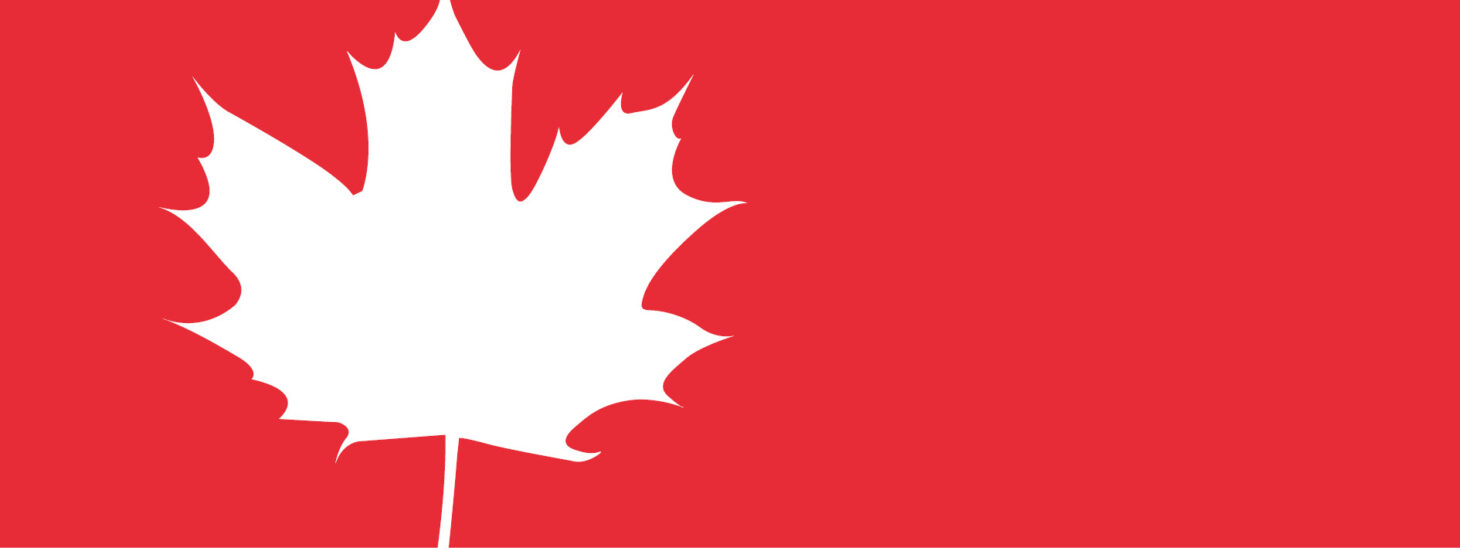
Vancouver Canucks fans and downtown locals will soon be able to enjoy expanded amenities when they visit the Rogers Arena, including the indispensable addition of new restaurants, bathrooms and parking.
However, Vancouver residents and workers may be even more excited by the upcoming increase in rental housing and office space that will be provided by the three new, mixed-use high-rise towers under construction surrounding the hockey arena.
Canucks fans and residents may not realize how difficult it was to build the Rogers Arena, which was squeezed between the existing Georgia Street and Dunsmuir Street Viaducts. Now building contractors face the greater feat of constructing three high-rise towers within even tighter jobsites – requiring a construction “hat trick” that hockey fans will appreciate.
Construction of the 31-story South Tower has been particularly demanding since this triangular-shaped tower is being wedged between the southern wall of Rogers Arena and the elevated Georgia Street Viaduct on one side, and the at-grade Pacific Boulevard and Griffiths Way on the two other sides. When complete, this high-rise will include five levels of underground parking, more than 200 rental units and multipurpose facilities.
Matcon Canada MESL Group of Companies recently tackled the challenging excavation, shoring, foundation, site remediation and demolition work for the South Tower. Building next to existing structures always requires special care to ensure that the structures don’t move, so a large part of Matcon’s work focused on careful stabilization of the adjacent foundations for the arena, viaduct and roadways. They used a range of underground solutions, including micropile foundation support and a jet-grout cutoff/shoring wall, to ensure a dry and stable shoring system for the tower’s underground parking garage. Construction was further complicated by a very constrained jobsite, intricate layout for shoring under the viaduct, internal bracing, buried debris, underground utilities, contaminated soil and groundwater issues. The complex shoring system was designed by a local geotechnical company GeoPacific Consultants Ltd.
Micropiling for viaduct foundation support
Construction of the South Tower extends to the property line on all three sides of the jobsite, so the neighbouring structures needed additional support during excavation and during the year with more required to build up the parking structure to ground level. Under and adjacent to the Georgia Street Viaduct, with 30 feet of clearance, micropiling was critical for stabilizing the three existing viaduct pier foundations.
Although Matcon had rigs capable of drilling the required borehole size and depth, they were concerned about performance. So they spoke with Champion Equipment Company, who supplied them with a versatile Soilmec SM-14 drill rig with a double rotary head.
Using the SM-14 rig, they installed 36 micropiles around the three Georgia Street Viaduct piers with 12 evenly-spaced micropiles encompassing each pier. The micropiles had a diameter of eight inches and depth of approximately 83 feet. Their entire length was reinforced with 2.5-inch 127/155 ksi cold-rolled double corrosion protected threadbars. The top 50 feet of each micropile was also reinforced with a six-inch diameter, 0.5-inch thick pipe in order to minimize the horizontal sheer force from the parking lot excavation. The micropiles were filled with Microsil anchor grout for the entire depth.
Real-time monitoring devices – such as vibrating wire spot-weldable strain gauges, bi-axial tiltmeters (MEMS) and high precision laser dis- placement meters (LDMs) – were used to measure any potential movement of the viaduct piers. Traditional precision surveying was also used to confirm the automated monitoring system. The micropile foundation support was very successful and none of the piers showed any movement beyond the allowable limits.
Jet grouting for soil stabilization and waterproofing
Double fluid jet grouting with tieback anchors were used around the entire jobsite perimeter, in order to provide ground stabilization at the shoring face. This was needed because the subsurface of the jobsite was composed of a fill layer overlying native wet clay deposits with a dense glacial till beneath. The top fill layer was typically a 30-foot deep, loose mixture of sand, buried debris and organics that had been added during the earlier reclamation of the nearby False Creek, so the jet grouting had to advance into the dense glacial till.
Matcon used double jet grouting, because they’ve found it to be the most practical and cost-effective technology for past projects with similar ground conditions. Double jet grouting uses a mixture of high-pressure grout shrouded by air to erode the in situ soil and form a cylindrical grout column as the drill rods are rotated and extracted from the bottom of each drill hole. Matcon worked closely with Sea to Sky Geotech Inc. to establish the optimal jet grouting parameters and mix design for the project.
The South Tower project consisted of approximately 330 jet grout columns with a diameter of three feet and depth ranging from 25 feet to 50 feet. The entire job required 14,000 linear feet of drilling for the columns. The majority of these columns were installed using a Soilmec SM-30 rig with a 4.5-inch rod, jet grout pump and mixer. Under the viaduct, the columns were installed utilizing another rig with adding and removing jet grout rods due to the limited headroom. A primary/secondary sequence was used in which every primary column contained a reinforcement element embedded at least 6 feet into the glacial till. These reinforcing elements were “wet set” through the jet grout columns and driven into the till layer utilizing an excavator mounted sonic side grip attachment.
Using the Soilmec SM-30 enabled Matcon to apply additional pressure when drilling and encountering obstructions. Each jet grout column was installed with a single stroke and without needing to add or remove rods during the drilling and jetting operations.
Jet grouting was also used to provide a temporary water cut-off. The groundwater levels sit about 10 to 12 feet below grade at this jobsite with additional minor tidal fluctuations due to the proximity of the False Creek shoreline 400 feet away. As a result, significant groundwater could seep through the bottom of the fill layer in the southern area of the site. Thus, a deep groundwater cut-off wall around the entire perimeter had to be embedded into the glacial till for excavation. This cut-off wall performed magnificently – tight, impervious and strong.
Anchoring with tiebacks
The excavation face was right next to Pacific Boulevard and Griffiths Way, so Matcon Canada installed tiebacks below the roads to support the excavation and prevent damage to the roads. Typically, nine to 11 rows of tiebacks were installed with vertical spacing of about four to six feet between them. A combination of solid threadbars and hollow core injection anchors were installed at an angle varying from five to 45 degrees and lengths of 20 to 80 feet. The hollow core injection anchors were installed using pressure-grouting techniques with a high-pressure (1,400 psi) grout pump. Some tiebacks and soil nails were also used along the Georgia Street Viaduct and Rogers Arena wall. Throughout the perimeter,horizontal shotcrete walers were used at each row of tieback anchors within the jet grouted areas. Conventional shotcrete with underpinning was used below the jet grouting in the dense glacial till to the base of excavation.
After the micropiling was copleted, the multipurpose Soilmec SM-14 rig was also utilized to install the necessary cased anchors. The SM-14 proved to be an ideal rig for tie-back and anchor drilling with its kinematic motion 90 degree mast articulation.
Since the jet grout columns did not reach the entire depth, a shotcrete wall was typically installed below the columns to a depth of about two feet below the top level of the parkade slab to provide further soil and anchor tie-back support. Shotcrete underpinning was also used along the foundation of the Rogers Arena southern wall.
The entire jobsite included the installation of 50,000 feet of tie-back anchors, 5,000 feet of shotcrete walers and 8,500 square feet of combined four-inch thick shotcrete face and 12-inch thick underpinning.
Protecting the environment
Working in a constricted urban environment added environmental issues to Matcon’s construction challenges. For instance, any groundwater or rainwater had to be pumped to a mechanical filtration system and treated for pH and total suspended particles prior to discharge into Vancouver’s storm system.
The upper fill material also contained areas of contaminated soil, which had to be segregated and removed to a permitted treatment facility throughout all excavation and shoring activities. During the bulk excavation, the site was split into a layered grid pattern and environ- mental personnel monitored all soil removal. Integration of these remediation procedures with daily activities was completed under the direction of Matcon’s Remediation entity to ensure no loss of schedule.
Matcon has completed its demolition, remediation, micropiling, jet grouting, anchoring and excavation work on the Rogers Arena South Tower and construction of the footings began in February. Using versatile and powerful Soilmec rigs, Matcon was able to overcome the challenges of a very constrained jobsite with limited overhead under the viaduct, difficult subsurface and groundwater conditions and environmental issues.
Dan Hunt is project manager at Matcon Canada MESL Group of Companies. Craig Berninger is sales associate at Champion Equipment Sales, LLC and Soilmec North America. Soilmec manufactures drilling and ground engineering construction equipment. Berninger can be reached at craig@championsales.net.