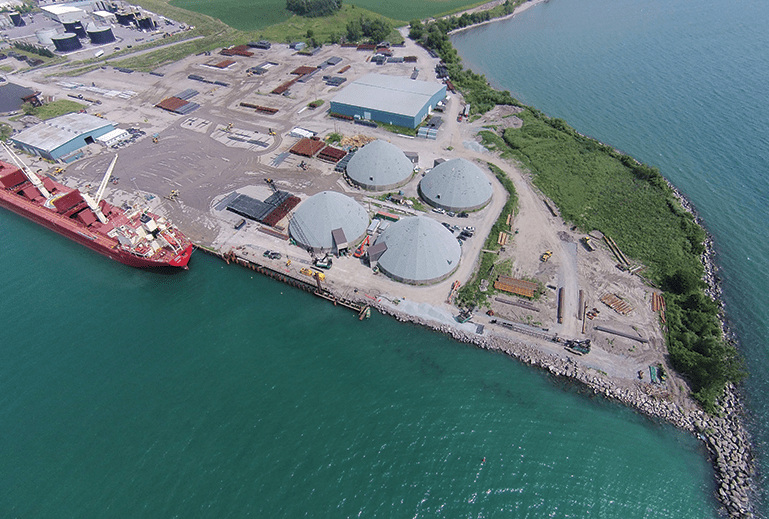
Allowing the port to handle more cargo, create new business opportunities and jobs
By Lisa Kopochinski
After several years of extensive revitalization, the Port of Oshawa is maintaining its spot as the city’s shining star.
Work has completed on the east wharf consolidation and rail spur projects – both which will provide an additional berth for ships and allow the port to handle more cargo, create new business opportunities and jobs.
“The Port of Oshawa is really coming into its own,” said Donna Taylor, CEO of the Oshawa Port Authority (OPA). “The wharf and rail spur were constructed concurrently – but were completely separate projects. While they will ultimately complement each other, they are stand-alone projects.”
In 2014, OPA managed more than $9 million in operating and capital expenditures, with the rail spur and east wharf consolidation project among the largest capital expenditures. This past year of growth and expansion has benefited port workers, resulting in more permanent full-time hours for crews who are handling rising cargo volumes.
Annually, the Port of Oshawa handles $23 million worth of cargo – from salt and steel products to asphalt and grain. The port’s movement of cargo supports nearly 300 jobs and raises $6 million in federal and provincial taxes.
Since the opening of this year’s shipping season in April, bulk cargo volumes through the port have increased by an unprecedented 93 per cent over the same timeframe last year.
Mid-construction
“Work on the east wharf was completed In early August 2015 with a four-month winter shut-down period. All scheduled milestones have been successfully achieved. in fact, work was completed five months prior to the final milestone deadline.”
– Mark Reinders, EIT, Bermingham Foundation Solutions
Relocation of industrial uses
It was in 2010 that the City of Oshawa, Transport Canada and OPA came to an agreement to relocate the heavy industrial uses of the west wharf of the port to the east wharf.
This would consolidate existing operations on the east side, but require a significant upgrade to the east dock face. W.F. Baird & Associates produced the final port design, and OPA gave award of the contract to Hamilton-based Bermingham Foundation Solutions in late May 2014.
Bermingham began work on the $7.4 million east wharf project in June 2014 (the company was not involved in the rail spur project).
“Work on the east wharf was completed in early August 2015 with a four-month winter shut-down period,” said Mark Reinders, EIT of Bermingham. “All scheduled milestones have been successfully achieved. In fact, work was completed five months prior to the final milestone deadline.”
Bermingham acted as general contractor and completed the excavation, grading, combi-wall installation, tieback installation and placement of marine materials. The following points provide the scope of pile driving work this project entailed.
- Removal and relocation of nearly a football field worth of armour stone – some nearly the size of a compact car.
- Excavation and clearing the driving line for the combi-wall with an overall length of 226 metres.
- Accurately driving 98 piles of 1.1 metre diameter, up to 18 metres long down to rock. Lace sheets of equal length between each pile.
- Drilling out the overburden within the piles, then proceeding to drill a three-metre rock socket.
- Air lifted and tremie placed concrete within the piles.
- Drilled 79 tiebacks, 31 metres long off a barge, through the pile. Each tieback was a 14-strand DCP anchor.
- Backfilled, graded and compacted material behind the completed wall.
“Toronto Zenith was our primary subcontractor, forming and pouring the concrete cap beam and parapet wall,” Reinders added. “They completed an excellent job and adapted well to the varying water conditions.”
Rock Socketing
Pile driving challenges
As for challenges the Bermingham team faced, Reinders says installation tolerances were tough to maintain with a combi-wall.
“To control the placement of the wall, a template was built to facilitate the installation of nine piles and seven sheets. The crew quickly became familiar with the process and was able to install all piles, sheets and even relocate the template within a week. This process resulted in the last pile along the wall being only 0.11 metres over the course of 204 metres!”
The project was visible to the general public and frequently harboured vessels with an eight-metre draft. This required drilling operations to be contained to avoid silt suspended in the water and sediment moving into the channel. While drilling the rock sockets, this containment was done through reverse circulation.
“Water was pumped into the pile from the outside, while air was pumped through the drill-string to the base of the rotary bit,” Reinders explained. “This pressurized the bottom of the pile, causing water, air and cuttings to flow up through a cavity in the drill-string and out through a discharge hose. The hose directed the cuttings to the landside of the combi-wall where they were later excavated and disposed.”
Drilling tiebacks proved to be a big challenge as well. The tiebacks were 24 metres of overburden and then a six-metre rock socket, and had to be drilled on a 42-degree angle towards the land.
“This required the tieback rig to be placed on a barge and drill the tiebacks off water,” said Reinders. “The barge used gravity spuds to help anchor it in place, but it was still buffeted by waves. With ideal conditions, we achieved four tiebacks drilled and placed within a 10-hour day.”
The pile driving equipment used on this project included the following:
- 165-ton crane with an HPSI 500 to drive the majority of the combi-wall.
- 110-ton crane was fitted with an extended crane-mounted vertical drill to remove the overburden from within the piles.
- 165-ton crane was fitted with one of Bermingham’s customized rock drilling systems. This system included 30 metres of L27 vertical travel leads (VTL); HHH-16 spotter; a lead mount hydraulic crowd; and a BHD-80 reverse circulation drill. This drill turned 21 metres of 460-millimetre drill string with a 20-millimetre rotary drill bit. All of this equipment was produced in-house by Bermingham’s manufacturing division.
- A tieback rig drilled the anchors off of a gravity spud barge and was serviced by a 165 crane.
- Several companies provided the equipment and materials used in this project.
- Skyline Steel provided all of the piling, which included:
- 98 pipe piles, 1.1 metre in diameter, ranging between up to 18 metres long. Skyline also provided the sheet pile connectors that Bermingham’s manufacturing division welded to all 98 piles.
- 79 pairs of AZ14-770 sheets that laced between the piles.
- 13 pairs of AZ46-700N sheets that were used as a deadman wall to support the end of the combi-wall.
- 107 metres of 53-millimetre threaded bar to span between the deadman wall and the end of the combi-wall.
- ConTech Systems provided all of the tieback material. This included:
- 80 anchors, 14 strands each, 33 metres in length. The top 27 metres was double-corrosion protected.
- Bearing plates, cover caps and grease.
Anchor Rebar provided the rebar cages that tie the piles into the concrete cap.
OPA’s Taylor added that the Port of Oshawa will now be truly intermodal and able to move cargo of all sizes year round.
“The port will see greater productivity and time and cost savings since manpower and equipment will not need to be split between two sides of the harbour. This will be beneficial to port customers by minimizing labour downtown and wear and tear on equipment. That’s a huge advantage.”