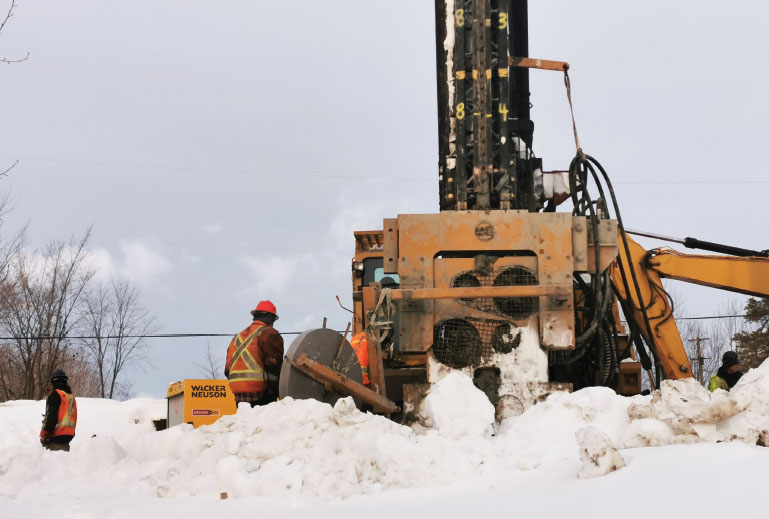
American Piledriving Equipment Inc. brings its deep foundation experience to northern Ontario, helping to install wick drains in the rebuild of the century-old Blanche River Bridge
In March 2019, the Government of Ontario announced that it would be investing $1.3 billion to help rebuild and restore 123 highway projects across the province, of which $291 million has been earmarked to support infrastructure renewal projects throughout northeastern Ontario. One of these important projects was the replacement of the Blanche River Bridge on Highway 569, near New Liskeard.
“Our government is delivering on our commitment to be open for business and open for jobs,” said Jeff Yurek, Ontario’s Minister of Transportation at the time of the announcement. “We are determined to improve our transportation infrastructure and create good jobs for our construction industry. This funding is a clear example of that commitment. We are working to improve road safety for all Ontarians.”
Built in the 1920s, the Blanche River Bridge was nearing the end of its design life and needed to be replaced. For almost a century, the bridge has served the area as a single-lane, three-span concrete structure founded on two pile-supported abutments situated on land, as well as two pile-supported piers in the water. This project will transform the bridge into a modern, two-lane structure that allows traffic to pass efficiently in either direction from both ends of the bridge.
The general contractor for the project, EXP Global, has tasked Ontario-based Facca Inc. with replacing the bridge, relying on Facca’s 60-plus years of experience in heavy civil construction, as well as its well-deserved reputation as an industry specialist in bridge and below grade reinforced concrete structure construction.
In completing this project, Facca teamed up with American Piledriving Equipment Inc. (APE), a world leader in research and development, production and sale of foundation construction equipment. APE produces some of the world’s largest pile drivers and has offices in every corner of the U.S., Canada and Asia, with a worldwide distribution network. The company is renowned for its commitment to providing outstanding products and service. APE’s dedication to assisting clients is the key to its success, and has established the company as being an industry leader in patents issued worldwide.
“APE has a unique way of doing business in the deep foundation construction industry,” said Eric “Wiggy” Legault, Canadian regional manager at APE. “We don’t rely on outside distributors and instead rent and sell directly to the contractor. We are boots on the ground at the job site and we assist our clients with the set up of the equipment they purchase or rent from us. We get our people out in the field where they can help, teach and learn. From design to production to installation, APE professionals are involved, and transforming a good idea into your job site reality is our specialty.”
The new bridge on Highway 569 is being constructed with a different alignment from the original structure, and that requires new embankments. This means that additional load will be applied to the soft, underlying clays that run deep throughout the region.
“Because of this additional load, the bridge design has called for wick drains of a maximum depth of 150 feet in the areas of new embankment construction in order to accelerate the settlement caused by the embankment loads and – most importantly – to reduce the effects of down-drag on the piles at the new structure abutments,” said Steve Gardonio, project manager at Facca.
When ground pressure is added to the area that a structure is being built upon, the water underneath will make its way to surface through seepage and the soils will naturally compress and settle from the weight that has been mechanically applied; with the soil matrix gradually taking up the pressure change and shrinking in volume. This laborious consolidation of water-saturated clays or soils is a progression that can take years or even decades to achieve. In the meantime, this process can potentially delay or stop any future plans for development in the immediate area until the required soil density is attained through settlement. However, this is a progression that can be significantly sped up by installing Prefabricated Vertical Drains (PVD) – or wick drains – in the ground.
“The use of wick drains will accelerate the time of settlement from a span of years to mere months, and any damage to roadways, embankments and structures resulting from the soil shrinkage will be non-existent,” said Legault. “Using wick drains will help to expedite schedules, greatly reduce costs and leave structures standing tall for many decades to come.”
The Blanche River Bridge replacement project has encountered a number of challenges to date, such as the depth of the wicks, the need to install them on a benched embankment, and surrounding earth with low bearing capacity and a propensity to slide.
Typically, wick drains are installed in a wide open and flat area. However, for this project the wick drains needed to be installed on a bench level, backfilled and then moved up to another bench level. With only 16 feet of travel area on most of the bench levels where the wick drains were being driven, the useable space for the work to be performed was extremely limited and restricted the degree of motion and manoeuvrability for the rig. Fortunately, APE’s light and compact Wick Bottom Drive Rig was able to position and manoeuvre in the limited space and sensitive soil conditions offered by the work area.
Overcoming this particular challenge required a high degree of co-ordination between APE and Facca. Together they devised a plan of assembling 60 feet of mast and the APE 200 Bottom Drive Unit to the rig. Then, after walking the machine down the steep ramp and lowering all 160 feet of wick leader over the edge of the bank to the machine, they completed the assembly in the hole. Once this was accomplished, the project team was able to raise the rig’s soaring 173-foot-tall mast into the air, where it could be seen for miles.
“This project – as with any project – has been a test,” said Legault. “There are always unforeseen obstacles that will rise up through the course of completing any job. Finding a way around these obstacles is what sets APE apart from the rest. We thrive on challenges and believe that, without hurdles, we can’t keep getting better and these kinds of projects are the heartbeat of what we represent at APE.”
Another complication for the project was the frigid climate of northern Ontario, with temperatures dropping below -40°C in the wind, combined with copious amounts of heavy snow which fell on the jobsite throughout the winter months.
“When the cold temperature is this extreme, its impact on the equipment needs to be properly addressed,” said Legault. “But while the cold proved to be a challenge, it was definitely not a show-stopper for us. APE has established cold weather procedures that allow our clients to successfully operate our equipment with minimal downtime.”
APE takes its responsibility to the environment seriously. In 1990, APE was the first to introduce pile driving and deep foundation equipment equipped with vegetable hydraulic oil and the company is the one of the largest North American users of vegetable hydraulic oil. APE has determined that vegetable hydraulic oil provides a high-quality performance when compared to even the more expensive petrochemical hydraulic oils.
“We choose to use non-toxic vegetable hydraulic oil because it makes sense for the environment,” said Legault. “When you are working with heavy duty equipment near a main water source up in northern Ontario, it is always a wise decision to go green when possible. In this, APE’s clients are always guaranteed some peace of mind that they are doing a part in protecting our planet.”
The health and safety of its clients and customers is always top of mind for APE, and the company designs all of its pile driving equipment with strict safety measures that go well beyond the industry standard. Everything that APE provides comes with the appropriate safety manuals, as well as a team of APE representatives who arrive on site to train and orientate clients’ crews on how to safely and efficiently operate APE equipment. The company even has a pile driving school that offers programming to teach its customers more about the foundation equipment industry.
“No matter where our equipment is sold – anywhere in the world – our clients have come to know that APE aims to exceed their expectations,” said Legault. “All of our equipment is designed based on our customers’ needs and requirements, and we always strive to seek out ways to make things better. We strongly believe that something ‘well said’ has nothing near the impact as something ‘well done.’”
The completion of the Blanche River Bridge is anticipated for the end of 2021.