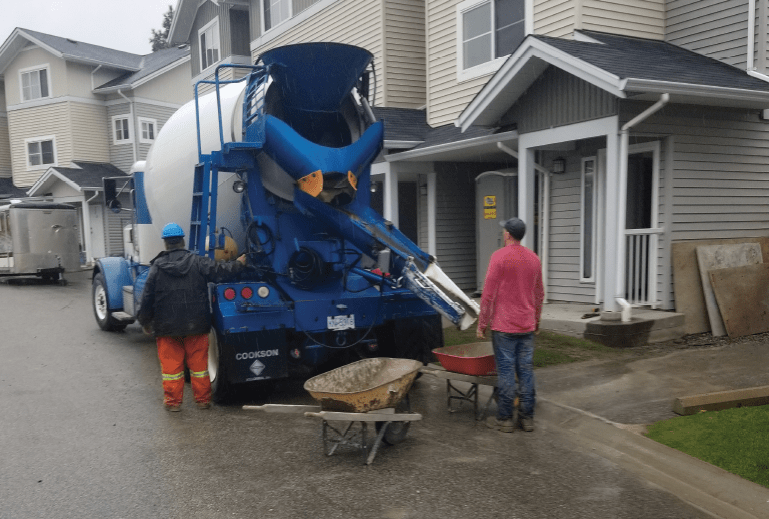
The Society of Hope, a Kelowna, B.C.-based non-profit organization that provides affordable housing, owns and operates 700 housing units in the interior of the province. One of its properties, Providence Vista, located in Westbank – about four hours east of Vancouver – includes several fourplex buildings, one of which showed signs of settlement almost immediately after construction was completed in 2001. A geotechnical report had recommended standard construction on the site, but soil instability became evident when exterior cracks on the building were noted.
In 2004, slope movement was confirmed by a geotechnical engineer. Monitoring of soil conditions continued until, in 2007, the Society chose to lift the building and install underpinning piles to a depth of 12 metres. Interior and exterior fixes were made, but the building continued to move. In 2016, the Society again decided that action was required and a team was put together to develop and implement a permanent solution:
- Geotechnical engineer – Tetra Tech
- Structural engineer – CWMM Consulting Engineers Ltd.
- Construction (helical pile installation, levelling of building) – Team Foundation Systems Ltd.
Tight quarters create logistical challenges
The plan to stop the sinking and ensure the building’s stability involved installing helical piles to properly support the foundation.
“It was a perfect storm for settlement on the site,” said Grant McKinney, owner and project manager of Team Foundation Systems (Team). “The soil is not the best and the building is on the edge of a bank. A finished building on a neighbouring lot had to be demolished and completely removed due to ongoing structural concerns.”
Conditions around the building meant Team had a small laydown space, a very tight working space and a ravine and creek to protect during the construction process. The crew was also cognizant of the families that were temporarily displaced to enable the work to be done and of the other families nearby that had to live through the noise and mess of a construction project in their development. As always, safety was a priority.
Before starting construction, Team had to ensure that the creek would not become contaminated with concrete or soil from the site. An existing chain-link fence with the addition of plywood in affected areas was deemed sufficient to prevent any materials from making their way downhill into the ravine and creek. Space limitations meant Team had to use small machines for all tasks and move limited amounts of material at a time, as it was needed.
The company’s Bobcat S650 skid-steer loader was vital and used to move all construction material and equipment, and for post site grading. A Kubota KX-91 mini-excavator was used for all pile preparation work and installation of all helical piles, the latter with an Eskridge BA-77 drive head. A custom-built John Deere remote hydraulic pump powered the drive head.
With the building empty of its tenants, Team began its work by removing all of the floor slabs (slabs on grade) in the ground-level units of the fourplex to gain access to the subgrade material beneath.
A combination of 31 Chance SS150 series and SS175 series helical piles, hot dipped galvanized to ASTMA153 and A123 specifications, was required by the engineering design. The SS150s are 1½-inch square-shaft piles with a 70,000-pound maximum ultimate compression and tension capacity; the SS175s have a 1¾-inch square shaft and a maximum ultimate compression and tension capacity of 100,000 pounds. Seven-foot and 10-foot lead sections were used in 8/10/12 and 10/12/14 configurations, along with a variety of extension lengths from three feet to 10 feet. Chance products are ISO9001 certified and ICC Evaluation Service (ICC-ES) determined the piles to be in compliance with code requirements ICC-ES, ESR-2794.
The deepest pile installed on the project was 78 feet deep before required torque values were obtained. Microsil anchor grout was used to encase the piles with a six-inch column around each unit. Eighty-kip underpinning foundation brackets were attached mechanically from the piles to the foundation to support the structure and prevent any further sinking. New grade beams were installed on top of the piles.
The piling and concrete work done by Team took more than five weeks to complete. Interior work to repair damage throughout the building caused by its shifting took about another six weeks. Residents were able to return to their homes within three months of the start of work and landscaping work continued after their return.
There’s a small possibility, says McKinney, that similar work will have to be undertaken at some point on two other buildings in the same complex. Engineering professionals will continue to monitor the site and initiate action if required. Team Foundation Systems was pleased to work on the project with the Society of Hope.
“We were happy to provide a service with trained and certified professionals, and work with a great non-profit toward a common goal – getting families back in their homes as soon as possible.”