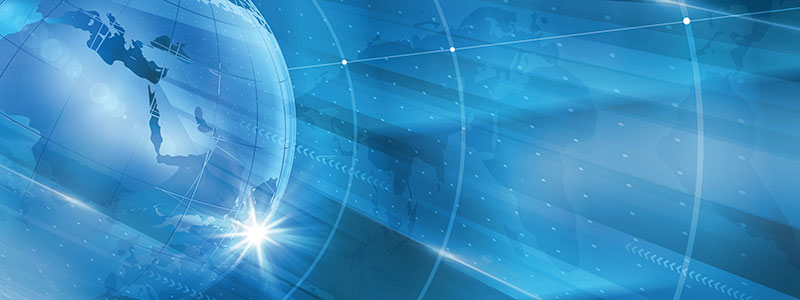
Dawes Rigging & Crane Rental earns 75-year longevity award from SC&RA
Seventy-five years ago, the organization that would become the Specialized Carriers & Rigging Association (SC&RA) was born, and Dawes Rigging and Crane Rental, a member of the ALL Family of Companies, was there as one of eight charter members.
Dawes has been formally recognized for this, earning its 75-year longevity award. In addition, the branch was honoured with safety awards for crane operation and transport.
The beginnings of SC&RA go back to 1947, when it was founded as part of the Local Cartage National Conference (LCNC) of the American Trucking Associations. The following year, the Heavy Haulers, Machinery Movers and Erectors Section of the LCNC (the precursor to SC&RA) was formed, with Dawes and seven other companies participating. Today, membership tops 1,400 companies located in nearly 50 countries.
Dawes general manager Steve Freckmann is a longtime believer in the value of SC&RA, including 15 years serving on various committees, with a chairmanship on the Crane & Rigging Group, and a three-year term on the board of directors. He currently serves on the Crane & Rigging Group Labor Committee.
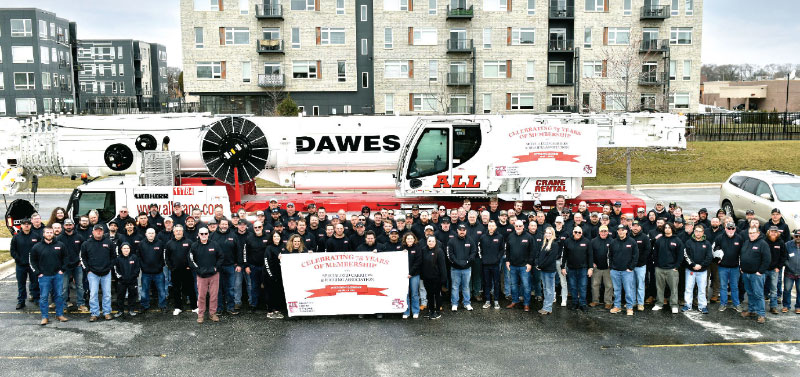
“From the networking opportunities SC&RA provides, to ongoing programming, to legislative and regulatory advocacy at the state and federal levels, no other organization has done more to advance our industry,” said Freckmann. “It is truly the central hub of information and action that moves all of us in this business forward.”
In addition to the monumental longevity award, 14 Dawes crane operators received the Operator Safety Award, recognizing 10,000 hours without an accident or incident. Driver Karl Jablonski earned the Driver Safety Award for his own 10,000-hour safety achievement.
These individual safety awards have become a regular occurrence for Dawes team members when SC&RA hands out the annual honours.
“Safety is an investment in your future,” said Freckmann. “The employees who win this award are proud of the national recognition they receive for their accomplishments. It strengthens their safety awareness and drive to want to win the honour again. Newer operators and drivers see the vests, the patches and the recognition winners earn, and they want to earn that too.”
Trevi Group awarded orders and contracts totalling $848.94 (€591) million since January
Trevi S.p.A., the division of the Trevi Group specialized in deep foundations and geotechnical works, and Soilmec S.p.A., the mechanical engineering division of the Trevi Group that designs and manufactures equipment for ground engineering, in line with the positive trend of the previous year, was awarded, in the first four months of 2023, orders and contracts for a total of $310.56 (€216.2) million. Thanks to these acquisitions, the Group’s order backlog amounted to $848.94 (€591) million in April.
“In addition to the Trevi acquisitions and the Soilmec orders that have consolidated our Group’s order backlog, we are working, with good prospects, on other interesting development opportunities both in Italy and abroad,” said Giuseppe Caselli, CEO of the Trevi Group.
Some of the most recent acquisitions include projects in Italy and the Middle East.
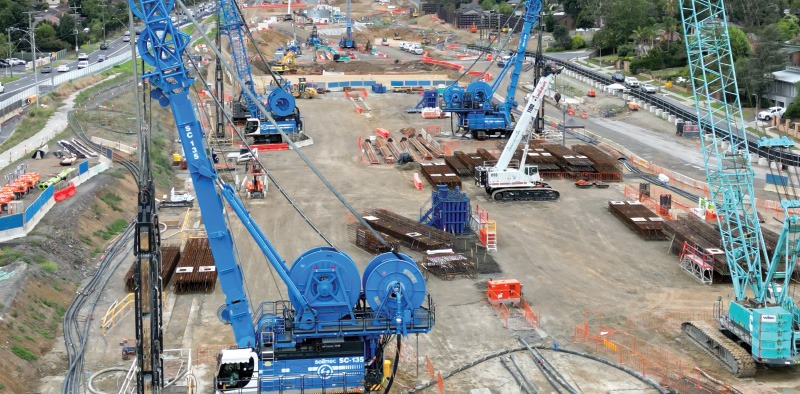
In Italy, Trevi S.p.A. has recently signed a contract for the execution of the foundation works for the new Railway Link in Florence. This is the urban section of the new HS/HC line that will run underground with two parallel tunnels for approximately seven kilometres.
In Milan, Trevi will be working on behalf of Evd Milan – a company belonging to the Cts Eventim Group, listed on the Frankfurt Stock Exchange – on the piling works for the construction of the new Santa Giulia Arena, a multi-purpose facility that will host hockey competitions during the Milan-Cortina 2026 Olympic Games.
In Sicily, Trevi will work for the Messina-Catania northern lot consortium, which was awarded by Rfi the “Fiumefreddo-Taormina Lot 2” of the railway doubling on the Messina-Catania section.
New acquisitions were also made in the Middle East.
In Saudi Arabia, Trevi Arabian Soil Contractor, the local subsidiary of the Trevi Division, will carry out the foundation works for the construction of the new DoubleTree by Hilton Jeddah King Abdullah Square Hotel and Suites.
In Kuwait, the Trevi subsidiary will carry out the foundation works for the CMA Tower, the new headquarters of the Capital Market Authority (the body that supervises the financial stability of the Kuwait Stock Exchange, the oldest in the Gulf region).
Finally, in the U.A.E., Swissboring Overseas, a subsidiary of Trevi, will be involved, on behalf of the MAG Group, a real estate company, in the foundation works for the Keturah Resort, destined to become, with villas, flats and hotels, one of the largest wellness centres in the world.
Con-tech can help Canada address housing, infrastructure challenges: KPMG in Canada
Digital technology can help address the backlog of Canadian housing and infrastructure projects bogged down by unprecedented demand and a chronic shortage of skilled labour, finds new research from KPMG in Canada.
A new KPMG in Canada survey of 275 construction companies finds that nearly nine in 10 construction companies say the lack of skilled labour or trades is impacting their ability to bid on projects and/or meet project deadlines and that digital technology can help make their labour force more effective to address these shortages.
“Technology can help the construction industry address Canada’s housing and infrastructure challenges,” said Tom Rothfischer, partner, and national industry leader, building, construction and real estate, KPMG in Canada. “Digital tools, if used smartly, save time and money, reduce waste and improve worker safety and productivity. In short, they help get projects done on time or ahead of schedule and on budget.”
He says that many technologies employed in the manufacturing sector can be deployed by the construction industry to increase productivity and reduce costs. Three-dimensional printing technologies in manufacturing have been adapted to the construction industry to lay concrete and build complex steel shapes. Robots can lay bricks and tie steel reinforcement bars. Drone-based surveying can help contractors quickly and accurately lay out work, measure quantities and monitor progress.
Building information modelling (BIM) allows project teams to collaborate more effectively to develop innovative solutions to optimize project cost and schedule. Digital twin technologies build on BIM to integrate real-time data from a built asset with its exact 3D virtual replica to test ‘what-if’ scenarios, including the impact of design changes, construction sequencing, weather disruptions and operational changes.
As in other countries, Canada’s construction industry, which spans residential and commercial real estate, industrial, institutional, civil and infrastructure, has been slow to adopt new digital technologies. However, the pandemic, combined with the intensifying labour shortage, has proven to be the catalyst the industry needed to rethink how they go about their business.
“We’re seeing a definite recalibration taking place in the construction sector,” said Rothfischer. “While many are still just at the beginning of their digital build, leaders see the power of technology to reshape the way they work and plan to invest heavily in the coming years. But having the technology is only half the battle. The real advantage will come to those firms who effectively integrate it into their operations – from the back office to the construction site.”
Key survey findings
- 73 per cent think that the construction industry in Canada lags other countries in digital technology adoption
- 67 per cent say the impacts of the pandemic prompted them to invest in technology
- 86 per cent agreed that disruptive technologies can generate savings and efficiency, of whom 50 per cent agreed strongly
- 85 per cent believe disruptive technologies could make their companies more competitive
- 81 per cent say their management and back-office teams and 80 per cent say their project teams and labour are excited about and supportive of new technologies and approaches
- 46 per cent plan to spend more than 11 per cent of their corporate operating budget on tech and digital transformation, 33 per cent anticipate spending between six to 10 per cent, and 20 per cent plan to spend up to five per cent
“Leading firms are already adopting technology to improve productivity and project management, safety on worksites, and decision-making,” said Mary Van Buren, president of the Canadian Construction Association (CCA). “Leading firms are already adopting technology to improve productivity and project management, safety on worksites and decision-making.
“There is a cost however to investing in digitization that isn’t necessarily shared among all parties in the procurement process. Margins are slim in construction, especially for the small- and medium-sized contractors, making it increasingly difficult for them to adopt these types of innovations in their business operations. This is why CCA continues to work with federal departments in an effort to modernize procurement processes that encourage innovation by supporting shared risk.”
The KPMG survey found a Canadian construction industry grappling with a double whammy of unprecedented increased demand for housing and infrastructure projects, and a severe labour shortage that’s challenging the ability of companies to bid on projects and/or meet project deadlines.
Labour crunch hits projects
To address this, almost all contractors are examining ways to alleviate current labour constraints to meet demands.
“The efficient allocation of trades is one of the industry’s most-pressing challenges and opportunities,” said Jordan Thomson, senior manager, infrastructure advisory, KPMG in Canada. “Many companies are deploying or planning to deploy digital tools to better improve efficiency on site and do more with less. The application of data analytics, wearables and internet of thing sensors and BIM can help to improve productivity, schedule efficiency, quality, minimize waste and improve worker safety.”
Yet, as companies embrace technologies, the composition of the workforce will also need to undergo change to incorporate new roles, such as software engineers, BIM designers, data analysts and drone operators into the project team, says Thomson. For example, drones are increasingly used for planning and design, site analysis, topographic mapping and land surveys, real-time monitoring and on-site worker safety.
“With so many construction projects on the horizon, the only way companies will be able to compete, and finish the job on time and within budget is by digitizing and modernizing their operations and ensuring they fully harness the potential of digital technologies,” he said.
KPMG’s survey found that:
- 90 per cent of construction companies are currently experiencing a shortage of skilled labour or trades. This jumps to 94 per cent in Quebec
- 86 per cent say that the shortage of skilled labour or trades is impacting their ability to bid on projects and/or meet project deadlines. This jumps to 94 per cent in Quebec and 90 per cent
in B.C. - 86 per cent say that given current labour constraints, they may need to consider alternatives, such as prefabrication and modularization and/or innovative new tools and machinery (94 per cent in Quebec)
- 89 per cent agree that better project management tools, such as analytics, BIM and digital twins, helps to address labour shortages and improves employee productivity
- 91 per cent believe the education system needs to be “much more flexible” to allow young people to pursue the trades – 97 per cent of Quebec respondents agree
- 77 per cent say that digital transformation will require hiring new talent within their organization to a “great” and “considerable” extent (44 per cent), and to a “moderate” extent (33 per cent)
Deal for new Ottawa Hospital construction shuts out thousands of Ottawa-area workers
Investment in infrastructure is badly needed in Canada. It is critical to the quality of life of Canadians and the competitiveness of the country. Canadians rely on power generation, roadways and transit, water management, hospitals and natural resource development to function personally, socially and economically.
The Canadian Construction Association (CCA) and their 20,000 members across the country have been sounding the alarm about critical infrastructure gaps, but like any investment, those made in infrastructure need to be sound and supported by judicious choices.
Unfortunately, The Ottawa Hospital’s necessary investment of $2.8 billion in a new Civic Campus will likely cost taxpayers hundreds of millions more and leave a majority of Ottawa-area construction workers ineligible to work on the vital project.
An exclusive project labour agreement (PLA) between the hospital and the Unionized Building and Construction Trades of Eastern Ontario and Western Quebec prohibits contractors and workers who are not affiliated with these specific unions from bidding on, or even participating in building, the hospital’s new Civic Campus.
A report by the Montreal Economic Institute (MEI) finds that The Ottawa Hospital’s restrictive PLA will stifle competition, escalating project costs by between $168 million and $525 million by 2028. The authors of the report find it unacceptable for a public entity to make taxpayers pay more by granting exclusivity to a specific group of affiliated workers.
“Not only are a large number of talented workers – many from small and medium-sized firms – barred, but, as the MEI points out, the projects are likely to cost taxpayers more than necessary as a result,” said Mary Van Buren, CCA’s president.
The Ottawa Hospital project is the latest in a series of concerning examples where public sector procurement is falling short on fair and open practices. Another such example is British Columbia’s Patullo Bridge project.
Even more concerning, given their national scale, are the labour requirements attached to the newly introduced federal clean tax credits established in Budget 2023, which again exclude non-unionized construction workers.
“The (CCA) takes issue with these examples and others that either categorically exclude or strongly disadvantage one group of workers,” said Van Buren. “We would take a similarly forceful position if the reverse had happened and union workers had been excluded or disadvantaged.”
In every province but Quebec, non-unionized labour makes up the vast majority of the construction industry. As such, procurement that excludes non-unionized workers excludes most construction workers in Canada. Rather than introducing labour force restrictions, progressive buyers of construction are exploring collaborative models, with improved risk sharing and communications, and focusing on achieving excellence in project delivery.
The public procurement process should not give preference to any particular individual, firm or group. Open and fair competition creates a level and inclusive playing field, which leads to better value for money. This is good for the economy and good for Canadians, says CCA.
Berminghammer announces new parts facility addition to warehouse in Hamilton
Berminghammer, a leading manufacturer of foundation construction equipment, is excited to announce its latest expansion project in Hamilton, Ont. The company is investing in a new parts facility addition to its existing warehouse, further strengthening its commitment to providing top-notch services and support to its valued customers.
This strategic expansion comes on the heels of the successful addition of a new wash, sandblast and paint facility in 2022, which has significantly enhanced Berminghammer’s capabilities. The new parts facility will allow the company to streamline its operations and deliver an even higher level of efficiency in fulfilling customer needs. The forthcoming parts facility addition will significantly increase the warehouse’s capacity for inventory storage, ensuring an extensive selection of spare parts is readily available to support Berminghammer’s diverse range of foundation construction equipment.
This investment reflects the company’s dedication to meeting customer demands promptly and delivering exceptional after-sales support. Berminghammer’s commitment to continuous improvement is not limited to the parts facility addition. Following this development, the company plans to introduce a new load and offload facility, further enhancing its logistical capabilities. These progressive measures exemplify Berminghammer’s dedication to innovation and meeting the evolving needs of the industry.
“Our investment in the new parts facility addition represents our unwavering commitment to providing our customers with unmatched support,” said George Micevski, plant manager at Berminghammer. “By expanding our warehouse capabilities, we aim to ensure that our customers have quick and convenient access to the critical spare parts they need to keep their operations running smoothly.”
The parts facility addition has been operational since June 28. With this expansion, Berminghammer aims to not only optimize its supply chain, but also bolster its ability to serve customers in a timely and efficient manner.
Helmets to Hardhats connects Afghan refugees to careers in the skilled trades with support from Aman Lara
As the Government of Canada works to resettle at least 40,000 Afghan refugees by the end of 2023, Helmets to Hardhats (H2H) is collaborating with Aman Lara and local building trades unions across Canada to provide recently resettled Afghan nationals with opportunities in the skilled trades.
For many Canadian newcomers, finding and securing well-paying, meaningful employment is a critical yet difficult step in their resettlement journey. That is why H2H, a national non-profit organization typically dedicated to supporting transitioning military members, veterans, cadets, reservists and military family members into opportunities in the skilled trades, has expanded their program eligibility to include resettled Afghan nationals. H2H believes that because of Afghan nationals’ sacrifices and support of the Canadian military, it is H2H’s turn to assist them. H2H is easing the transition into Canadian society with career and apprenticeship opportunities in the unionized construction industry.
H2H provides direct and meaningful connections to ensure that Afghans interested in joining the skilled trades can break into the industry with little to no stress and at no cost to the career seeker. The inclusion of Afghans into the H2H program is aiding their successful transition into Canadian life by providing financial stability, earn-while-you-learn training opportunities and access to health benefits and pension plans.
H2H works directly with Canada’s 14 Building Trades Unions to find its clients careers in over 60 different trades and occupations. Aman Lara is also supporting H2H in connecting Afghan refugees to well-paying careers in the skilled trades. Currently, H2H is working closely with:
- Aman Lara: a non-profit organization that evacuates vulnerable people from nations in crises. They communicate directly with vulnerable clients throughout the evacuation process and assist in their resettlement upon arrival in Canada. Aman Lara has been vital in spreading awareness of the opportunities and benefits within the skilled trades to resettled Afghans and their families.
- Carpenters’ Regional Council: is composed of 31 affiliated Local Unions of the United Brotherhood of Carpenters and Joiners of America, representing members from Ontario to British Columbia. Many of their Locals are now employing Afghan nationals through the H2H Program and are supported by their Veteran Liaison, Michael Humphries.
- Canada’s Building Trades Unions (CBTU): is the national voice of over half a million Canadian construction workers – members of 14 international unions who work in more than 60 different trades and occupations. CBTU is committed to representing all workers in the unionized construction industry, building a diverse workforce and ensuring all workers are treated equally.
These organizations are filling critical labour shortages while providing sustainable employment and developing a diverse and inclusive skilled trades workforce. Over the last 18 months, many of the Local Unions of the Carpenters’ Regional Council have provided work opportunities for Afghan refugees and their family members since they arrived in Canada, including Local 27 and Local 675 in the Greater Toronto Area and Local 1946 in London, Ont.
H2H will continue collaborating with Canada’s unions and like-minded organizations to assist additional Afghan nationals in finding and retaining stable careers in the skilled trades.
CZM introduces two new models to their fleet
Recently, CZM announced two new models it is including in its Long Reach series and Ultra Short Mast lineup.
The EK200USM, part of the Ultra Short Mast lineup, is mounted on a Caterpillar 340 Next Generation base with extendable crawlers for 360-degree stability, has an operational weight of 135,000 pounds and a minimum transport weight of 97,000 pounds (without Kelly and counterweight). The EK200USM can be equipped with a self-erecting counterweight for easy set-up and break-down. The operator can lift the counterweight from ground level and install it in place using the hydraulic cylinders installed in the back, eliminating the need for a crane or forklift to set up the machine at the jobsite. This also reduces the operation cost and boosts the contractor’s return on the investment.
This is the only machine of its class that allows contractors to drill under 20 feet of overhead obstructions, up to a depth of 55 feet at a diameter of 10 feet, making it ideal for drilling under transmission lines, bridges and tight overhead areas. With a torque of 193,360-foot pounds, the EK200USM is very productive when drilling in harder soil conditions and rock. The main winch features a special groove for better cable winding and longer cable life. It also comes with two gears allowing for both high speed and high pulling force with a maximum pull force of 63,540 pounds. The robust design of the rotary allows for two groups of hydraulic motors and planetary gears for higher torque and longer life. The rotary head also comes equipped with a high-speed spin off, enabling the operator to discharge soil quickly. Other highlights are the three operation speeds and three spinoff speeds for higher torque. The rotary also comes equipped with automatic gear shifting for seamless operation and has bolted in exchangeable keys, eliminating the need to rebuild the keys by welding on the inside of the rotary.
The EK200USM comes equipped with real time telematics, allowing CZM to monitor and adjust drilling parameters, perform some functions automatically, help with diagnostics, maintenance tracking and remote login to troubleshoot and resolve issues.
The LR40, part of the Long Reach series, is the smallest of the LR series and is mounted on a Caterpillar 317 Next Generation base. It has the lowest overhead clearance, can work under 15 feet of headroom and has a maximum reach of nine feet and five inches. Highlights of this machine include 53,200-foot pounds of rotary torque, a maximum drilling diameter of six feet, a maximum drilling depth of 60 feet, main winch line pull of 27,200 pounds with two gears for high speed and pulling force and an operational weight of 64,000 pounds. The CZM LR40 comes equipped with a robust rotary design and offers three operating speeds and three spin-off speeds for higher torque along with automatic gear shifting for seamless operation and high production. The rotary is also built with exchangeable keys that have been designed to be bolted in, eliminating any need for welding inside the rotary when replacing worn out keys. The LR40 is offered with three optional round interlocking Kelly bars ranging in drilling depths of 35 feet to 60 feet. CZM also offers round friction bars, and like the traditional square friction bars, the round friction bars are great for softer soil conditions and high production jobsites.
This model is extremely light and can be transported in one load, with the Kelly bar. It is also easy to set up, eliminating the need for support equipment, making this model ideal for utility drilling, soundwalls, substations and limited access jobsites. The LR40 also comes equipped with real time telematics.
All CZM models come equipped with a host of next gen drilling features such as touch screen display, auto drill, auto mast level, auto crowd and return to centre.
For more information on any of the other CZM models go to www.czm-us.com.