We’ll use pipe that’s 4½ up to 7½ inches, whatever we need to manoeuvre the pipe in that soil for the loads required for the structure,” he said.
Braddell says the company’s underpinning jobs typically involve six or so people, but it can be up to 20 for larger projects. He adds there’s a fairly stringent training process that goes into installing push piers that emphasises touch point safety awareness.
“The person in the excavation who is pushing the piles has full control of the ram. There’s an install switch [they’ll] turn off and on, and [they] always [have] to make sure [their] fingers aren’t where they shouldn’t be,” Braddell said.
“Before we allow a person to be the one in the hole manoeuvring the install switch, [they have] to have gone through a significant number of installs as the recorder, who is at the top of the hole recording pressures and anomalies that we might encounter with the soil as the pile goes in. That’s where we start people, generally.
“Our niche is tight-access underpinning and foundation stabilization in spots that other equipment can’t get into.”
Kevin Braddell, Abarent Construction Ltd.
“Our structural engineer does significant site inspections, monitors the install, reviews all the install logs, all the pressures. That way, when [they go] to do [their] final inspection and compliance at the end of the job to certify all the piles as being installed appropriately and to proper loads, [they] can actually say that [they’ve] had a hands-on visual accounting of what went on.”
Braddell says two main benefits of the type of building remediation work his company does are that it can be done in close quarters and without heavy equipment. “Our niche is tight-access underpinning and foundation stabilization in spots that other equipment can’t get into,” he said. “One example would be a residential setting where houses are placed very close together and it’s hard to manoeuvre. Everything is just loaded in by hand, and sometimes the excavations are done by hand because there’s no opportunity for using machinery due to space restrictions.”
Braddell says that apartment buildings present another unique challenge.
“In one case, we had to underpin the outside perimeter, but we also had to underpin the interior bearing walls and strip footings at the same time. So, we’re inside apartments, we’re inside hallways, storage rooms, mechanical rooms. You can’t use anything other than the hand-held equipment in those spaces,” he said.