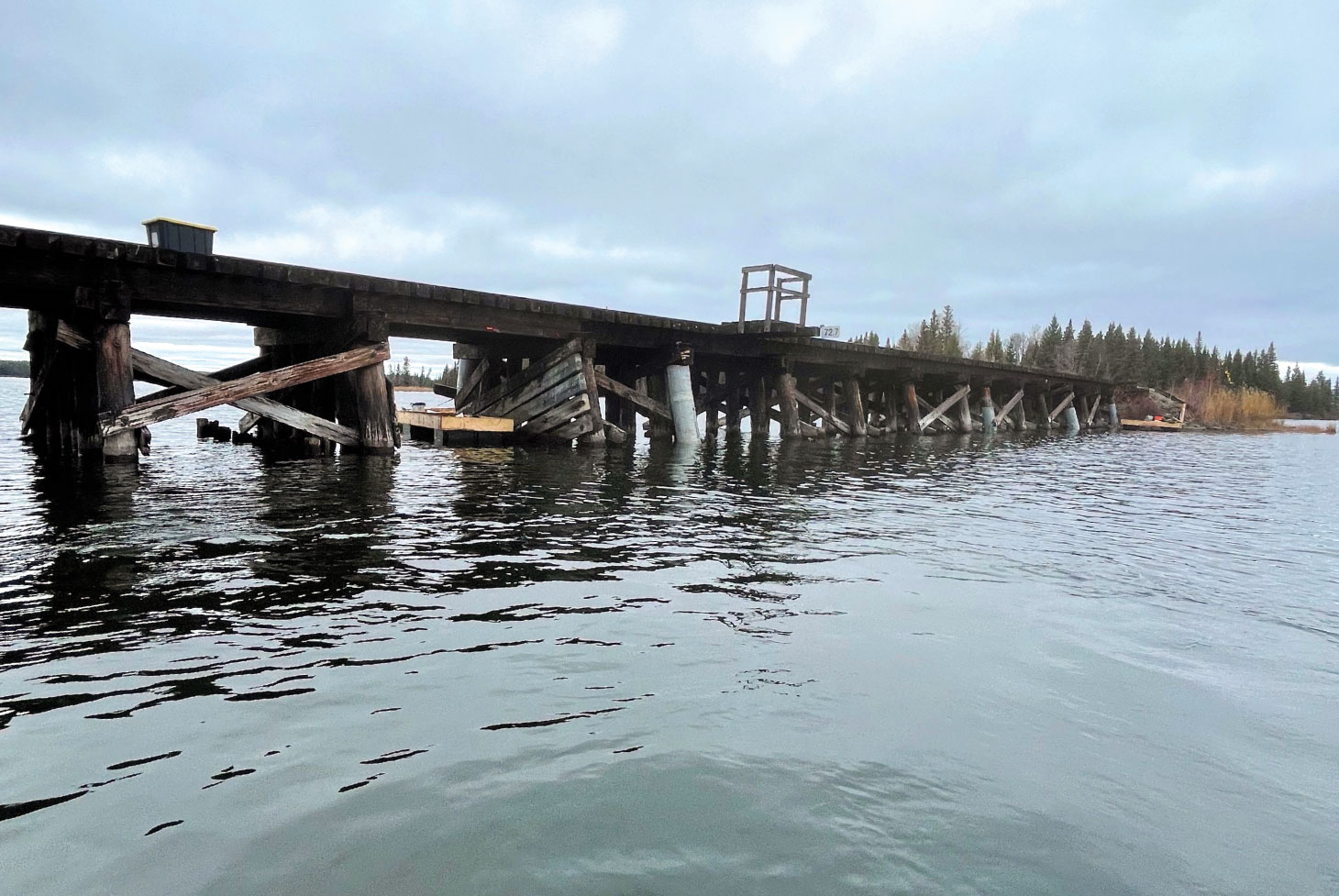
Timber piles support many railroad and secondary highway bridges across North America, but many are deteriorating as they near the end of their design life. These structures are often in remote locations, where repair methods requiring minimal equipment are preferred. Canadian companies have successfully used two techniques to extend the life of aging piles. Both techniques use 1.1-millimetre (mm) thick laminates made of glass fibre reinforced polymer (GFRP) products, supplied in 1,200-mm wide rolls over 100 metres (m) long.
In one technique, a laminate – cut to twice the pile’s circumference plus 200 mm – is coated with epoxy and wrapped around the pile, forming a structural shell. The narrow annular space (1–2 mm) is filled with low-viscosity resin, bonding the GFRP to the pile and restoring its strength.
For the other technique, longitudinal reinforcing bars are positioned around the pile. The laminate is wrapped around these bars to create an annular space up to 75 mm wide. The annular space is filled with concrete, creating a new reinforced concrete column around the deteriorated timber pile. The GFRP laminate provides significant confinement pressure and eliminates the need for ties. Both techniques have been successfully implemented on several projects throughout Canada.
Timber piles have long been used in bridges due to their availability and low cost. Historically treated with creosote for durability, environmental restrictions have limited such treatments, making them more prone to decay. Meanwhile, cleaner waterways have led to a resurgence of marine pests like gribbles and shipworms, which further weaken wood piles.
Loss of cross-sectional area reduces axial capacity, necessitating reinforcement. Remote bridge sites often lack road access, making repairs with heavy equipment expensive and impractical. Timber piles also vary in size, making pre-manufactured jackets unsuitable, as incorrect fits cause delays and increase costs. GFRP-based repairs address these challenges efficiently.
Repair system
Fibre reinforced polymer (FRP) products were introduced in the late 1980s for repair of structural members. The original system consisted of fabrics of carbon or glass that would get saturated with epoxy in the field and bonded to the exterior surface of the structural element. When the epoxy cures the next day, FRP reaches a tensile strength two to three times that of steel. While the technique known as wet layup has been successfully used on thousands of projects worldwide, the flexible fabric must be bonded to a flat, smooth surface such as a concrete beam or slab – it is not suitable for repair of timber piles with uneven exterior surfaces.
The patented solution for repair of piles uses a special type of FRP laminate developed by Mo Ehsani, PhD, PE, SE, over a decade ago commonly known as PileMedic. These laminates are made in a special process where one or more layers of reinforcing fabric are saturated with resin and subjected to heat and pressure to produce a very thin laminate. The laminates can be supplied in rolls that are up to three metres wide by over 100 m long. However, for repair of piles, a 1,200 mm (4 feet) wide roll is most convenient for handling in the field. The system has been tested extensively by various agencies (Gull et al. 2015; Hammons, et al. 2018).
Shape and size
Conventional fibreglass jackets must be ordered to size for each project, potentially creating delays if the jackets are manufactured too big or too small. In contrast, the small thickness of these laminates, which is typically less than 1.5 mm, makes them flexible enough to be wrapped around piles of any shape and size. Standard practice wraps the laminate twice plus a 200 mm extension around the pile.
After cutting the required length from a roll, the second half of the laminate is coated with an epoxy paste, and it is wrapped around the pile and bonded to the first layer, creating a two-ply structural shell around the pile. This eliminates the need for custom ordering the jackets, saving significant time, shipping and storage cost. Each of the 120-metre-long rolls can repair 75 m of 250 mm diameter piles, or 63 m of 300 mm diameter piles, etc.
In repair of badly deteriorated piles, it is necessary to add supplemental reinforcing bars to increase the flexural capacity of the pile. Placement of these bars and maintaining their position during the placement of grout is a challenging task. We have developed multi-purpose plastic spacers in a variety of shapes and sizes. A zip tie can be passed through several spacers and fastened around the pile. When needed, the longitudinal reinforcing bars (typically made of glass FRP that will not corrode) can be snapped into these spacers. This allows the engineer to know the precise location of each bar and the width of the annular space that are needed for strength calculations. The annular space between the jacket and the pile will be filled with grout, concrete or epoxy later.
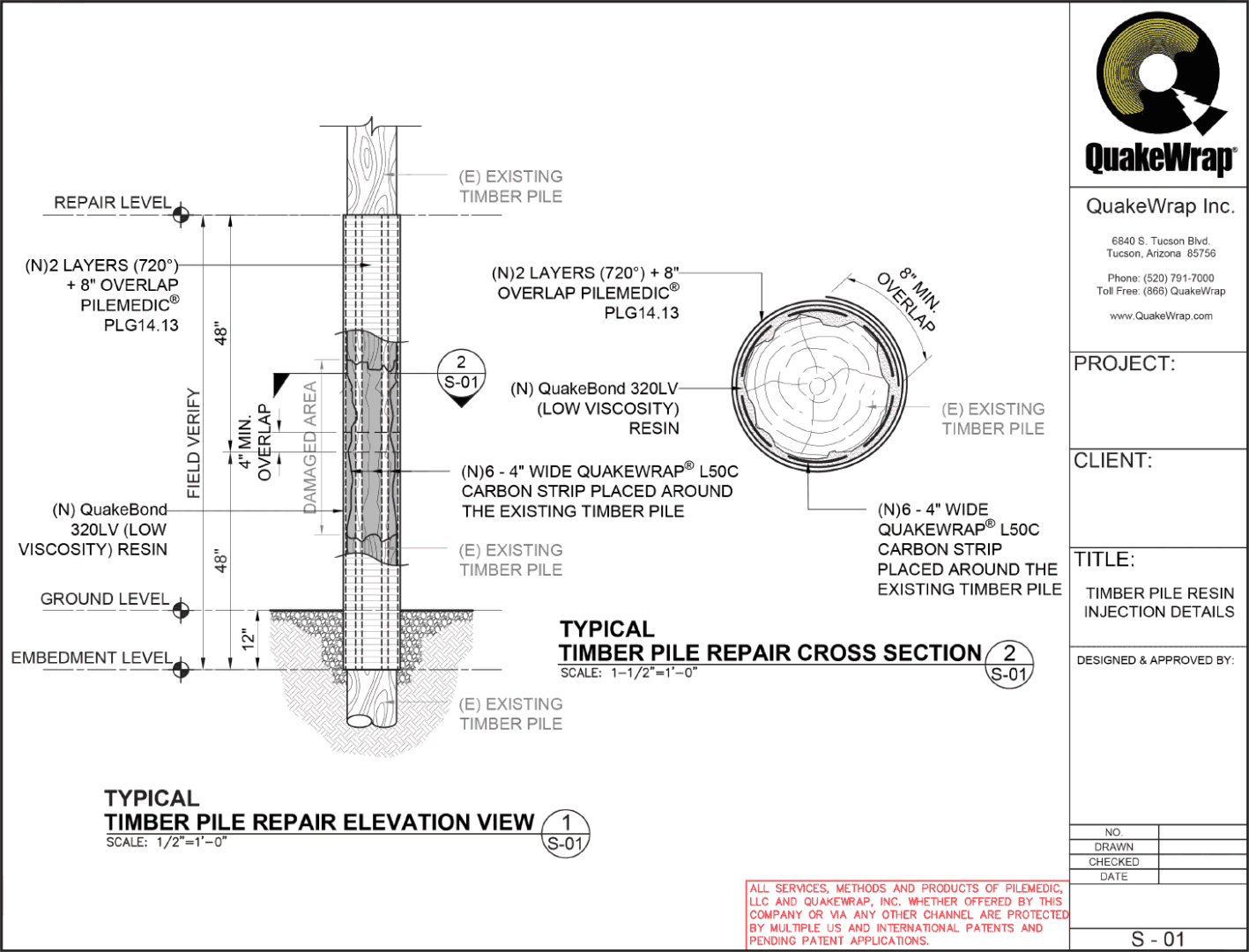
Reinforcement and confinement
Depending on the type of fibre used (carbon or glass) the FRP laminates have tensile strength ranging between 200-1050 megapascal (MPa). Furthermore, by selecting the orientation of the fibres within the fabrics the strength of the laminate in the longitudinal and transverse directions can be adjusted to meet the specific project requirements. The jacket creates a uniform confining pressure (i.e. 360 degrees) around the pile and eliminates the need for hoop reinforcement. This allows divers to install the vertical reinforcing bars individually (when needed) and the lateral reinforcement or tie is provided by the jacket itself.
The elimination of handling assembled reinforcing cages that requires two divers results in significant dive time and savings for the project. The most common laminate (PLG14.13) is equivalent to 12 mm ties placed at a spacing of 70 mm along the height of the pile. The confining pressure of the jacket also increases the compressive strength of the original pile and any grout that is placed in the annular space. This results in a larger axial load-carrying capacity of these piles compared to a pile repaired with conventional FRP jackets of the same size.
The jackets also have significant strength along the axis of the pile that could contribute to the axial and flexural capacity of the repaired pile. However, to fully engage the jacket, it must be bonded to the pile. The use of an epoxy as the filler material achieves this. But, when a cementitious material is used to fill the annular space, it is conservative to ignore the contribution of the jacket in flexure. A more economical way to increase the flexural strength of the pile is to introduce GFRP rebars in the annular space and fill the space with a non-shrink grout or concrete.
Corrosion protection
It is well recognized that oxygen present in water is the fuel for the corrosion process. The laminates create a seamless shell around the pile, preventing any moisture or oxygen ingress. In the same way that paint is used to protect steel structures from corrosion, FRP products can be used with longer lasting results. FRP materials do not corrode and offer a very long service life. Unlike paints that crack and peel off after several years, the fibres in these laminates prevent them from cracking, giving them an extended service life. This will drastically reduce the corrosion rate in the pile. In contrast, most jackets on the market are comprised of two pieces that are bolted together in the field; these seams will allow for passage of some moisture and oxygen and the corrosion process will continue after the repair is completed.
Another benefit of the seamless shell is that it allows the use of a low viscosity resin as the filler material without any concern of epoxy leaking from the seams.
Filler material
The filler material can be either resin-based or a cementitious material. The examples presented here use a low viscosity resin that bonds the jacket to the pile and fills all the voids, cracks and cavities inside the pile. In this case, it is best to keep a minimal annular space to keep the repair cost down. Alternatively, a non-shrink anti-washout concrete or grout can be used. These are often accompanied by GFRP reinforcing bars placed in the annular space. The annular space for these applications is 40 mm or larger to allow the concrete to flow freely.
In some cases, the repair portion of the pile extends to the mud line and the soil provides a seal at the bottom of the jacket for placement of the grout. However, there are applications where the length of the repair is limited to the splash zone, requiring the creation of a seal at a point along the height of the pile where the bottom of the jacket will be positioned.
Field applications
The system above has been used to repair approximately 200 piles in Canada recently.
The Selkirk trestle
The Selkirk trestle in northwest Victoria, B.C. provides a link for pedestrians and cyclists between Victoria/ Saanich and Victoria West. The trestle was initially erected in 1917 for the Canadian Northern Railway (now called Canadian National (CN) Railway). Use of the trestle for rail service terminated in the early 1980s and it was subsequently threatened by fire in the early 1990s. The structure was repurposed in 1995, turning the trestle into a multi-use regional trail (part of the Galloping Goose trail system). The trestle is comprised of 61 timber bents, typically spaced at 4.5 m and generally constructed with six piles each, and a 37 m long steel Scherzer Rolling Lift Bridge commonly referred to as the bascule. The overall structure is 302 m long.
The Galloping Goose trail project and other projects that have expanded the Greater Victoria Cycling Network have been very successful, with use exceeding the original expectations of the project. According to Statistic Canada, the Victoria area has the greatest percentage of walkers and cyclists in Canada, with more than 15 per cent of workers over the age of 15 biking or walking to work daily.
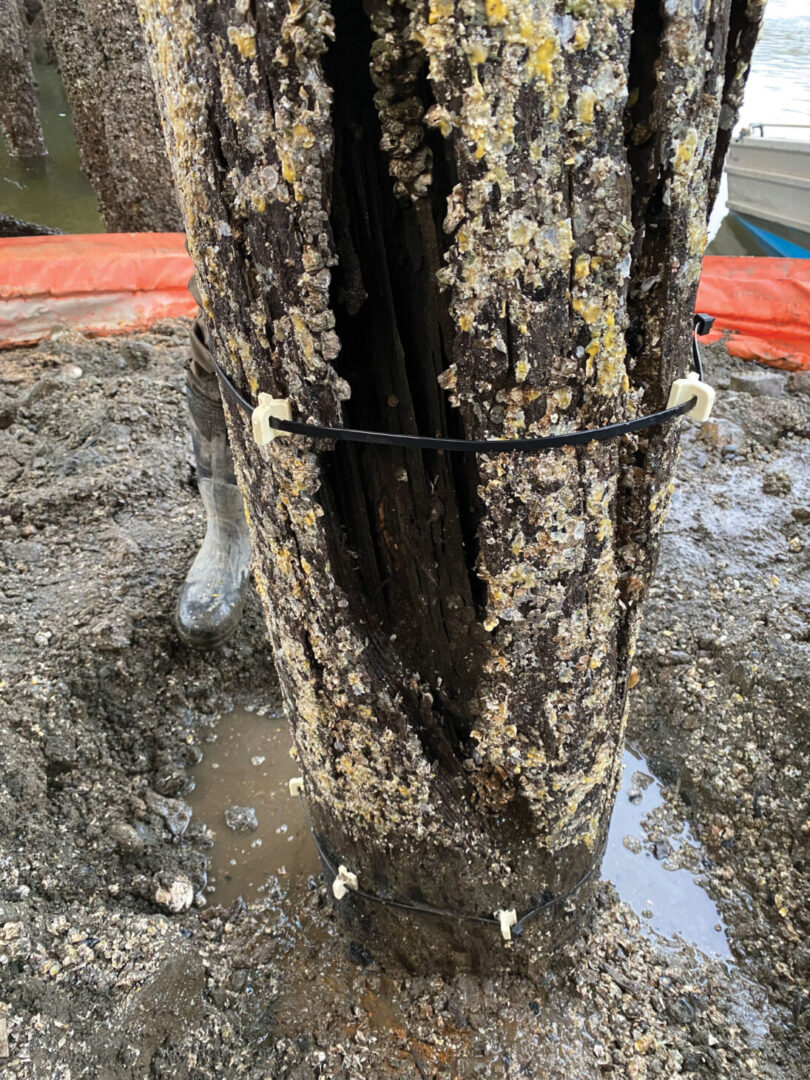
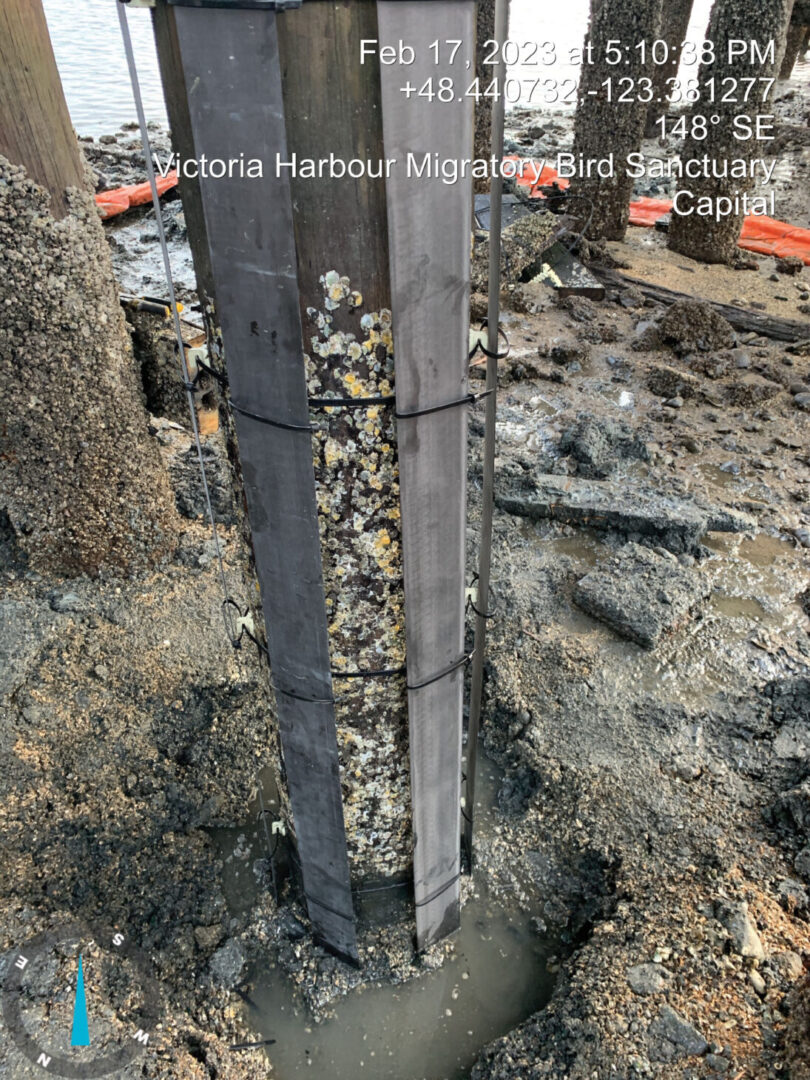
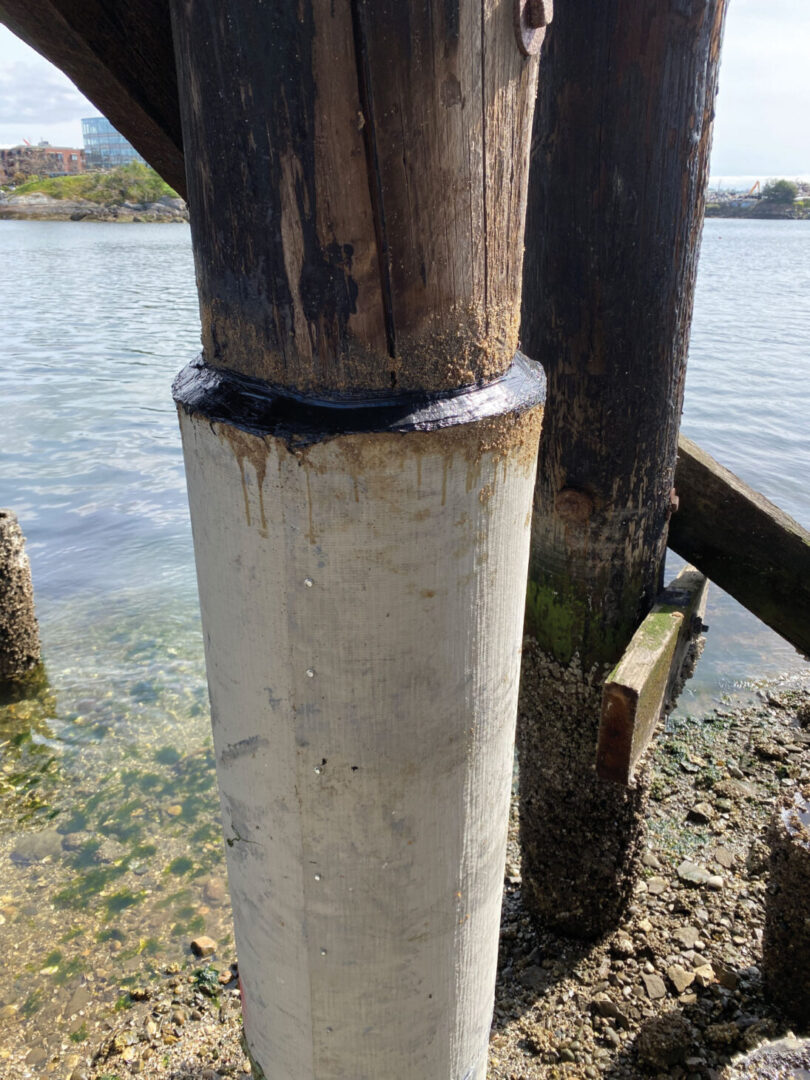
The original Selkirk trestle crossing was constructed to support rail loading, which is significantly heavier than the current loading for the structure. Stantec completed a detailed condition assessment of the trestle in 2021 and noted that the time is approaching where a substantial substructure upgrade will be needed to keep the trestle in service. Stantec anticipates up to 60 of the existing 366 piles will need substantial repairs. As part of an eventual repair, the CRD is also considering widening the structure to accommodate the future demands of cyclists and pedestrians.
As part of the 2021 condition assessment, Stantec recommended using a FRP repair system for the damaged piles. This system was recommended for the Selkirk trestle primarily because it would allow the structure to remain in use during the repair construction.
The main deterioration method for the timber piles is marine borer attack. Marine borer is a collective term used to describe invertebrates that thrive in brackish water and burrow into and damage wood members. Preservative wood treatment systems such as creosote have traditionally been used to protect wood from this kind of damage. Typical marine borer damage often results from a small split or bolt hole whereby the invertebrates gain entry to the untreated heartwood of a pile. The treated shell of the pile often remains intact, while the invertebrates effectively hollow out the inside of the pile. This damage often goes unnoticed until it has progressed to the point where the shell of the pile starts to fail. FRP repair is a good option to mitigate this condition, as the marine borer damage is typically localized to the intertidal zone, with sound wood being found above and below the area of marine borer attack.
In the fall of 2022, Stantec prepared repair drawings and specification for a trial project, which would repair four of the existing timber piles. A local marine contractor, Salish Seas Industrial Services, completed the repairs. Four 100 mm (four inches) wide carbon laminate strips with tensile strength of 2,825 MPa were placed around the pile in the damaged zone.
PileMedic laminate wrapped around pile created a seamless shell that was filled with a low viscosity high compressive strength resin. This resin bonds the carbon strip, timber pile and the PileMedic shell together to resist all imposed loads. The low viscosity resin also flows through all cracks and fills the voids formed by the marine borers, increasing the axial capacity of the pile. The carbon strips and the PileMedic shell provide significant flexural capacity for the repaired pile.
Railroad bridges in remote sites
Northern Canada experiences extreme cold temperatures that can make any construction project challenging. Over the last four years, Western Infrastructure Renewal, Inc. has been repairing hundreds of bridge piles using the PileMedic system. Many of these bridges belong to municipalities or are on rural roads and are used to transport people and various freight. Western Canadian Short Line Rail-way Association is an industry association representing 18 short line railways across Alberta, Saskatchewan and Manitoba.
In 2023, Western Infrastructure Renewal repaired 135 piles located on eight bridges; they were scattered throughout northern Manitoba, which experiences very cold temperatures and snowfall. The bridges had piles that varied in diameter between 400 to 500 mm. The repairs were completed over the period of April through late November 2023. Many of the piles had rot and damage just above and below the water level, although eight piles required encapsulation for their full height. Once the damaged portion of the piles was wrapped in a two-ply shell created on site with PileMedic laminates, the annular space was filled with a high strength, low viscosity resin.
The remote locations of these projects cause significant challenges in terms of mobilization and demobilization. Most of these sites were not easily accessible by cars. The crew used floats and rafts to access the piles. The railroads provided high rail trucks to carry these rafts and lower them in water below the bridges. They would subsequently lift the raft at the end of each project and move it and the other equipment and materials to the next repair site.
Epoxies in general have a temperature range for storage, mixing and application. The system can be applied in temperatures higher than 7C (45F). In most cases, the crew can keep the quantity of the resin needed for each shift inside the heated cab of a work truck. But this was not possible for the extreme conditions on these sites. A closed quarter was built on a raft using insulated tarp. A heater on the rail truck continuously provided hot air through a flexible duct to keep the crew and the resin warm.
One of the advantages of the PileMedic system is that the thin laminates can be wrapped around a pile in very tight spaces and small clearances. Each laminate covers a length of 1,200 mm (4 feet) along the pile. Additional laminates can be installed overlapping the previous one by 100 mm (4 inches) to cover the desired height. Once the required length of the pile is wrapped in the PileMedic shell, the high strength low viscosity resin is mixed and gravity fed into the annular space. This will fill all the cracks and voids in the pile, and it will bond the shell to it. All the epoxies that are a part of this repair system cure underwater. This is of particular significance because it eliminates the need for construction of cofferdams and dewatering.
Diagonal braces are usually bolted to the piles on timber bridges. These bolts could be temporarily removed, and a wooden peg of the same size could be placed in the bolt hole. Once the jacket is wrapped, it can be pierced to allow the removal of the wooden peg and installation of the same diagonal brace or a new one using the same bolt hole. As the last step, the annular space is filled with low viscosity resin.
In terms of productivity, this repair system can be installed very quickly. A main advantage is the fact that the laminates can be formed into a shell of any shape or size in the field, preventing delays. On this project, each crew could finish between two to three piles a day. The 135 piles were repaired in about six months.
Prior to these repairs, several of these bridges were planned to be replaced, at costs exceeding $10 million. The repair system will extend the service life of these bridges for decades with virtually no disruption of service during the repairs. Considering the huge savings, the railroads are planning to increase the number of piles being repaired. They are also considering strengthening some of the deteriorated beams and stringers with wet layup FRP.
PileMedic cost
The PileMedic laminates used on these projects cost around US$120 per square metre. The epoxies used in this system cost roughly US$35 per litre. As an example, the cost of a 300 mm shell including the epoxy paste applied to the second half of the laminate is less than $350 per metre height of the shell. To minimize the volume of the injection resin, it is best to wrap the laminate tightly around the pile. Some piles may have excessive cracks and cavities in the middle that are not easily detected from the outside, making it difficult to calculate the volume of resin needed to fill those cavities. Assuming four litres of resin per metre of the pile, the total cost of the repair system, including the shell and the injection resin is about US$500 per metre.
Approximately two piles can be repaired each day, allowing many of these bridges that have been considered for demolition to be returned to service shortly and at minimal investment. Repairs can be performed while the bridges remain open to traffic.