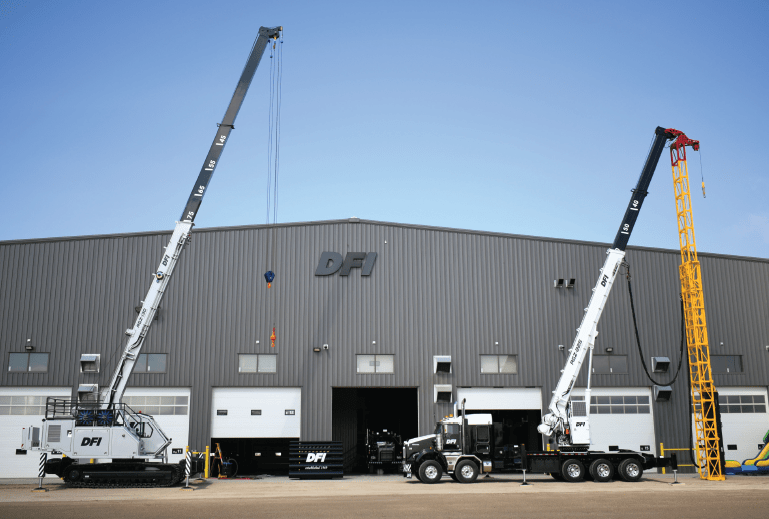
DFI Corporation celebrates 50 years of success
This year marks the 50th anniversary of DFI Corporation (DFI), a multi-national company headquartered in Edmonton, Alta., that has become a leader in the design, manufacturing, supply and installation of steel piling products.
Under the leadership of owner Dave Freeland, a man of vision and determination, DFI has with safety and efficiency, become a “one-stop shop,” able to complete any job from start to finish by providing pile design, pile manufacturing, pipe supply, transportation and installation services. By owning its supply chain, DFI can maintain control over project schedules and costs – a huge benefit to its customers.
How it all began
“In the beginning, Dave Freeland Transport Ltd. was primarily an oilfield trucking service provider,” said Mark Dyck, vice president of operations. “Starting with one truck, Dave continued to grow the business at a moderate pace while expanding into rental equipment.”
Twenty years later, with increasing experience in hauling equipment and materials across Western Canada and into the Northwest Territories, Freeland came across an opportunity to get into the pile driving business and he saw what the future offered.
Wade Thompson, president of DFI, has been with the company for over 22 years and he tells the story this way: “In 1989, we hauled process equipment out to a customer’s location and arrived to find out the pile driving had not been completed. The customer mentioned to Dave that he should get into the pile driving business because there was a need for someone who could provide a reliable service.
“There was limited competition in the piling sector at that time, so DFI shifted focus from transportation to foundation construction and began a rapid expansion over the next few years to meet the demands of its customers.”
Dyck says that early on it became apparent that the equipment available in the piling market was unreliable, inefficient and unable to withstand the rigors of pile driving in harsh Canadian conditions. With innovation being a key strength at DFI, and decades of experience in the field, the solution was to build the equipment in-house. The first RGZ model crane was designed and built in 1993, paired with a DFI purpose-built leader, drop-hammer and follower.
“Dave saw a need in the market and employed people that were capable of providing solutions to initial challenges, and it evolved from there,” said Thompson. “That’s one of the great things about Dave; he has always invested back into the company to further develop our equipment and capabilities. Dave has the vision and desire to not just provide the service, but to also push the boundaries and set the standards for the rest of the industry.”
Equipment made to measure
In the years following, the company’s RGZ line of cranes expanded from truck chassis-mounted units to crawler cranes in 1996, ranging from 35- to 50-ton capacity. This equipment has allowed DFI to take on projects in rough terrain conditions that others simply couldn’t handle.
Today, DFI is still building their own equipment. Thompson notes DFI just completed two new builds; a 50-ton track-crane and a 45-ton truck-mount crane, both equipped with RGZ hydraulic pile driving equipment. The units have been turned over to the operations group for deployment on upcoming installation projects.
Facility operations manager, Chris Whitford has been with DFI for 21 years, starting out as a heavy-duty mechanic, becoming a foreman and working his way up from there. “DFI is very quick to give people opportunities, room to advance,” he said. “Everything is built from scratch. We have our own designers, a welding shop and a CNC machine shop. We paint our equipment on-site in our paint booth and auto body shop. We have a team that completes assembly followed by the automation and control group that program and install of all the PLCs (Programmable Logic Controllers), data logging and touch-screen displays.”
Today, DFI has a fleet of over 30 RGZ cranes, rubber tire and track-mounted, that can be converted into pile driving rigs in 30 minutes. These powerful units are capable of installing driven or helical piles up to 26 metres in length (without splicing), 60 inches in diameter and are agile in hard-to-reach locations while also capable of pile extraction and typical crane services.
In support of these services, DFI also has a fleet of hydrovac units, air and auger drilling rigs, and a fleet of 25 commercial transport trucks as well as DFI-built heavy-haul trailers. Eight blast-hole rigs that can pre-drill up to 18-inch outside diameter (OD), have been modified in-house to be effective pile pre-drilling units. Ancillary field welding services include the cutting and capping of piles as well.
The company also carries a full suite of pile installation equipment, all made in their 75,000 square-foot manufacturing facility in Edmonton and it doesn’t end there.
Whitford adds that DFI also designs and manufactures helical piles, custom pile tip accessories and pile caps. The steel manufacturing facility is equipped with a 60-foot plasma table, sub arc unit, helix presses and multiple automated welding stations. DFI also supplies and installs sheet piles, H-beams, wooden and concrete piles.
“Our in-house design and fabrication capabilities allow us to be responsive to our customers’ needs,” said Whitford. “If a job requires us to modify or upgrade equipment, we have the versatility to do it very quickly by having our engineers collaborate with our operations and manufacturing teams to examine the requirements, create a design, prove it out and provide drawings to the fabrication group to take the concept to reality. Our customers benefit from our abilities to adapt quickly while maintaining high standards of safety, project schedule and cost control.”
Completing the supply chain
“The company’s greatest risk and greatest reward was the design and build of the ERW (Electric Resistance Welding) Pipe Mill,” said Dyck. “With a lack of competitively priced structural pipe in the market combined with a short supply of quality used material, the decision was made to acquire and operate a pipe mill. Having no luck sourcing a quick-change mill that was capable of producing 114.3-millimetre to 406.4-millimetre OD pipe sizes and wall thickness up to 12.7 millimetres, Dave decided to design and manufacture a pipe mill in-house.”
Armed with one mechanical engineer and a team of mechanics and machinists, that’s what they did. Two years later, on Oct. 11, 2000, the first piece of pipe rolled off the assembly line.
Matt O’Donnell, pipe mill manager, has been working for DFI for 18 years. “I’ve been dedicated to improving the efficiency of the pipe mill for the past 12 years,” said O’Donnell. “When we moved to our new 125,000 square foot piling facility in 2015, we added an accumulator that enables us to run our pipe mill without stopping to load a new coil. As a result, we’ve doubled our production output and can easily accommodate
large jobs with minimal change in the pipe mill.
“In the pipe mill we can change from one diameter to another in three hours instead of the normal 24 to 48 hours. We do custom lengths of pipe with changes made on the fly, no stopping, no possibility of defects in welds.”
The DFI pipe mill manufactures 4 ½-inch (114.3 millimetre) to 16-inch (406.4 millimetre) OD piling material with up to half-inch (12.7 millimetre) wall thickness. Custom lengths can go up to 85 feet (26 metres) uninterrupted. Inventory consists of thousands of tons of hot rolled coil and manufactured ASTM A252 piling pipe in all the standard diameters and wall thicknesses.
As Dyck said, “Owning our own supply chain, having the ability to produce high quality material in short order, made to length and with little to no waste, is a tremendous competitive advantage as we can maintain control over project schedules and costs.”
Pulling it all together
In-house engineering and technical teams work collaboratively with customers and field crews to provide complete pile design (driven or helical), survey, material supply, installation, cutting, capping and pile testing services. The DFI team of civil engineers assess geotechnical data and structural requirements to develop a foundation design that can be verified through either static and/or dynamic load-testing programs if needed. DFI has the specialized equipment capable of performing load-testing on-site and quality control checks on piles when installed.
The DFI survey division uses Topcon technology for rugged terrain and can provide industrial survey from initial layout to pile cap setup, final as-builts and commissioning, including information planning, mapping and risk assessment.
It all comes down to the people
Currently DFI has 309 employees coming from 10 different trades, as well as others with professional designations in accounting, engineering and human resources, and this year DFI partnered with Women Building Futures to take part in their apprenticeship program.
“I’m proud of the fact that 104 of our employees have been with DFI between five and 10 years,” said Thompson. “Twenty-three between 10 and 15 years; nine between 15 and 20 years; seven between 20 and 25 years, while our longest employee has been here for 34 years.”
Mark Dyck began his career with DFI as a piling operator on a truck-mounted crane, gaining experience and training over the years before transitioning into his current role. “DFI has been built on empowering employees, recognizing and rewarding talent and promotion from within. We invest heavily in training, mentoring and preparing employees for their current and future roles at DFI.”
DFI holds zero compromise towards safety and is driven to continuously improve its safety performance, and as such has recently achieved the Gold Shovel Standard Certification for Ground Disturbance activities.
Dave Freeland is still the sole owner of DFI, remaining an active and integral part of the business. “He is on the shop floor every day, looking to continuously improve,” said Whitford. “We have a lot of support to take on new endeavours or to upgrade our equipment, make something a little bit faster, a little bit stronger, a little bit safer. I don’t have to talk to a board of directors, I don’t have to keep shareholders happy, I have to keep one guy happy who truly understands the business.”
The business has come a long way from the one-truck operation 50 years ago, now with seven Western Canadian branches in addition to its head office. As an entity of DFI, Montana Resource Services is based out of Missoula, Mont., servicing the west and midwest regions of the U.S., while DFI Energy Services has been operating successfully out of Brisbane, Australia, since 2016.
“As we continue to grow, and as opportunities present themselves, DFI will strategically expand its reach into new markets and geographical areas,” said Dyck. “With a continued focus on our core business – piling – we will invest in people, equipment and products to better serve our current and future customers.”
Thompson believes, as does the founder of DFI, that people are DFI’s greatest strength, and collectively they are always looking for ways to improve the final product. “The recipe for success is operational excellence, innovation and technology, and we try to employ all three elements in everything we do.”
From day one, DFI’s focus and vision have been on delivering responsive, innovative and reliable service wherever customers need them. This remains as true today, 50 years later, as it was in 1969.