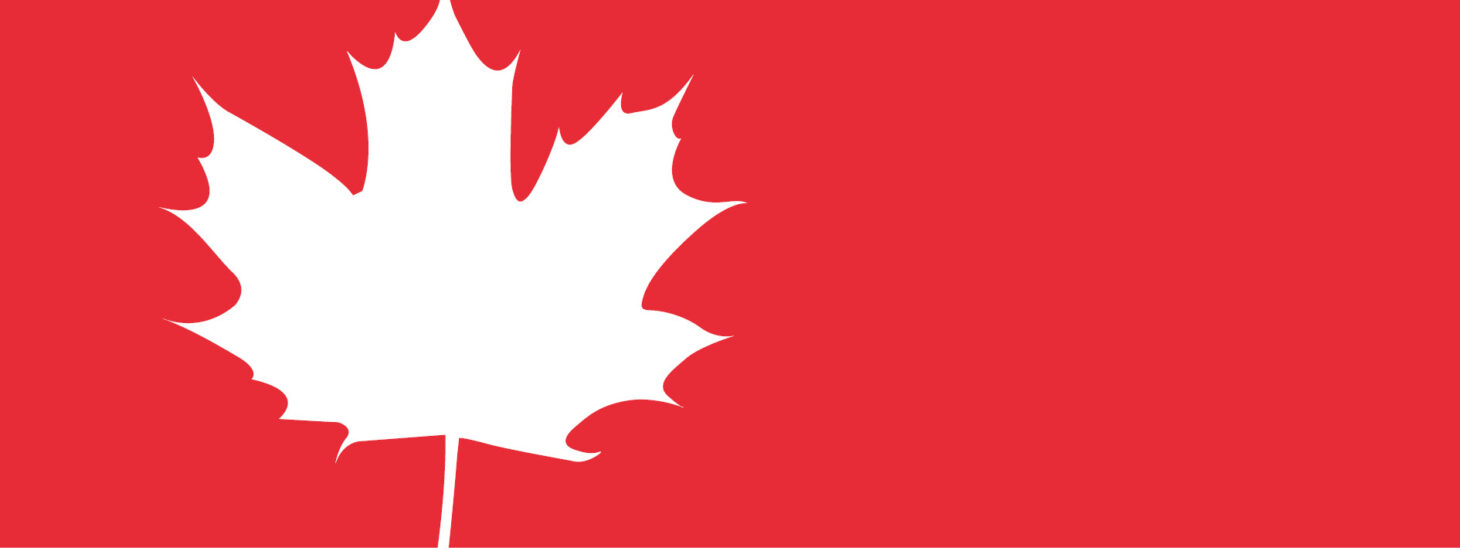
Crux Subsurface, Inc. (Crux), a Quanta Services company headquartered in Spokane Valley, Wash., is a specialty geotechnical drilling contractor providing geotechnical exploration, geotechnical construction and design-build foundation solutions in North America. Crux specializes in logistically challenging and environmentally sensitive projects where access and subsurface conditions present difficulties.
Crux was founded in 1998 with a focus on geotechnical exploration and engineering design support through geotechnical data acquisition. The founders were already experienced geotechnical drillers and fabricators, and chose the name “Crux” (“an essential point requiring resolution or resolving an outcome”) to emphasize their mission and their strength – solving difficult logistical problems.
A history of problem-solving
When Crux first began installing micropiles in 2002, the company was already known for providing difficult-access geotechnical exploration services throughout the western United States for tunnel, dam, highway and slope stabilization projects, including the Hoover Dam Bypass. Crux initially utilized micropiles for structure foundation support and slope stabilization before adapting the technology as a foundation alternative in the electrical transmission market. Micropiles provide the ability to install a high capacity deep foundation system in remote or environmentally sensitive locations, says Scott Tunison, Crux’s vice president of operations.
“Micropiles are replacement piles constructed using high-strength grout and steel, and can be installed using lightweight equipment,” he explained.
In 2004, Crux began construction on the 57-mile-long Swan Lake-Lake Tyee Intertie between two hydroelectric projects in Southeast Alaska. This was the first project of its magnitude to use helicopter-supported micropile foundations exclusively for its whole alignment, relying on Crux’s customized drills, skilled helicopter support and specially trained drillers.
“There was no road access and no development for miles, so custom barge camps were used as mobile living quarters, machine shops, helicopter landing zones and whatever else was needed,” Tunison recalled. “Between access restrictions and the tight window we had to complete foundation work, this was an extremely challenging project. It’s what really launched us into the transmission market.”
Crux grew steadily within this market, and now provides design-build foundation solutions for lattice, self-supporting single shaft and guyed transmission tower foundations located in remote areas, or where geotechnical conditions present a challenge to conventional foundation construction. Landmark projects include installing the first micropile foundations for lattice towers on Southern California Edison’s Tehachapi Renewable Transmission Project in 2007, and implementing Crux’s patented steel micropile cap design on San Diego Gas & Electric’s Sunrise Powerlink Project in 2012.
Depending on site conditions, micropile foundations might be beneficial for an entire alignment, or for just a handful of structures located in particularly challenging terrain. Their lightweight elements and the smaller, lighter equipment required for installation can be transported by helicopter, allowing for construction in areas where road access is not permitted or feasible. Micropiles can also be beneficial when subsurface conditions are challenging or unknown. The threaded sections of casing and high-strength rebar can be adjusted onsite quickly and easily, so the length of the micropiles can be increased in softer-than-expected soils to achieve higher capacity without having to redesign or bring in different equipment. They can also be tested to validate designs, improving efficiency while maintaining safety.
“The projects we go after involve limited-access or challenging subsurface conditions, and there isn’t typically equipment available on the open market that can do the work exactly as we’d like to do it,” said Tunison. “Ever since Crux was founded, we’ve taken an active role in being innovative, building almost all of our equipment in-house or taking existing technology and evolving it to support our needs.”
Crux’s in-house fabrication shop maintains the company’s equipment fleet and designs, and its manufacturing division, Inland Pacific Drill Supply, fabricates and provides threaded tubular steel products.
Safety is the core value
“A majority of our upper management, superintendents and even operators have been with us since we started the company,” Tunison said. “We have a great core group of knowledgeable and experienced employees that have been really key to our success.”
In 2011, Crux was acquired by Quanta Services, an S&P 500 company that specializes in building infrastructure for the electric power and natural gas and pipeline industries, with approximately 17,800 employees and field operations across the United States and Canada. Crux’s own workforce is around 100 right now, Tunison estimates, and can fluctuate from 70 to 140.
“Some of that is union, because when we do these large construction jobs we’ll have additional local labour forces that supplement our lead operators,” he explained. Safety is always in the forefront, and new employees are required to work hand-in-hand with lead helpers and operators for a designated period of time to gain experience, as well as take safety training programs and submit to hazard analysis reviews. The company also has stringent helicopter company and pilot requirements for the work it subcontracts.
Recently entering the Canadian transmission market, Crux provided design-build micropile foundation services in northern British Columbia as a subcontractor to another Quanta company, Valard Construction. Micropiles were employed at seven of the 1,100 self-supporting lattice tower structures on the 287-kilovolt Northwest Transmission Line project between Skeena Substation, more than 1,000 kilometres northwest of Vancouver near Terrace, and a new substation that will be built near Bob Quinn Lake almost 350 kilometres further north. These seven structures were located in rugged, mountainous terrain and necessitated helicopter- only access.
The company will also be designing and building the foundations for three dead-end lattice tower structures and two tubular steel pole tangent structures for northwest British Columbia’s Forrest Kerr hydroelectric project.