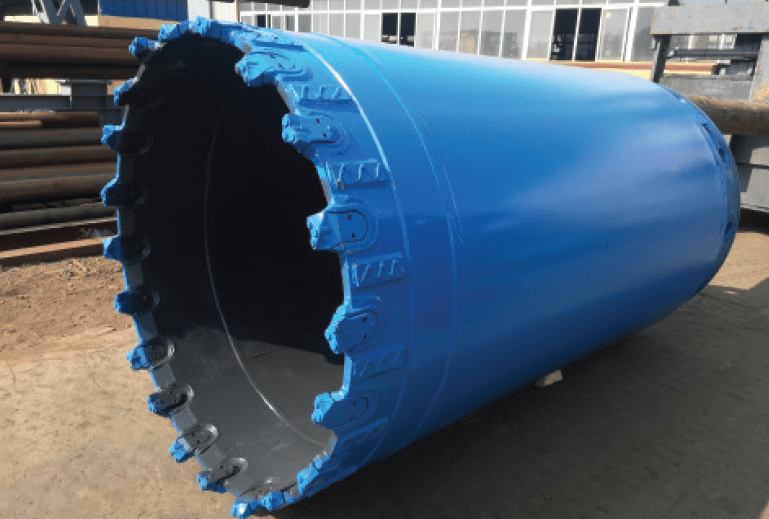
Unexpected conditions and countless variables prove that the choice of tooling and parts is not an exact science
When it comes to drilling a deep foundation into rock or silty soils, selecting the best tooling and wear parts for the job will help to keep a project on track and on budget.
The tools of the trade include the Kelly box, the Kelly bar, rock or soil augers, rock or soil buckets, and the wear parts, including teeth. The selection of tools depends on the application. There are tools for everything from soft, silty soil to gravel and sand to the ancient rock in the Canadian Shield.
Knowing the application is essential before any work takes place. Usually around six core samples are drilled to determine the conditions, but Mother Earth can be full of surprises. That’s why it’s important to purchase tooling and wear parts from experienced professionals who have seen it all.
Matt Krueger, a sales associate with Jeffrey Machine, has been helping customers select the best tools for deep foundations for 21 years. Jeffrey Machine, a U.S.-based manufacturer of auger tooling, along with a wide range of other drilling tools, has made rock tools that have been popular with some Canadian construction companies.
“You can drill soil with a rock tool, but you can’t drill rock with a dirt tool,” Krueger said. “Selecting the right tools for the job is critical. Just about every order has some customization specific to the soil and job.”
Jeffrey Machine’s Dragon tooth rock-cutting system needs no introduction to the deep foundation industry in Canada. Made for Jeffrey Machine’s rock augers, the sharp, angular dragon teeth are treated with high-grade carbide. As the auger spins, the teeth turn as well, breaking up rock more efficiently than the traditional bullet-style teeth.
Another Jeffrey Machine innovation that’s invaluable when crews drill into unexpected conditions is the .990 Tri-Holder (or pocket). The holder is engineered for use with multi-purpose augers equipped with a .990 Tri-Holder. It accommodates three different types of teeth: the .990 dirt tooth, the standard .990 tooth also known as C-31 and the .990 Dragon tooth.
“The tri-pocket is perfect for unexpected conditions. Swapping out the teeth will help eliminate damage to equipment,” said Krueger.
Anthony Royan, a sales manager with Caisson Consultant Inc., knows a thing or two about drilling deep foundations into rocky terrain. He works in Ontario, home to some of the oldest rocks on Earth. In Ontario, younger sedimentary rocks and soils overlay ancient Precambrian igneous and metamorphic rock which is extraordinarily hard on equipment and wear parts.
One of Caisson Consultant’s most successful wear parts is the BK47-02 tooth because of its ability to chomp through rock. The teeth are hot dipped in high-quality carbide powder which creates a rough surface area, enabling better rotation. The design and coating help to maintain the sharp cutting tip for more linear drilling metres with teeth consumption.
“It’s been a great success in the Canadian market,” said Royan. “We sell 3,000 to 4,000 of them a year.” Royan has received feedback from customers that for every 10 to 12 metres of rock drilled, just two to four teeth will need replacing. Most small, 540-millimetre-rock augers have around 10 to 12 teeth, but as the diameter goes up, and with a progressive style, the number of teeth can exceed 25.
Different soil types will determine the type of auger used. For instance, for soft to medium dense soil, a single-cut auger with earth teeth will be most effective. A flat rock auger will be effective for drilling a smooth, level foundation if the rock strength is around 60 to 80 megapascal (MPa). For rock strength above 80 MPa, a progressive rock auger will deliver the more concentrated force required to break up the rock.
As with Jeffrey Machine, Caisson Consultant’s team provides recommendations based on sample corings. “If you encounter an unexpected underlying factor, do not blame us,” Royan joked, adding. “We tell customers to let the soil determine the auger – and don’t mix applications.”
How to sustain the life of the equipment, tools and wear parts
If you ask manufacturers how long equipment, tools and wear parts will last, they will invariably say, “It depends.” It depends on the applications. It depends on the competency of the operator. It depends on whether the core samples give the team the information they need for seamless execution of the project.
Of course, selecting the right equipment for the right application is the first step to prolonging the life of equipment, but daily maintenance is also essential. “Daily maintenance involves inspecting the tool in the morning before the work begins and as it comes out of the hole every time you drill,” said Dan Dragone, a sales manager with BAUER Equipment America. “Replacing teeth when they show wear or break is another part of daily maintenance.”
Over time, more complex, technical maintenance will be required such as cutting off and replacing the Kelly box. “The key to success is to choose the right tool for the job and do the daily maintenance,” said Dragone. “When the tool needs to go to the shop, send it in. Don’t drill it to destruction.”
Krueger, Royan and Dragone have all seen issues come out on jobs that damage expensive equipment and sometimes there’s not much that can be done to prevent damage. It’s not common, but there are projects that are particularly hard on equipment.
For instance, a crew was drilling a foundation at an old steel mill. As they drilled into the soil, they hit steel slag, causing the auger to bend up and break. “They couldn’t see they were getting into it, so they destroyed tools,” said Dragone.
Fortunately, that’s a worst-case scenario and it’s not a common occurrence on work sites. If equipment is used for the applications for which it was built, it will have a lifespan of six months to four years.
In general, earth augers last longer than rock augers and need less maintenance. For dirt tools, a lifespan of one to four years is reasonable. For rock tools, it’s not uncommon for the lifespan to be around six months, but it can be as long as two years – and that’s with good maintenance.
“Eventually it becomes cheaper to buy a new tool,” said Dragone. When is it time to replace equipment? When it stops performing as it should and when sending it to the shop would just be a Band-Aid solution.