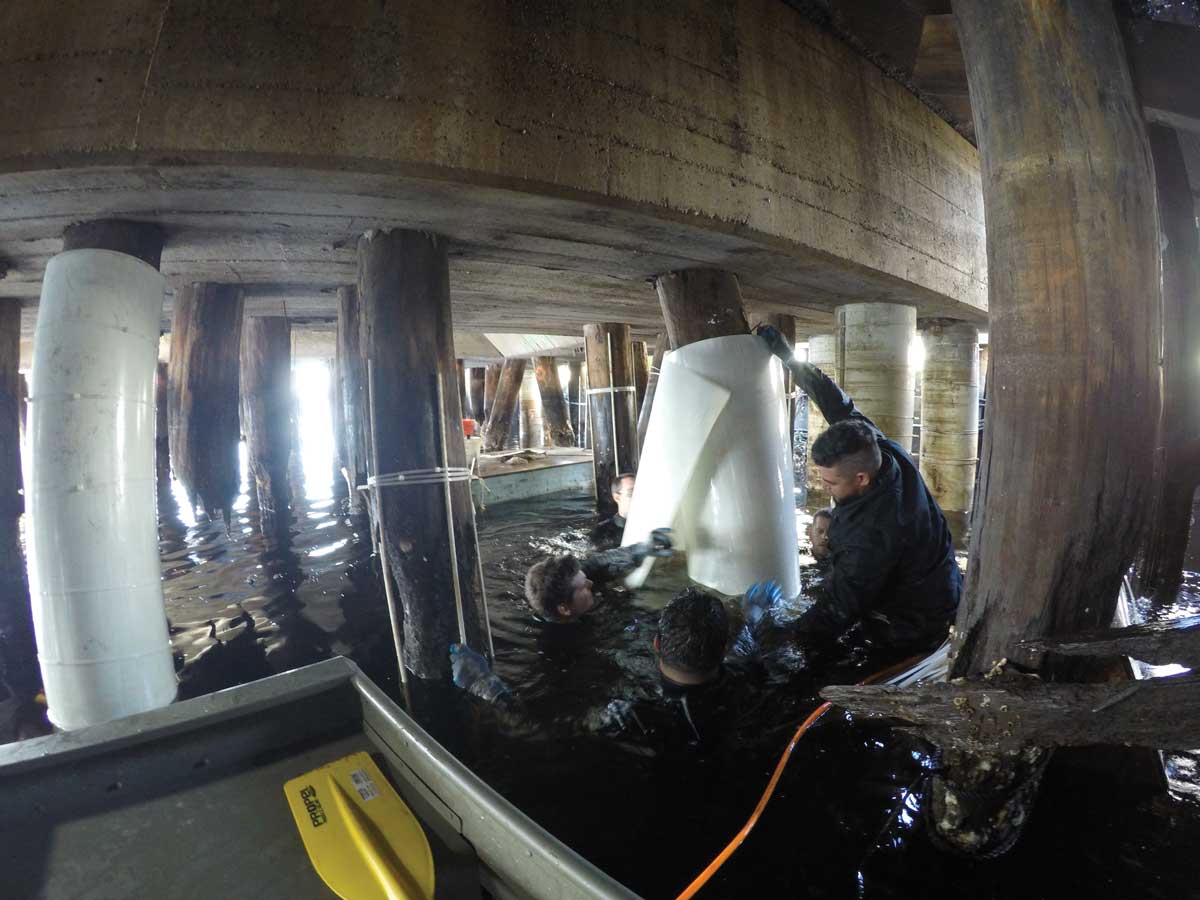
Piles face a lot of challenges during their life cycle. Structural supports deteriorate over time. This deterioration happens faster when supports are placed in seawater or exposed to corrosive materials such as road salt. Just think back to Toronto’s Gardiner Expressway.
The roadway’s crumbling underside stands out as a prime example of what snow de-icing chemicals can do to infrastructure. Fortunately, help is at hand with products such as PileMedic.
PileMedic is made by the people who invented QuakeWrap, an innovative Fibre Reinforced Polymer (FRP) product developed in the late 1980s by University of Arizona Civil Engineering professor Mohammad (Mo) Ehsani, Ph.D. QuakeWrap offers the ability to make piles and columns earthquake-resistant and changes the standard repair protocols. The company followed this innovation with PileMedic in 2008. “This FRP product is primarily for repair of submerged piles and foundations,” said Ehsani, president and CEO of QuakeWrap.
While PileMedic is excellent for strengthening utility poles and cellphone towers, Ehsani says it is also useful to increase the strength of columns in buildings where additional loads are applied, or if the columns are deemed weak due to construction errors. According to Ehsani, the pile repair system is the fastest and most economical method for strengthening columns, underwater piles, utility poles and bridge piling with little disruption of service. He adds that with PileMedic, contractors don’t have to repair and smooth the pile surface before installation of the FRP membrane. “PileMedic is very forgiving and easy to install,” he said.
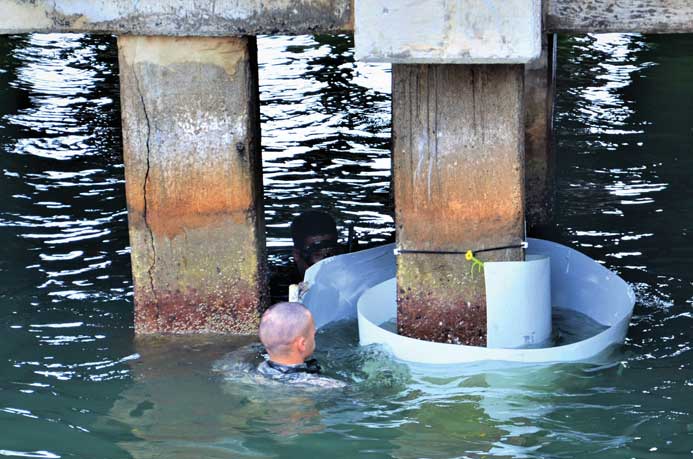
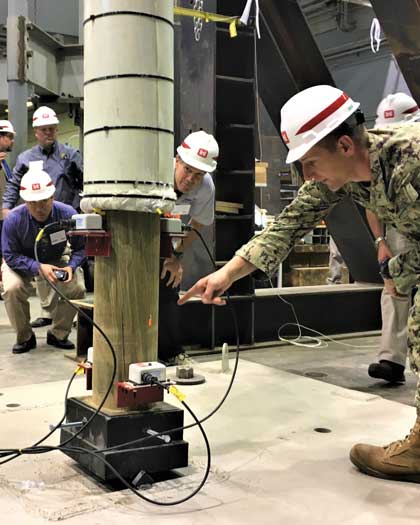
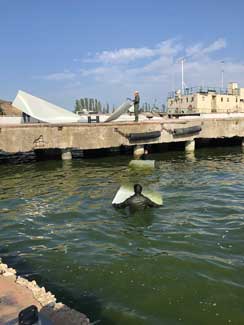
In the past, pile repair involved complicated processes to seal cracks and strengthen underwater supports. With PileMedic, repair time is reduced. This means less cost for contractors. “With PileMedic, a single diver can install the product over six or eight spacer bars and then zip-tie the membrane to the pile before moving on to the next section. Pieces can be slid down the column and can overlap to create a strong, tight seal.”
PileMedic laminates come in 4-foot-wide rolls, in addition to complete kits that offer everything required to undertake a pile repair. Contractors cut the laminate to the desired length and apply a two-part epoxy to the sheets. The laminate is then wrapped around the pile to create a two-ply shell of any desired size. The annular space between the shell and the pile is filled with epoxy grout or cementitious grout.
From a structural point of view, PileMedic jackets offer a uniform “confining pressure” that extends 360 degrees around the pile. “This confining pressure results in significant additional strength for the original pile and the newly placed grout. Thus, a pile of the same cross-section dimension becomes much stronger if it is wrapped with PileMedic compared to other conventional fibreglass jackets.
“Workers in the field can create a jacket of any size. This is a major product advantage that saves time and money on projects,” said Ehsani. “This feature is also one of the main reasons why the United States military has selected PileMedic as the only solution for its use globally.”
U.S. sailors assigned to Naval Construction Battalion 133, the ‘Runnin’ Roos’ from Gulfport, Miss., recently completed an overhaul project on the main naval pier in Ochakiv, Ukraine. The project saw a team of 13 sailors complete the repair ahead of schedule.
PileMedic laminates come in 4-foot-wide rolls, in addition to complete kits that offer everything required to undertake a pile repair.
“This project was designed to significantly increase the lifespan of the pier,” said builder chief Craig Claudio, Leading Chief Petty Officer for Construction Dive Detachment Bravo, Underwater Construction Team (UCT) ONE. “The project required repair of 12 concrete mats resting on concrete or timber piles located in soft, unstable ground. This repair was essential to provide a suitable, stable foundation to the pier.”
Claudio says that the pier work came after an exhaustive study of the PileMedic capability. “We spent three years experimenting with this technology in the U.S. Indo-Pacific Command,” said Claudio. “Multiple mixed detachments from both UCT ONE and TWO have participated in a number of exercises designed to test this technology in a time-constrained manner for contingency operations, and the technology has proven how it can enhance fleet logistics from sea to shore and shore to sea.”
Practice makes perfect, and the U.S. engineering team in Ukraine was able to get the job done more easily than with other pile repair products and finished weeks ahead of schedule.
“PileMedic is much simpler to install compared to other jackets available in the market,” said Ehsani, mentioning that QuakeWrap offers a training/certification course to contractors who wish to install PileMedic. “This is a two-day course that includes classroom/lecture-type presentation, plus hands-on installation of the product in our construction yard.”
Ehsani says PileMedic is the only jacket that does not require prior measurement and order to a specific size. “This not only reduces time and cost, but it also eliminates delays due to incorrectly sized jackets being delivered to the jobsite,” he said, remarking further that PileMedic’s unique features eliminate any seams along the height of the pile. “Seams allow moisture and oxygen to pass through the jacket and reach the pile, allowing the corrosion process to continue.”
As an example of how forgiving PileMedic can be, Ehsani describes a recent job at Perdue Agriculture’s pier in Virginia. “Engineers were told piles were 12-inches in diameter. On-site, crews discovered that many piles were 14-inches in diameter. This discovery meant greater lengths of fibreglass reinforced sheet material [were] required to complete the job. The nature of PileMedic allowed crews to make the jackets to specifications [found] on the site. As a result, the project challenge was easily mitigated and no time was lost.”
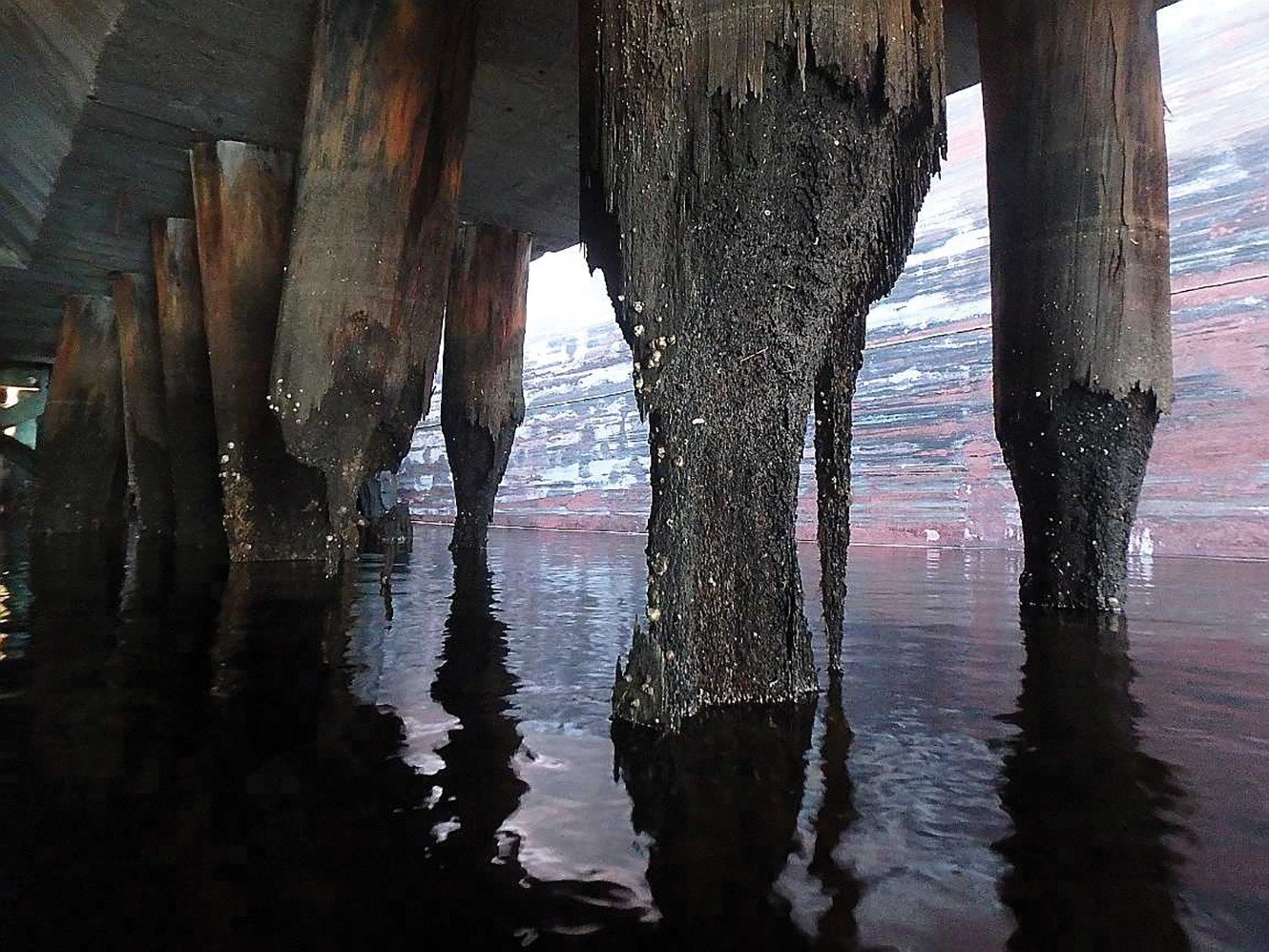
Ehsani says that with conventional pile jackets that are ordered and constructed in a factory and delivered to the jobsite, those on-site sizing changes could not be accommodated; a 12-inch diameter factory-made jacket would not fit around a 14-inch diameter pile.
“Since PileMedic jackets are made in the field, one could easily cut a longer length of laminate (from the long rolls) and create a tube of any diameter such as 12-inch, 14-inch or 18-inch. The flexibility of the thin laminates even allows them to be made into non-circular shapes for the repair of square or rectangular shaped piles.”
PileMedic is safe to use with precautions similar to those of other pile repair jackets. Ehsani says that workers must be protected and trained in mixing and applying the epoxy. As well, underwater installation must be performed by certified divers.
Ehsani says that the product has undergone rigorous testing from government agencies in Canada and the United States. “PileMedic is the most highly-vetted product for the proposed applications,” he said, adding that the amount of government testing on this innovative FRP product is something that helps ease the minds of engineers and contractors undertaking pile repair jobs. “Our products are in use around the world and have shown that they can handle the toughest environments. They also reduce costs for contractors,” said Ehsani, inviting industry professionals to discover how simple pile repair can be.
Visit www.pilemedic.com for more information.