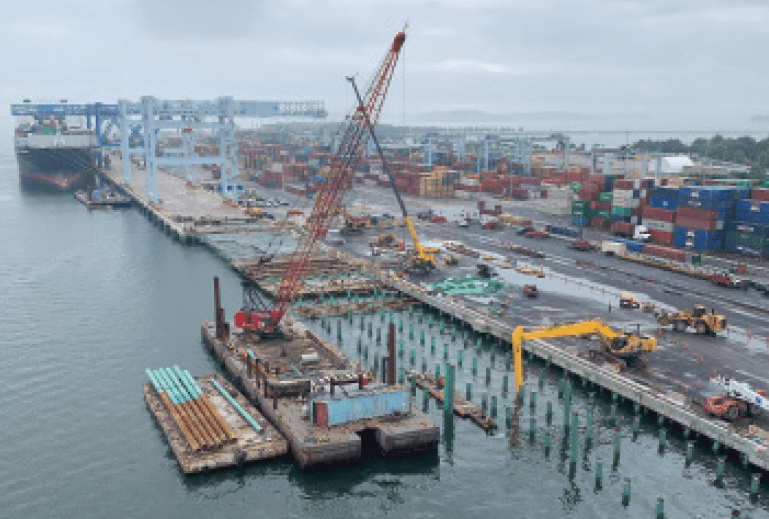
Coastal Marine partners with Berminghammer to improve efficiency at the Paul W. Conley Container Terminal in Boston, Mass.
The importance of the Paul W. Conley Container Terminal in Boston, Mass., to the regional economy is undeniable. According to the terminal operator, Massport, Conley Terminal is the only full-service container terminal in New England and serves all of the world’s major international container lines. In 2019, Conley Terminal set a new record in cargo volumes for the fifth consecutive year when it handled more than 307,000 20-foot equivalent units – an increase of eight per cent over the previous year – connecting more than 14 million people who call New England home with the goods and services they depend on each and every day.
Recognizing Conley Terminal’s growth and significance, Massport unveiled a massive $850 investment program in 2017 to improve port capacity to attract some of the larger vessels that currently dock in New York and New Jersey, and help to ensure that Boston’s port remains competitive for the foreseeable future.
As part of this investment, general contractor, D.W. White, has constructed a new 1,300 linear feet (LF) long by 110 LF wide deep construction-supported reinforced concrete pier, providing an additional 158,000 square feet of pier space for Massport to berth large cargo container vessels. Overall, the Conley Terminal project allows Massport to significantly increase the import and export of cargo and will accommodate approximately 100,000 additional containers. Coastal Marine Construction LLC was brought onto this three-phase project in late 2018, and recently completed the third and final phase of pile driving in February.
“We started on [the] first phase with general contractor, which included the installation of a 1,200 LF long, king pile bulkhead and the demolition of all of the marine structures that were in the footprint of where the new pier was going,” said Eugene Kelley, estimator at Coastal Marine. “Then, when D.W. White won the additional phases of the project, we went right from installing the bulkhead wall to driving the piles.”
Based out of Canton, Mass., Coastal Marine specializes in marine and heavy civil construction and is considered to be one of the best when it comes to pile driving, earth support, bridge, pier and deck construction, and demolition. The company takes great pride in its proven track record of delivering projects of all sizes on time, safely and within budget. The company has also established a strong working relationship with Massport and works on up to 80 per cent of the port’s marine work.
The deep foundation of the Conley Terminal project included the installation of almost 900 26- and 30-inch diameter steel pipe piles that were between 60 and 105 feet in length. Some of the piles were driven from land, but the majority were installed from the water by barge.
The piles were driven a few feet into the rock where overburden was present, with approximately 100 of the 30-inch diameter piles along the face of the pier having drilled rock sockets where overburden was minimal. The inshore and outshore crane beams and pile caps are cast-in-place pieces and lock together to provide the framework for the deck, which consists of 870 precast deck panels with a cast-in-place topping slab. The pier work also includes a new gantry crane running rail, marine bollards, fenders, drainage, water and electrical installed on the deck.
When driving the piles, Coastal Marine made use of the Berminghammer L27 crane-mounted Vertical Travel Lead (VTL) system. When paired with Coastal Marine’s cranes, Berminghammer’s VTL system combined the fast and accurate positioning of a fixed lead system with the ability to adjust the height of the lead base up and down.
“Although I had seen them around a lot, this was our first experience in using the Berminghammer lead system on a job,” said Kelley. “Considering the size and scope of the Conley Terminal project, we saw an opportunity to try them out. It’s a good system that’s rugged and heavy, and it worked out beautifully for us; Berminghammer really is the next level lead system for next level projects.”
One of the benefits of the Berminghammer VTL system is that it proved to be very rigid without much ‘slop,’ allowing Coastal Marine to drive piles without the need for any falsework. In addition, Coastal Marine equipped the lead system with a separate Global Positioning System (GPS) that the crane operator could access via computer screen, moving the leads to a precise point as indicated by the GPS and further speeding up production.
“The GPS calibrates the exact centre of the pile so that the operator has a spot on his screen where he sticks that pile, which saved us a bunch of time and money over the course of the project,” said Kelley. “We believe Berminghammer’s system saved us about half the time that it would have taken if we used another system.”
Coastal Marine had two Manitowoc 2250 cranes and a single Manitowoc 4100 crane working on the Conley Terminal project, all of which were used to drive piles on the water and from shore. The company also had a Manitowoc 4000 that worked on the barge. When transitioning from land to water – and vice versa – the company would crawl the Manitowoc 2500 cranes (fully loaded with VTL leads and spotter) from the pier onto the barge, which proved to be a feat unto itself.
“Our cranes weighed more than 900,000 pounds each and, to move them off and on the barges, we would place steel mats on both the barge and the pier, and then wait for when the tide was right to crawl it across,” said Kelley.
The challenges facing the project were primarily related to weather, wind and a large number of obstructions. Fortunately, the obstructions could be worked around and Coastal Marine drove piles from the shore during most of the colder winter months. Another hurdle for the project was the lack of overburden in the water, which made it difficult to keep the piles in place.
“The sloping rock with no overburden made it tough to keep the piles within tolerance,” said Kelley. “But the Berminghammer lead system we had kept us pretty stable. The leads aren’t fixed to the boom and can travel vertically, going up and down independently to the angle of the boom, and this made it much easier to drive the piles while also taking into account the 10-foot tides. If the tide was high, we would just travel the leads down; the Berminghammer system just proved to be great for the job we were doing.”
Coastal Marine believes strongly in encouraging a safe work environment for its workers. The company maintained a high level of safety oversight during all stages of the Conley Terminal project and held constant daily safety meetings, which helped result in no lost time due to injuries throughout the project’s lifecycle. In addition to its health and safety efforts, Coastal Marine also remained focused on sustainability over the course the project, such as in the use of silt curtains and debris booms, to help preserve the immediate environment. To further protect marine wildlife in the area, the company also enlisted fish observers during blasting and used a sonar noise system to frighten fish out of the area where it was working.
“When we were driving the piles, we also used bubble curtains, which was something new for us,” said Kelley. “The system pushes compressed air through an underwater curtain system and puts up a bubble screen – or wall – so the fish would stay out of the space where we were impacting the piles.”
The Coastal Marine team is made of experienced industry professionals with more than a century of combined experience in the marine construction business and, as such, the company is able to complete much of its work in-house. In the case of the Conley Terminal project, Coastal Marine self-performed virtually all aspects of the job, including building slicing beds and welding all of the approximately 600 pile splices on site.
“The Conley Terminal project represented large undertaking for us here at Coastal Marine, and it required a large and disciplined self-performance staff to successfully complete,” said Kelley. “By having our crews doing all the work, we are able to circumvent many of the common trade issues. And while we may not be a big company, we are always all-in with each and every project we take.”