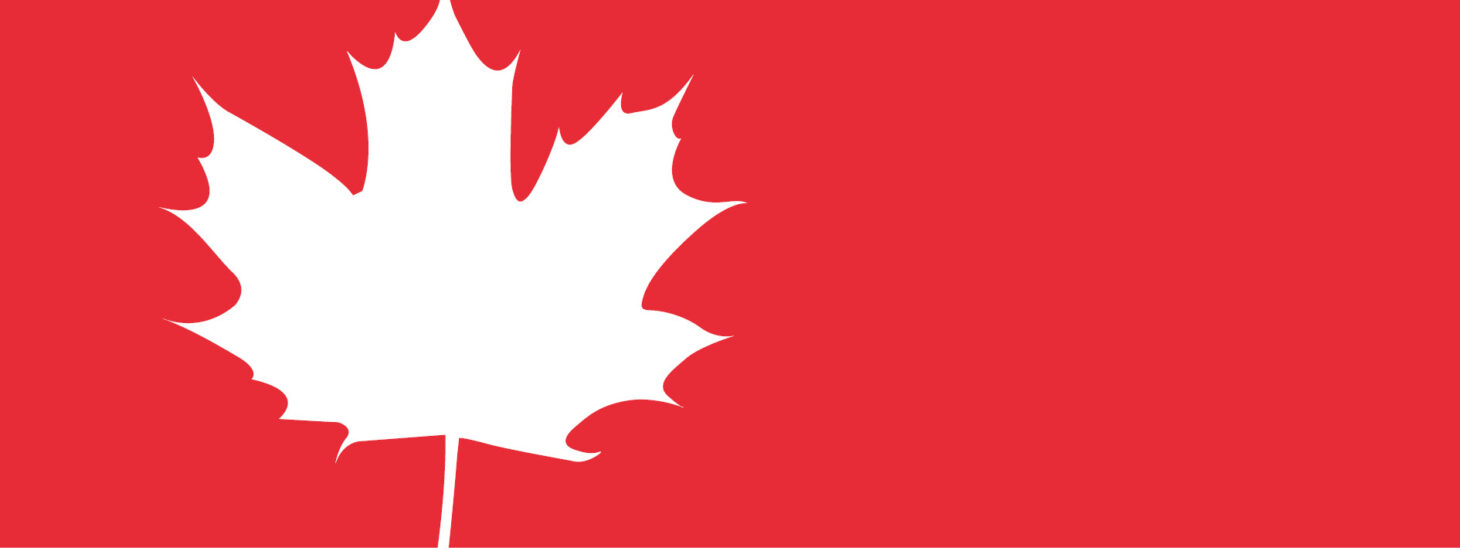
Design-build and remote PDA testing
Sharpening the proverbial pencil
It’s a familiar saying, and in an engineering office it may sound like this: “Four per cent overstress … maybe I can sharpen the pencil and make it work.”
Despite the fact that a given balance between load and resistance cannot be “made to work,” there is some insight that this euphemism provides. In reality, deeper understanding of a problem is being sought with the intent of removing uncertainty. As engineers, we are inherently and appropriately risk averse. If we have not personally proven or maintained control of an idea from inception to completion, we become skeptical of it. In practice, this tends result in unnecessary conservatism, particularly where often-disconnected design professionals have tangential or overlapping responsibility. Such is the case with driven piles.
Much of the excessive conservatism that persists in the driven pile industry can be reduced significantly through a design method that treats the pile foundation as a performance specified component. Utilizing bid solicitations, which include pile design criteria and subsurface reports, foundation contractors, along with a driven-pile specialty engineer, can provide design-build solutions with pricing and schedule to be evaluated for best value. Further, by incorporating remote dynamic pile testing within the scope of the design-build team, the most optimized foundation and installation schedule can be achieved. If the pile specialty engineer and contractor team are engaged from concept through design and certification, the pencil is always sharp with respect to foundation design.
Traditional design method
Consider the traditional method of foundation design by an engineer of record (EOR). The design process varies somewhat, but typically begins with engaging a geotechnical engineer for reporting on subsurface conditions. Foundation recommendations are typically included in a report that also advises on site preparation, paving, slab system requirements and seismic risk assessment. Further, the foundation recommendations are often limited to relatively few options and based on minimal information regarding the structure. This is somewhat reasonable since the geotechnical investigation often proceeds the completion of any substantive structural design, which could advise a more targeted approach. As a preliminary assessment to be used in future collaboration between engineering disciplines, this information may be adequate. However, all too often the scope of geotechnical work is complete (test pile and field monitoring not withstanding) upon issuing the initial subsurface report, leaving what would be a good initial step in developing an efficient foundation solution as final options for selection by the EOR. From the initial subsurface report, a single pile type is proportioned to provide a safe design, with the knowledge that field-testing will substantiate the geotechnical analysis. The result is often a pile foundation proposed by the geotechnical engineer, without substantive input by the structural engineer, and then specified by a structural engineer without additional geotechnical input. The expectation of this process resulting in the most economical solution is unrealistic.
The traditional model lacks attention of specialized knowledge at critical points in the process, which creates uncertainty and often leads to unnecessary conservatism from the geotechnical and structural engineers. To illustrate why, consider how the geotechnical report is used. Typically, design recommendations are taken as safe design values without consideration of soil borings or laboratory tests, which are far more useful in establishing an optimized pile design. These recommendations are the geotechnical engineer’s method of simplifying the complexity of soil-pile interaction for the sake of providing an EOR with an easily understandable design model. Adequate design is normally the result due to conservative principles used to develop a very simple soil strength model. However, the most efficient solution is rarely attained through strict adherence to these design recommendations. Optimizing the pile type and length requires depth of understanding of the geotechnical report by the EOR. In the exceptional circumstance where the EOR has a sophisticated understanding of the reported geotechnical data, uncertainty can persist with respect to installation methods, control of field-testing schedule and the ability to make adjustments to design during production pile driving. Consequently there is a high probability that the traditional method will either result in larger, longer piles than are necessary, or an expanding construction schedule necessary to coordinate the interaction of three to four separate entities.
Design-build
It seems logical that removing uncertainty inherent in the traditional design model results in substantial improvement to the efficiency of pile foundations. But how can this be done in a systematic way, such that the results are repeatable? Several years ago, Ryan Structural Engineers, LLC (RSE) and Force Pile Driving, Inc. (FPD) believed that the answer was the design-build model. At that time, RSE had become an established driven-pile specialty design firm, focused on combining efforts related to structural and geotechnical aspects of pile design. FPD was an aggressive and rapidly growing pile-driving company interested in providing Western Canada with value-added services. Recognizing a special opportunity in one of the world’s most prolific construction markets, a natural partnership formed.
{fastsocialshare}
Through a series of projects that started small and gradually increased in size, a simple set of steps has become the basis for providing optimized pile design. For any given project, RSE provides a design concept based on pile loading requirements provided by the EOR and the geotechnical subsurface report. Through collaboration with FPD, a pile foundation is customized based on material and equipment availability, site assessment, and schedule. A price, typically lump-sum, for a turn-key pile foundation is provided to the client, which includes engineering, shop drawings, pile installation, PDA testing and certification. Upon project award, pile design is completed with final foundation requirements incorporated. Test piles are installed and tested. Utilizing remote PDA monitoring, capacity can be determined within hours of testing. This allows for optimized standard length piles to be ordered and delivered as quickly as 24 hours subsequent to testing. Production piles are installed with continuous pile monitoring. With the design specialty engineer on call during production, unforeseen driving conditions are reported and resolved immediately. Upon completion, a stamped and signed Schedule C is issued, indicating that the piles were installed in compliance with the design per the Alberta Building Code. As a result, the following advantages are realized, eliminating uncertainty and maximizing efficiency:
- Geotechnical and structural aspects of pile design becomes an integral part of the bid process, substantially reducing the uncertainty inherent in deciphering construction documents by the contractor.
- RSE brings the capability of establishing design from soil borings and laboratory testing, rather than relying on design recommendations alone, eliminating uncertainty of the geotechnical and structural engineers interpreting one another’s intent.
- Precise knowledge capabilities and limitations of equipment become part of the design process, allowing the engineer greater control of proposed installation methods.
- Awareness of real-time availability of standard material and surplus material, including market pricing, becomes a part of design.
- The specifying engineer responsible for the pile certification maintains focus on the project at the time of production pile driving. Direct decision-making authority by an accountable design professional in direct contact with the piling crew diminishes delays due to project team interaction.
Remote PDA testing
High-strain dynamic pile load testing, commonly referred to as PDA testing, is an indispensible design tool for the optimization of driven-pile foundations. Through PDA testing, an abundance of useful information – including driving stresses, pile capacity at intervals along the pile length, hammer efficiency and damage assessment – can be determined. The development of dynamic testing equipment has progressed since the time of its inception in the early 1970s. Current instruments and field processing computers are more portable, reliable and durable as processor technology and software improvements have been made. Among the most exciting advancements is the ability of engineers to remotely connect to these computers in the field from anywhere in the world, monitor driving as if they were in the field and download data for expedited signal matching (CAPWAP) analysis. Although there are many good reasons to employ remote testing, substantial improvement to the project schedule remains the primary impetus. Consider the following advantages created by sending testing equipment into the field with technicians trained to operate the testing equipment and connecting remotely to engineers:
- CAPWAP analysis, required for compliance with ASTM 4945, can begin immediately upon data collection.
- The engineer can focus on data quality, leaving the field technician to focus on proper instrument set-up, field measurements and management of site personnel. This allows the engineer the opportunity to manage the overall testing program in real-time, without being subject to the stresses of being on site. When piling and testing is proceeding well, the advantages are marginal. However, when unforeseen conditions are present, the advantage of measured reflection in a controlled environment can be very beneficial.
- The engineers’ schedule is not impacted by travel. In an area as large as Western Canada, mobilization can take 16 hours or more in good weather conditions. With remote monitoring, engineers can concentrate on analyzing data, optimizing design and responding to unforeseen conditions rather than transporting equipment. This creates a more efficient design operation without sacrificing best practices.
- The experience of exceptionally qualified engineers is available to any site in the world, irrespective of the engineer’s physical location. In fact, remote testing has allowed RSE to engage some of the foremost dynamic testing experts in the U.S. through a partnership with Terracon Consulting Engineers. With an exceptionally experienced knowledge base, Terracon has been instrumental in developing our remote testing program.
Results
Through the utilization of the design-build model and remote PDA testing as described above, Ryan Structural Engineers, LLC and Force Pile Driving, Inc. have been successful in bringing best engineering and pile driving practices to bear in the Western Canadian construction market. By servicing projects of all types sizes, ranging from four-pile communication towers to an 8,000-pile SAGD facility, the process has been demonstrated as effectively scalable. The design-build model combines specialized engineering knowledge with best-practice piling methods for the purpose of systematically removing uncertainty from the design and installation process. Remote PDA testing provides for efficiently engaging the most qualified testing expertise on site for all projects. Combining the two creates an effective method for optimizing driven-pile lengths and sizes, while minimizing the piling schedule. It follows that these methods will continue to make driven piles a preferred deep foundation solution in Western Canada.
{fastsocialshare}