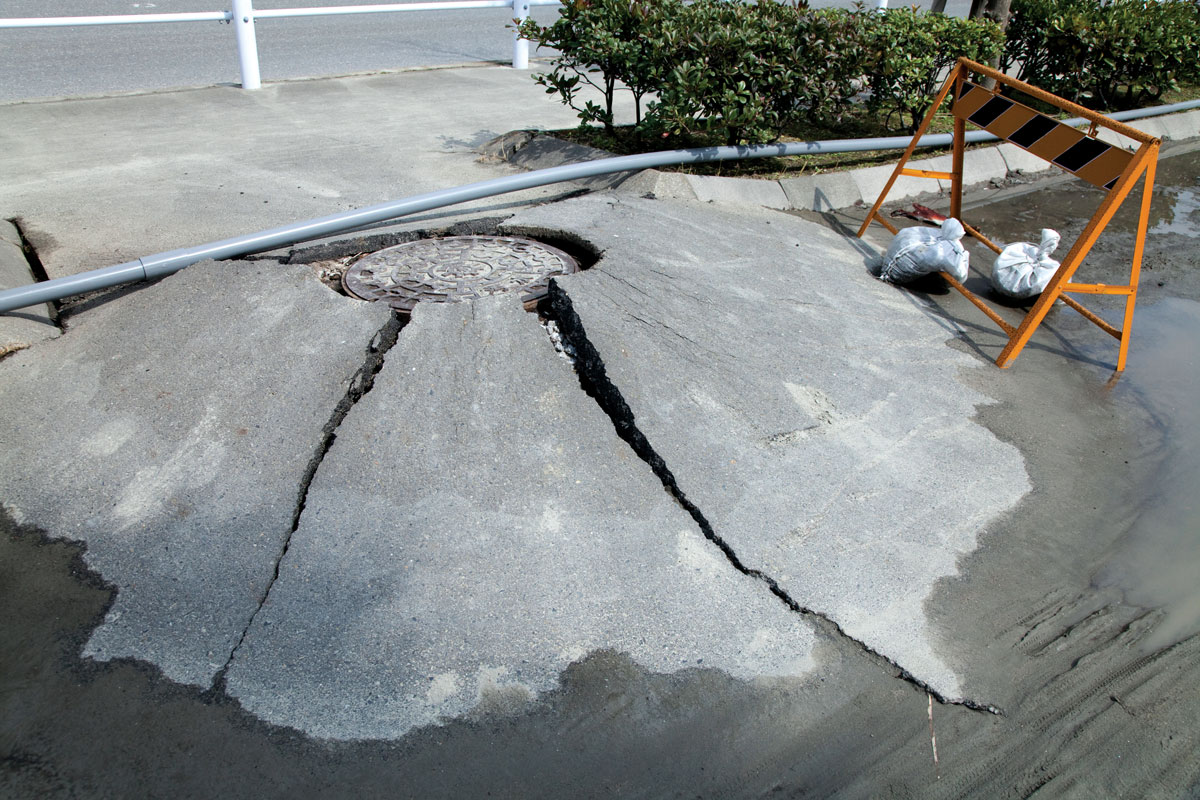
The jumping of a manhole cover due to liquefaction (Photo: paylessimages/123RF)
While most people may not be familiar with the term liquefaction, it’s a phrase many individuals working in the deep foundation industry are all too familiar with.
In simple terms, seismic liquefaction occurs when soil loses strength and stiffness as a result of cyclic loading from an earthquake. All of this shaking generates excess pore water pressure and results in the soil losing a significant amount of stiffness and strength, which causes it to act more like a viscous liquid than a solid. This can result in the loss of bearing capacity and excess settlement and cause significant damage to overlying structures.
“The liquefaction risk if left unmitigated can be significant. It’s a life safety hazard,” said Jim Gingery, a chief engineer for Keller North America.
“You can have buildings that punch into the ground and collapse. In the case of dams, a dam that fails can have an uncontrolled release of water that could threaten life. It can also be damaging and costly to the owners of structures that aren’t designed to handle liquefaction.”
There are essentially three ingredients required for liquefaction to occur. The first is sandy or silty soil. Second, this soil must typically be loose to medium dense. Third, an earthquake is required to shake the ground hard enough to generate liquefaction.
Gingery says liquefaction is largely a problem where earthquakes occur and where sandy soil is most commonly found, such as the West Coast areas of Canada and the U.S. This includes Vancouver where active faults, including the Cascadia subduction zone, can generate large earthquakes. It’s also a concern in areas of Eastern Canada along the St. Lawrence River where smaller, but damaging earthquakes are possible.
In simple terms, seismic liquefaction occurs when soil loses strength and stiffness as a result of cyclic loading from an earthquake.

Liquefaction is particularly worrisome when structures are built on a slope, such as a dam. It’s also a concern with shallow foundation projects that sit on liquefiable soils since it can result in bearing capacity failure and excessive settlement. Buildings that have been constructed on pile foundations or have incorporated some form of ground improvement are far less at risk.
So, how can contractors determine if a project is at-risk of liquefaction?
Gingery says liquefaction characterization work is normally conducted by a geotechnical engineer or consultant as part of their initial field exploration and subsequent laboratory testing and analysis program. This preliminary work allows everyone involved to determine the liquefaction potential at a worksite and then analyze how much of a hazard it is and what the consequences of it could be.
The two most common field testing techniques used in liquefaction evaluation are standard penetration testing (SPT) and cone penetration testing (CPT). SPT involves driving a cylindrical soil sampler into the ground using a specified weight and drop of a hammer, and measuring the number of blows required to advance the sampler 30 centimetres into the ground. In the case of CPT, a cone with an area of 10 to 15 square centimetres is pushed into the ground, which determines soil density and type. The penetration resistances are then used to evaluate the soil’s liquefaction resistance relative to the design earthquake loading.
The good news is that even if liquefaction is determined to be a risk at a site, that doesn’t necessarily mean the location has to be eliminated from consideration. There are several different methods of soil liquefaction mitigation that can be employed to provide added strength and stability to that ground.
Gingery says liquefaction mitigation is generally divided into two categories: deep foundation and ground improvements.
The list of deep foundation options, he says, includes drilled shafts, auger cast piles and driven piles. Compaction piles are particularly effective because they can both densify and reinforce soils, and can be driven up to depths of 60 feet. Gingery says that larger diameter piles tend to be the most effective because of their structural robustness.
Ground improvement mitigation methods can include stone columns, deep soil mixing, deep dynamic compaction, jet grouting and compaction grouting, which involves injecting stiff, mortar-like grout into the ground to form bulbs that push soil to the side and increase its density. Gingery says stone columns and deep soil mixing are two of the most popular and effective methods used in North America.

There are several different methods of soil liquefaction mitigation that can be employed to provide added strength and stability to that ground.
With stone columns, a vibratory probe is inserted into the ground and gravel is introduced into the ground through a tube at the end of the probe. The probe moves up and down to compact the gravel and push it laterally into the soil. The process is repeated over and over in a triangular or square array of columns, which Gingery says results in a mass of soil that’s densified and reinforced.
Deep soil mixing is a technique in which a large drill rig with a mixing blade that resembles a giant eggbeater is used to pump a grout slurry into the ground and mix it with the soil to form columns of something referred to as soilcrete. It can provide a compressive strength of anywhere from 100 to 1,000 PSI. Gingery says in the case of liquefaction mitigation, these columns are built in a “grid of intersecting panels like a lattice.” This grid shields the ground from becoming loaded during an earthquake and essentially renders the soil non-liquefiable, he adds.
Which mitigation method is best to use depends largely on the particular needs of a project, the owner’s performance requirements for the building and what the budget is, says Gingery. The type of soil at a site is another huge determining factor, he adds. For example, if the soil is silty or clay-like, the stone column technique is not likely to be effective since it won’t drain fast enough to be compactible. Soil mixing might be the best choice in that case because it can work in all soil types.
Gingery says liquefaction mitigation should be one of the first orders of business when it comes to building on sandy or silty soil.
“For new construction, it’s something you should do right at the beginning because everything you’re going to construct is going to rely on that work,” he said.
However, that doesn’t mean that liquefaction mitigation can’t be used with existing structures or facilities where the hazard already exists and wasn’t properly addressed when the structure was built. In cases like that, Gingery says techniques like compaction grouting can be used with relatively small equipment that can be used inside the building.