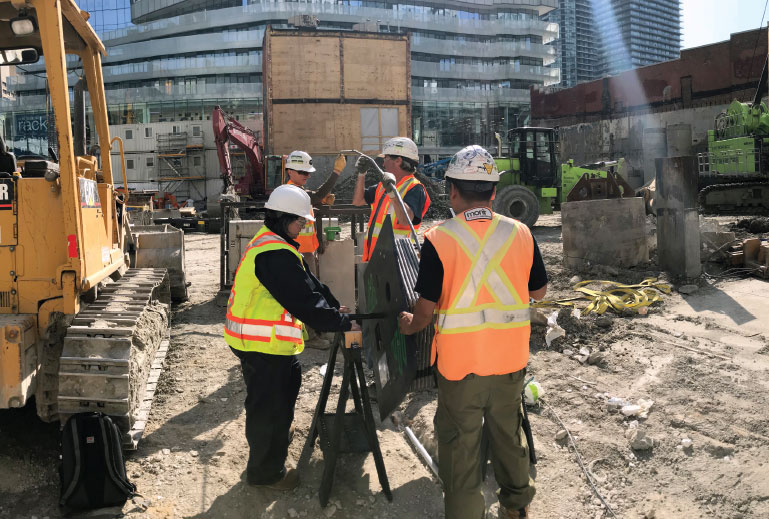
Cutting-edge monitoring system plays a key role in constructing Canada’s tallest high-rise building
When construction of The One condominium and retail development in downtown Toronto wraps up in 2023, it will almost certainly be one of Canada’s most talked about architectural marvels.
At 85 storeys and more than 1,000 feet in height, it will be the tallest high-rise building in Canada. It will also be one of the country’s swankiest addresses. Each of its 416 units, which are expected to sell for between $2 and $24 million, will measure between 1,352 and 6,037 square feet and offer picturesque views as far as Lake Ontario.
Still, as impressive as all that may sound, what may be the most notable aspect of the project is one that most people will never catch a glimpse of. Located on the southwest corner of Bloor and Yonge streets, one of the busiest intersections in Toronto, the site’s small, L-shaped footpad (58 by 47 metres) posed some serious challenges for contractors when it came to excavation and constructing the building’s foundation.
As a result of its small footprint and close proximity to other structures, including a nearby heritage building, a comprehensive monitoring plan was required throughout construction of The One’s foundation to ensure the safety of neighbouring buildings and the almost 100,000 people who pass by the corner on any given day.
Mississauga, Ont.-based Monir Precision Monitoring was brought in by its sister company, Isherwood Geostructural Engineers, the shoring design engineers, and GFL Environmental, the shoring contractor on the project, to implement and oversee monitoring throughout the excavation of the site and construction of the building’s foundation.
Due to the challenges posed in excavating the site – depths of up to 28 feet in some spots and little to no easements for shoring at others – it was quickly determined some form of automated monitoring would be required to ensure any settlements were quickly detected, and to safeguard workers throughout the excavation and foundation construction.
Monir’s team chose to go with the ShapeArray system to complement the extensive monitoring program deployed for this site. The ShapeArray was developed by Fredericton, N.B.-based Measurand. One of the first versions of the system was created for motion capture technology used in live action and animated feature films. It was subsequently adapted for use in urban construction.
Monir general manager Samantha Ford says one of the main reasons the ShapeArray was chosen for the project is the flexibility the system offers. It can be deployed into a variety of different sized casings, from inclinometer casings to small diameter conduit pipe, and is held in place using compression.
The system features a series of stainless-steel sensors that each contain a micro-electro-mechanical system accelerometer and are connected by flexible joints. The accelerometers allow the sensors to measure tilt relative to gravity for the purpose of recording the X, Y and Z coordinates for each segment. Once inserted in the ground, the system is easily wired to a data logging system that can then send detailed real-time information about what’s happening underground via Wi-Fi to its users. Within the data logging system is an onboard drive that records the information in case the connection to the sensor is lost.
“What really struck us was the ease of use, the simplicity of the system and the applications for urban construction,” Ford said.
“It’s delivered on a large reel. Once at site all we need is a flat, safe work surface for us to unreel the instrument into the casing. It’s more or less a plug and play application in terms of the sensor itself. Where the complexity of it comes in is knowing when and where to install the instrument to maximize its value.”
Perhaps the biggest challenge posed by The One’s small footprint was that workers had little ‘elbow room’ when it came to digging or pouring the foundation because of the existing deep foundations from other adjacent buildings and underground utility systems. That was especially problematic on the south and west sides of the site, where they had very limited ability to install tieback systems. As a result, workers had to install 13 rows of tiebacks along an extremely narrow alleyway to transfer the load from the north to the south sections of shoring and limit the deflection of the corner. The design load of nearly 16,500 Kilonewtons (kN) in this particular corner, equates to roughly 22 fully-loaded transport trucks.
The ShapeArray provides real-time data, which was critically important in addressing that unique challenge, and provided an opportunity for a value-added approach, Ford says.
“The beauty of the ShapeArray technology, which is similar to that of inclinometer technology, is the team can be proactive rather than reactive to changes (below grade). It provides near real-time results of subgrade changes and there’s really no other technology in our market at this time that can provide that.
“The team having detailed information of the pile bending and behaviour of the subgrade before excavating, allows for discussion prior to movements becoming an issue that can create delays,” she said.
“In terms of safety that’s paramount since there’s a significant amount of load being retained. If there’s any chance that this building is going to move or the shoring wall is not performing as intended, knowing that in advance gives the team an opportunity to address the means and methods, or to install additional bracing if needed.”
ShapeArray also played a key role in the installation of several foundation elements including numerous large diameter caissons that were drilled into rock to help support the weight of the building. The caissons ranged between four and 11 feet in diameter.
“The program included monitoring as the caissons were being installed because there was a vibratory driver required for portions of the installation,” she said.
“It was unknown if the vibrations would affect the shoring, and if so, how much. So by undertaking readings at different locations around the site as the caisson installations were progressively closer to the walls, we were able to discern the amount of impact on the shoring wall. The 40-metre ShapeArray was pulled from the inclinometer casing at one side of the site using the tower crane and gingerly placed within another casing for us to quickly facilitate monitoring as this work was undertaken.”
The real-time data the ShapeArray provides is also significant in terms of ensuring the safety of the workers underground on a project like The One, Ford says.
“The real-time monitoring plays a significant part [in] the protection of workers inside the site as well as for the surrounding structures,” she said. “Construction is a very dangerous environment. Having access to real-time information can be critical for protecting those workers 30 metres down in an excavation. Their safety is paramount.”
While the inner workings of ShapeArray are fairly complex, the system itself is pretty user-friendly. Measurand and Monir technicians worked closely on preparing for this installation and Measurand provided some preliminary training and was on site at various times during the project. The ShapeArray was so significant to the monitoring that part of Monir’s risk management was to have the technical support of Measurand ready and available if needed at any point during significant activities on site.
“I think it worked exactly as we hoped it would,” Ford said, adding the system has proven to be extremely durable. “We did have redundant monitoring in place including inclinometer casings installed very close to the sensor location so if there were any malfunction with the instrument, if a cable was damaged or there was a question about any movement we saw from the sensor, we could confirm it. Our monitoring programs always provide for redundancy; in construction it’s too risky to rely on only one instrument.”
Robert Praeg, a geotechnical instrumentation specialist with Measurand, says the company is proud to be involved in such a high-profile project.
“ShapeArray has been used in some of the most high-profile projects all over the world. It’s always nice to get a chance to add to that portfolio of projects, especially with a project so close to home with The One. It’s not every day that the largest skyscraper in Canada is built on one of the busiest streets in one of the busiest cities in the country,” he said.
Construction on The One began during the summer of 2017 with Clark Management serving as construction managers for the project. Most of the underground work on the project is expected to wrap up early this year with aboveground construction scheduled to start later this year and continue through to 2023.