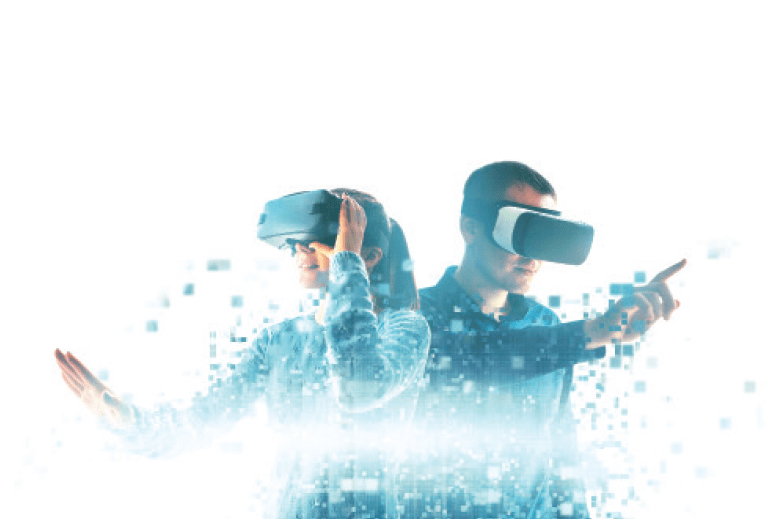
Fairly or unfairly, the Canadian construction industry has a reputation for being slow when it comes to the adoption of new technologies.
In fact, a 2017 industry survey conducted by KPMG indicated the majority of Canadian construction and engineering firms did not have a technology integration strategy in place, and most considered themselves technological followers rather than leaders.
Despite this technological reluctance, one relatively new form of technology is becoming adopted by an increasing number of companies in Canada’s architecture, engineering and construction (AEC) sector, and has the potential to be a serious game-changer for many segments of the industry, including deep foundation construction.
Virtual reality (VR) and augmented reality (AR) are perhaps best known for their use in today’s multi-billion-dollar video game industry. However, that same technology is starting to gain a toehold in the construction industry, and is being used for everything from planning and virtual walk-throughs of design plans to helping conduct quality assurance inspections.
While VR and AR technologies have been around since the 1990s, they did not become mainstream until the past decade; and it wasn’t until about five years ago – thanks to the increasing use of building information modelling (BIM) – that they started being used in construction.
Piling Canada recently spoke with two leading technology companies about why VR and AR use is increasing in the construction industry, what these advancements have to offer to both large and small construction firms and what this all means for the future of construction in Canada.
Virtual reality vs. augmented reality
Prior to any discussion about the merits of VR and AR in the construction industry, it is worth noting the differences between the two. In simple terms, VR is a completely simulated environment created by computer technology. AR, on the other hand, enables the user to stay visually present in the real world while elements are augmented by computer-generated overlays that provide an X-ray view into an object or environment.
Unlocking spatial understanding
New York-based IrisVR is one of the world’s leading companies when it comes to the use of VR in the construction industry. Its software system is currently used in more than 100 countries, including Canada. The company was founded in 2014, by partners Shane Scranton and Nate Beatty, both of whom had been working in the AEC industry and encountered difficulties communicating design intent using conventional 2D and 3D models.
Scranton, a self-professed “geek,” had become fascinated a few years earlier with the new generation of VR headsets that was available. He and Beatty soon began thinking of how this technology could be used to overcome some of the communication difficulties they had been dealing with.
“I was interested in trying out the new technology and got some 3D files of buildings into a headset manually so you could walk around and look,” said Scranton, the company’s CEO. “Suddenly in a headset, it was such a clear representation that really unlocked spatial understanding for building design much earlier in the process. VR and AR are really the only mediums where it’s a literal representation of what you’re going to get. You don’t have to stretch your brain to imagine it. It feels like you’re physically there. It’s such a fundamental difference.”
How does it work?
Scranton says the IrisVR software system was designed to be user-friendly for everyone, including people who aren’t overly familiar with the technology.
A user can upload virtually any kind of 3D design file, including Navisworks or Revit files, to a cloud-based server where it is converted for use with a VR headset. It can then be shared with any number of colleagues or clients regardless of where they may be located. Users can choose to use a standalone VR headset (which cost about US$400) or one linked to a personal computer for a premium experience.
Once the user is connected to the IrisVR system, they become completely immersed in a building’s design. They can literally walk anywhere within it and view it from multiple angles.
Scranton says one of the system’s biggest benefits for construction clients is that it allows them to catch errors earlier in the design process and correct them much sooner and cheaper.
“You’re not doing it on a jobsite that way, you’re doing it when you’re in the office or in your home office. You’re able to make changes earlier in the process so that things don’t pop up later and cost you a lot more,” he said.
Another advantage of the IrisVR system is that it helps promote collaboration between company staff, other construction firms and various trades. Regardless of where they may be physically located, every stakeholder tours the virtual building site at the same time and can communicate with each other in real-time thanks to a built-in voice-chat feature. The system also allows users to delineate workflows and mark up any proposed changes to a building plan, which Scranton says is ideal during the current pandemic when many people are working from home or remote locations.
The IrisVR system is already used by a number of Canadian construction companies including SNC-Lavalin and Exergy Solutions. One of the advantages of the system when it comes to deep foundation or piling work, according to Scranton, is that it allows companies to provide site-specific training to workers before they ever set foot on a job and thereby increase worker safety.
“You can put on a headset from the safety of your home or office, and using our technology, you can essentially walk through a project site and walk through any kind of sequence that would have to be done on-site. And by the time someone who is an operator or in maintenance shows up to the project, they are much more situated about what they need to do, how to do it and what the safety requirements are around a project,” he said.
What a difference
While IrisVR’s core customers are in the AEC and oil and gas sectors, its system is also in use in several other industries: defence, aerospace, automotive and manufacturing. Scranton says what differentiates it from other similar systems is that it’s enterprise grade thanks to the company’s early research into the technology, and it supports a broad range of file formats and headsets. “We talk a lot internally about being agnostic on the inputs and agnostic on the outputs,” he said.
The system is also easy to learn.
“We typically see folks getting their ‘VR legs’ and getting comfortable with the technology literally within a few minutes. We’ve done a ton of work to basically make it point and click easy,” Scranton said. “Ultimately, we only succeed if people are talking about the building rather than our technology.”
The starting price for IrisVR software is US$225 a month for individuals while volume discounts are available for businesses.
Filling a need
California-headquartered Avatar Partners, a pioneer when it comes to AR, is starting to gain some traction in construction. It was founded in 2003, and has been providing solutions to a lengthy list of industry partners since then, including the U.S. Navy, Northrop Grumman, Mitsubishi, the U.S. Airforce, BAE Systems and the U.S. Coast Guard. It set its sights on the commercial construction industry two years ago after realizing the monumental benefits – such as safety improvement, expense reduction and elimination of errors – that were being achieved by agencies using its software would also apply to commercial construction.
Avatar Partners, which has offices across the U.S., offers 11 augmented and mixed reality software applications including six specific to the construction industry: Avatar Connect, SimplifyXR, Smart Design, BIM2Field, ARFab and the Augmented Reality Maintenance Aid.
Unlike VR, Avatar’s AR software allows users to overlay virtual content into the physical world in a way that makes the content seem physically there, and essentially merges the digital and physical worlds using a mobile device. For example, users can draw in objects in 3D using a tablet or remote PC to provide guidance or instructions to ensure a job is performed correctly thanks to a unique annotation feature that is part of the system.
Brian Toppel, subject matter expert for Avatar’s AEC division, says the company’s BIM2Field product has three primary uses for construction firms: installation location, installation instruction and installation verification or QA/QC.
That’s especially important when it comes to deep foundation work such as installing caissons or piles. For example, with the Avatar system a worker can simply mark on a tablet or mobile device the location of where a caisson or pile has been installed. The program then creates an overlay which can be used to compare that location with the intended location.
“The key to successful enterprise AR is precision,” said CEO Marlo Brooke. “Our solutions maintain an accuracy of one-eighth of an inch on any situation, whether that’s a doorway frame or a large stadium. This means that the BIM model is implemented correctly the first time around. We can also use artificial intelligence to perform auto QA-checks during every step of the build cycle, ensuring that any deviations are caught and can be corrected early-on.”
Toppel says because the system is so accurate, it helps to dramatically reduce errors on construction sites which in turn eliminates a lot of “rework” and thereby reduces costs.
A former project manager in the construction industry, he says the Avatar construction apps can also help increase worker safety on a jobsite.
“Look at a caisson operation. You’ve got all these things going on at once: guys drilling, guys coming in with Bobcats. It’s kind of a choregraphed ballet,” he said. “With our system we can actually do a training solution that goes through all of that and see what steps people are actually doing compared to what they should be doing, and we can create a more safe environment.”
The Avatar software can also help achieve significantly better production rates. Toppel says in some cases using it can translate into time savings of as much as five to 10 minutes per caisson.
“That’s important because it’s all about unit rates in deep foundation. It’s all about how many can I get done in a day?” he said.
Toppel says Avatar solutions also help make it easier to share knowledge between senior employees and personnel on the ground. Therefore, tasks that would normally be handled by senior staff can now be performed by less experienced people.
X-ray vision
Perhaps one of the coolest features of the Avatar AR solutions is that users are provided with a sort of X-ray vision into any kind of object. Users can easily pull the object out of wherever it is located and examine it from any angle.
“What we’ve found is a 90 per cent reduction in QA inspections and quality inspection time with augmented reality, and being able to identify errors that were not in the paper schematics,” Brooke said.
Cost savings
While wearable devices such as the Microsoft HoloLens allow hands-free use of Avatar’s software, it can also be easily used on mobile devices such as smartphones and tablets. The software itself starts at about US$5,000 and can range as high as US$30,000 depending on a client’s requirements. The company also provides a codeless offering environment where clients can develop their own mixed reality and AR construction solutions.
Brooke says that’s a small price to pay compared to the net savings a company can realize by using the system.
“The return on investment is immediate. It’s generally within the first one or two uses,” she said. “The thing to know is augmented reality is not a silver bullet. There’s very specific times when it will and will not be useful. Using AR for advertising is not going to provide a huge return on investment. However, if you can prevent a wiring error that could not only save lives, but save money, that’s huge.”
Breaking into market
Despite making inroads into the U.S. construction industry, Avatar is still looking to crack the Canadian market. Brooke and her company have begun talking with a number of systems integrators in Canada about bringing its software north of the border and is hopeful those discussions will soon bear fruit.
“We know in Canada that efficiency and saving money [are] very important, and there tends to be more of an open mindedness in Canada and Europe about new technology. We are looking for partners that are based in Canada and specialize in construction to help facilitate progress,” she said.
Only just begun
Scranton says the sky is the limit for companies that are offering AR and VR solutions, especially in the construction and deep foundation industries where productivity levels have not kept pace with other sectors.
“I don’t think we’re close to the finish line yet. I think there’s a lot more coming in terms of being able to represent a building more accurately earlier on so that more can be decided early. And installation is much easier and training is easier when it comes to dealing with the physical side of things,” he said.
Toppel wholeheartedly concurs.
“It hasn’t even started. AR and VR are not even close to being mainstream yet. We haven’t even come close yet to breaking in. It was only 10 years ago people started using BIM. Now it’s everywhere. In terms of where we’re at with AR, we’re really just beginning.”