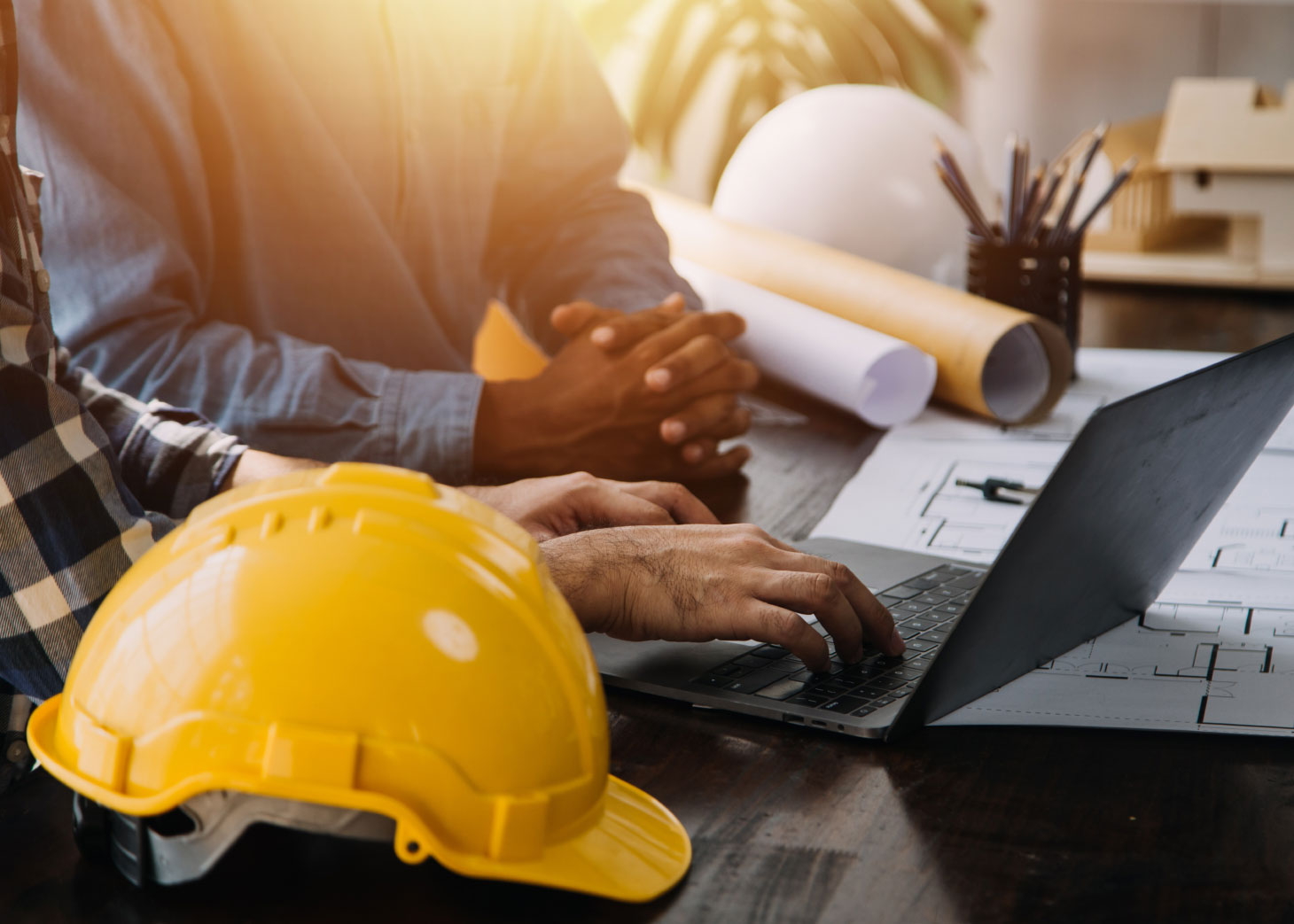
The most crucial phase of any construction project is pre-construction planning. Due to the significant demand for fast construction, new technologies and complex structures, pre-construction plays a pivotal role in a project’s duration and provides a better assessment of its schedule and cost. It offers flexibility through early planning, design, communication and co-ordination between different stakeholders. It is the key for any project’s success.
Before starting any project, project managers should conduct a feasibility study to account for potential risks, constraints, costs and complexity of construction. Pre-construction is an integral part of project planning and allows stakeholders to make any modifications and manage risks upfront. Thus, design-engineering is crucial during this phase. An initial site survey addresses soil reports, terrain studies and contractor benefits associated with the report.
Pre-construction aids project planning, contractors and stakeholders by using modern planning techniques like the critical path method, which allows identification of project tasks and proper allocation of resources. Other techniques used are data analytics and predictive modelling – based on historical data, virtual design and construction, and building information modelling (BIM). These techniques give a clearer picture of the completion date, cost estimation, unknown variables and any value engineering needed. By leveraging these modern planning techniques, the pre-construction phase becomes efficient, streamlined and economical.
The bid design
Pre-construction starts with the client’s conceptualization of the project. This defines preliminary goals, objectives, requirements, potential risks and overall benefits of the project. The client starts a plan of action to finalize the project’s permits and bid documents.
Most pre-design modelling, analysis, testing requirements and additional interactions are taken at the bid design phase to visualize and estimate proper project co-ordination. Initial bid designs are welcomed by other design consultants to study viable and efficient strategies related to the contractor’s ideas.
Larger projects involve multiple design iterations with different levels of bid design submissions, such as pre-initial design package (or 10 per cent design package) with minimum design and analysis; 30 per cent bid design and analysis package, with finalized structure and other parameters from the pre-initial design package; 60 per cent bid design and analysis package that is helpful for bill of quantity, purchase of machinery and technologies, logistics and pre-site preparation; and 90 per cent permit and bid design package to get needed approvals. These steps help reduce modifications into the bid phase and allow more flexibility before construction starts.
Incorporating all stakeholders early in project planning provides valuable input and enhances communication and co-ordination during project execution. Most contractors assess the submitted bid designs, leveraging their skills and resources to establish a suitable budget and address any suggestions during the bid phase. This process facilitates the exploration of new technologies, the acquisition of advanced machinery for improved construction outputs and the use of sustainable materials to extend the project’s lifespan.
Modern pre-construction technologies
The preliminary feasibility study, survey planning, environmental constraints and governmental regulations are studied to evaluate the challenges and overall approach of the project. After finishing the initial proposal of project alignment and requirements, a team of engineers, architects and other design professionals collaborate to start bidding on design plans and specifications.
The industry is leveraging advanced technologies to enhance and improve pre-construction planning. Geographic information systems (GIS), light detection and ranging (LiDar) surveys, drone inspection and BIM are widely used early in pre-construction. These technologies study, model and analyze virtual structures in real time with proper data and information.
BIM fully integrates 3D modelling with ground conditions and survey snapping, providing better visualization, co-ordination and project optimization. GIS, LiDar surveys and drone inspection can analyze real-time ground site conditions, mapping the layout of structure orientation and existing hazards. Cloud-based platforms allow all stakeholders to track the project’s progress in real time. These platforms provide efficient communication and design processes for larger projects.
Most pre-construction teams make design-construction-bid specifications to streamline the project and to use as a reference for future projects. They use new software like Procore and Primavera to track the schedule, collaboration of all stakeholders and construction progress.
Pre-construction in the geotechnical field
Early engagement of geotechnical engineers, drilling contractors and foundation experts helps mitigate potential geotechnical challenges. Most new projects include pre-assessing the geotechnical baseline report with all site measurements, required soil testing, boring exploration, ground improvement recommendations and suitable foundation systems for project structures. For any successful project execution, pre-geotechnical determination and design are important and include the site geotechnical report, bid level foundation and geotechnical contractor planning.
Sometimes, pre-fabrication, pre-testing and prototype modelling in a lab or site increase productivity and optimize construction time and labour costs. Instrument monitoring, pile testing and integration at an early stage of geotechnical construction allow structures to be incorporated and re-designed with proper data.
In major infrastructure projects, many geotechnical stakeholders such as material suppliers, designers, geologists, contractors and testing analysts collect pre-bid information through specification and site surveys. This avoids any major risks associated with geotechnical construction and can be mitigated at the pre-construction phase. Ground improvement techniques like vibro-stone columns, stabilizing soil and grouting are used when natural soil conditions at the project site are not suitable for construction, and are useful to get economical and efficient foundation structures.
Pre-construction planning is more helpful in deep excavation, shoring and marine construction projects where there will be risks and complexity in the construction. Proper documentation and geotechnical design ensures the durability of the foundation structures and minimizes any costly repairs in the future.
Every project scope should focus on pre-construction to be successful. The construction and post-construction phases are better controlled when proper pre-construction planning is executed. Pre-construction gives an idea of resource allocation, cost optimization, project schedules, design modifications and any improvements on the project before construction. This process should give the construction team and client a better understanding of what to follow for successful completion. It also serves as data collection and a base for any future project with similar construction.