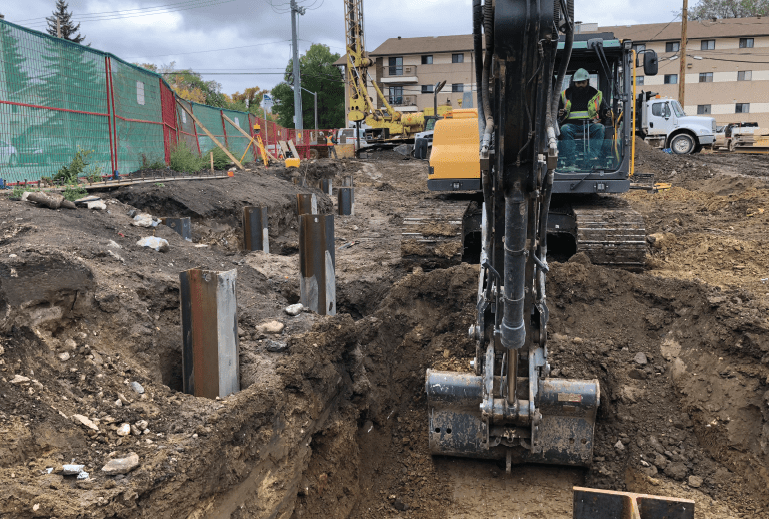
Saskatoon’s City Park neighbourhood is a vibrant downtown mixed-use area bordered by the South Saskatchewan River to the east, railway tracks to the west, 33rd Street to the north, and 25th Street to the south. Along with all types of residential homes, the area offers a host of desirable amenities including schools, parks, Saskatoon City Hospital, shopping, restaurants and leisure programs.
Busy Queen Street is lined with commercial businesses and is also the most direct route to Saskatoon City Hospital. It’s a challenging environment for any type of construction project – and that’s before you look below the surface.
“Some contractors won’t work in downtown Saskatoon because it’s too hard to dig there,” said Banain Cote, president and CEO of Innovative Piling Solutions (IPS), which is headquartered in nearby Martensville, Sask. “The ground is firm till until about 10 feet, and then there is a five-foot-thick layer of boulders, and under that is very hard glacial till with SPT [standard penetration test] values approaching 80.”
That’s exactly what IPS encountered when it was hired in mid-July 2018 to provide a soldier pile and wood lagging shoring wall for temporary earth retention – as well as underpinning and structural piling installation – for the new Monarch Building, a two-storey commercial infill development at the southeast corner of Queen Street and 2nd Avenue North. The site is the former home of Ming’s Kitchen and Juliette’s Dance Centre, both Saskatoon landmarks that were demolished to make way for the new 17,000-square-foot retail and office development. Immediately, IPS realized the job quite literally put them between a rock and hard place.
“Since Queen Street is the main corridor for City Hospital, it had to stay open for ambulance access,” said Cote. “Being an infill project, we were confined between Queen Street to the north, 2nd Avenue to the west, the brick wall of the Saskatoon Construction Association building to the south and an alley to the east.”
Access to the site was severely restricted. Materials and equipment had to be trucked in through the alley with minimal disruption to the tenants of a neighbouring building who parked there. Cote said IPS did much of the moving between midnight and 3 a.m., working a fair bit of overtime to keep the project on schedule. From late July until mid-November, IPS was onsite at the Monarch Building, working through several phases of the job.
First was the underpinning of the Saskatoon Construction Association building next door to address some structural concerns as well as the start of the structural cast-in-place piling. Next, IPS performed shoring and earth retention for the Queen Street utility corridor using a drilled soldier pile and wood lagging system.
“There were 21 soldier piles and a lagging system installed because of the geotechnical constraints and the access the concrete contractors needed to construct some of their footings,” said Cote. “It was all rock where we were trying to build. So, we chose a drilled soldier pile shoring system because we could break up the rock and remove it. These soldier piles were 24 inches in diameter and 25 feet deep.”
Crews also encountered a lot of construction debris and rubble from the previous building, including old lead drains. All of it had to be removed, which proved to be yet another challenge. “We had to do our own hauling because it was downtown in a very congested area. Some of the moves happened at midnight and some at 3 a.m. to avoid traffic. That was the biggest work-around for us.”
Phase three involved what Cote referred to as “value-added engineering” for the building’s owner. “Originally they had planned for a mix of cast in place foundations and footings. Our experience on the shoring wall led us to propose drilling the piles as opposed to doing footings, which would have extended the schedule. We were able to save the owner both time and money by switching some of those footings over, as well as adapting to changing site conditions.”
IPS installed 16 cast in place piles (16 to 24 inches in diameter), up to 30 feet deep for the structural elements. At the south end of the site, crews were surprised to encounter a deep, segregated sand layer. “We couldn’t drill and install the temporary casing because of the rocks, so we had to switch nine of the remaining structural piles to beefed-up helical steel screw piles, with 9.625-inch and 10.75-inch shaft diameter with 36-inch helices, 28 feet long installed to 120,000 foot pounds of torque.”
All told, the Monarch Building project involved three piling types: Soldier pile and wood lagging temporary earth retention, high capacity cast in place piles and high capacity helical steel screw piles. IPS used three different pieces of piling equipment, including a DH40 LoDril, a Watson 2500 crawler mount and a Hitachi 270 with an Eskridge D1400 drive head.
“Reaching deep into our equipment inventory was definitely a reason this project was so successful and we pride ourselves on the diversity and capability of our deep foundation equipment,” said Cote. “We basically went in armed for bear,” he continued. “We needed equipment to drill through the Saskatoon rock. At one point, we were working [on] the building’s structural piling on the east end of the site where the power lines and building almost intersect, which had about [16 feet] of working clearance, due to the de-energized power lines. So, a DH40 LoDril was a primary selection for us because the rotary and Kelly bar attachment is so compact and the rig has enough rotary torque to core and break up the rock.”
IPS crews finished work on the Monarch Building on Nov. 14, 2018. Cote said the weather largely co-operated throughout the project and it was a pleasure to work with the other local contractors on the job. “I think this job went very well, even considering what we were up against,” he said. “Other companies come in to work in downtown Saskatoon and they are often unprepared. Local geotechnical knowledge is gold in our business. We went in expecting the worst drilling we’d done all year, and it was – but we were prepared.”
Material suppliers for the Monarch Building project included Burnco Rock Products, Helical Pier Systems, Ardel Steel, Varsteel, L&M Wood Products, Browns Landscaping and Leveling, Atel Concrete, and Turner’s Transport. Cote said the building owner was pleased with the on-time and under-budget performance of IPS. Plus, he himself is proud that his crews had no safety-related incidents on the site.
“Our culture of safety is a very important value to us and we were faced with challenges every step of the way, but we handled them efficiently and safely. It was a challenging project, but that does not deter the success we had in both the construction and safety aspects, even though we were performing some of the most dangerous piling procedures.”