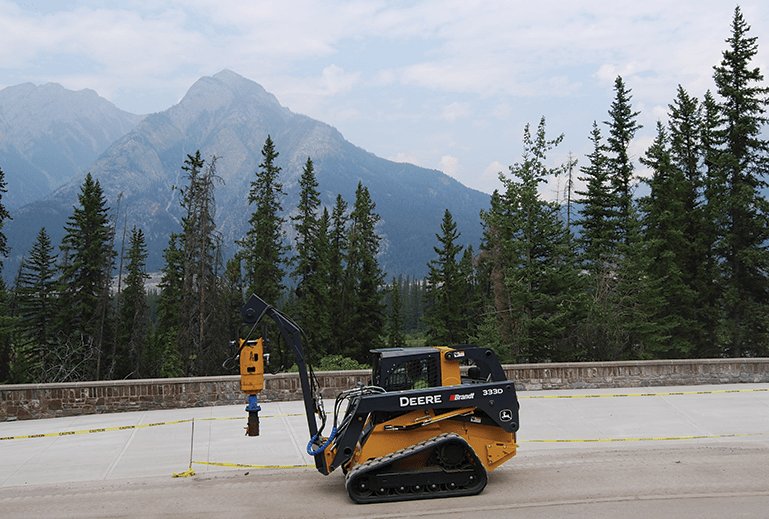
Working in the piling industry, a company can be faced with a number of projects that are unique. While each job has its own dynamics, there are some that stand out as being different from the “norm” that one might see in a downtown Canadian city or in rural centres across our country.
Such was the case for Calgary-based Cyntech Canada. Founded in 1981, Cyntech has grown to be one of the premier companies in North America not only for piling projects, but also pipelining and tank services. Recently, they were called upon to be part of one of the most demanding jobs a piling company could face – working in a national park.
The project, as Cyntech project manager Joe Roper says, was in the Cave and Basin in Banff National Park. Located on Sulphur Mountain, the area is one of the hot springs in Banff, originally discovered in 1883 by CP Rail workers. The road to it becoming national open property itself is unique.
“It was a dispute over ownership back then that caused the issues,” said Roper. “It was decided that no one should own it and it should be made a reservation and protected park.”
Just a couple years after its discovery, the land was developed with hot springs feeding into pools, which remained open until 1992. The new work being done came to the tune of $13.8 million, which included historic stone restoration and creating an interactive museum that retells the story of the development of Parks Canada. This is where Cyntech’s expertise was called in.
“We designed and installed small diameter helical piles to support the second-story promenade, which is now home to interactive displays, new change rooms and washrooms for the pools,” said Roper. The equipment being used had to be pristine – as new as possible, clean and well maintained – just part of a large number of environmental specifications that were dictated for the project overall. A John Deere 333 skid steer was used to install the helical piles
Challenges
Because Cave and Basin has been in existence for decades, a potential hurdle to overcome in breaking new ground within a protected park was not a concern, but there indeed were issues that needed to be taken into consideration, especially around piles. As Roper says, one animal dwelling in the hot springs meant that a different strategy had to be used in the project work than what one would normally see at a job site.
“There’s an endangered species called the Banff Springs snail that resides in the hot pools, and that’s where our restrictions were – protecting the snail and ensuring that any work being done on site didn’t have any changes to the temperature, turbidity or chemical composition of the water,” said Roper. “The big one for us was vibration. They originally called for traditional driven piles, but they weren’t able to cause any significant vibration or high impact to the ground.”
It was at this point that Hurst Construction Management, the lead company on the project, reached out to Cyntech. Their rig options weren’t suitable for being able to work without creating a disturbance that would impact the snail. Cyntech’s solution, thus, was to redesign and use helical piles instead.
“We could get in there with small materials and small equipment, and install without any wasted energy propagated through the soils, which you have when dropping hammers on driven piles or even with drilling holes,” said Roper. “The benefit of the helical pile is that it’s a displacement pile, which is rotated into the ground with a controlled amount of torque, which correlates to verify soil conditions and installed capacity, so there’s no wasted energy that goes into the soils to disrupt anything, be it the snails or sensitive instrumentation from refineries.”
Herein, however, lay a second challenge. The equipment being used had to be pristine – as new as possible, clean and well maintained – just part of a large number of environmental specifications that were dictated for the project overall. Failure to adhere by the specifications, Roper was told, could have resulted in penalties as high as jail time (per the National Parks Act). Base Pile & Anchor had supplied the crew and equipment that installed the piles, and they showed up ready to work and in immaculate condition.
The project also had issues that needed to be handled at the job site. First came locating the previously existing piles, which was accomplished by working with the assigned structural engineers, Read Jones Christoffersen Consulting Engineers. Once this was determined, there were procedural issues.
“We couldn’t just lay them out like we typically would want to,” said Roper. “There were certain areas of the ground that had moving groundwater table, where we couldn’t impede the flow.”
Historically, Roper says, there had been issues in this respect. He notes that piles installed previously had re-routed hot spring water area into a bog area, leading to cross-contamination. Thus, this time around, Hurst and Cyntech, together with Read Jones Christofferson, had to be very careful with pile placement from the environmental impact perspective, along with also keeping a close eye on capacities of each pile for structural considerations. Additionally, attempts were made to remove piles that were soaked in creosete, which is considered a toxic tar, and the contaminated surrounding soil, which were then taken to Brooks, Alta. for disposal, at a considerable cost. The more contaminated soils removed, the more expensive the project became, which was an indirect saving helical piles provided through their sensitive and spoil-free installation technique.
In the end, the piling project went off without a hitch, as all challenges were met with professionalism and with a concerted effort from all parties, including Cyntech. Still, working in the area did provide Roper with a closing thought as to just how far the piling industry had come.
“We were provided with technical reports dating back to the 1960s and 1980s,” he said. “It was quite interesting to see the evolution of our science.”
Equipment |
Installation – John Deere 333 Skid Steer |
Piles – 25 piles, 5.5″ OD shafts, 25 ft. total length |
Material – Hot-dip galvanized (to combat sulphate content) |