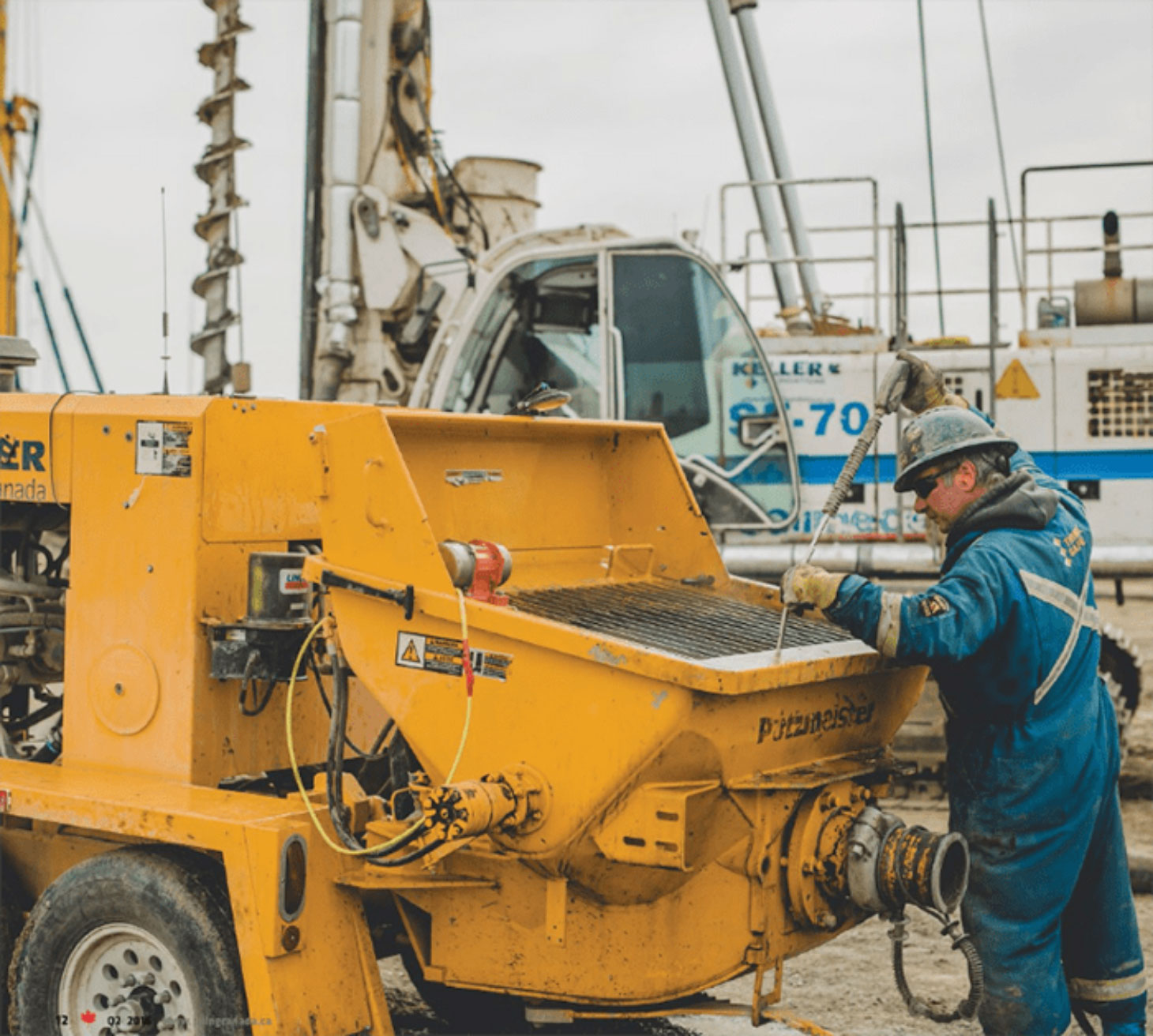
The piling industry is much safer than it once was. Dennis Bell, HSE manager for Northstar Energy Services Inc., recalls how different things used to be, even around the turn of the millennium.
“Now, we have designated pile driving units and hydraulic hammers,”he said. “Riggers used to climb the leads, so you had fall issues. Now, if something happens, [the clients supply a] zoom boom platform; we don’t climb leads anymore. It’s nice to see that the industry has come to a higher level of safety.”
But even with the advances, there are still concerns.
“The piling construction industry continues to have one of the highest WSIB premium rates in industry [twelfth highest out of 155 rate groups in Ontario],” said Paul Belair, MBA, BASc, CRSP, CHSE, the director of health, safety and environment for Keller Canada. Among the common industry hazards, he lists musculoskeletal injuries, trips and falls, contact with mobile equipment and rigs, injuries from equipment contact with live utilities services and entanglement from rotating parts.
Know the common hazards
In fact, the risks are “pretty obvious,” says Owen Langton, project manager for Henry Foundation Drilling Inc. “Large equipment, operating in a con ned area…it makes for a very busy site with a lot of heavy equipment, all in a tight, con ned space. Your crew is performing heavy manual labour to rather exacting standards; the work shifts are quite long,” said Langton.
“One [risk] that stands out, of course, is falling objects. It takes a lot of energy to drive a big pipe into the ground; there’s a very high potential for things to break off and fall,” said Bell. Less obvious is the noise factor, and not just from sheer decibel levels, he says. “In the pile driving industry, [the hazard is] impulse noise or impact noise.”
Site conditions
“We’re always the first contractor there and the last to leave, so the sites are never in the best condition,” said Willis La Rose, HSE director for Doublestar Drilling (1998) Ltd. To avoid the incidents caused by slips, trips, falls, open holes, pinch points and related hazards, “we have what we call LMRA: last minute risk assessment, a quick 10- to 15-second visual assessment of the work zone.”
“Working conditions always play a key factor,” said Ben Brockmann, CHSO, safety manager for Bermingham Foundation Solutions Limited. “When you’re [using] large cranes, you have to have a proper pad for your crane. It’s also critical to ensure all your equipment – rigging, cranes, slings – is in good condition and that it has sufficient capacity to do the job.”
Learning from mistakes
Despite these everyday dangers, the most serious types of accidents in the piling industry are rare enough that everyone remembers them for years. Such a case was the 2011 rig collapse on a TTC extension project on the York University campus in Toronto that killed a 24-year-old worker and injured others. The Ministry of Labour determined that inadequate site preparation and operation of equipment on too steep a slope were among the causes. No matter the severity of the outcome, every incident offers an opportunity to learn how to prevent a reoccurrence.
“Best practices after accidents are based around lessons learned,” said Belair. “After an event, the circumstances of the event are investigated. Root-cause models are then used to investigate the failure or multiple failures that led up to the accident. Once these are identified, the investigation team will review the findings with subject matter experts to find appropriate controls and best practices to prevent a reoccurrence. Keller actively participates with industry associations where the findings of events are communicated and discussed to find and share solutions to ensure everyone goes home safe. We also have an extensive network within Keller that assists us with cascading lessons learned down to our workforce.”
It’s critical to know exactly why any accidents occurred.
“The method that we try to use is that you ask ‘why’ five times,” said Brockmann. “Why was there an accident? Why did the crane tip over? Why wasn’t the work pad up to snuff? Why wasn’t it properly prepared? Why wasn’t the standard enforced? It’s just trying to get underneath the surface to the root of the problem. A root-cause analysis is such a common term, but it really is about trying to get down and eliminate the actual causes of the problem.”
Conducting an analysis
Learning from an incident involves losing time from the job, but offers incalculable payback.
“Almost invariably, with anything of any consequence you shut the site down to bring everybody together and make sure there’s no reoccurrence. Then an investigation is really a big part of it. You need to go and have a look at what caused the accident with somebody impartial to the incident; it allows you to revise the protocols for the site,” said Langton. “When you talk to your clients, you have to be upfront and deal with the problem that occurred. With both employees and clients, you have to reassure them that you’re going to be putting the systems in place that are going to prevent another accident occurring.”
Accidents happen
La Rose recalls an odd situation in which a person walked into an open hole and wasn’t found until almost an hour later.
“You never leave an open hole,” he said. “All my supervisors are trained in accident investigation; they will call me, and we will go down to the site. Very often, the supervisor is quite capable of running the situation without my involvement.”
“One that stands out for me is a pile driver that tipped over. There was high potential for very serious implications,” said Bell. “As it turned out, the only loss was the unit itself. The learning from that was about knowing your equipment. In this case, it was a rented piece of equipment, not completely familiar to the company. The other thing is there is no requirement for a journeyman certification for a designated pile driving unit operator in Alberta.”
Safety standards
As Bell points out, unlike some other parts of the construction sector, the piling industry does not have its own complete set of national standards. is is beginning to change. Ontario has become the first jurisdiction in Canada to add explicit training requirements for drill rig operators into its health and safety legislation. As of July 1 of this year, the new requirements under the Occupational Health and Safety Act will be in effect for all workers operating rotary foundation drill rigs.
Meanwhile, as detailed in Quarter 4 2015 issue of Piling Canada, the Northern Alberta Institute of Technology (NAIT), the International Association of Foundation Drilling (ADSC-IAFD) and the Western Canadian chapter of the ADSC are collaborating on the development of a drill rig operators training program that will be available online. Eventually, says Kevin Sharp, general manager of Sharp’s Construction Services (2006) Ltd. and president of the Western Canadian chapter of ADSC, candidates will be able to use this training to prepare for Ontario’s Ministry qualification.
Also underway is a joint venture between ADSC’s Western and Eastern Canadian chapters to introduce a CSA standard for the industry. A draft document for consideration to becoming a Canadian Standard for Drilled Shafts has already been prepared in consultation with industry stakeholders.
It is intended as the first step towards a common working safety standard for the installation of drilled shafts in Canada, to align the industry and improve the overall safety and performance of the companies involved in the foundation construction process. The standard would address proper procedures for such job tasks as site investigation, permitting, acquisition and maintenance of materials and equipment, use of pressurized lines and hoses, and work near power lines, water and transport routes, among others.
Working on a Canadian national standard
“We’re one of the only industries in Canada that doesn’t have to build to a standard,” said Sharp. Following the release of an American National Standards Institute (ANSI) spec for the safe installation of drilled shafts, he says, the ADSC Western Canadian chapter decided to use it as a basis for a Canadian standard.
“Our safety committee went through the ANSI standard, [comparing it to] our federal regulations to ensure that we would be in compliance,” he said. “Then we went to the CSA [Canadian Standards Association] to see whether we could build this spec.”
The CSA process requires a workshop that comes with a price tag of $25,000, which will be shared by the ADSC’s Eastern and Western Canadian chapters. The next step, formalizing the standard, would require a further industry investment of a figure between $125,000 and $250,000.
“This country is getting smaller by the day as companies get larger,” said Sharp. “It’s a benefit to have a standard that’s recognized and built by the industry to protect the public, the people working on the site, the environment and the owners; it’s a win-win for everybody.”
Building a safety culture
While these new additions to the safety toolkit are being developed, many companies already perform to high standards in building a culture of safety. But in order to achieve this, safety has to be a priority at the highest level, and it must be integrated into every facet of the company.
“If [safety] is not supported from the very top, it will not happen in any organization; if it is strongly supported, you cannot help but win,” said Bell. Top-down support isn’t just a budgetary matter, he adds, but must include “the true commitment from the person. If the president walks onto the site without the vest and the glasses and the PPE [personal protective equipment], he’s just shot the safety manager in the foot.”
Belair agrees, and Keller Canada mandates safety throughout the entire organization.
“One of the things that Keller Canada does is demonstrate a commitment, leadership and effective participation to ensure the successful implementation of our occupational health, safety and environment management system,” said Belair. “This commitment to health, safety and environment is integrated throughout our entire organization. Nothing is more important than the health, safety and wellbeing of our employees, subcontractors, clients and visitors.
“Our occupational health, safety and environment management system standard (OHSEMS) for Keller Canada is based on the BS OHSAS 18001:2007 Occupational Health and Safety Management System standard and ISO 14001:2004 Environmental Management Standard,” said Belair. “The OHSEMS provides the structure for occupational health, safety and environmental management system requirements. The company has taken a proactive approach to ensure all our regions are OHSAS 18001:2007 and ISO 14001:2004 certified by the third quarter of this year. We are also ISO 9000 certified, and we will be the only piling and geotechnical construction company in North America with all three standards.”
One of the most critical aspects of a strong safety culture is that employees feel empowered to speak up when they feel something is amiss.
“It is absolutely crucial for companies to have a strong policy that if any worker feels something is not safe or feels they don’t know how to proceed safely, they need to stop, engage the supervisor and ask for direction,” said Brockmann. “At Bermingham, we call that the safety huddle. Any worker at any time can call for a safety huddle. Our primary goal is to have our workers thinking critically about hazards and their control, as opposed to thinking by instinct or habit or routine.”
Training is another key link in the safety chain.
“First and foremost, you have to engage the workers,” said Brockmann. “There are so many safety programs out there that they’re not only overwhelmed, but they’re just tuned out to the material. As opposed to telling them what to do, it’s asking them to think about the job they’re doing, what the hazards may be and how they plan to control them.”
Northstar and Sharp are among the Canadian companies owned by Quanta Services Inc., which is based in Houston.
“They have a fabulous training and safety culture; they spend millions of dollars on safety training. They even have a place called the Lazy Q Ranch, where they bring people in [for safety training in simulated job situations],” said Sharp.
At Doublestar Drilling, “we’ve introduced a BBS [behavioural based safety] system,” said La Rose. “Person by person, I train them in BBS, then they observe one of their coworkers. You’d be surprised what [can be noticed and improved] just standing back and observing for five minutes. We’re also introducing a mentorship program, because there are always new people coming into the industry.”
For some, safety is a passion, but for others, it’s personal. Sharp will never forget an accident that gravely injured his uncle about 10 years ago. “As far as a legacy for me,” he said, “that would be to do something in the name of my uncle to make the industry safer, so that nothing like that ever happens to anybody else.”
It’s an aspiration that everyone in the industry can be part of.