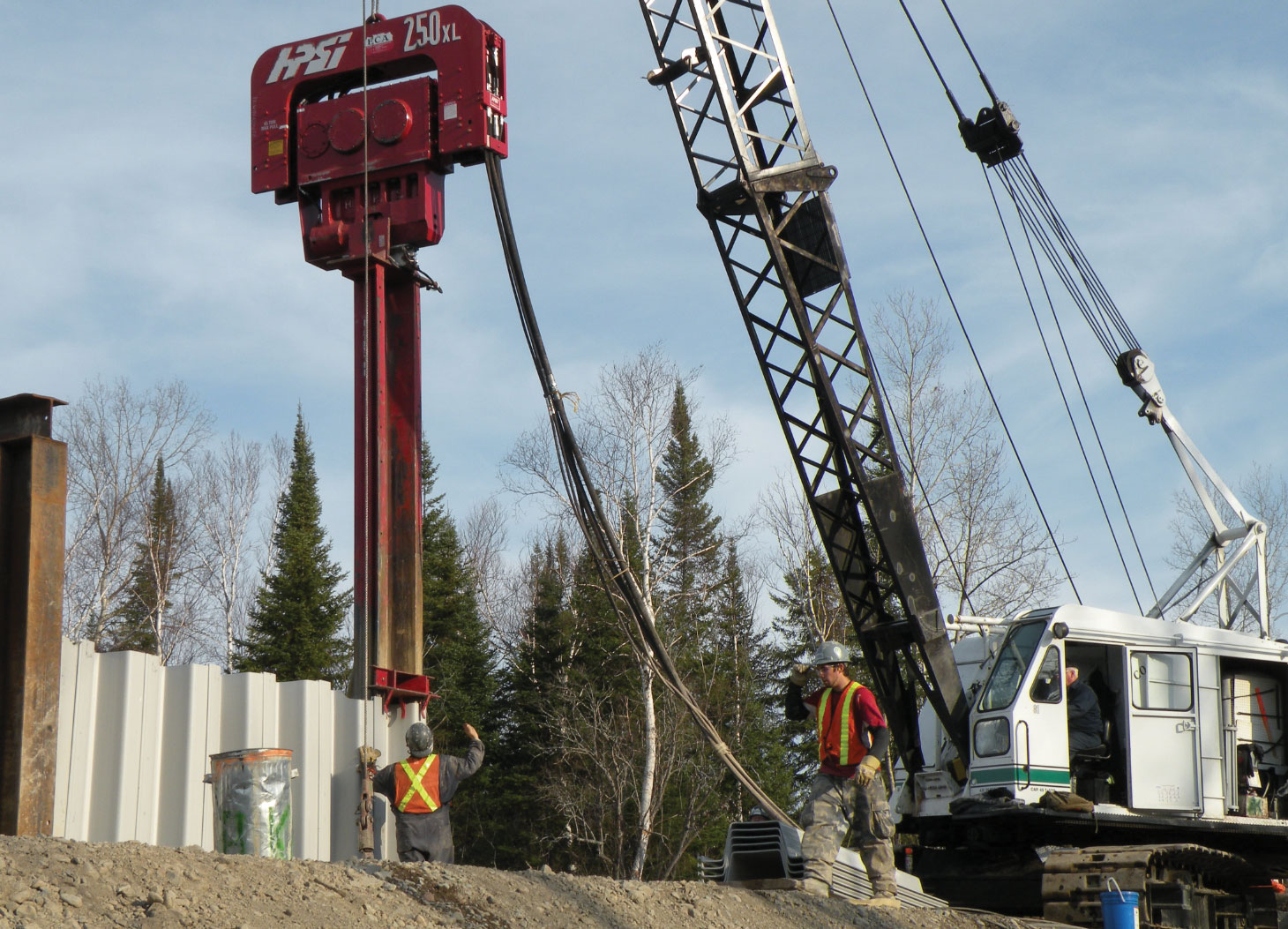
There is a secret at the Jefferson Memorial in Washington, D.C., that isn’t visible to the untrained eye. Tourists who visit often marvel at the 19-foot-tall statue of Thomas Jefferson, holding the Declaration of Independence and staring out over the waters of the Tidal Basin.
But if they looked closely at the edges of the property, they’d see a different installation – one designed to safeguard the shoreline from the harsh winters and blistering summers that strike the U.S. capital. Larry King, vice-president of sheeting at CMI, says ShoreGuard vinyl sheet piling replaced traditional materials that were used to protect the shoreline around the monument.
“Due to the harsh environmental conditions and the need for a low-maintenance, long-lasting solution, ShoreGuard far outperformed the previous materials by offering a durable corrosion-resistant alternative,” said King, adding that the installation at the monument was efficient because of the product’s lower weight and ease of handling. “It has continued to protect the site from erosion with minimal maintenance over the years,” he said.
Three decades of experience
For over 30 years, CMI (formerly Crane Materials International), has been developing alternative materials for infrastructure projects. Transitioning from traditional wood and steel, CMI pioneered ShoreGuard vinyl sheet piling in the early 1990s. Since then, the company’s products have gained widespread acceptance, including endorsement by organizations such as the U.S. Army Corps of Engineers. Its product line has expanded to include UltraComposite sheet piles and PileClaw installation equipment.
Steve Hargrave, director of innovation at CMI, says there are growing challenges around erosion and environmental changes, particularly in the context of climate change – and their products are designed to tackle the issue head on.
“These systems are highly effective in erosion control, protecting infrastructure and shorelines by acting as barriers that prevent soil displacement and mitigate the impact of rising sea levels, extreme weather and coastal flooding,” he said.
Demand for environmentally friendly solutions
Keith Coleman, CMI’s director of engineering, says there has been a shift in both focus and demand towards long-lasting and environmentally friendly solutions. The move towards synthetic materials like ShoreGuard and UltraComposite sheet piling is driven by their longer design life and superior resistance to corrosion, especially in harsh marine environments.
“Synthetic sheet piles require less energy to transport and install compared to traditional steel, contributing to lower overall emissions,” he said, adding that both government and private-sector clients are prioritizing materials that reduce carbon emissions during production and installation.
Differences in materials
Comparing ShoreGuard to traditional materials, David Olvey, regional sales manager – international at CMI, says there are several advantages.
“It is lighter and easier to transport, allowing for four times as much material per truckload, which greatly reduces the carbon footprint compared to traditional materials,” he said. “It’s far less disruptive to the jobsite and the surrounding environment.”
“Synthetic sheet piles require less energy to transport and install compared to traditional steel, contributing to lower overall emissions.”
Keith Coleman, CMI
When it comes to longevity, it also significantly outperforms traditional materials, says Olvey. “Unlike wood, concrete or steel, ShoreGuard does not rust, rot or corrode,” he said. “This durability leads to lower maintenance costs and fewer replacements, making it a cost-effective and sustainable solution for long-term soil stabilization and shoreline protection.”
Additional innovations
One reason it works so well is CMI’s patented I-Beam Lock. Hargrave said it “stiffens the lock mechanism, making it more rigid and balanced, which directly improves the driveability of the sheet pile during installation.” This feature ensures a more stable installation, reducing potential issues like misalignment or deformation. Advanced UV protection and XCR Technology further contribute to the product’s durability, he says.
“Exposure to sunlight can cause materials to degrade over time. The advanced UV protection embedded in ShoreGuard ensures that the sheet pile retains its structural integrity and appearance despite prolonged exposure to sunlight.”
XCR Technology provides additional layers of protection against environmental factors and allows for customizable finishes, including wood grain and concrete looks. Dave Trzeciak, northeast regional sales manager at CMI, says there’s a reason ShoreGuard is often chosen for high-profile projects. “(It) has the longest history in the industry, making it a trusted partner for large-scale, high-stakes projects,” he said. “We have the most robust engineering team in the business, and our products are backed by ASTM standards and rigorously evaluated by the Army Corps of Engineers.
“We own the entire manufacturing process, ensuring full control over the quality of every sheet produced.”
Adapting to climate change
With climate change increasing the frequency of extreme weather events, ShoreGuard helps communities and infrastructure adapt to these challenges, says Coleman, who highlighted the product’s quick response time in emergencies.
“Unlike traditional materials that may require weeks or months to deliver, ShoreGuard can be deployed in days.” Coleman recalls an instance where a customer in Australia flew tons of ShoreGuard sheet piling on a cargo plane to address an urgent need. The product is also engineered to withstand severe weather conditions.
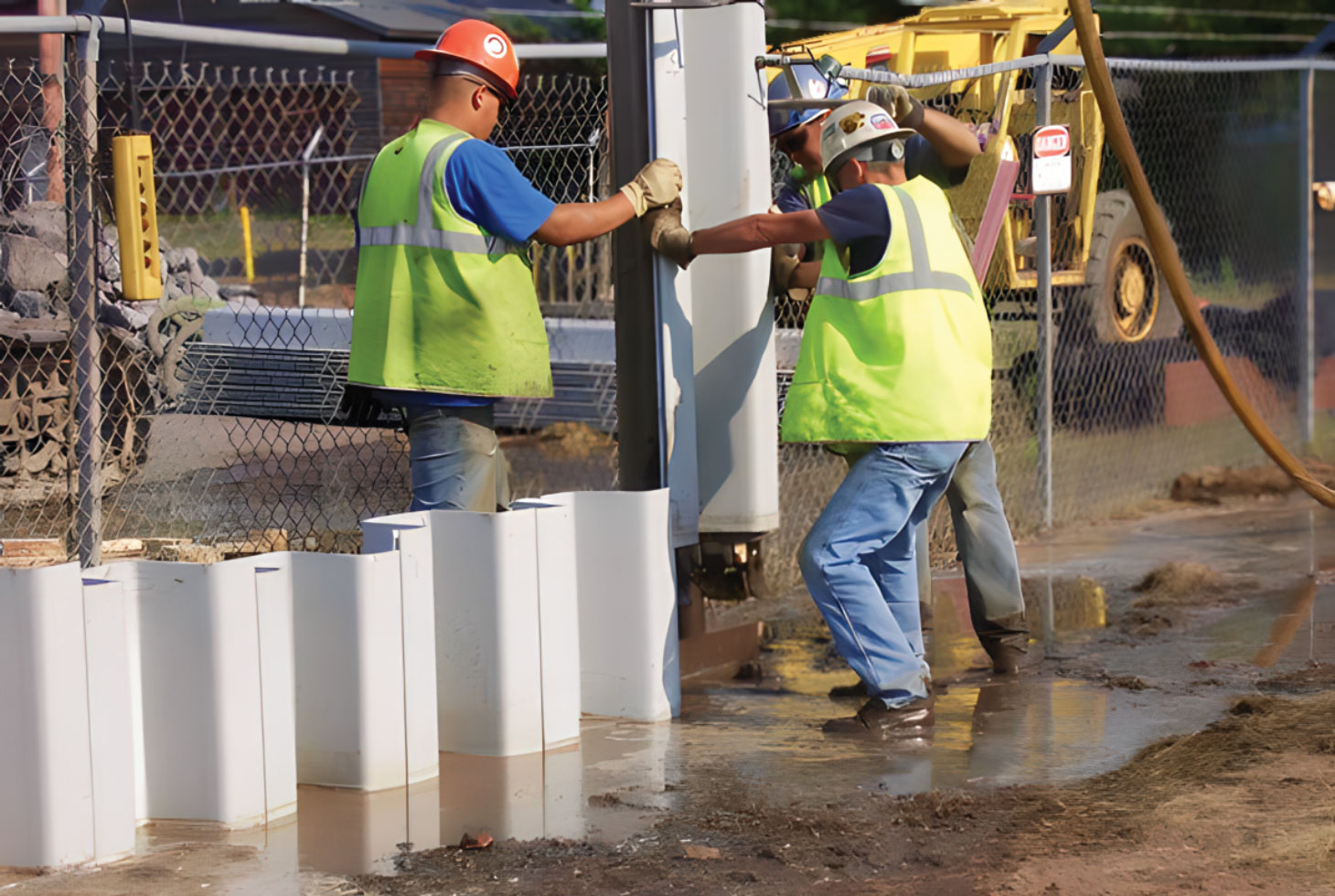
“Its robust design enables it to protect against 100- or even 500-year flood events,” Coleman said. “By offering a low-maintenance, long-lasting solution that can be quickly deployed, ShoreGuard helps communities bolster their resilience against the growing impacts of climate change.”
CMI is also focused on using recycled materials, with more than one per cent of all recycled PVC in Canada and the U.S. being used in ShoreGuard production. “We recycle plastic, packaging materials, and water in our manufacturing process,” said Olvey.
Moreover, ShoreGuard is inert and does not leach harmful chemicals into the environment, he says. “Unlike wood, which often requires preservatives linked to health issues, ShoreGuard is a safer option for use in waterways,” Olvey said.
Overcoming skepticism
Implementing new and different solutions isn’t without its challenges. Hargrave points to concerns around the variability of recycled materials and the skepticism with using plastic sheet pile for structural applications.
“We’ve invested in refining the process to ensure that the recycled content used in ShoreGuard is of consistent, high quality,” he said. “By eliminating variability, we ensure that the product meets strict performance standards.”
He also says there’s a need to educate the engineering community. “Many experienced engineers have traditionally relied on steel, concrete and wood,” Hargrave said. “We’re proactive in informing engineers about the capabilities of ShoreGuard and focusing on educating them about the advantages of vinyl sheet piling.”
The company’s wide variety of profiles ensures that their sheet piling solutions can meet the specific needs of any application. “This versatility has been key in overcoming skepticism and broadening acceptance of our products,” Hargrave said.